What is ECMS?
An Electronic Collaborative Manufacturing Service System (ECMS) is an integrated platform that enables companies to collaborate electronically throughout the entire manufacturing process, from design and development to production and delivery. ECMS solutions leverage advanced technologies like cloud computing, Internet of Things (IoT), artificial intelligence (AI), and big data analytics to facilitate seamless communication, data sharing, and process automation across the supply chain.
The main objectives of implementing an ECMS are to:
- Improve efficiency and productivity
- Reduce lead times and costs
- Enhance product quality and innovation
- Increase agility and responsiveness to market demands
- Strengthen relationships with suppliers and customers
Key Components of an ECMS
A comprehensive ECMS typically consists of the following key components:
1. Product Lifecycle Management (PLM)
PLM is a core component of an ECMS that manages the entire lifecycle of a product, from conception to retirement. It provides a central repository for all product-related data, including design files, specifications, bill of materials (BOM), and change histories. PLM enables cross-functional teams to collaborate effectively, streamline product development processes, and ensure data integrity and traceability.
2. Supply Chain Management (SCM)
SCM is another critical component of an ECMS that optimizes the flow of goods, information, and finances across the supply chain. It includes modules for demand forecasting, inventory management, procurement, logistics, and supplier relationship management. SCM helps companies to reduce inventory costs, improve delivery performance, and mitigate supply chain risks.
3. Manufacturing Execution System (MES)
MES is a real-time system that monitors and controls production operations on the shop floor. It collects data from machines and sensors, tracks work-in-progress, and generates production reports and quality metrics. MES integrates with other systems like ERP, PLM, and SCM to provide end-to-end visibility and optimize manufacturing processes.
4. Enterprise Resource Planning (ERP)
ERP is a business management system that integrates various functions like finance, accounting, human resources, and customer relationship management. It provides a unified view of the entire organization and enables data-driven decision making. ERP integrates with other ECMS components to ensure seamless data flow and process coordination.
5. Internet of Things (IoT)
IoT refers to the network of connected devices, sensors, and machines that can collect and exchange data in real-time. In an ECMS context, IoT enables remote monitoring and control of manufacturing assets, predictive maintenance, and real-time production optimization. IoT data can be analyzed using AI and machine learning algorithms to generate insights and improve decision making.
6. Artificial Intelligence (AI) and Analytics
AI and analytics are key enablers of an ECMS that can process vast amounts of data generated by various sources like PLM, SCM, MES, ERP, and IoT. AI techniques like machine learning, natural language processing, and computer vision can be used to identify patterns, predict failures, optimize processes, and automate decision making. Analytics provides real-time dashboards and reports to monitor key performance indicators (KPIs) and support continuous improvement initiatives.
Benefits of Implementing an ECMS
Implementing an ECMS can bring numerous benefits to manufacturing companies, including:
-
Increased Efficiency and Productivity: By automating manual processes, reducing errors and rework, and optimizing resource utilization, an ECMS can significantly improve operational efficiency and productivity. For example, a case study by Siemens PLM Software found that implementing an integrated PLM and MES solution helped a medical device manufacturer to reduce product development time by 50% and increase production throughput by 30%.
-
Reduced Costs and Lead Times: An ECMS can help companies to reduce costs associated with inventory, logistics, and quality issues by providing real-time visibility into supply chain operations and enabling proactive decision making. For instance, a study by Capgemini found that companies that implemented an integrated SCM solution achieved an average reduction of 15% in inventory costs and 10% in transportation costs.
-
Enhanced Product Quality and Innovation: An ECMS can support product quality and innovation by enabling collaborative product development, version control, and change management. It can also facilitate compliance with regulatory standards and customer requirements. A survey by Accenture found that companies that invested in PLM and quality management systems reported a 13% increase in new product introduction success rates and a 16% reduction in product defects.
-
Improved Agility and Responsiveness: An ECMS can help companies to respond quickly to changing market demands and disruptions by providing real-time visibility into supply chain operations and enabling scenario planning and what-if analysis. For example, a case study by Oracle found that implementing a cloud-based SCM solution helped a consumer goods company to reduce its planning cycle time from weeks to days and improve its forecast accuracy by 30%.
-
Stronger Supplier and Customer Relationships: An ECMS can facilitate collaboration and information sharing with suppliers and customers, leading to stronger partnerships and improved service levels. It can also enable co-innovation and joint problem-solving. A survey by McKinsey found that companies that engaged in collaborative innovation with suppliers and customers achieved a 20-30% higher rate of success in new product development compared to those that did not.
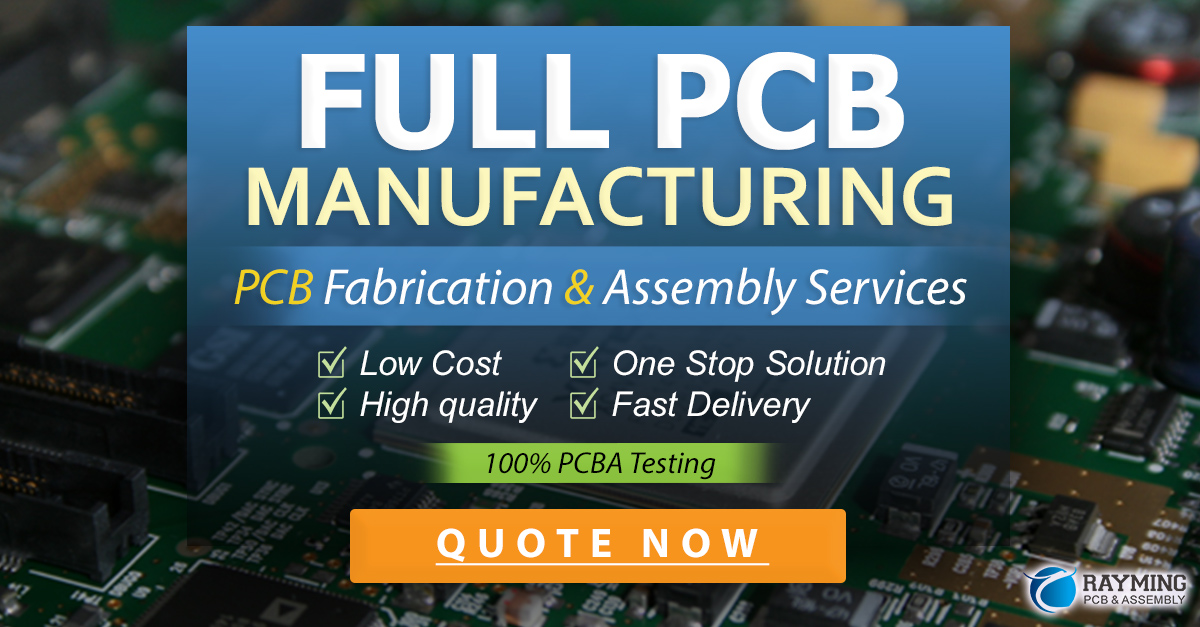
Challenges and Best Practices in ECMS Implementation
While an ECMS can bring significant benefits, implementing it can also pose several challenges, including:
-
Integration with Legacy Systems: Many manufacturing companies have multiple legacy systems that need to be integrated with the ECMS, which can be complex and time-consuming. It is important to carefully plan the integration strategy and prioritize the most critical systems and data flows.
-
Data Quality and Governance: An ECMS relies on accurate and consistent data to function effectively. However, data quality issues like duplication, inconsistency, and incompleteness are common in manufacturing environments. It is essential to establish data governance processes and tools to ensure data quality and integrity.
-
Change Management and User Adoption: Implementing an ECMS often requires significant changes to existing processes, roles, and responsibilities, which can lead to resistance from employees. It is crucial to develop a change management plan that includes communication, training, and incentives to drive user adoption and continuous improvement.
-
Security and Privacy: An ECMS deals with sensitive data like intellectual property, financial information, and personal data, which need to be protected from unauthorized access and cyber threats. It is important to implement robust security measures like encryption, access controls, and monitoring to ensure data security and privacy.
To overcome these challenges and ensure successful ECMS implementation, manufacturing companies should follow best practices such as:
- Defining clear business objectives and KPIs aligned with the overall strategy
- Conducting a thorough assessment of current processes, systems, and data flows
- Engaging key stakeholders from different functions and levels in the planning and implementation process
- Selecting the right ECMS platform and partners based on specific requirements and constraints
- Adopting an agile and iterative approach to implementation, starting with a pilot project and scaling up gradually
- Investing in training and support to ensure effective user adoption and continuous improvement
- Establishing governance structures and processes to manage the ECMS over its lifecycle
FAQs
- What is the difference between an ECMS and a traditional manufacturing system?
A traditional manufacturing system typically focuses on a specific function like production planning or quality control, whereas an ECMS provides an integrated platform that connects all the functions and processes across the manufacturing value chain. An ECMS also leverages advanced technologies like IoT, AI, and analytics to enable real-time visibility, optimization, and decision making.
- How long does it take to implement an ECMS?
The implementation timeline of an ECMS varies depending on factors like the size and complexity of the organization, the scope of the project, and the readiness of the existing systems and processes. A typical ECMS implementation can take anywhere from 6 months to 2 years or more. It is important to break down the implementation into phases and prioritize the most critical functionalities and data flows.
- How much does an ECMS cost?
The cost of an ECMS depends on various factors like the platform, modules, and services selected, the number of users and sites, and the implementation and support services required. The total cost of ownership (TCO) of an ECMS includes the upfront software and hardware costs, as well as ongoing costs like maintenance, upgrades, and training. According to a report by MarketsandMarkets, the global ECMS market is expected to grow from $11.2 billion in 2020 to $18.2 billion by 2025, at a CAGR of 10.2% during the forecast period.
- What are the key success factors for ECMS implementation?
Some of the key success factors for ECMS implementation include:
- Strong executive sponsorship and leadership commitment
- Clear definition of business objectives and KPIs
- Effective communication and change management
- Adequate resources and skills for implementation and support
- Robust data governance and quality management
- Agile and iterative implementation approach
-
Continuous improvement and benefits realization
-
What are the future trends in ECMS?
Some of the emerging trends in ECMS include:
- Cloud-based and software-as-a-service (SaaS) deployment models
- Increased adoption of AI and machine learning for predictive analytics and optimization
- Integration with blockchain for supply chain traceability and security
- Virtual and augmented reality (VR/AR) applications for product design and training
- 5G and edge computing for real-time data processing and control
- Sustainable and circular manufacturing practices enabled by ECMS
Conclusion
An Electronic Collaborative Manufacturing Service System (ECMS) is a game-changer for manufacturing companies looking to stay competitive in today’s fast-paced and global business environment. By leveraging advanced technologies and integrating all the functions and processes across the manufacturing value chain, an ECMS can help companies to improve efficiency, reduce costs, enhance quality, and increase agility. However, implementing an ECMS is not a simple task and requires careful planning, execution, and continuous improvement. By following best practices and partnering with the right platform and service providers, manufacturing companies can successfully implement an ECMS and realize its full potential benefits.
As the manufacturing industry continues to evolve and face new challenges like digital transformation, personalization, and sustainability, an ECMS will become an increasingly critical enabler of success. Manufacturing companies that invest in an ECMS today will be well-positioned to thrive in the future and create value for all stakeholders, including customers, employees, partners, and shareholders.
Leave a Reply