Introduction to OSP-PCB
Printed Circuit Boards (PCBs) are essential components in modern electronics, providing a platform for interconnecting and supporting electronic components. As the demand for PCBs continues to grow, there is an increasing focus on developing environment-friendly manufacturing processes. One such process is Organic Solderability Preservative (OSP), which has gained popularity due to its eco-friendly nature and excellent performance in preserving the solderability of copper surfaces on PCBs.
What is OSP?
OSP is a chemical coating applied to the exposed copper surfaces of a PCB to prevent oxidation and maintain solderability during storage and assembly. The coating is typically composed of organic compounds, such as benzimidazole or imidazole derivatives, which form a protective layer on the copper surface.
Benefits of OSP-PCB
OSP offers several benefits compared to traditional surface finishes like Hot Air Solder Leveling (HASL) and Electroless Nickel Immersion Gold (ENIG):
-
Environment-friendly: OSP is a lead-free and halogen-free process, making it a more eco-friendly option compared to HASL, which involves the use of lead.
-
Cost-effective: OSP is a relatively inexpensive surface finish compared to alternatives like ENIG, making it an attractive option for cost-sensitive applications.
-
Excellent solderability: OSP provides good wettability and solderability, ensuring reliable solder joints during the assembly process.
-
Flat surface: Unlike HASL, which can result in uneven surfaces, OSP provides a flat surface that is suitable for fine-pitch components and surface mount technology (SMT).
OSP-PCB Manufacturing Process
The OSP-PCB manufacturing process involves several steps to ensure a high-quality, environment-friendly product.
1. PCB Fabrication
The first step in the OSP-PCB manufacturing process is the fabrication of the bare PCB. This involves the following sub-steps:
a. PCB Design: The PCB layout is designed using computer-aided design (CAD) software, taking into account the component placement, routing, and other design considerations.
b. Material Selection: The appropriate PCB substrate material, typically FR-4, is selected based on the application requirements.
c. Copper Cladding: A thin layer of copper is laminated onto the PCB substrate using heat and pressure.
d. Drilling: Holes are drilled into the PCB to accommodate through-hole components and vias.
e. Copper Patterning: The desired copper pattern is created on the PCB using a photolithography process, which involves applying a photoresist coating, exposing it to UV light through a photomask, and developing the resist to reveal the copper pattern.
f. Etching: The unwanted copper is removed using a chemical etching process, leaving behind the desired copper traces and pads.
2. Surface Preparation
Before applying the OSP coating, the PCB surface must be properly prepared to ensure good adhesion and uniform coverage.
a. Cleaning: The PCB is cleaned to remove any dirt, oils, or contaminants that may interfere with the OSP coating. This is typically done using a mild alkaline cleaning solution.
b. Microetching: A microetching step is performed to roughen the copper surface slightly, improving the adhesion of the OSP coating.
3. OSP Coating Application
The OSP coating is applied to the exposed copper surfaces of the PCB using one of the following methods:
a. Immersion: The PCB is immersed in an OSP solution for a specific duration, allowing the organic compounds to form a protective layer on the copper surface.
b. Spraying: The OSP solution is sprayed onto the PCB surface using a spray nozzle, ensuring uniform coverage.
4. Drying and Curing
After the OSP coating is applied, the PCB is dried and cured to remove any excess moisture and ensure the formation of a stable protective layer. This is typically done using a combination of air drying and oven curing at elevated temperatures.
5. Inspection and Testing
The finished OSP-PCB undergoes various inspection and testing procedures to ensure quality and reliability:
a. Visual Inspection: The PCB is visually inspected for any defects, such as incomplete coverage, pinholes, or contamination.
b. Thickness Measurement: The thickness of the OSP coating is measured using non-destructive techniques like X-ray fluorescence (XRF) to ensure it meets the specified requirements.
c. Solderability Testing: The solderability of the OSP-coated PCB is tested using standard methods like the wetting balance test or the dip-and-look test to ensure good wettability and solder joint formation.
Step | Process |
---|---|
PCB Fabrication | Design, material selection, copper cladding, drilling, patterning, etching |
Surface Preparation | Cleaning, microetching |
OSP Coating Application | Immersion or spraying |
Drying and Curing | Air drying, oven curing |
Inspection and Testing | Visual inspection, thickness measurement, solderability testing |
Advantages of Environment-friendly OSP-PCB
1. Reduced Environmental Impact
One of the primary advantages of OSP-PCB is its reduced environmental impact compared to traditional surface finishes. By eliminating the use of lead and other hazardous substances, OSP-PCB contributes to a greener and more sustainable electronics industry.
2. Compliance with Environmental Regulations
OSP-PCB helps manufacturers comply with increasingly stringent environmental regulations, such as the Restriction of Hazardous Substances (RoHS) directive and the Waste Electrical and Electronic Equipment (WEEE) directive. By adopting OSP-PCB, companies can ensure their products meet these regulations and avoid potential fines or legal issues.
3. Improved Health and Safety
The use of environment-friendly OSP-PCB also contributes to improved health and safety for workers involved in the manufacturing process. By reducing exposure to hazardous substances, OSP-PCB minimizes the risk of adverse health effects and creates a safer working environment.
4. Enhanced Corporate Social Responsibility
Adopting environment-friendly OSP-PCB demonstrates a company’s commitment to corporate social responsibility (CSR) and sustainability. This can help enhance the company’s reputation, attract environmentally conscious customers, and improve overall brand image.
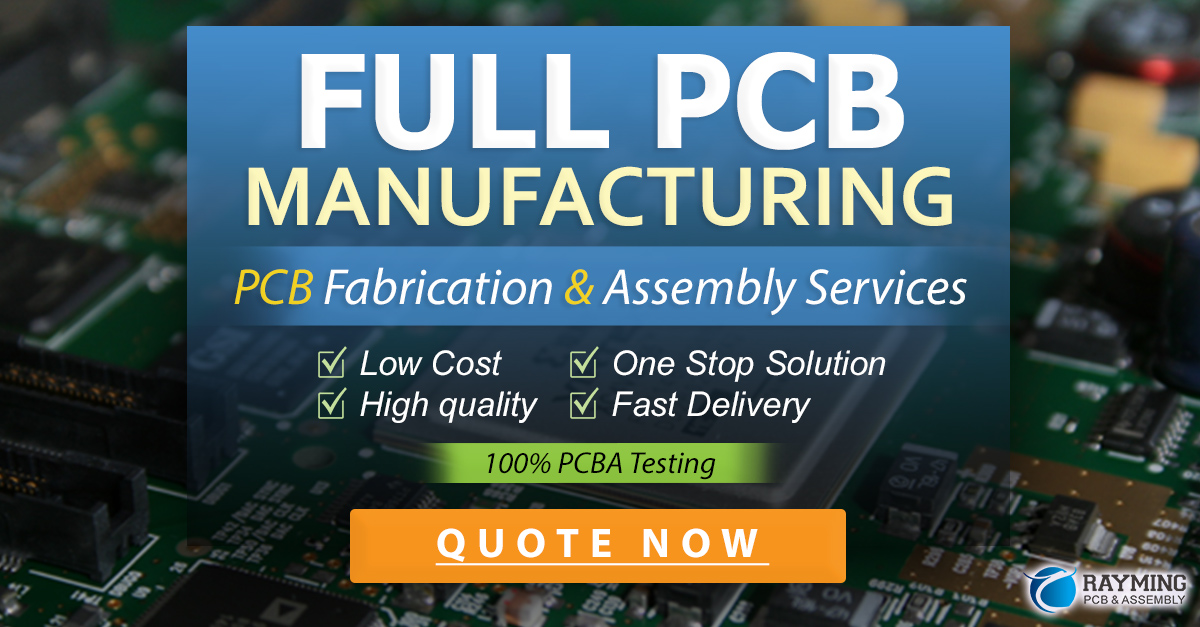
Challenges and Future Developments
Despite the numerous benefits of OSP-PCB, there are still some challenges and areas for future development:
1. Limited Shelf Life
One of the main challenges associated with OSP-PCB is its limited shelf life compared to other surface finishes. The organic compounds used in OSP coatings can degrade over time, reducing the solderability and reliability of the PCB. Researchers are working on developing new OSP formulations with improved stability and longer shelf life.
2. Sensitivity to Handling and Storage Conditions
OSP-coated PCBs are more sensitive to handling and storage conditions compared to other surface finishes. Improper handling, such as touching the coated surface with bare hands, can lead to contamination and reduced solderability. Manufacturers must implement strict handling and storage protocols to ensure the integrity of the OSP coating.
3. Compatibility with Certain Assembly Processes
OSP-PCB may not be suitable for certain assembly processes, such as those involving high temperatures or long exposure times. The organic compounds in the OSP coating can degrade under these conditions, leading to poor solderability and potential reliability issues. Manufacturers must carefully consider the compatibility of OSP-PCB with their specific assembly processes.
4. Advancements in OSP Formulations
Researchers are continually working on developing new and improved OSP formulations to address the limitations of current options. This includes the development of OSP coatings with enhanced thermal stability, longer shelf life, and better compatibility with various assembly processes. As these advancements are made, the adoption of OSP-PCB is expected to increase further.
Frequently Asked Questions (FAQ)
1. What is the typical thickness of an OSP coating on a PCB?
The typical thickness of an OSP coating on a PCB ranges from 0.2 to 0.5 microns. This thin layer is sufficient to provide protection against oxidation and maintain solderability.
2. How long can an OSP-coated PCB be stored before assembly?
The shelf life of an OSP-coated PCB depends on various factors, such as the specific OSP formulation, storage conditions, and handling practices. In general, OSP-coated PCBs can be stored for up to 6-12 months under proper conditions before assembly.
3. Can OSP-PCB be reworked or repaired?
Yes, OSP-PCB can be reworked or repaired using standard soldering techniques. However, the rework process may require the removal of the existing OSP coating and reapplication of a new coating to ensure proper solderability.
4. Is OSP-PCB suitable for high-temperature applications?
OSP-PCB may not be suitable for high-temperature applications, as the organic compounds in the OSP coating can degrade at elevated temperatures. In such cases, alternative surface finishes like ENIG or immersion silver may be more appropriate.
5. How does the cost of OSP-PCB compare to other surface finishes?
OSP-PCB is generally more cost-effective than other surface finishes like ENIG or immersion silver. The lower cost can be attributed to the simplicity of the OSP process and the use of relatively inexpensive organic compounds.
Conclusion
Environment-friendly OSP-PCB represents a significant advancement in the field of printed circuit board manufacturing. By eliminating the use of hazardous substances and promoting sustainability, OSP-PCB contributes to a greener and more responsible electronics industry. As manufacturers continue to adopt OSP-PCB and researchers work on addressing its limitations, the future of PCB manufacturing looks promising, with a focus on both performance and environmental stewardship.
Leave a Reply