Introduction to Fly Buck Converters and PCB layout
Fly buck converters, also known as isolated buck converters, are switching Voltage Regulators that provide electrical isolation between the input and output. They are commonly used in applications requiring isolation such as industrial systems, medical devices, and power supplies.
Proper PCB layout is critical for the optimal performance and reliability of fly buck converters. A well-designed layout minimizes noise, reduces electromagnetic interference (EMI), improves thermal management, and ensures the converter operates efficiently and stably.
In this article, we will dive into key considerations and best practices for fly buck converter PCB layout. By following these tips, you can create robust and high-performance designs.
Key Components of a Fly Buck Converter
Before discussing layout tips, let’s review the main components of a typical fly buck converter:
- Power Stage:
- Power MOSFETs or IGBTs
- Rectifier diodes
- Inductor
-
Input and output capacitors
-
Flyback Transformer:
- Provides galvanic isolation between input and output
-
Steps down or steps up the voltage
-
Controller IC:
- Generates PWM signals to drive the power switches
-
Implements control loops and protection features
-
Auxiliary Components:
- Snubber Circuits
- Gate drive circuitry
- Feedback and sensing networks
Understanding the role of each component is essential for making informed layout decisions.
Power Stage Layout Considerations
Minimizing Loop Areas
One of the primary goals in fly buck converter layout is to minimize the loop areas of high-frequency current paths. Large loop areas can lead to increased noise, EMI, and ringing. To minimize loop areas:
- Place the power switches, rectifier diodes, and capacitors as close together as possible.
- Use wide and short traces for high-current paths to reduce inductance.
- Arrange components to create compact loops for the power stage.
Reducing Parasitic Inductance
Parasitic inductance in the power stage can cause voltage spikes and ringing, which can stress components and degrade performance. To reduce parasitic inductance:
- Use multiple vias for ground connections to create low-impedance paths.
- Minimize the distance between the power switches and the input capacitor.
- Consider using a ground plane to provide a low-impedance return path.
Thermal Management
Proper thermal management is crucial for the reliability and longevity of the fly buck converter. To improve thermal performance:
- Provide adequate copper area for heat dissipation, especially for power MOSFETs and rectifier diodes.
- Use thermal vias to transfer heat from components to the ground plane or heatsink.
- Consider using a heatsink or Thermal Pad for high-power components.
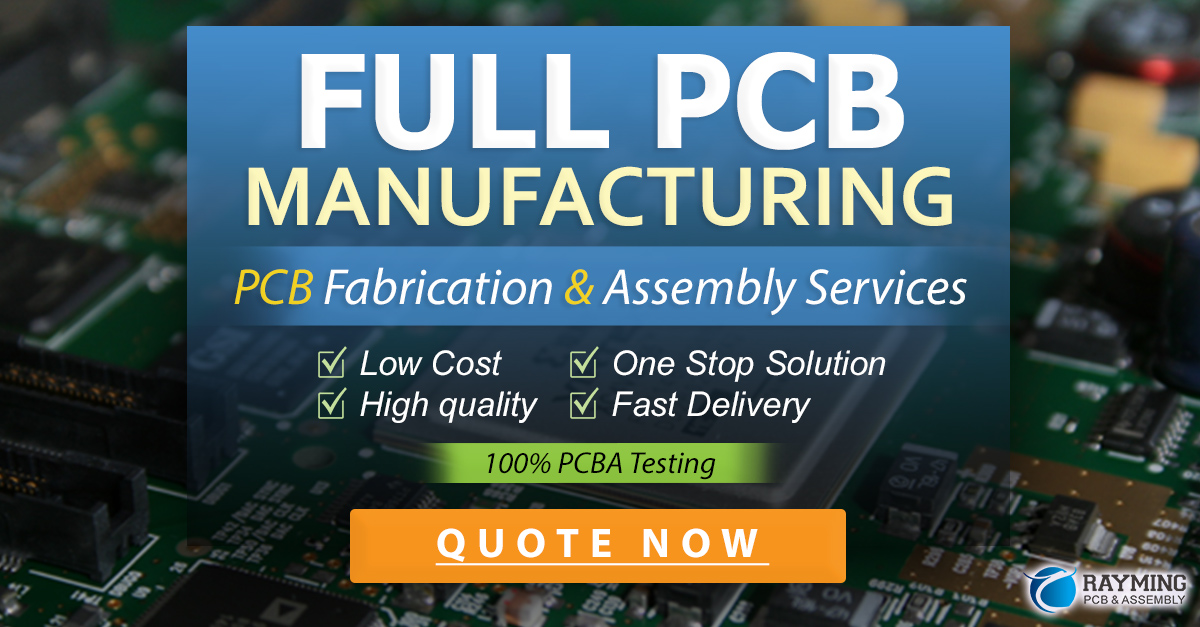
Flyback Transformer Layout
The flyback transformer is a critical component in the fly buck converter and requires careful layout considerations.
Minimizing Leakage Inductance
Leakage inductance in the transformer can cause voltage spikes and increase EMI. To minimize leakage inductance:
- Keep the primary and secondary windings as close together as possible.
- Use a compact winding structure, such as a sectioned or interleaved winding.
- Minimize the distance between the transformer and the power switches.
Providing Adequate Clearance
Proper clearance between the primary and secondary windings is essential for maintaining isolation and preventing arcing. Follow these guidelines:
- Adhere to the minimum clearance requirements specified by safety standards.
- Use appropriate insulation materials between windings.
- Avoid routing traces or components too close to the transformer windings.
Controller and Signal Layout
Separating Analog and Digital Grounds
To minimize noise coupling between analog and digital circuits, it’s important to separate their ground planes.
- Use separate ground planes for analog and digital sections of the controller IC.
- Connect the analog and digital grounds at a single point, typically near the controller IC.
Routing Sensitive Signals
Proper routing of sensitive signals, such as feedback and sensing paths, is crucial for accurate regulation and noise immunity.
- Route sensitive signals away from high-current paths and noisy components.
- Use shielded traces or guard rings to isolate sensitive signals from noise sources.
- Keep feedback traces as short as possible to minimize noise pickup.
Decoupling and Filtering
Adequate decoupling and filtering are necessary to provide clean power to the controller IC and reduce noise.
- Place decoupling capacitors close to the controller IC’s power pins.
- Use appropriate filtering techniques, such as ferrite beads or inductors, for noise suppression.
EMI Considerations
Fly buck converters can generate significant EMI due to their switching nature. To mitigate EMI:
- Use proper grounding techniques, such as a low-impedance ground plane.
- Implement input and output filtering to attenuate high-frequency noise.
- Minimize the loop areas of high-frequency current paths.
- Consider using shielding techniques, such as a Faraday cage, for sensitive components.
Layout Simulation and Verification
Before finalizing the PCB layout, it’s valuable to perform simulations and verifications to identify potential issues.
- Use PCB layout software with built-in simulation tools to analyze signal integrity and EMI.
- Perform thermal simulations to ensure adequate heat dissipation and identify hot spots.
- Conduct design rule checks (DRC) to verify that the layout meets manufacturing constraints.
Frequently Asked Questions (FAQ)
1. What is the importance of minimizing loop areas in fly buck converter layout?
Minimizing loop areas in fly buck converter layout is crucial for reducing noise, EMI, and ringing. Large loop areas can lead to increased high-frequency current loops, which can cause electromagnetic radiation and affect the performance and reliability of the converter.
2. How can I reduce parasitic inductance in the power stage?
To reduce parasitic inductance in the power stage, you can use multiple vias for ground connections, minimize the distance between power switches and input capacitors, and consider using a ground plane. These techniques help create low-impedance paths and minimize the inductance associated with component interconnections.
3. What are the considerations for flyback transformer layout?
When laying out the flyback transformer, it’s important to minimize leakage inductance by keeping the primary and secondary windings close together and using a compact winding structure. Additionally, provide adequate clearance between windings to maintain isolation and prevent arcing. Follow the minimum clearance requirements specified by safety standards.
4. How can I separate analog and digital grounds in the controller section?
To separate analog and digital grounds, use separate ground planes for the analog and digital sections of the controller IC. Connect these grounds at a single point, typically near the controller IC. This helps minimize noise coupling between the analog and digital circuits.
5. What are some techniques to mitigate EMI in fly buck converters?
To mitigate EMI in fly buck converters, use proper grounding techniques like a low-impedance ground plane, implement input and output filtering to attenuate high-frequency noise, minimize loop areas of high-frequency current paths, and consider shielding techniques such as a Faraday cage for sensitive components. These measures help reduce electromagnetic radiation and improve the converter’s EMI performance.
Conclusion
Proper PCB layout is essential for achieving optimal performance, reliability, and EMI mitigation in fly buck converters. By following the tips and best practices discussed in this article, you can design robust and efficient fly buck converter PCBs.
Remember to focus on minimizing loop areas, reducing parasitic inductance, ensuring proper thermal management, and paying attention to the layout of the flyback transformer and controller sections. Additionally, consider EMI mitigation techniques and perform layout simulations and verifications to identify and address potential issues early in the design process.
By mastering the art of fly buck converter PCB layout, you can develop high-quality power conversion solutions that meet the demands of various applications while ensuring reliable operation and compliance with relevant standards.
Leave a Reply