Introduction to FR4 and Its Significance in PCB Manufacturing
FR4 (Flame Retardant 4) is a widely used material in the manufacturing of printed circuit boards (PCBs). It is a composite material composed of woven fiberglass cloth with an epoxy resin binder. FR4 has become the standard material for PCBs due to its excellent mechanical, electrical, and thermal properties. It offers good insulation, high strength, and dimensional stability, making it suitable for a wide range of applications.
Advantages of FR4 in PCB Manufacturing
- High mechanical strength and durability
- Excellent electrical insulation properties
- Good thermal stability and flame retardancy
- Dimensional stability and resistance to warping
- Cost-effective and readily available
The Need for FR4 Material Upgrade
As technology advances and electronic devices become more sophisticated, the demands on PCBs have increased. Higher operating temperatures, improved signal integrity, and better reliability are now essential requirements for modern PCBs. To meet these challenges, manufacturers have been exploring ways to upgrade the traditional FR4 material.
Limitations of Standard FR4
- Limited thermal stability at high temperatures
- Susceptibility to thermal expansion and warping
- Increased dielectric loss at higher frequencies
- Potential for signal integrity issues in high-speed applications
ALLPCB’s New Tg150 Covered FR4 Prototype
ALLPCB, a leading PCB manufacturer, has developed a new FR4 material upgrade called Tg150 Covered FR4. This innovative material aims to address the limitations of standard FR4 and provide enhanced performance for demanding applications.
Key Features of Tg150 Covered FR4
- Higher glass transition temperature (Tg) of 150°C
- Improved thermal stability and reduced thermal expansion
- Enhanced signal integrity and reduced dielectric loss
- Increased reliability and durability
- Compatibility with existing PCB manufacturing processes
Benefits of Tg150 Covered FR4 for PCB Designers and Manufacturers
- Ability to withstand higher operating temperatures
- Reduced risk of warping and dimensional changes
- Improved signal integrity for high-speed applications
- Extended product lifespan and reliability
- Seamless integration into existing PCB fabrication workflows
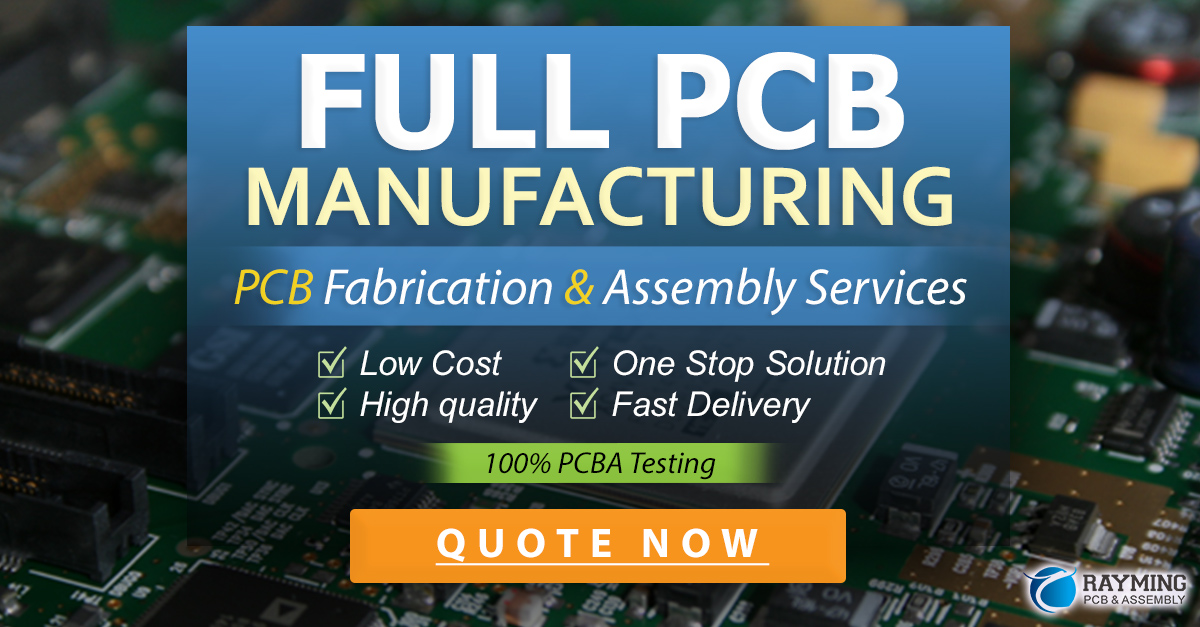
Comparison of Tg150 Covered FR4 with Standard FR4
To demonstrate the advantages of Tg150 Covered FR4, let’s compare its properties with those of standard FR4:
Property | Standard FR4 | Tg150 Covered FR4 |
---|---|---|
Glass Transition Temperature (Tg) | 130°C | 150°C |
Thermal Expansion Coefficient (CTE) | 14-16 ppm/°C | 12-14 ppm/°C |
Dielectric Constant (at 1 GHz) | 4.2-4.5 | 4.0-4.3 |
Dissipation Factor (at 1 GHz) | 0.02-0.03 | 0.01-0.02 |
Moisture Absorption | 0.15-0.20% | 0.10-0.15% |
As evident from the table, Tg150 Covered FR4 offers superior thermal stability, lower thermal expansion, improved dielectric properties, and reduced moisture absorption compared to standard FR4. These enhancements make Tg150 Covered FR4 an ideal choice for applications that demand higher performance and reliability.
Applications of Tg150 Covered FR4
Tg150 Covered FR4 is suitable for a wide range of applications that require enhanced thermal stability, signal integrity, and reliability. Some of the key application areas include:
- Automotive electronics
- Aerospace and defense systems
- High-speed communication networks
- Industrial control and automation
- Medical devices and equipment
Case Studies
To illustrate the practical benefits of Tg150 Covered FR4, let’s explore a couple of case studies:
Case Study 1: Automotive Engine Control Unit (ECU)
An automotive manufacturer was facing challenges with the reliability of their engine control units (ECUs) due to high operating temperatures and thermal cycling. By switching to Tg150 Covered FR4 for the ECU PCBs, they were able to:
- Improve the thermal stability of the ECUs
- Reduce the risk of warping and component failure
- Extend the lifespan of the ECUs
- Enhance the overall reliability of the automotive electronics system
Case Study 2: High-Speed Networking Equipment
A networking equipment manufacturer was experiencing signal integrity issues and increased dielectric loss in their high-speed PCBs. By adopting Tg150 Covered FR4, they were able to:
- Minimize signal distortion and attenuation
- Reduce crosstalk and electromagnetic interference (EMI)
- Improve the overall signal integrity of the PCBs
- Achieve higher data transmission rates and bandwidth
These case studies demonstrate the real-world benefits of Tg150 Covered FR4 in demanding applications where standard FR4 may fall short.
Implementing Tg150 Covered FR4 in Your PCB Designs
If you’re considering using Tg150 Covered FR4 for your PCB designs, here are some tips to help you get started:
- Consult with your PCB manufacturer to ensure they offer Tg150 Covered FR4 and have experience working with it.
- Update your PCB design software libraries to include Tg150 Covered FR4 material properties.
- Review your PCB layout and design rules to optimize for the enhanced properties of Tg150 Covered FR4.
- Conduct thorough testing and validation to ensure your PCB design meets the desired performance and reliability requirements.
By following these guidelines and collaborating closely with your PCB manufacturer, you can successfully implement Tg150 Covered FR4 in your PCB designs and take advantage of its superior properties.
Frequently Asked Questions (FAQ)
-
Q: Is Tg150 Covered FR4 compatible with standard PCB manufacturing processes?
A: Yes, Tg150 Covered FR4 is fully compatible with existing PCB manufacturing processes, including drilling, plating, and soldering. It does not require any special equipment or techniques. -
Q: How does the cost of Tg150 Covered FR4 compare to standard FR4?
A: The cost of Tg150 Covered FR4 is slightly higher than standard FR4 due to its enhanced properties. However, the improved performance and reliability often justify the additional cost, especially in demanding applications. -
Q: Can Tg150 Covered FR4 be used for multilayer PCBs?
A: Yes, Tg150 Covered FR4 is suitable for both single-layer and multilayer PCBs. Its improved thermal stability and dimensional stability make it particularly beneficial for complex multilayer designs. -
Q: Is Tg150 Covered FR4 suitable for lead-free soldering processes?
A: Yes, Tg150 Covered FR4 is compatible with lead-free soldering processes. Its higher glass transition temperature (Tg) helps prevent delamination and other defects during the soldering process. -
Q: How can I learn more about ALLPCB’s Tg150 Covered FR4 and request samples?
A: You can visit ALLPCB’s website or contact their sales team directly to learn more about Tg150 Covered FR4 and request samples for evaluation. They will be happy to provide additional information and support for your specific requirements.
Conclusion
The introduction of Tg150 Covered FR4 by ALLPCB represents a significant advancement in PCB material technology. With its enhanced thermal stability, improved signal integrity, and increased reliability, Tg150 Covered FR4 addresses the limitations of standard FR4 and meets the demands of modern electronics.
By upgrading to Tg150 Covered FR4, PCB designers and manufacturers can unlock new possibilities for their products, especially in challenging applications such as automotive, aerospace, and high-speed communications. The improved performance and reliability offered by Tg150 Covered FR4 can lead to longer product lifespans, reduced maintenance costs, and enhanced customer satisfaction.
As the electronics industry continues to evolve, materials like Tg150 Covered FR4 will play a crucial role in enabling the next generation of PCBs. By staying at the forefront of material innovation, ALLPCB is committed to providing its customers with the tools and solutions they need to succeed in an increasingly competitive market.
If you’re looking to upgrade your PCB designs and take advantage of the benefits of Tg150 Covered FR4, ALLPCB is ready to support you every step of the way. With their expertise, experience, and dedication to quality, ALLPCB is your trusted partner for all your PCB manufacturing needs.
Leave a Reply