Introduction to PCB Material Pricing
Printed Circuit Boards (PCBs) are essential components in modern electronics, forming the backbone of devices ranging from smartphones to aerospace systems. The cost of manufacturing PCBs is heavily influenced by the materials used in their construction. This comprehensive guide will delve into the various aspects of gross PCB material price, providing valuable insights for manufacturers, purchasers, and enthusiasts alike.
Factors Affecting PCB Material Price
Several key factors contribute to the overall cost of PCB materials:
1. Raw Material Costs
2. Market Demand and Supply
3. Manufacturing Processes
4. Technology Advancements
5. Regulatory Compliance
Let’s explore each of these factors in more detail.
Raw Material Costs
The cost of raw materials used in PCB manufacturing is a significant driver of overall pricing. The primary materials include:
– Copper foil
– Fiberglass reinforcement
– Epoxy resins
– Solder mask
– Silkscreen inks
Fluctuations in the prices of these raw materials directly impact the cost of PCB Production. For example, copper, a key component in PCBs, is a commodity whose price is subject to global market forces. When copper prices rise, so does the cost of PCB materials.
Market Demand and Supply
The law of supply and demand plays a crucial role in determining PCB material prices. When demand for PCBs is high, such as during periods of rapid growth in the electronics industry, prices tend to increase. Conversely, when demand slows down, prices may stabilize or even decrease.
Additionally, the availability of raw materials and production capacity can affect supply. If there are shortages or bottlenecks in the supply chain, prices may rise due to scarcity.
Manufacturing Processes
Advancements in PCB manufacturing processes can have a significant impact on material prices. As technology improves, manufacturers can produce PCBs more efficiently, reducing waste and lowering costs. Some key manufacturing processes that influence pricing include:
– Multilayer PCB fabrication
– High-density interconnect (HDI) technology
– Flexible and Rigid-Flex PCBs
– Embedded components
Investing in state-of-the-art manufacturing equipment and techniques can help PCB Manufacturers optimize their processes and offer competitive pricing.
Technology Advancements
The constant evolution of electronics technology drives changes in PCB material requirements. As devices become smaller, faster, and more complex, PCBs must adapt to meet these new demands. Some technological advancements that impact PCB material prices include:
– High-speed materials for faster signal propagation
– Low-loss materials for improved signal integrity
– Thermally conductive materials for better heat dissipation
– Halogen-free materials for environmental compliance
Developing and producing advanced materials to keep pace with technological progress can increase costs, which are often passed on to the end-user.
Regulatory Compliance
Regulatory requirements play a significant role in PCB material pricing. Governments and international organizations set standards for the use of hazardous substances, environmental impact, and worker safety. Compliance with these regulations often requires the use of specialized materials or additional processing steps, which can increase costs.
Some notable regulatory standards that impact PCB material prices include:
– Restriction of Hazardous Substances (RoHS) Directive
– Registration, Evaluation, Authorization, and Restriction of Chemicals (REACH) Regulation
– Underwriters Laboratories (UL) Standards
– International Organization for Standardization (ISO) Standards
Ensuring compliance with these standards is essential for PCB manufacturers to maintain market access and avoid penalties, but it can also contribute to higher material costs.
PCB Material Price Trends
Over the years, PCB material prices have experienced both ups and downs due to various market factors. Let’s take a look at some recent trends:
Year | Trend | Key Factors |
---|---|---|
2018 | Increase | Rising copper prices, high demand from automotive and IoT sectors |
2019 | Stabilization | Slowing demand, trade tensions, increased competition |
2020 | Decrease | COVID-19 pandemic, reduced global demand, supply chain disruptions |
2021 | Recovery | Economic recovery, pent-up demand, raw material price increases |
As the global economy continues to recover from the impact of the COVID-19 pandemic, PCB material prices are expected to stabilize and potentially increase in the coming years. However, ongoing trade tensions, shifts in supply chains, and technological advancements may contribute to price fluctuations.
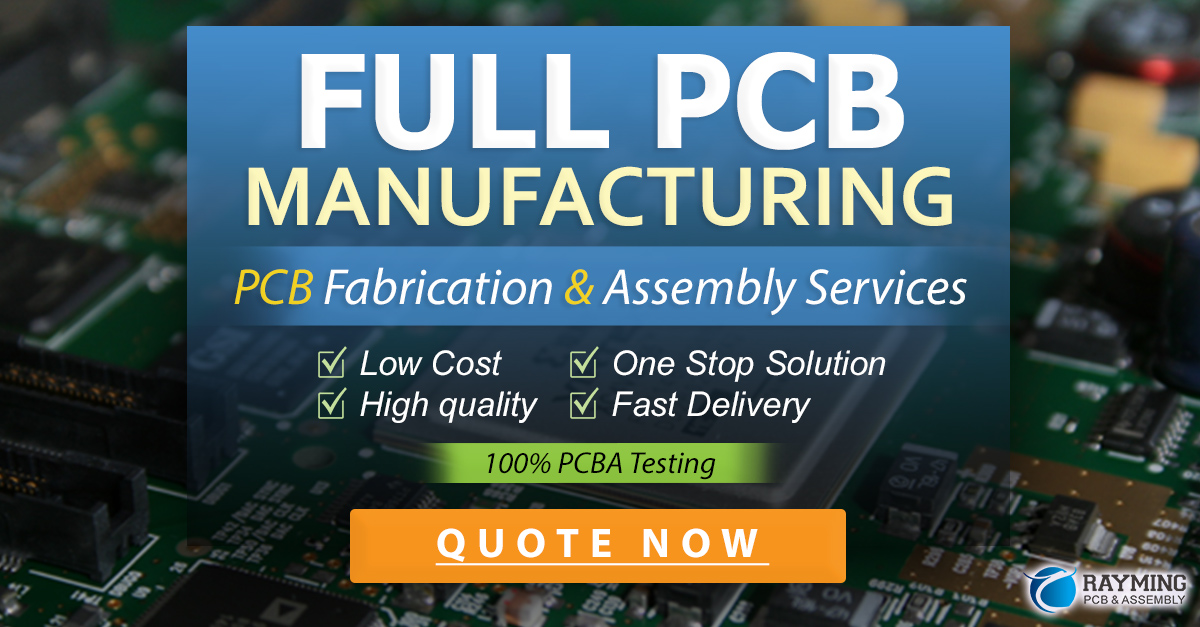
Strategies for Managing PCB Material Costs
For manufacturers and purchasers alike, managing PCB material costs is crucial for maintaining profitability and competitiveness. Here are some strategies to consider:
-
Strategic Sourcing: Develop relationships with multiple suppliers to ensure a stable supply of materials at competitive prices. Regularly review and compare pricing from different suppliers to identify opportunities for cost savings.
-
Volume Purchasing: Negotiate better prices by purchasing materials in larger quantities. This can help reduce per-unit costs and provide a buffer against potential price increases.
-
Design Optimization: Work closely with PCB designers to optimize layouts and material usage. Minimizing waste, reducing layer counts, and using standardized materials can help control costs.
-
Material Substitution: Explore alternative materials that offer similar performance characteristics at a lower cost. However, be cautious when substituting materials, as changes can impact product quality and reliability.
-
Inventory Management: Implement effective inventory management practices to minimize carrying costs and avoid stockouts. Use forecasting tools to predict demand and adjust inventory levels accordingly.
-
Continuous Improvement: Regularly review and optimize manufacturing processes to identify opportunities for cost savings. Investing in automation, lean manufacturing, and staff training can help improve efficiency and reduce material waste.
By implementing these strategies, manufacturers and purchasers can better manage PCB material costs and maintain a competitive edge in the market.
Frequently Asked Questions (FAQ)
-
What is the most expensive component in PCB materials?
The most expensive component in PCB materials is typically the copper foil used for the conductive layers. Copper prices are subject to global market fluctuations and can significantly impact overall PCB material costs. -
How do I know if a PCB material complies with regulatory standards?
PCB manufacturers should provide documentation certifying compliance with relevant regulatory standards, such as RoHS and REACH. Look for material datasheets and certificates of compliance when purchasing PCB materials. -
Can I use cheaper materials to reduce PCB costs?
While using cheaper materials may seem like an attractive option to reduce costs, it is essential to consider the potential impact on product quality and reliability. Always evaluate the performance requirements of your application before making material substitutions. -
How can I stay informed about PCB material price trends?
Stay informed about PCB material price trends by regularly reviewing industry publications, attending trade shows and conferences, and maintaining open communication with your suppliers. Many suppliers offer regular price updates and market insights to their customers. -
What are the long-term prospects for PCB material prices?
The long-term prospects for PCB material prices are influenced by a variety of factors, including global economic conditions, technological advancements, and shifts in supply and demand. While prices may fluctuate in the short term, the overall trend is likely to be one of stability with potential for gradual increases over time.
Conclusion
Understanding gross PCB material prices is essential for anyone involved in the electronics industry. By considering the various factors that influence pricing, staying informed about market trends, and implementing cost management strategies, manufacturers and purchasers can navigate the complex landscape of PCB material costs. As technology continues to advance and new applications emerge, the demand for high-quality, cost-effective PCB materials will only grow. By staying ahead of the curve and adapting to changing market conditions, companies can position themselves for success in this dynamic industry.
Leave a Reply