Introduction to Flexible PCBs
Flexible printed circuit boards (PCBs) have gained significant popularity in recent years due to their unique characteristics and versatility in various applications. Unlike traditional rigid PCBs, flexible PCBs offer the ability to bend, twist, and conform to different shapes, making them ideal for devices that require compact packaging, lightweight design, and enhanced reliability. In this article, we will explore the key characteristics of flexible PCBs that contribute to their widespread adoption and discuss their advantages in different industries.
What is a Flexible PCB?
A flexible PCB, also known as a flex circuit or flex PCB, is a type of printed circuit board that consists of a thin, flexible substrate made of materials such as polyimide or polyester. The substrate is laminated with copper traces and other components, allowing for electrical connectivity and signal transmission. The flexibility of the substrate enables the PCB to be bent, folded, or twisted without compromising its functionality or reliability.
Advantages of Flexible PCBs over Rigid PCBs
Characteristic | Flexible PCB | Rigid PCB |
---|---|---|
Flexibility | High | Low |
Weight | Lightweight | Heavy |
Thickness | Thin | Thick |
Durability | High | Moderate |
Space Savings | Significant | Limited |
Flexible PCBs offer several advantages over traditional rigid PCBs:
- Flexibility and Conformity: Flex PCBs can bend and conform to various shapes, allowing for more compact and space-saving designs.
- Lightweight: The thin and lightweight nature of flex PCBs makes them ideal for portable and wearable devices.
- Durability: Flex PCBs can withstand repeated bending and flexing without damage, enhancing the overall reliability of the device.
- Reduced Assembly Costs: Flex PCBs can replace multiple rigid PCBs and connectors, simplifying the assembly process and reducing costs.
Key Characteristics of Flexible PCBs
1. Flexibility and Bendability
One of the most significant characteristics of flexible PCBs is their ability to bend and flex without breaking or losing functionality. The flexibility is achieved through the use of thin, pliable substrate materials such as polyimide or polyester. These materials have excellent mechanical properties, allowing them to withstand repeated bending and flexing cycles without cracking or delaminating.
The flexibility of flex PCBs is quantified by the minimum bend radius, which represents the smallest radius to which the PCB can be bent without causing damage. The minimum bend radius depends on factors such as the substrate material, copper thickness, and the number of layers in the PCB. Typical minimum bend radii for flex PCBs range from 6 to 10 times the total thickness of the board.
Advantages of Flexibility in Different Applications
The flexibility of flex PCBs enables their use in various applications where traditional rigid PCBs may not be suitable:
- Wearable Devices: Flex PCBs can conform to the shape of the human body, making them ideal for wearable devices such as smartwatches, fitness trackers, and medical monitoring systems.
- Aerospace and Defense: Flex PCBs can withstand vibrations and shocks better than rigid PCBs, making them suitable for aerospace and defense applications where reliability is critical.
- Automotive Electronics: Flex PCBs can be bent and routed in tight spaces within vehicles, enabling more compact and lightweight designs for automotive electronics.
2. Lightweight and Thin Profile
Another key characteristic of flexible PCBs is their lightweight and thin profile. Flex PCBs are typically much thinner than rigid PCBs, with thicknesses ranging from 0.05mm to 0.3mm. The thin profile is achieved by using thin substrate materials and minimizing the number of layers in the PCB.
The lightweight nature of flex PCBs is a result of the reduced material usage compared to rigid PCBs. The combination of thin substrate materials and fewer layers contributes to the overall weight reduction. This characteristic is particularly advantageous in applications where weight is a critical factor, such as aerospace, drones, and portable devices.
Benefits of Lightweight and Thin Profile
The lightweight and thin profile of flex PCBs offer several benefits:
- Reduced Weight: Lightweight flex PCBs contribute to the overall weight reduction of the device, which is crucial in applications where weight is a constraint, such as aerospace and portable devices.
- Space Savings: The thin profile of flex PCBs allows for more compact packaging and space savings, enabling the development of smaller and more streamlined devices.
- Improved Portability: Lightweight and thin flex PCBs enhance the portability of devices, making them easier to carry and use on the go.
3. High Reliability and Durability
Flexible PCBs are known for their high reliability and durability, even under challenging environmental conditions. The key factors contributing to the reliability and durability of flex PCBs include:
- Robust Materials: Flex PCBs use materials such as polyimide, which has excellent thermal stability, chemical resistance, and mechanical strength. These properties enable flex PCBs to withstand harsh environments and maintain their integrity over time.
- Reduced Interconnections: Flex PCBs can replace multiple rigid PCBs and connectors, reducing the number of interconnections and potential failure points. This simplification of the assembly leads to enhanced reliability.
- Resistance to Vibration and Shock: The flexibility of flex PCBs allows them to absorb vibrations and shocks better than rigid PCBs. This characteristic is particularly beneficial in applications where the device is subjected to constant motion or impact.
Reliability Testing of Flexible PCBs
To ensure the reliability and durability of flexible PCBs, manufacturers conduct various tests:
Test | Purpose |
---|---|
Bend Test | Evaluates the flexibility and durability of the PCB |
Thermal Cycling Test | Assesses the PCB’s ability to withstand temperature variations |
Humidity Test | Checks the PCB’s resistance to moisture and humidity |
Vibration and Shock Test | Evaluates the PCB’s performance under vibration and shock |
These tests help validate the reliability and durability of flex PCBs, ensuring they can withstand the intended application environment.
4. Enhanced Signal Integrity
Flexible PCBs offer enhanced signal integrity compared to traditional rigid PCBs. The key factors contributing to improved signal integrity in flex PCBs include:
- Reduced Crosstalk: Flex PCBs allow for controlled impedance routing, which minimizes crosstalk between adjacent traces. By maintaining consistent trace spacing and width, flex PCBs can reduce electromagnetic interference (EMI) and ensure cleaner signal transmission.
- Shorter Signal Paths: The ability to bend and fold flex PCBs enables shorter signal paths between components. Shorter signal paths result in reduced signal attenuation, distortion, and delay, leading to improved signal quality.
- Elimination of Connectors: Flex PCBs can eliminate the need for connectors between multiple rigid PCBs, reducing signal loss and reflections associated with connector interfaces. This characteristic is particularly beneficial in high-speed and high-frequency applications.
Signal Integrity Simulation and Analysis
To optimize signal integrity in flex PCBs, designers use simulation and analysis tools:
- Signal Integrity Simulation: Software tools simulate the signal behavior in flex PCBs, considering factors such as trace geometry, material properties, and termination conditions. These simulations help identify potential signal integrity issues and optimize the PCB design.
- Eye Diagram Analysis: Eye diagrams provide a visual representation of the signal quality in high-speed digital systems. By analyzing eye diagrams, designers can assess the signal integrity and make necessary adjustments to improve the signal quality.
5. Design Flexibility and Customization
Flexible PCBs offer significant design flexibility and customization options compared to rigid PCBs. The ability to bend, fold, and shape flex PCBs allows for more creative and space-saving designs. Designers can route the flex PCB in three-dimensional space, enabling more efficient use of available space within the device.
Flex PCBs can be customized to meet specific application requirements. Some common customization options include:
- Multilayer Flex PCBs: Flex PCBs can have multiple layers, allowing for more complex routing and higher component density. Multilayer flex PCBs can be designed with a combination of flexible and rigid layers, known as rigid-flex PCBs, for added functionality and mechanical support.
- Customized Shapes and Cutouts: Flex PCBs can be designed with custom shapes and cutouts to fit the specific mechanical requirements of the device. This customization enables more efficient use of space and reduces the overall size of the device.
- Selective Stiffening: Certain areas of the flex PCB can be selectively stiffened using materials such as polyimide or epoxy. Selective stiffening provides additional mechanical support in areas where components are mounted or where the PCB needs to maintain a specific shape.
Design Considerations for Flexible PCBs
Designing flexible PCBs requires careful consideration of several factors:
- Bend Radius: The minimum bend radius of the flex PCB must be considered to ensure the PCB can withstand the required bending without damage.
- Strain Relief: Proper strain relief techniques, such as the use of stiffeners or adhesives, should be employed to prevent excessive stress on the components and solder joints during bending.
- Component Placement: Components should be placed strategically on the flex PCB to minimize stress during bending. Placing components in the neutral bend axis or using flexible components can help mitigate the risk of component failure.
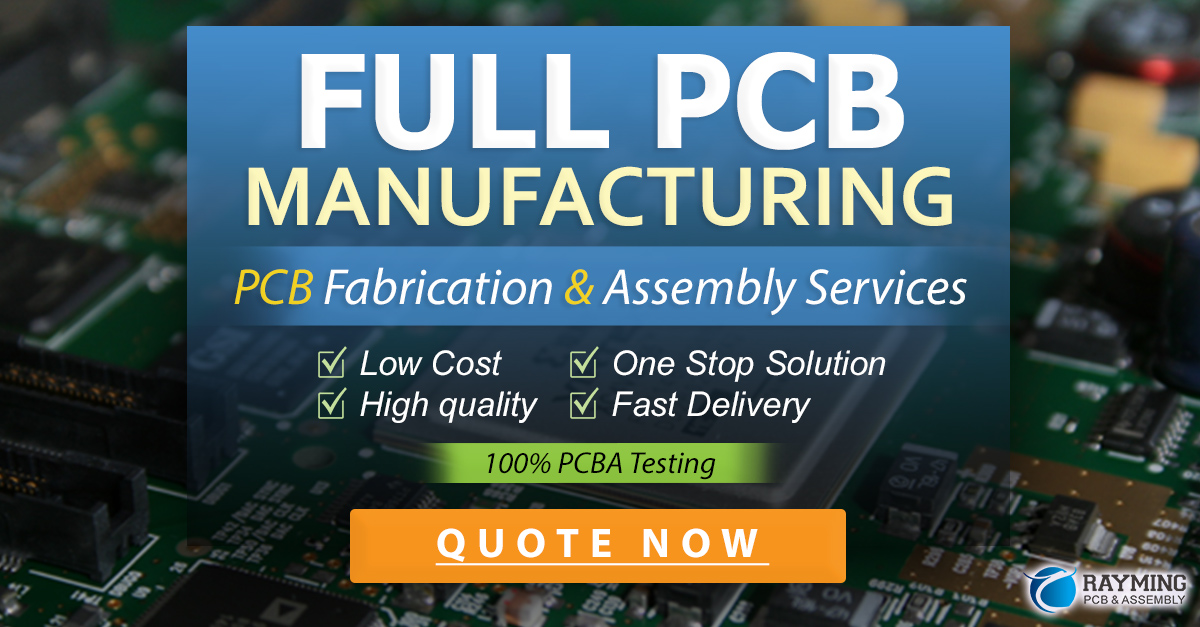
Applications of Flexible PCBs
Flexible PCBs find applications in various industries due to their unique characteristics and benefits. Some common applications include:
1. Consumer Electronics
Flex PCBs are widely used in consumer electronics, such as smartphones, tablets, and wearable devices. The flexibility and thin profile of flex PCBs enable compact and lightweight designs, making devices more portable and user-friendly. Flex PCBs also allow for the integration of advanced features, such as curved displays and flexible sensors, enhancing the user experience.
2. Medical Devices
Flex PCBs are increasingly used in medical devices, particularly in implantable and wearable medical electronics. The biocompatibility and flexibility of flex PCBs make them suitable for devices that come in direct contact with the human body. Flex PCBs enable the development of compact and lightweight medical devices, such as pacemakers, hearing aids, and insulin pumps, improving patient comfort and mobility.
3. Automotive Electronics
Flexible PCBs are used in various automotive electronics applications, such as infotainment systems, instrument clusters, and sensors. The ability to route flex PCBs in tight spaces within the vehicle enables more compact and lightweight designs. Flex PCBs also offer improved reliability and durability, withstanding the harsh environmental conditions and vibrations encountered in automotive applications.
4. Aerospace and Defense
Flex PCBs are used in aerospace and defense applications due to their lightweight, high reliability, and ability to withstand harsh environments. Flex PCBs are used in avionics systems, satellites, and military equipment, where weight reduction and reliability are critical. The flexibility of flex PCBs allows for more efficient packaging and routing of electronics in space-constrained applications.
5. Industrial Equipment
Flex PCBs are used in various industrial equipment, such as robotics, automation systems, and control panels. The flexibility and durability of flex PCBs enable their use in moving parts and harsh industrial environments. Flex PCBs can withstand repeated flexing, vibrations, and extreme temperatures, ensuring reliable operation in demanding industrial applications.
Frequently Asked Questions (FAQ)
1. What is the difference between a flexible PCB and a rigid PCB?
A flexible PCB is made of a thin, flexible substrate material that allows it to bend and conform to different shapes, while a rigid PCB is made of a solid, non-flexible substrate. Flex PCBs offer advantages such as flexibility, lightweight, and improved durability compared to rigid PCBs.
2. Can flexible PCBs be used in high-temperature applications?
Yes, flexible PCBs can be designed to withstand high temperatures. The choice of substrate material, such as polyimide, and the use of high-temperature solder masks and components enable flex PCBs to operate reliably in high-temperature environments.
3. How do flexible PCBs improve signal integrity?
Flexible PCBs offer improved signal integrity through controlled impedance routing, reduced crosstalk, shorter signal paths, and the elimination of connectors. These characteristics minimize signal distortion, attenuation, and interference, resulting in cleaner and more reliable signal transmission.
4. Can flexible PCBs be made with multiple layers?
Yes, flexible PCBs can be made with multiple layers, known as multilayer flex PCBs. Multilayer flex PCBs allow for more complex routing and higher component density. They can also be combined with rigid layers to form rigid-flex PCBs for added functionality and mechanical support.
5. How are flexible PCBs tested for reliability and durability?
Flexible PCBs undergo various reliability and durability tests, such as bend tests, thermal cycling tests, humidity tests, and vibration and shock tests. These tests evaluate the PCB’s ability to withstand the intended application environment and ensure reliable operation over the expected lifecycle of the device.
Conclusion
Flexible PCBs have gained significant popularity due to their unique characteristics and benefits, such as flexibility, lightweight, thin profile, high reliability, and enhanced signal integrity. These characteristics enable the development of compact, lightweight, and durable devices across various industries, including consumer electronics, medical devices, automotive electronics, aerospace and defense, and industrial equipment.
The design flexibility and customization options offered by flex PCBs allow for creative and space-saving designs, enabling more efficient use of available space within devices. However, designing flex PCBs requires careful consideration of factors such as bend radius, strain relief, and component placement to ensure reliable operation and longevity.
As technology continues to evolve and the demand for compact and reliable electronics grows, flexible PCBs will play an increasingly important role in shaping the future of electronic devices. With their unique characteristics and benefits, flex PCBs offer a versatile and reliable solution for a wide range of applications, driving innovation and enabling the development of advanced and user-friendly devices.
Leave a Reply