What is FR4?
FR4 (Flame Retardant 4) is a type of printed circuit board (PCB) material that is widely used in the electronics industry. It is a composite material made of woven fiberglass cloth with an epoxy resin binder that is flame resistant. FR4 is known for its excellent mechanical, electrical, and thermal properties, making it a popular choice for a wide range of applications.
Properties of FR4
FR4 has several properties that make it an ideal material for PCBs:
-
High Strength and Stiffness: FR4 has a high strength-to-weight ratio and is very stiff, which makes it resistant to bending and twisting.
-
Flame Resistance: FR4 is flame retardant, which means it has a high resistance to catching fire and spreading flames.
-
Electrical Insulation: FR4 has excellent electrical insulation properties, which makes it suitable for use in electronic circuits.
-
Thermal Stability: FR4 has a high Glass Transition Temperature (Tg), which means it can withstand high temperatures without deforming or losing its mechanical properties.
-
Moisture Resistance: FR4 has a low moisture absorption rate, which helps to prevent warping and delamination of the PCB.
FR4 Quality Standards
To ensure consistent quality and performance of FR4 PCBs, several industry standards have been established. The most commonly used standards are:
IPC-4101
IPC-4101 is a specification that defines the requirements for laminate materials used in PCBs, including FR4. It covers the physical, mechanical, and electrical properties of the material, as well as its dimensional stability and processing requirements.
IPC-6012
IPC-6012 is a standard that defines the requirements for the qualification and performance of rigid printed boards, including those made with FR4. It covers the design, fabrication, and testing of PCBs to ensure they meet the specified requirements.
UL 94
UL 94 is a standard that measures the flammability of plastic materials used in electronic devices, including PCBs made with FR4. It classifies materials based on their ability to resist ignition and flame spread.
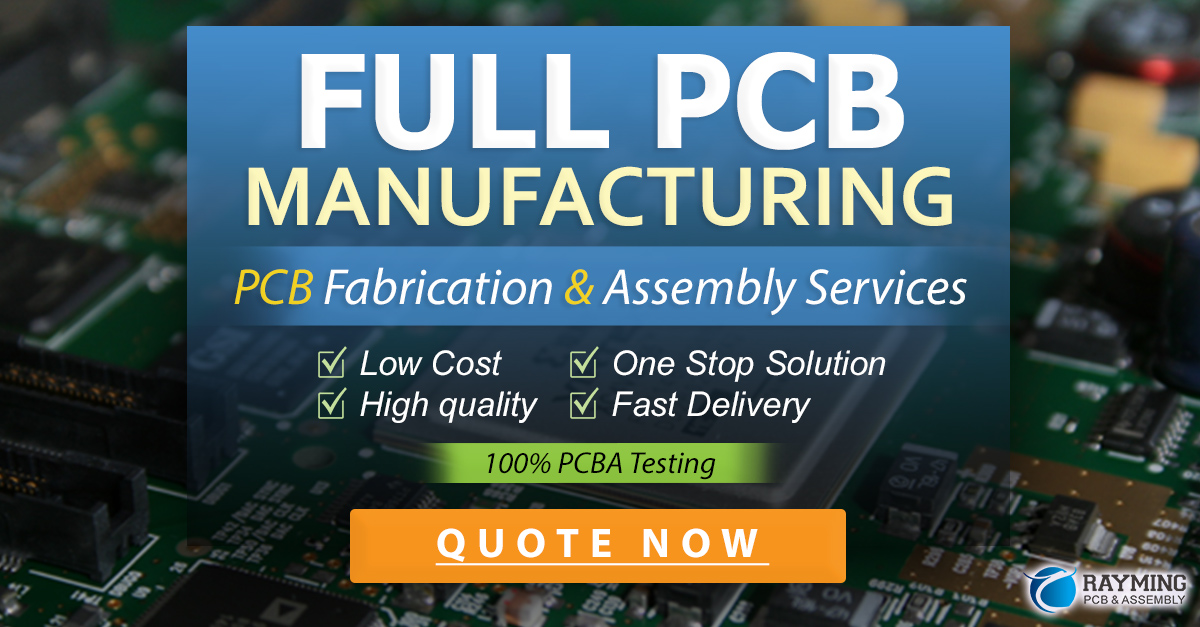
Factors Affecting FR4 Quality
Several factors can affect the quality of FR4 PCBs, including:
-
Material Composition: The quality of the fiberglass cloth and epoxy resin used in FR4 can vary depending on the manufacturer and the specific grade of material used.
-
Manufacturing Process: The manufacturing process used to produce FR4 PCBs can affect their quality. Factors such as the lamination process, drilling, and plating can all impact the final product.
-
Environmental Conditions: Exposure to high temperatures, humidity, and other environmental factors can degrade the quality of FR4 PCBs over time.
-
Handling and Storage: Improper handling and storage of FR4 PCBs can lead to damage such as scratches, dents, or warping.
Choosing High-Quality FR4
When selecting FR4 for your PCB project, there are several things to consider to ensure you are getting a high-quality product:
-
Reputable Manufacturer: Choose a reputable manufacturer with a track record of producing high-quality FR4 PCBs.
-
Material Grade: Select the appropriate grade of FR4 material for your application based on the required properties and performance.
-
Certifications: Look for FR4 materials and PCBs that are certified to meet industry standards such as IPC-4101, IPC-6012, and UL 94.
-
Testing and Inspection: Work with a manufacturer that has a robust testing and inspection process in place to ensure the quality of the final product.
Common FR4 Quality Issues
Even with careful selection and handling, FR4 PCBs can still experience quality issues. Some common problems include:
-
Delamination: Delamination occurs when the layers of the PCB separate due to poor bonding or exposure to high temperatures or humidity.
-
Warping: Warping can occur when the PCB is exposed to uneven temperatures or humidity, causing it to bend or twist.
-
Copper Foil Thickness Variation: Variations in the thickness of the copper foil can affect the electrical performance of the PCB.
-
Drilling and Plating Issues: Problems with drilling and plating, such as oversized holes or poor plating adhesion, can affect the reliability of the PCB.
Testing FR4 Quality
To ensure the quality of FR4 PCBs, several testing methods are used:
Visual Inspection
Visual inspection is used to check for any visible defects or damage to the PCB, such as scratches, dents, or discoloration.
Microsection Analysis
Microsection analysis involves cutting a cross-section of the PCB and examining it under a microscope to check for any internal defects or delamination.
Electrical Testing
Electrical testing is used to verify the electrical performance of the PCB, including its resistance, capacitance, and inductance.
Thermal Stress Testing
Thermal stress testing involves exposing the PCB to high temperatures to check for any deformation or delamination.
Maintaining FR4 Quality
To maintain the quality of FR4 PCBs over time, proper handling and storage are essential:
-
Handling: Always handle PCBs by the edges to avoid damaging the surface or components.
-
Storage: Store PCBs in a cool, dry place away from direct sunlight and sources of heat or humidity.
-
Packaging: Use appropriate packaging materials, such as anTI-STatic bags or boxes, to protect PCBs during storage and transportation.
FAQ
What does FR stand for in FR4?
FR stands for “Flame Retardant”. FR4 is a type of PCB material that is flame resistant.
What is the difference between FR4 and other PCB materials?
FR4 is a composite material made of woven fiberglass cloth with an epoxy resin binder. It has excellent mechanical, electrical, and thermal properties compared to other PCB materials such as phenolic paper or CEM.
Can FR4 PCBs be used for high-frequency applications?
Yes, FR4 PCBs can be used for high-frequency applications up to a few gigahertz. However, for very high-frequency applications, other materials such as Rogers or Teflon may be more suitable.
How can I ensure the quality of my FR4 PCBs?
To ensure the quality of your FR4 PCBs, choose a reputable manufacturer, select the appropriate grade of FR4 material, look for certifications, and work with a manufacturer that has a robust testing and inspection process in place.
How should I store my FR4 PCBs to maintain their quality?
Store your FR4 PCBs in a cool, dry place away from direct sunlight and sources of heat or humidity. Use appropriate packaging materials, such as anti-static bags or boxes, to protect them during storage and transportation.
Conclusion
FR4 is a high-quality PCB material that offers excellent mechanical, electrical, and thermal properties. To ensure the quality of FR4 PCBs, it is important to choose a reputable manufacturer, select the appropriate grade of material, and follow proper handling and storage procedures. By understanding the factors that affect FR4 quality and the testing methods used to verify it, you can ensure that your PCB project meets the highest standards of reliability and performance.
Property | Value |
---|---|
Dielectric Constant (at 1 MHz) | 4.2 – 4.5 |
Dissipation Factor (at 1 MHz) | 0.02 |
Dielectric Strength (kV/mm) | 20 – 28 |
Volume Resistivity (Mohm-cm) | 10^6 – 10^8 |
Surface Resistivity (Mohm) | 10^5 – 10^7 |
Thermal Conductivity (W/mK) | 0.3 – 0.4 |
Glass Transition Temperature (°C) | 130 – 140 |
CTE (ppm/°C) | 12 – 16 |
Moisture Absorption (%) | 0.1 – 0.3 |
Flexural Strength (MPa) | 415 – 480 |
Leave a Reply