Understanding Hand-soldering techniques
Hand-soldering techniques refer to the manual methods used to create electrical connections between components on a PCB. These techniques require a skilled operator who uses a soldering iron to apply solder to the desired points on the board. The goal is to create strong, reliable connections that ensure the proper functioning of the electronic device.
Point-by-Point Soldering
Point-by-point soldering, also known as hand soldering or manual soldering, is the most common hand-soldering technique. It involves using a soldering iron to apply solder to individual points on the PCB, one at a time. This technique is often used for small-scale production, prototyping, and repair work.
Advantages of Point-by-Point Soldering
- Precision: Point-by-point soldering allows for precise control over the application of solder, making it ideal for working with small components or tight spaces.
- Flexibility: This technique can be used on a wide variety of PCBs and components, regardless of their size or complexity.
- Low cost: Point-by-point soldering requires minimal equipment and can be performed with a basic soldering iron and solder.
Disadvantages of Point-by-Point Soldering
- Time-consuming: Soldering each point individually can be a slow process, especially for larger PCBs with many components.
- Operator skill: The quality of the solder joints depends heavily on the skill and experience of the operator.
- Inconsistency: Due to the manual nature of the process, there may be variations in the quality of solder joints across the PCB.
Mini-Wave Soldering
Mini-wave soldering is a semi-automated hand-soldering technique that uses a miniature wave of molten solder to create connections on a PCB. The PCB is placed on a conveyor belt that moves it through a small solder wave, allowing the solder to flow onto the desired points on the board.
Advantages of Mini-wave Soldering
- Speed: Mini-wave soldering is faster than point-by-point soldering, as it can solder multiple points simultaneously.
- Consistency: The automated nature of the process ensures more consistent Solder Joint Quality across the PCB.
- Reduced operator fatigue: Since the operator does not need to manually apply solder to each point, mini-wave soldering can reduce operator fatigue and the risk of repetitive strain injuries.
Disadvantages of Mini-wave Soldering
- Equipment cost: Mini-wave soldering machines are more expensive than basic Soldering Irons, making this technique less accessible for small-scale operations or hobbyists.
- Limited flexibility: Mini-wave soldering may not be suitable for all PCB Designs or components, as the solder wave may not reach certain areas or may damage sensitive components.
- Setup time: Configuring the mini-wave soldering machine for a specific PCB design can be time-consuming, especially for small production runs.
Best Practices for Hand-soldering
Regardless of the hand-soldering technique used, following best practices can help ensure high-quality solder joints and reliable electrical connections.
Proper Tools and Materials
- Soldering iron: Choose a soldering iron with adjustable temperature control and a tip size appropriate for the components being soldered.
- Solder: Use high-quality solder with the correct alloy composition and diameter for the application. lead-free solder is often preferred due to environmental and health concerns.
- Flux: Apply flux to the soldering area to improve solder flow and remove oxides from the surfaces being joined.
- Cleaning supplies: Have isopropyl alcohol, lint-free wipes, and a brass sponge on hand for cleaning the soldering iron tip and the PCB.
Soldering Technique
- Tip maintenance: Keep the soldering iron tip clean and tinned with a small amount of solder to ensure optimal heat transfer.
- Pre-heating: Pre-heat the components and PCB to reduce thermal stress and improve solder flow.
- Solder application: Apply solder to the joint, ensuring that it flows evenly around the component lead and pad. Use just enough solder to create a strong connection without creating excess.
- Cooling: Allow the solder joint to cool naturally; avoid blowing on the joint or moving the PCB until the solder has solidified.
Inspection and Quality Control
- Visual inspection: Examine each solder joint for proper shape, size, and wetting. Look for signs of bridging, insufficient solder, or excessive solder.
- Mechanical testing: Gently tug on component leads to ensure they are securely attached to the PCB.
- Electrical testing: Use a multimeter or other testing equipment to verify electrical continuity and resistance across the solder joints.
Choosing the Right Hand-soldering Technique
Selecting the appropriate hand-soldering technique depends on various factors, including the scale of production, PCB complexity, available resources, and operator skill level.
Factor | Point-by-Point Soldering | Mini-wave Soldering |
---|---|---|
Production scale | Small to medium | Medium to large |
PCB complexity | Suitable for all levels | May be limited |
Equipment cost | Low | High |
Operator skill | High | Moderate |
Consistency | Variable | High |
Speed | Slow | Fast |
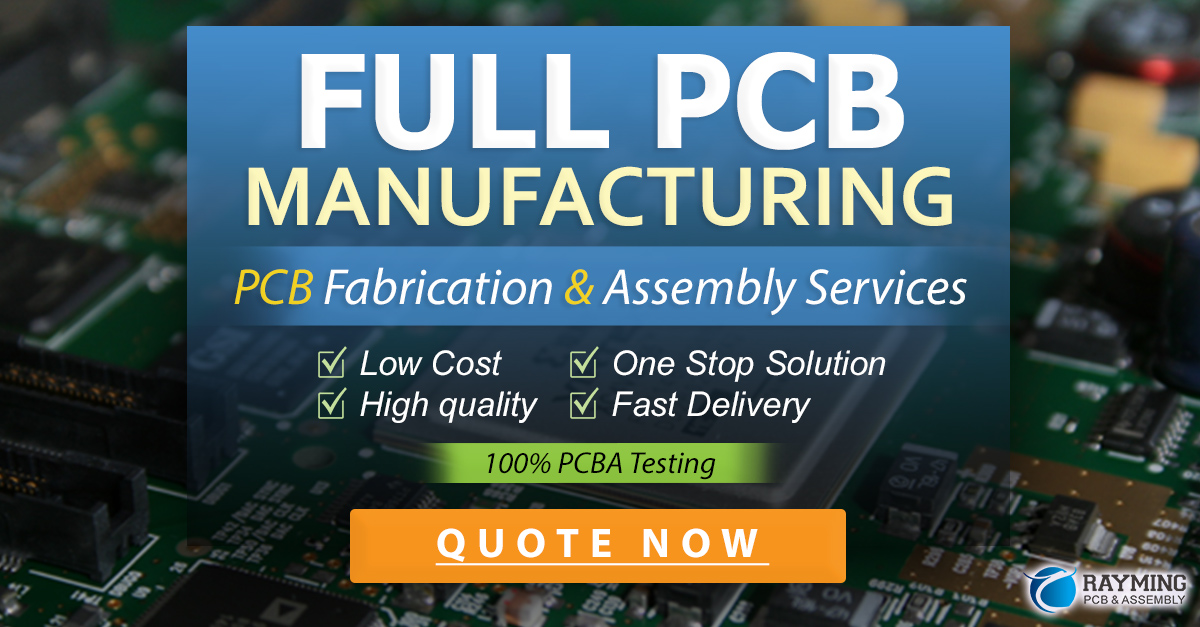
Frequently Asked Questions (FAQ)
-
Q: What is the difference between point-by-point soldering and mini-wave soldering?
A: Point-by-point soldering involves manually applying solder to individual points on a PCB using a soldering iron, while mini-wave soldering uses a semi-automated process where the PCB is passed through a small wave of molten solder. -
Q: Which hand-soldering technique is best for small-scale production or prototyping?
A: Point-by-point soldering is generally more suitable for small-scale production or prototyping, as it requires minimal equipment and offers greater flexibility in handling various PCB designs and components. -
Q: How can I ensure consistent solder joint quality when using point-by-point soldering?
A: To ensure consistent solder joint quality, use proper tools and materials, maintain a clean and tinned soldering iron tip, apply the correct amount of solder, and allow the joint to cool naturally. Regular inspection and quality control measures can also help identify and address any issues. -
Q: What are the advantages of using mini-wave soldering over point-by-point soldering?
A: Mini-wave soldering offers increased speed, consistency, and reduced operator fatigue compared to point-by-point soldering. It is particularly advantageous for medium to large-scale production runs. -
Q: Can mini-wave soldering be used for all types of PCBs and components?
A: Mini-wave soldering may not be suitable for all PCB designs or components. Some areas of the PCB may be difficult to reach with the solder wave, and certain sensitive components may be damaged by the soldering process. It is essential to assess the compatibility of the PCB and components with mini-wave soldering before implementing this technique.
Conclusion
Hand-soldering is an essential skill in the electronics manufacturing and repair industry, with point-by-point soldering and mini-wave soldering being two commonly used techniques. Point-by-point soldering offers precision, flexibility, and low cost, making it ideal for small-scale production and prototyping. Mini-wave soldering, on the other hand, provides increased speed, consistency, and reduced operator fatigue, making it suitable for medium to large-scale production.
Choosing the right hand-soldering technique depends on various factors, such as production scale, PCB complexity, available resources, and operator skill level. Regardless of the technique used, following best practices for tools, materials, soldering technique, inspection, and quality control is crucial for achieving high-quality solder joints and reliable electrical connections.
By understanding the advantages, disadvantages, and best practices associated with point-by-point soldering and mini-wave soldering, electronics manufacturers and technicians can make informed decisions and optimize their hand-soldering processes for improved efficiency and product quality.
Leave a Reply