Introduction to Nickel Electroplating in PCB Manufacturing
Nickel electroplating is a crucial process in the manufacturing of printed circuit boards (PCBs). This process involves depositing a thin layer of nickel onto the copper traces of the PCB, providing several benefits that enhance the performance and durability of the final product. Nickel-PCB electroplating offers improved solderability, increased corrosion resistance, and better adhesion for subsequent surface finishes.
Benefits of Nickel Electroplating on PCBs
- Enhanced solderability
- Improved corrosion resistance
- Better adhesion for surface finishes
- Increased durability and reliability
The Nickel Electroplating Process
Pre-treatment
Before the actual electroplating process begins, the PCB undergoes a series of pre-treatment steps to ensure optimal adhesion and uniform deposition of the nickel layer.
- Cleaning: The PCB is thoroughly cleaned to remove any contaminants, such as dirt, grease, or oxides, that may interfere with the electroplating process.
- Micro-etching: A mild etching solution is used to roughen the copper surface slightly, promoting better adhesion of the nickel layer.
- Activation: The PCB is immersed in an activator solution, which helps to remove any remaining oxides and prepares the surface for electroplating.
Electroplating Bath
The nickel electroplating bath is the heart of the process, where the actual deposition of nickel onto the PCB takes place.
Composition of the Nickel Electroplating Bath
The typical composition of a nickel electroplating bath includes:
Component | Concentration |
---|---|
Nickel Sulfate (NiSO4) | 200-400 g/L |
Nickel Chloride (NiCl2) | 30-60 g/L |
Boric Acid (H3BO3) | 30-50 g/L |
Wetting Agent | 0.1-1.0 g/L |
pH | 3.5-4.5 |
Temperature | 40-60°C |
Electroplating Parameters
To achieve optimal results, the following electroplating parameters should be maintained:
Parameter | Value |
---|---|
Current Density | 2-10 A/dm² |
Cathode Efficiency | 90-98% |
Plating Time | 10-30 minutes |
Agitation | Moderate |
Post-treatment
After the electroplating process, the PCB undergoes post-treatment to ensure the quality and stability of the nickel layer.
- Rinsing: The PCB is rinsed with deionized water to remove any remaining electrolyte solution.
- Drying: The PCB is dried using hot air or an oven to prevent water spots and ensure a clean surface.
- Inspection: The nickel-plated PCB is visually inspected for any defects, such as pitting, nodules, or uneven coverage.
Quality Control and Testing
To ensure the quality and reliability of nickel-plated PCBs, several tests and inspections are carried out.
Visual Inspection
A visual inspection is performed to check for any surface defects, such as pitting, nodules, or uneven coverage. This inspection can be done using a microscope or high-resolution camera.
Thickness Measurement
The thickness of the nickel layer is measured using non-destructive methods, such as X-ray fluorescence (XRF) or beta backscatter. The typical thickness range for nickel plating on PCBs is 1-5 µm.
Adhesion Test
The adhesion of the nickel layer to the copper substrate is tested using various methods, such as the tape test or the cross-hatch test. These tests involve applying and removing adhesive tape or making a grid of cuts on the surface and checking for any peeling or flaking of the nickel layer.
Solderability Test
The solderability of the nickel-plated PCB is assessed using a wetting balance test or a dip-and-look test. These tests evaluate the ability of the surface to be wetted by molten solder and the formation of a strong solder joint.
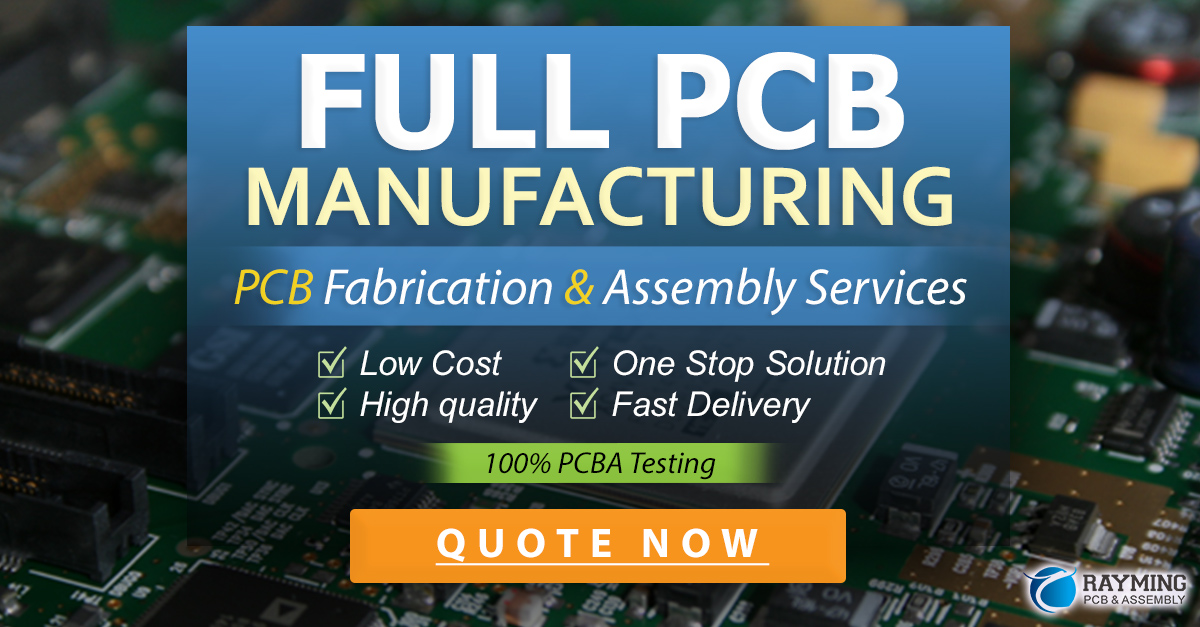
Troubleshooting Common Issues
Despite the numerous benefits of nickel electroplating on PCBs, several issues can arise during the process. Some common problems and their solutions are discussed below.
Poor Adhesion
Poor adhesion of the nickel layer to the copper substrate can be caused by insufficient cleaning or activation of the surface prior to electroplating. To resolve this issue, ensure that the pre-treatment steps are carried out effectively, and the surface is free from contaminants and oxides.
Uneven Coverage
Uneven coverage of the nickel layer can result from improper agitation or incorrect positioning of the PCB in the electroplating bath. To achieve uniform coverage, maintain moderate agitation and ensure that the PCB is positioned correctly in the bath.
Pitting or Nodules
Pitting or nodules on the nickel surface can be caused by impurities in the electroplating bath or incorrect current density. To prevent these defects, maintain the purity of the bath solution, control the current density within the recommended range, and regularly filter the bath to remove any particulate matter.
Environmental Considerations and Sustainability
As with any industrial process, nickel electroplating on PCBs has an environmental impact that must be considered and managed responsibly.
Waste Management
The waste generated from the nickel electroplating process, such as spent electrolyte solutions and rinse water, must be properly treated and disposed of in accordance with local regulations. This may involve neutralization, precipitation, or other methods to remove heavy metals and other pollutants before discharge.
Energy Efficiency
Electroplating is an energy-intensive process, and efforts should be made to optimize energy consumption. This can be achieved through the use of energy-efficient equipment, such as low-voltage rectifiers and heat exchangers, as well as implementing best practices for bath maintenance and operation.
Sustainable Materials
To promote sustainability, the use of eco-friendly and biodegradable additives in the electroplating bath should be considered. Additionally, the development and adoption of alternative surface finishes, such as organic solderability preservatives (OSPs), can help reduce the environmental impact of PCB manufacturing.
Future Trends and Developments
As the electronics industry continues to evolve, so too will the nickel electroplating process for PCBs.
Advances in Electroplating Technology
Research and development efforts are ongoing to improve the efficiency, quality, and sustainability of nickel electroplating. This includes the development of new electrolyte formulations, advanced process control systems, and innovative plating techniques, such as pulse plating or jet plating.
Alternative Surface Finishes
While nickel electroplating remains a popular choice for PCB surface finishing, alternative options are being explored to meet the changing needs of the industry. These include immersion silver, electroless nickel/immersion gold (ENIG), and organic solderability preservatives (OSPs), each with their own unique advantages and applications.
Miniaturization and High-Density Interconnects
As electronic devices become smaller and more complex, the demand for high-density interconnects (HDIs) and miniaturized PCBs will continue to grow. Nickel electroplating will play a crucial role in enabling these advances by providing reliable and robust surface finishes for fine-pitch components and high-density layouts.
Frequently Asked Questions (FAQs)
-
Q: What is the purpose of nickel electroplating on PCBs?
A: Nickel electroplating on PCBs serves multiple purposes, including enhancing solderability, improving corrosion resistance, providing better adhesion for subsequent surface finishes, and increasing the overall durability and reliability of the PCB. -
Q: What are the typical thickness ranges for nickel plating on PCBs?
A: The typical thickness range for nickel plating on PCBs is 1-5 µm. The exact thickness required depends on the specific application and the subsequent surface finish to be applied. -
Q: How can poor adhesion of the nickel layer be prevented?
A: Poor adhesion of the nickel layer can be prevented by ensuring that the pre-treatment steps, such as cleaning and activation, are carried out effectively. This helps to remove contaminants and oxides from the surface, promoting better adhesion of the nickel layer to the copper substrate. -
Q: What environmental considerations are associated with nickel electroplating on PCBs?
A: Nickel electroplating on PCBs generates waste, such as spent electrolyte solutions and rinse water, which must be properly treated and disposed of in accordance with local regulations. Efforts should also be made to optimize energy consumption and adopt sustainable materials and practices where possible. -
Q: What are some alternative surface finishes to nickel electroplating on PCBs?
A: Alternative surface finishes to nickel electroplating on PCBs include immersion silver, electroless nickel/immersion gold (ENIG), and organic solderability preservatives (OSPs). Each of these options has its own unique advantages and applications, and the choice depends on the specific requirements of the PCB and the end-use application.
Conclusion
Nickel electroplating is a critical process in the manufacturing of printed circuit boards, offering numerous benefits that enhance the performance, reliability, and durability of the final product. By understanding the principles, parameters, and best practices associated with nickel-PCB electroplating, manufacturers can optimize their processes to achieve consistent, high-quality results while minimizing environmental impact and promoting sustainability. As the electronics industry continues to evolve, ongoing research and development in nickel electroplating technology will be essential to meeting the ever-changing needs of the market and enabling the next generation of advanced PCB applications.
Leave a Reply