Introduction to Flexible PCBs and Their Advantages
Flexible printed circuit boards (PCBs) have revolutionized the electronics industry by providing a versatile and reliable solution for connecting electronic components in a variety of applications. Unlike traditional rigid PCBs, flexible PCBs are made from thin, flexible materials that allow them to bend and twist without breaking or losing their electrical properties. This unique characteristic makes them ideal for use in devices that require compact, lightweight, and durable electronic assemblies, such as smartphones, wearables, medical devices, and aerospace equipment.
The advantages of flexible PCBs over rigid PCBs are numerous. Some of the key benefits include:
- Space savings: Flexible PCBs can be bent and folded to fit into tight spaces, reducing the overall size and weight of electronic devices.
- Increased reliability: The flexible nature of these PCBs allows them to withstand vibrations, shocks, and thermal stress better than rigid PCBs, making them more reliable in harsh environments.
- Improved signal integrity: Flexible PCBs can be designed with shorter signal paths and reduced electromagnetic interference (EMI), resulting in better signal integrity and higher performance.
- Enhanced design flexibility: The ability to bend and fold flexible PCBs enables designers to create more complex and innovative electronic assemblies that would be impossible with rigid PCBs.
- Cost-effectiveness: In many cases, using a flexible PCB can reduce the number of connectors and cables required, leading to lower assembly costs and improved reliability.
Understanding the Flexible PCB Manufacturing Process
The manufacturing process for flexible PCBs is similar to that of rigid PCBs, but with some key differences. The basic steps involved in producing a flexible PCB are as follows:
- Material selection: The base material for a flexible PCB is typically a thin, flexible polymer such as polyimide or polyester. Copper foil is then laminated onto one or both sides of the polymer substrate to create the conductive layer.
- Circuit design: The desired circuit pattern is designed using computer-aided design (CAD) software, taking into account the specific requirements of the flexible PCB, such as bend radius, fold lines, and material properties.
- Imaging: The circuit design is transferred onto the copper-clad laminate using a photolithographic process. This involves coating the laminate with a light-sensitive resist, exposing it to UV light through a photomask, and then developing the resist to reveal the desired circuit pattern.
- Etching: The exposed copper is chemically etched away, leaving only the desired circuit traces on the flexible substrate.
- Coverlay application: A protective coverlay is laminated onto the circuit side of the PCB to insulate and protect the traces from damage.
- Cutting and drilling: The flexible PCB is cut to its final shape and size, and any necessary holes or slots are drilled or punched.
- Surface finishing: The exposed copper traces are coated with a protective finish, such as gold or solder mask, to prevent oxidation and improve solderability.
- Electrical testing: The completed flexible PCB is thoroughly tested to ensure that it meets all electrical and mechanical specifications before being shipped to the customer.
Factors Affecting Flexible PCB quotes
When requesting quotes for flexible PCBs, several factors can impact the final price. Understanding these factors can help you optimize your design and get the most cost-effective solution for your project. Some of the key factors affecting flexible PCB quotes include:
- Board size and shape: Larger and more complex board shapes generally cost more to manufacture due to increased material usage and processing time.
- Layer count: The number of conductive layers in a flexible PCB directly affects its cost, as each additional layer requires more materials and processing steps.
- Material selection: The choice of base material, copper thickness, and surface finish can significantly impact the cost of a flexible PCB. Higher-performance materials and finishes typically come at a premium.
- Quantity: As with most manufactured products, ordering larger quantities of flexible PCBs can result in lower per-unit costs due to economies of scale.
- Design complexity: Features such as tight tolerances, small trace widths, and high-density interconnects can increase the manufacturing complexity and, consequently, the cost of a flexible PCB.
- Lead time: Faster turnaround times often come with a higher price tag, as manufacturers may need to prioritize your order and work overtime to meet the deadline.
- Certifications and testing: If your application requires specific certifications (e.g., UL, IPC) or additional testing (e.g., impedance control, thermal cycling), these services will add to the overall cost of your flexible PCB.
To illustrate the impact of some of these factors on flexible PCB pricing, consider the following example:
Factor | Option A | Option B |
---|---|---|
Board size | 50 mm x 50 mm | 100 mm x 100 mm |
Layer count | 2 layers | 4 layers |
Material | Polyimide, 18 μm copper | Polyimide, 35 μm copper |
Quantity | 100 pieces | 1,000 pieces |
Lead time | 4 weeks | 2 weeks |
In this scenario, Option B would likely result in a higher per-unit cost due to the larger board size, higher layer count, thicker copper, and shorter lead time. However, the larger order quantity could help offset some of these costs through volume discounts.
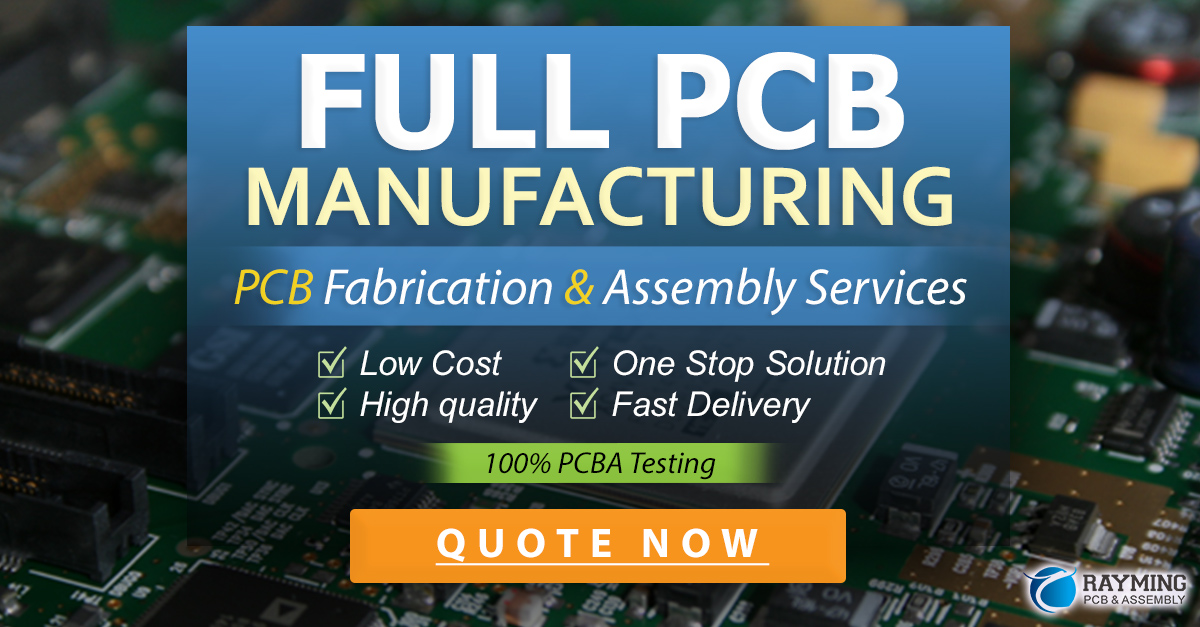
Choosing the Right Flexible PCB Manufacturer
Selecting the right manufacturer is crucial to ensuring the success of your flexible PCB project. When evaluating potential suppliers, consider the following factors:
- Experience and expertise: Look for manufacturers with a proven track record of producing high-quality flexible PCBs for applications similar to yours.
- Manufacturing capabilities: Ensure that the manufacturer has the necessary equipment and processes in place to meet your specific requirements, such as fine-pitch traces, tight tolerances, or special materials.
- Quality control: Inquire about the manufacturer’s quality control processes, including inspections, testing, and certifications (e.g., ISO, IPC).
- Customer support: Choose a manufacturer that offers responsive and knowledgeable customer support, from the initial design review to the final delivery and beyond.
- Pricing and lead times: Compare quotes from multiple manufacturers to ensure you are getting a competitive price and lead time for your project.
- Minimum order quantity (MOQ): Some manufacturers may have high MOQs that exceed your needs, so be sure to ask about their minimum order requirements.
- Location and logistics: Consider the manufacturer’s location and shipping options, especially if you have tight deadlines or require specialized handling.
To help you compare and evaluate flexible PCB manufacturers, consider creating a vendor comparison matrix like the one below:
Factor | Manufacturer A | Manufacturer B | Manufacturer C |
---|---|---|---|
Experience | 10+ years | 5+ years | 15+ years |
Capabilities | 2-6 layers, 50 μm traces | 1-4 layers, 100 μm traces | 1-8 layers, 25 μm traces |
Quality control | ISO 9001, IPC Class 2 | ISO 9001 | ISO 9001, IPC Class 3 |
Customer support | Email, phone | Email, phone, on-site | |
Pricing | $$ | $ | $$$ |
Lead times | 3-4 weeks | 4-6 weeks | 2-3 weeks |
MOQ | 100 pieces | 500 pieces | 50 pieces |
Location | China | USA | Europe |
By carefully evaluating each manufacturer based on these factors, you can make an informed decision and choose the supplier that best meets your needs.
Optimizing Your Flexible PCB Design for Cost and Performance
To get the most competitive quotes for your flexible PCB project, it’s essential to optimize your design for both cost and performance. Here are some tips to help you achieve this:
- Keep it simple: Whenever possible, use standard materials, processes, and features to minimize manufacturing complexity and cost.
- Minimize layer count: Use the fewest number of layers necessary to achieve your desired functionality, as each additional layer adds cost.
- Opt for larger traces and spacing: Smaller traces and tighter spacing require more advanced manufacturing processes, which can increase costs. Use the largest trace widths and spacing that your design allows.
- Avoid unnecessary features: Carefully consider each feature in your design and eliminate any that are not essential to your application.
- Use standard sizes and shapes: Non-standard board sizes and shapes can require custom tooling and processing, which can drive up costs. Stick to standard sizes and shapes whenever possible.
- Consider panelization: If you are ordering smaller quantities, consider panelizing your design to maximize material usage and reduce per-unit costs.
- Plan for manufacturability: Involve your manufacturer early in the design process to ensure that your flexible PCB can be efficiently and cost-effectively produced.
- Leverage simulation tools: Use simulation software to optimize your design for signal integrity, EMI, and thermal performance before committing to a physical prototype.
By following these guidelines and working closely with your chosen manufacturer, you can create a flexible PCB design that balances cost and performance to meet your specific application requirements.
Frequently Asked Questions (FAQ)
-
Q: What is the typical lead time for flexible PCB production?
A: Lead times for flexible PCBs can vary depending on the complexity of the design, the chosen materials, and the manufacturer’s workload. Typical lead times range from 2 to 6 weeks, but expedited options may be available for an additional cost. -
Q: What is the minimum order quantity (MOQ) for flexible PCBs?
A: MOQs for flexible PCBs vary by manufacturer and can range from 50 to 1,000 pieces or more. Some manufacturers may offer lower MOQs for standard designs or prototyping services. -
Q: Can I use the same design files for flexible PCBs as I do for rigid PCBs?
A: While the basic design principles are similar, flexible PCBs have unique requirements that must be considered during the design process. These include bend radius, fold lines, and material properties. It’s best to consult with your manufacturer to ensure that your design files are optimized for flexible PCB production. -
Q: Are there any special considerations for soldering components to flexible PCBs?
A: Yes, soldering components to flexible PCBs requires special techniques to avoid damaging the flexible substrate or components. These techniques include using low-temperature solder, minimizing heat exposure, and providing strain relief for components. Your manufacturer should be able to provide guidance on the appropriate soldering methods for your specific design. -
Q: How can I ensure the reliability and durability of my flexible PCB in harsh environments?
A: To ensure the reliability and durability of your flexible PCB in harsh environments, consider the following: - Choose materials that are suitable for your application’s temperature range, chemical exposure, and mechanical stresses.
- Use appropriate protective coatings and encapsulation to shield your PCB from moisture, dust, and other contaminants.
- Design your PCB with strain relief features to minimize stress on components and solder joints during flexing.
- Conduct thorough testing and qualification to validate your PCB’s performance in the intended environment.
Conclusion
Flexible PCBs offer numerous advantages over traditional rigid PCBs, making them an attractive option for a wide range of applications. When seeking quotes for your flexible PCB project, it’s essential to understand the factors that influence pricing, such as board size, layer count, material selection, and manufacturing complexity. By carefully evaluating potential manufacturers and optimizing your design for cost and performance, you can ensure that you get the best value for your investment.
As the electronics industry continues to evolve, flexible PCBs will play an increasingly important role in enabling the next generation of compact, lightweight, and high-performance devices. By staying informed about the latest developments in flexible PCB technology and working closely with experienced manufacturers, you can leverage the benefits of these versatile interconnects to create innovative and reliable electronic products.
Leave a Reply