What is PCB Assembly?
PCB assembly is the process of assembling electronic components onto a printed circuit board (PCB) to create a functional electronic device. The process involves several stages, including:
- PCB design and fabrication
- Component selection and procurement
- Solder paste application
- Component placement
- Soldering
- Inspection and testing
Each stage plays a vital role in the overall quality and functionality of the assembled PCB.
The Importance of Functional Testing in PCB Assembly
Functional testing is a critical step in the PCB assembly process, as it ensures that the assembled board performs as intended and meets the required specifications. The primary objectives of functional testing are:
- Verifying the functionality of the assembled PCB
- Identifying and rectifying any defects or issues
- Ensuring the reliability and durability of the final product
By conducting thorough functional testing, PCB assembly service providers in China can deliver high-quality products that meet or exceed customer expectations.
Types of Functional Testing
There are several types of functional testing performed during PCB assembly, each targeting specific aspects of the board’s performance. Some of the most common types include:
-
In-Circuit Testing (ICT): This test involves using a bed of nails fixture to make contact with specific points on the PCB, allowing for the verification of individual component functionality and connectivity.
-
Flying Probe Testing: Flying probe testing utilizes mobile probes to test the PCB without the need for a custom fixture. This method is more flexible and cost-effective for low-volume production or prototypes.
-
Boundary Scan Testing: Also known as JTAG testing, boundary scan testing uses a special test access port (TAP) to test the functionality of digital components and the interconnections between them.
-
Functional Circuit Testing: This test involves applying input signals to the PCB and measuring the output to verify that the board functions as intended in a real-world scenario.
Benefits of Functional Testing in PCB Assembly
Incorporating functional testing into the PCB assembly process offers several benefits for both the service provider and the end customer:
-
Early Detection of Defects: Functional testing allows for the early detection and rectification of defects, reducing the risk of faulty products reaching the market.
-
Improved Product Quality: By ensuring that assembled PCBs meet the required specifications and perform as intended, functional testing contributes to the overall quality of the final product.
-
Cost Savings: Identifying and addressing issues early in the assembly process helps avoid costly rework or product recalls later on.
-
Enhanced Customer Satisfaction: Delivering high-quality, functionally tested PCBs increases customer satisfaction and builds trust in the service provider’s capabilities.
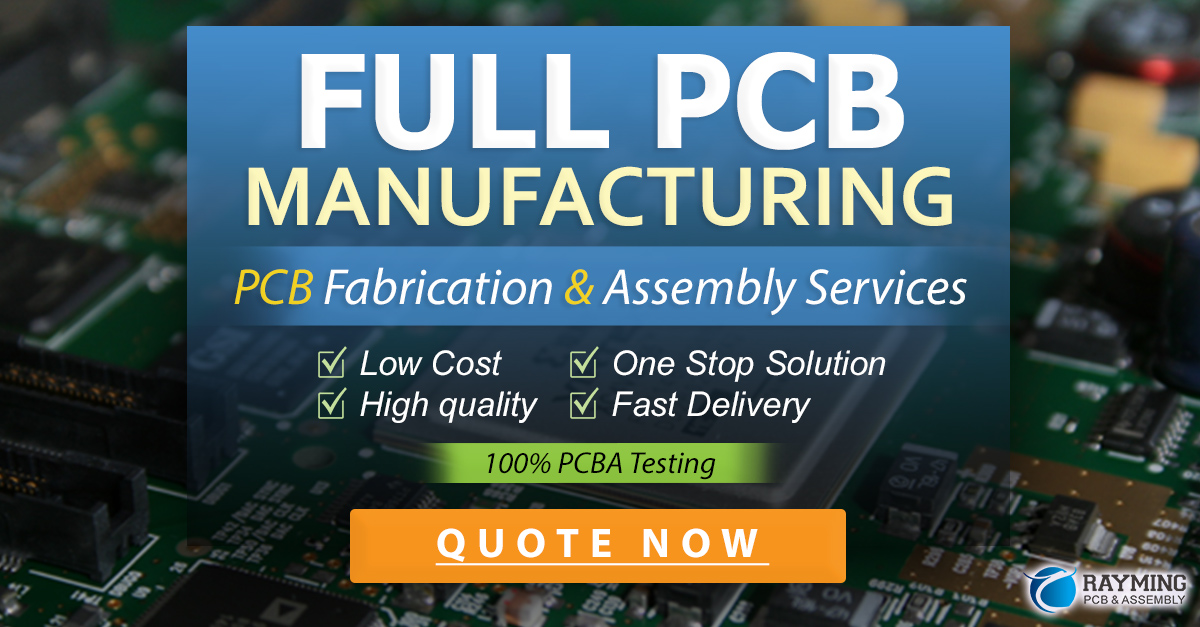
Challenges in Functional Testing
While functional testing is essential for ensuring the quality and reliability of assembled PCBs, it also presents certain challenges:
-
Test Coverage: Ensuring comprehensive test coverage can be difficult, especially for complex PCBs with numerous components and interconnections.
-
Test Fixture Design: Designing and fabricating custom test fixtures for ICT can be time-consuming and costly, particularly for low-volume production.
-
Test Program Development: Creating effective test programs requires skilled personnel and can be a time-intensive process.
-
Balancing Cost and Quality: Striking the right balance between the cost of functional testing and the desired level of quality can be challenging for PCB assembly service providers.
Best Practices for Functional Testing in PCB Assembly
To overcome these challenges and ensure the effectiveness of functional testing, PCB assembly service providers in China should adopt the following best practices:
-
Early Involvement: Engage the testing team early in the PCB design process to ensure testability and optimize test coverage.
-
Automated Testing: Utilize automated testing solutions to improve efficiency, accuracy, and repeatability.
-
Skilled Personnel: Invest in training and development to ensure that the testing team possesses the necessary skills and expertise.
-
Continuous Improvement: Regularly review and update test programs and procedures to incorporate lessons learned and industry best practices.
The Future of Functional Testing in PCB Assembly
As technology continues to advance and electronic devices become increasingly complex, the importance of functional testing in PCB assembly will only grow. Some of the trends shaping the future of functional testing include:
-
Industry 4.0: The integration of smart technologies, such as the Internet of Things (IoT) and artificial intelligence (AI), will enable more advanced and automated testing solutions.
-
5G and High-Speed Applications: The growing demand for high-speed, low-latency applications will require more stringent testing to ensure signal integrity and performance.
-
Miniaturization: As electronic devices become smaller and more compact, functional testing will need to adapt to the challenges posed by reduced test access and increased component density.
-
Environmental Considerations: With the increasing focus on sustainability and eco-friendly practices, functional testing will need to incorporate environmental testing to ensure compliance with relevant regulations and standards.
Choosing the Right PCB Assembly Service Provider in China
When selecting a PCB assembly service provider in China, it is essential to consider their functional testing capabilities and expertise. Some key factors to evaluate include:
-
Testing Infrastructure: Ensure that the service provider has the necessary equipment and facilities to perform comprehensive functional testing.
-
Expertise and Experience: Look for a provider with a proven track record in functional testing and experience with similar projects.
-
Quality Management System: Verify that the provider has a robust quality management system in place, such as ISO 9001 certification.
-
Communication and Support: Choose a provider that offers clear communication channels and responsive support throughout the assembly and testing process.
Conclusion
Functional testing is a vital component of PCB assembly services in China, ensuring the quality, reliability, and performance of electronic devices. By understanding the importance of functional testing, adopting best practices, and selecting the right service provider, businesses can leverage the expertise and capabilities of China’s PCB assembly industry to bring their products to market successfully.
Frequently Asked Questions (FAQ)
-
Q: What is the difference between functional testing and other types of testing, such as visual inspection or X-ray testing?
A: Functional testing focuses on verifying the actual performance and functionality of the assembled PCB, while visual inspection and X-ray testing primarily address the physical aspects, such as component placement and solder joint quality. -
Q: Is functional testing necessary for all PCB assembly projects?
A: While the extent and complexity of functional testing may vary depending on the specific requirements of the project, it is generally recommended to perform some level of functional testing to ensure the quality and reliability of the assembled PCBs. -
Q: How long does functional testing typically take?
A: The duration of functional testing depends on various factors, such as the complexity of the PCB, the type of testing performed, and the test coverage required. It can range from a few minutes to several hours or even days for more extensive testing. -
Q: Can functional testing be performed in-house, or is it better to outsource to a PCB assembly service provider?
A: Outsourcing functional testing to a specialized PCB assembly service provider is often more cost-effective and efficient, as they have the necessary equipment, expertise, and resources to perform comprehensive testing. -
Q: How can I ensure that my PCB assembly project receives adequate functional testing when working with a service provider in China?
A: Communicate your functional testing requirements clearly with the service provider, and verify their testing capabilities and expertise before engaging in a project. Establish clear quality criteria and maintain open communication throughout the assembly and testing process to ensure that your expectations are met.
Type of Functional Testing | Description | Benefits |
---|---|---|
In-Circuit Testing (ICT) | Uses a bed of nails fixture to test individual components and connectivity | Comprehensive testing of component functionality and interconnections |
Flying Probe Testing | Utilizes mobile probes to test the PCB without a custom fixture | Flexible and cost-effective for low-volume production or prototypes |
Boundary Scan Testing (JTAG) | Tests the functionality of digital components and interconnections using a test access port | Effective for testing complex digital circuits |
Functional Circuit Testing | Applies input signals to the PCB and measures output to verify overall functionality | Ensures the PCB functions as intended in a real-world scenario |
Leave a Reply