Introduction to PCB Testing
Printed Circuit Boards (PCBs) are the backbone of modern electronics. They are used in virtually every electronic device, from smartphones and laptops to medical equipment and aerospace systems. As such, ensuring the quality and reliability of PCBs is critical to the success of any electronic product. This is where PCB testing comes in.
PCB testing is the process of verifying that a PCB functions as intended and meets the required specifications. It involves a series of tests and inspections that are performed at various stages of the manufacturing process to identify and correct any defects or issues that may affect the performance or reliability of the PCB.
Types of PCB Testing
There are several types of PCB testing that are commonly used in the industry. These include:
-
Visual Inspection: This is the first step in PCB testing and involves a visual examination of the PCB for any obvious defects or issues, such as scratches, dents, or missing components.
-
Automated Optical Inspection (AOI): This is a more advanced form of visual inspection that uses cameras and image processing software to automatically detect and classify defects on the PCB.
-
In-Circuit Testing (ICT): This involves using a bed-of-nails fixture to make electrical contact with specific points on the PCB and verify that the components are correctly installed and functioning.
-
Flying Probe Testing: This is similar to ICT but uses movable probes instead of a fixed fixture to make contact with the PCB. This allows for more flexibility in testing different PCB designs.
-
Functional Testing: This involves testing the PCB under real-world operating conditions to verify that it functions as intended and meets the required specifications.
Importance of Functional Testing
Functional testing is a critical step in the PCB manufacturing process. It is the final test that is performed before the PCB is shipped to the customer and is designed to verify that the PCB functions as intended in its intended operating environment.
There are several reasons why functional testing is so important:
-
Verifying Functionality: Functional testing is the only way to verify that the PCB actually works as intended. It tests the PCB under real-world operating conditions and verifies that it performs all of its intended functions correctly.
-
Catching Defects: Functional testing can catch defects that may have been missed by earlier tests, such as issues with signal integrity or power delivery.
-
Ensuring Reliability: Functional testing helps ensure that the PCB will be reliable in the field. By testing the PCB under a range of operating conditions, it can identify any potential issues that may affect its long-term reliability.
-
Meeting Specifications: Functional testing verifies that the PCB meets all of the required specifications, such as power consumption, signal integrity, and EMI/EMC compliance.
Functional Testing Methods
There are several methods that can be used for functional testing of PCBs. The choice of method will depend on the specific requirements of the PCB and the intended application. Some common functional testing methods include:
-
Boundary Scan Testing: This involves using a special test access port (TAP) on the PCB to test the interconnections between components and verify that they are functioning correctly.
-
Functional Probe Testing: This involves using probes to apply signals to specific points on the PCB and measuring the response to verify that the PCB is functioning correctly.
-
Hot Mock-up Testing: This involves testing the PCB in a simulated operating environment that mimics the actual operating conditions of the intended application.
-
Burn-in Testing: This involves running the PCB at elevated temperatures for an extended period of time to identify any potential reliability issues.
Functional Testing Process
The functional testing process typically involves the following steps:
-
Test Planning: The first step is to develop a comprehensive test plan that outlines the specific tests that will be performed, the test conditions, and the acceptance criteria.
-
Test Fixture Design: A custom test fixture may need to be designed and built to interface with the PCB and provide the necessary test signals and measurements.
-
Test Program Development: A test program must be developed to control the test equipment and automate the testing process.
-
Test Execution: The actual testing is performed according to the test plan, and the results are recorded and analyzed.
-
Debugging and Troubleshooting: If any issues are identified during testing, they must be debugged and troubleshot to determine the root cause and implement corrective actions.
-
Reporting and Documentation: The test results and any corrective actions are documented and reported to the relevant stakeholders.
Functional Testing Equipment
Functional testing requires specialized equipment to generate the necessary test signals and measure the response of the PCB. Some common types of functional testing equipment include:
Equipment | Description |
---|---|
Function Generator | Generates precise electrical signals to stimulate the PCB |
Oscilloscope | Measures and displays the electrical signals on the PCB |
Logic Analyzer | Captures and analyzes digital signals on the PCB |
Spectrum Analyzer | Measures the frequency content of signals on the PCB |
Power Supply | Provides power to the PCB during testing |
Temperature Chamber | Simulates different temperature conditions for testing |
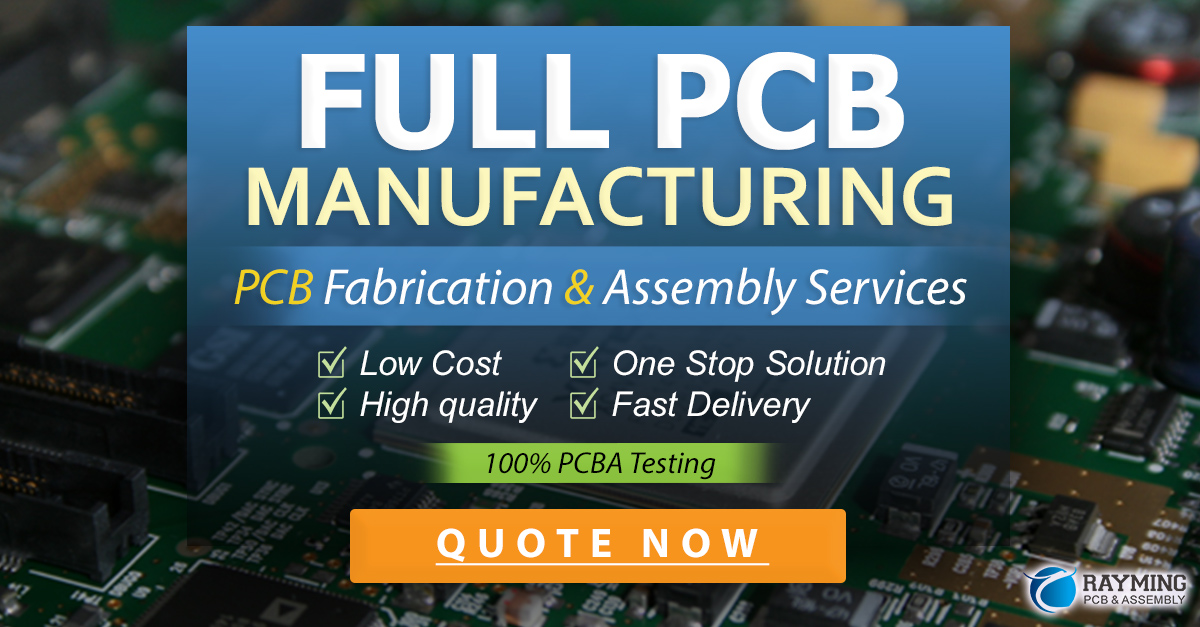
Benefits of Functional Testing
Functional testing provides a number of benefits to PCB manufacturers and their customers. Some of the key benefits include:
-
Improved Quality: Functional testing helps ensure that PCBs are of high quality and meet all of the required specifications. This reduces the risk of defects and failures in the field.
-
Reduced Costs: By catching defects early in the manufacturing process, functional testing can help reduce the costs associated with rework and scrap.
-
Faster Time-to-Market: Functional testing can help speed up the development and production of new PCB designs by identifying and correcting issues early in the process.
-
Enhanced Reliability: Functional testing helps ensure that PCBs will be reliable in the field, which is critical for applications where downtime is not an option.
-
Improved Customer Satisfaction: By delivering high-quality, reliable PCBs, manufacturers can improve customer satisfaction and build long-term relationships with their customers.
Challenges of Functional Testing
While functional testing provides many benefits, it also presents some challenges that manufacturers must overcome. Some of the key challenges include:
-
Complex Designs: As PCBs become more complex and dense, functional testing becomes more challenging. It can be difficult to access all of the necessary test points and generate the required test signals.
-
High-Speed Signals: Testing high-speed signals on PCBs requires specialized equipment and techniques to ensure accurate measurements and avoid signal integrity issues.
-
Environmental Factors: PCBs must be tested under a range of environmental conditions, such as temperature, humidity, and vibration, to ensure they will function reliably in the field.
-
Cost and Time: Functional testing can be time-consuming and expensive, particularly for complex PCB designs. Manufacturers must balance the need for thorough testing with the need to keep costs down and meet production schedules.
Best Practices for Functional Testing
To overcome these challenges and ensure effective functional testing, manufacturers should follow some best practices, such as:
-
Early Involvement: Involve the testing team early in the PCB design process to ensure that the design is testable and that the necessary test points and interfaces are included.
-
Comprehensive Test Planning: Develop a comprehensive test plan that covers all of the necessary tests and conditions, and ensure that all stakeholders are aligned on the plan.
-
Automated Testing: Use automated testing equipment and software to speed up the testing process and ensure consistent and accurate results.
-
Continuous Improvement: Continuously monitor and analyze test results to identify areas for improvement and implement corrective actions as needed.
-
Collaboration: Foster collaboration between the design, manufacturing, and testing teams to ensure that everyone is working towards the same goals and that issues are identified and resolved quickly.
Future Trends in Functional Testing
As PCB technology continues to evolve, so too will the functional testing process. Some of the future trends in functional testing include:
-
Increased Automation: The use of automated testing equipment and software will continue to grow as manufacturers look to speed up the testing process and reduce costs.
-
Artificial Intelligence: AI and machine learning techniques will be used to analyze test data and identify patterns and trends that can help optimize the testing process.
-
Digital Twin Technology: Digital twins, which are virtual replicas of physical PCBs, will be used to simulate and test PCB behavior under different conditions before physical prototypes are built.
-
5G and IoT: The growth of 5G networks and the Internet of Things (IoT) will drive demand for more complex and high-speed PCBs, which will require new testing techniques and equipment.
FAQ
-
What is functional testing in PCB manufacturing?
Functional testing is the process of verifying that a PCB functions as intended under real-world operating conditions. It is the final test performed before the PCB is shipped to the customer. -
Why is functional testing important?
Functional testing is important because it ensures that PCBs are of high quality, meet all required specifications, and will function reliably in the field. It helps catch defects that may have been missed by earlier tests and reduces the risk of failures and returns. -
What are some common methods used for functional testing?
Some common methods used for functional testing include boundary scan testing, functional probe testing, hot mock-up testing, and burn-in testing. The choice of method depends on the specific requirements of the PCB and the intended application. -
What equipment is used for functional testing?
Functional testing requires specialized equipment such as function generators, oscilloscopes, logic analyzers, spectrum analyzers, power supplies, and temperature chambers. This equipment is used to generate test signals, measure the response of the PCB, and simulate different operating conditions. -
What are some best practices for functional testing?
Some best practices for functional testing include involving the testing team early in the design process, developing a comprehensive test plan, using automated testing equipment and software, continuously monitoring and analyzing test results, and fostering collaboration between the design, manufacturing, and testing teams.
Conclusion
Functional testing is a critical step in the PCB manufacturing process that ensures the quality, reliability, and functionality of PCBs. It involves testing PCBs under real-world operating conditions to verify that they meet all required specifications and will function as intended in the field.
While functional testing presents some challenges, such as complex designs, high-speed signals, and environmental factors, manufacturers can overcome these challenges by following best practices such as early involvement, comprehensive test planning, automated testing, continuous improvement, and collaboration.
As PCB technology continues to evolve, functional testing will also evolve to keep pace with new requirements and trends. The use of automation, artificial intelligence, digital twin technology, and new testing techniques will help manufacturers meet the demands of emerging applications such as 5G and IoT.
By prioritizing functional testing and following best practices, PCB manufacturers can deliver high-quality, reliable products that meet the needs of their customers and drive business success.
Leave a Reply