Introduction to PCB Grounding
Proper grounding is essential for the reliable operation and performance of printed circuit boards (PCBs). PCB grounding refers to the techniques and strategies used to create a low-impedance path for currents to return to their source, minimize noise, and ensure the stable functioning of the circuit. Effective grounding is crucial for signal integrity, electromagnetic compatibility (EMC), and the overall robustness of the PCB Design.
In this article, we will delve into the fundamentals of PCB grounding, explore various grounding techniques, discuss the importance of ground planes, and provide best practices for implementing a solid grounding scheme in your PCB designs.
Understanding the Importance of PCB Grounding
Minimizing Noise and Interference
One of the primary reasons for implementing proper grounding in PCBs is to minimize noise and interference. Noise can originate from various sources, such as power supplies, digital circuits, analog circuits, and external electromagnetic interference (EMI). Inadequate grounding can lead to ground loops, common-mode noise, and other unwanted effects that can degrade signal quality and overall system performance.
By providing a low-impedance path for currents to return to their source, effective grounding helps to reduce the impact of noise and interference on sensitive circuits. It ensures that unwanted currents are quickly shunted to ground, minimizing their impact on signal integrity.
Ensuring Signal Integrity
Maintaining signal integrity is another critical aspect of PCB grounding. Signal integrity refers to the ability of a signal to propagate through the PCB without distortion, attenuation, or interference. Poor grounding can introduce impedance mismatches, reflections, and crosstalk, which can compromise signal integrity.
Proper grounding techniques, such as using ground planes, minimizing ground impedance, and careful routing of signal traces, help to maintain signal integrity throughout the PCB. By providing a stable reference point for signals and minimizing the impact of noise and interference, effective grounding ensures that signals remain clean and reliable.
Enhancing Electromagnetic Compatibility (EMC)
Electromagnetic compatibility (EMC) is a critical consideration in PCB design, particularly in applications that are sensitive to electromagnetic interference (EMI) or require compliance with EMC regulations. Proper grounding plays a vital role in achieving EMC by minimizing the radiation of electromagnetic energy from the PCB and reducing its susceptibility to external EMI.
Effective grounding techniques, such as using ground planes, implementing shielding, and properly terminating high-speed signals, help to contain electromagnetic energy within the PCB and prevent it from interfering with other devices or being affected by external sources of EMI.
Grounding Techniques for PCBs
Ground Planes
One of the most effective grounding techniques in PCB design is the use of ground planes. A ground plane is a large, continuous copper area on one or more layers of the PCB that serves as a low-impedance return path for currents. Ground planes provide several benefits, including:
- Low impedance: Ground planes offer a low-impedance path for return currents, minimizing the impact of noise and ensuring efficient current flow.
- Shielding: Ground planes act as a shield, helping to contain electromagnetic energy within the PCB and reduce emissions.
- Reduced inductance: The large surface area of ground planes minimizes inductance, which is essential for high-speed signals and reducing ground bounce.
When designing ground planes, it is important to consider factors such as the placement of components, the routing of signal traces, and the connection of ground planes between layers. Proper design and implementation of ground planes are crucial for achieving effective grounding in PCBs.
Star Grounding
Star grounding is a technique that involves connecting all ground points to a single, central point, forming a star-like pattern. This approach helps to minimize ground loops and ensure that all ground points have a common reference. Star grounding is particularly useful in mixed-signal designs, where analog and digital grounds need to be separated to prevent noise coupling.
In a star grounding scheme, each subsystem or functional block of the PCB has its own ground connection that radiates from the central ground point. This helps to isolate different sections of the circuit and prevent noise from propagating between them.
However, star grounding can become impractical in complex designs with a large number of ground connections. In such cases, a hybrid approach combining star grounding with ground planes can be employed to achieve effective grounding.
Partitioning and Isolation
Partitioning and isolation are techniques used to separate sensitive analog and digital sections of a PCB to minimize noise coupling and interference. By physically separating these sections and providing dedicated ground connections, the impact of noise generated by digital circuits on analog circuits can be minimized.
Partitioning involves dividing the PCB into distinct regions for analog and digital components, with separate ground planes or ground connections for each section. This helps to confine noise within each partition and prevents it from spreading to other parts of the circuit.
Isolation techniques, such as using split ground planes, guard traces, or isolation barriers, further enhance the separation between analog and digital sections. These techniques help to prevent noise coupling through the substrate or via electromagnetic fields.
Ground Stitching and Stitching Capacitors
Ground stitching is a technique used to improve the electrical connection between ground planes on different layers of a Multi-Layer PCB. It involves placing vias at regular intervals along the edges of the ground planes to create a low-impedance path between them. Ground stitching helps to minimize impedance differences and ensure a consistent ground reference throughout the PCB.
Stitching capacitors, also known as Decoupling Capacitors, are used in conjunction with ground stitching to provide a local low-impedance path for high-frequency noise. These capacitors are placed near noise-sensitive components or between ground planes to shunt high-frequency noise to ground, preventing it from propagating throughout the circuit.
The placement and value of stitching capacitors are critical for their effectiveness. They should be placed as close as possible to the noise source and have a low equivalent series inductance (ESL) to provide a low-impedance path at high frequencies.
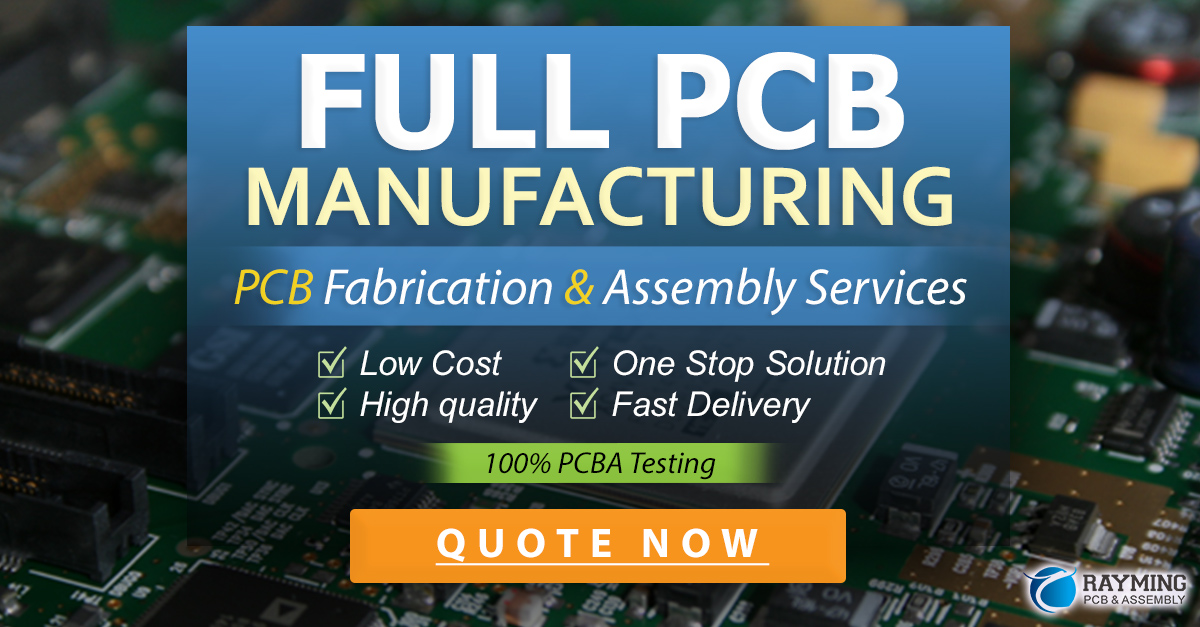
Best Practices for PCB Grounding
To achieve effective grounding in your PCB designs, consider the following best practices:
-
Use ground planes: Incorporate ground planes in your PCB design to provide a low-impedance return path and minimize noise.
-
Minimize ground impedance: Keep ground connections short and wide to minimize impedance and ensure efficient current flow.
-
Separate analog and digital grounds: Use techniques like partitioning and isolation to separate analog and digital grounds and prevent noise coupling.
-
Implement star grounding: Use star grounding for critical subsystems or in mixed-signal designs to minimize ground loops and ensure a common reference point.
-
Use ground stitching and stitching capacitors: Employ ground stitching and stitching capacitors to improve the electrical connection between ground planes and provide a local low-impedance path for high-frequency noise.
-
Route signals carefully: Consider the placement and routing of signal traces to minimize crosstalk and interference. Use techniques like trace shielding and proper trace spacing to maintain signal integrity.
-
Terminate high-speed signals properly: Use appropriate termination techniques, such as series termination or parallel termination, to minimize reflections and ensure signal integrity in high-speed designs.
-
Conduct thorough testing and analysis: Perform comprehensive testing and analysis, including impedance measurements, noise analysis, and EMC testing, to validate the effectiveness of your grounding scheme.
By following these best practices and carefully considering grounding techniques in your PCB designs, you can achieve reliable, noise-free, and high-performance circuits.
Grounding Strategies for Different Applications
The specific grounding strategies employed in a PCB design may vary depending on the application and the unique requirements of the circuit. Here are some common grounding strategies for different types of applications:
Analog Circuits
In analog circuits, proper grounding is critical for maintaining signal integrity and minimizing noise. Some key considerations for grounding analog circuits include:
- Using separate analog and digital ground planes to prevent noise coupling.
- Implementing star grounding for sensitive analog components to minimize ground loops.
- Placing analog components close to their respective ground connections to minimize ground impedance.
- Using ground stitching and stitching capacitors to provide a low-impedance path for noise.
Digital Circuits
Digital circuits, especially high-speed digital designs, require careful grounding to ensure signal integrity and minimize electromagnetic interference (EMI). Some grounding strategies for digital circuits include:
- Using solid ground planes to provide a low-impedance return path for digital signals.
- Implementing proper termination techniques, such as series termination or parallel termination, to minimize reflections and ensure signal integrity.
- Using ground stitching and stitching capacitors to minimize ground bounce and provide a stable reference for digital signals.
- Placing decoupling capacitors close to digital components to provide a local low-impedance path for high-frequency noise.
Mixed-Signal Circuits
Mixed-signal circuits, which combine analog and digital components on the same PCB, require special attention to grounding to prevent noise coupling and ensure proper functioning of both analog and digital sections. Some grounding strategies for mixed-signal circuits include:
- Partitioning the PCB into separate analog and digital sections with dedicated ground planes.
- Using isolation techniques, such as split ground planes or isolation barriers, to prevent noise coupling between analog and digital sections.
- Implementing star grounding for the analog section to minimize ground loops and ensure a clean reference for analog signals.
- Placing stitching capacitors at the interface between analog and digital sections to provide a low-impedance path for noise.
High-Frequency and RF Circuits
High-frequency and RF circuits are particularly sensitive to grounding issues due to the presence of high-frequency signals and the potential for electromagnetic interference (EMI). Some grounding strategies for high-frequency and RF circuits include:
- Using a solid ground plane to provide a low-impedance return path for high-frequency signals.
- Minimizing the length of ground connections to reduce inductance and ensure efficient current flow.
- Using ground stitching and stitching capacitors to provide a low-impedance path for high-frequency noise.
- Implementing proper shielding techniques, such as using grounded shield cans or coplanar waveguides, to contain electromagnetic energy and prevent interference.
By tailoring the grounding strategies to the specific requirements of each application, designers can ensure optimal performance, signal integrity, and electromagnetic compatibility in their PCB designs.
FAQ
1. What is the purpose of grounding in PCBs?
Grounding in PCBs serves several important purposes, including:
– Providing a low-impedance return path for currents to minimize noise and ensure efficient current flow.
– Maintaining signal integrity by minimizing impedance mismatches, reflections, and crosstalk.
– Enhancing electromagnetic compatibility (EMC) by minimizing the radiation of electromagnetic energy and reducing susceptibility to external EMI.
2. What is a ground plane, and why is it important?
A ground plane is a large, continuous copper area on one or more layers of a PCB that serves as a low-impedance return path for currents. Ground planes are important because they provide a low-impedance path, act as a shield to contain electromagnetic energy, and minimize inductance, which is essential for high-speed signals and reducing ground bounce.
3. How does star grounding differ from using ground planes?
Star grounding involves connecting all ground points to a single, central point, forming a star-like pattern. This approach helps to minimize ground loops and ensure that all ground points have a common reference. In contrast, ground planes provide a continuous, low-impedance return path across the entire PCB. Star grounding is particularly useful in mixed-signal designs, while ground planes are more commonly used in general-purpose designs.
4. What are stitching capacitors, and how do they improve grounding?
Stitching capacitors, also known as decoupling capacitors, are used to provide a local low-impedance path for high-frequency noise. They are placed near noise-sensitive components or between ground planes to shunt high-frequency noise to ground, preventing it from propagating throughout the circuit. Stitching capacitors help to improve grounding by providing a low-impedance path for noise and ensuring a stable reference for signals.
5. How can I ensure effective grounding in my PCB design?
To ensure effective grounding in your PCB design, consider the following best practices:
– Use ground planes to provide a low-impedance return path and minimize noise.
– Minimize ground impedance by keeping ground connections short and wide.
– Separate analog and digital grounds using techniques like partitioning and isolation to prevent noise coupling.
– Implement star grounding for critical subsystems or in mixed-signal designs to minimize ground loops.
– Use ground stitching and stitching capacitors to improve electrical connections and provide a local low-impedance path for high-frequency noise.
– Route signals carefully to minimize crosstalk and interference, and use proper termination techniques for high-speed signals.
– Conduct thorough testing and analysis to validate the effectiveness of your grounding scheme.
By understanding the principles of PCB grounding, employing appropriate grounding techniques, and following best practices, designers can achieve reliable, noise-free, and high-performance circuits in their PCB designs.
Conclusion
Effective grounding is a critical aspect of PCB design that directly impacts the performance, reliability, and electromagnetic compatibility of electronic circuits. By understanding the importance of grounding and employing techniques such as ground planes, star grounding, partitioning, and isolation, designers can create robust and noise-free PCB designs.
The use of ground planes provides a low-impedance return path for currents, minimizes noise, and enhances signal integrity. Star grounding helps to minimize ground loops and ensure a common reference point, while partitioning and isolation techniques separate sensitive analog and digital sections to prevent noise coupling.
Ground stitching and stitching capacitors further improve the electrical connection between ground planes and provide a local low-impedance path for high-frequency noise. By following best practices and carefully considering grounding strategies for different applications, designers can optimize their PCB designs for optimal performance and reliability.
As PCB technology continues to advance and the demand for high-speed, low-noise, and EMC-compliant designs grows, the importance of effective grounding will only increase. By mastering the principles and techniques of PCB grounding, designers can create robust and reliable electronic products that meet the ever-increasing demands of modern applications.
Leave a Reply