Introduction to EAGLE and DesignLink
EAGLE (Easily Applicable Graphical Layout Editor) is a powerful PCB design software developed by Autodesk. It is widely used by electronic designers and engineers to create schematics, design PCBs, and generate manufacturing files. EAGLE offers a user-friendly interface, extensive component libraries, and a wide range of features that make the PCB design process efficient and accurate.
DesignLink is a complementary tool that integrates with EAGLE to provide valuable information about electronic components. It allows users to access real-time data about component availability, pricing, and technical specifications directly within the EAGLE environment. By leveraging the power of EAGLE and DesignLink together, designers can streamline their workflow and make informed decisions throughout the PCB design process.
Benefits of Using EAGLE and DesignLink
Extensive Component Libraries
One of the key advantages of using EAGLE is its extensive component libraries. EAGLE comes with a vast collection of pre-defined components, including resistors, capacitors, ICs, connectors, and more. These libraries are regularly updated to include the latest components from various manufacturers, saving designers time and effort in creating their own component symbols and footprints.
Real-Time Component Information
DesignLink takes component management to the next level by providing real-time information about components directly within EAGLE. When a component is selected in the schematic or PCB layout, DesignLink retrieves up-to-date data from trusted sources, such as component distributors and manufacturers. This information includes:
- Availability: DesignLink displays the current stock levels of the component at various distributors, helping designers make informed decisions about component selection based on availability.
- Pricing: Designers can view the latest pricing information for the selected component, allowing them to optimize their design costs and make budget-conscious choices.
- Technical Specifications: DesignLink provides access to detailed technical specifications, datasheets, and application notes for each component, enabling designers to verify compatibility and performance characteristics.
Automated Bill of Materials (BOM) Generation
EAGLE and DesignLink simplify the process of generating a Bill of Materials (BOM) for a PCB design. With DesignLink integration, the BOM can be automatically populated with the most recent component information, including part numbers, quantities, and pricing. This automation reduces the risk of errors and ensures that the BOM is always up to date.
Design Rule Checking (DRC)
EAGLE’s Design Rule Checking (DRC) feature helps designers identify and resolve potential issues in their PCB designs. DRC analyzes the design against a set of predefined rules and constraints, such as minimum trace widths, clearances, and drill sizes. By running DRC, designers can catch and fix errors early in the design process, saving time and reducing the risk of manufacturing issues.
Seamless Integration with Manufacturing
EAGLE and DesignLink provide a seamless connection to the manufacturing process. Once a PCB design is complete, EAGLE can generate manufacturing files, such as Gerber files, drill files, and pick-and-place files, which are essential for PCB Fabrication and assembly. DesignLink ensures that the component information in these files is accurate and up to date, minimizing the chances of manufacturing delays or errors.
Getting Started with EAGLE and DesignLink
Installing EAGLE
To get started with EAGLE and DesignLink, you first need to install the EAGLE software on your computer. Here are the steps to install EAGLE:
- Visit the Autodesk EAGLE website (https://www.autodesk.com/products/eagle/overview) and click on the “Download” button.
- Choose the appropriate version of EAGLE for your operating system (Windows, Mac, or Linux) and click “Download.”
- Follow the installation wizard to install EAGLE on your computer. During the installation process, you will be prompted to create an Autodesk account or sign in with an existing one.
- Once the installation is complete, launch EAGLE.
Configuring DesignLink
To take advantage of DesignLink’s features, you need to configure it within EAGLE. Here’s how:
- Open EAGLE and navigate to the “Options” menu.
- Select “DesignLink” from the menu.
- Enter your DesignLink credentials (username and password) or create a new account if you don’t have one.
- Choose the component distributors you want to include in DesignLink’s search results.
- Click “OK” to save your DesignLink configuration.
Creating a New Project
To start a new PCB design project in EAGLE, follow these steps:
- Click on the “File” menu and select “New Project.”
- Choose a location on your computer to save the project and give it a name.
- Click “OK” to create the new project.
Designing the Schematic
The first step in PCB design is creating a schematic diagram that represents the electrical connections and components of your circuit. Here’s how to design a schematic in EAGLE:
- Double-click on the schematic file (.sch) in your project to open the schematic editor.
- Use the “Add” tool to place components from the libraries onto the schematic canvas.
- Use the “Net” tool to create electrical connections between the components.
- Use the “Name” tool to assign names to the nets and components for easy identification.
- Use the “Value” tool to assign values to the components, such as resistance or capacitance.
Laying Out the PCB
Once the schematic is complete, you can proceed to lay out the PCB. Here’s how:
- Click on the “Board” button in the schematic editor to switch to the PCB layout view.
- Use the “Move” tool to position the components on the PCB canvas.
- Use the “Route” tool to create copper traces that connect the components according to the schematic.
- Use the “Via” tool to create vias (plated holes) for connecting traces on different layers of the PCB.
- Use the “Polygon” tool to create copper fills for ground planes or power planes.
Running Design Rule Checks (DRC)
Before finalizing your PCB design, it’s crucial to run Design Rule Checks (DRC) to ensure that your design meets the manufacturing requirements and constraints. Here’s how to run DRC in EAGLE:
- Click on the “Tools” menu and select “DRC.”
- Configure the DRC settings based on your PCB Manufacturer’s specifications, such as minimum trace width, clearance, and drill size.
- Click “Check” to run the DRC.
- Review the DRC report and address any violations or warnings.
Generating Manufacturing Files
Once your PCB design is complete and has passed the DRC, you can generate the necessary manufacturing files. Here’s how:
- Click on the “File” menu and select “CAM Processor.”
- Select the appropriate CAM job, such as “Gerber” or “Drill,” based on your PCB manufacturer’s requirements.
- Configure the CAM job settings, such as layer selection and file format.
- Click “Process Job” to generate the manufacturing files.
- Save the generated files and send them to your PCB manufacturer for fabrication.
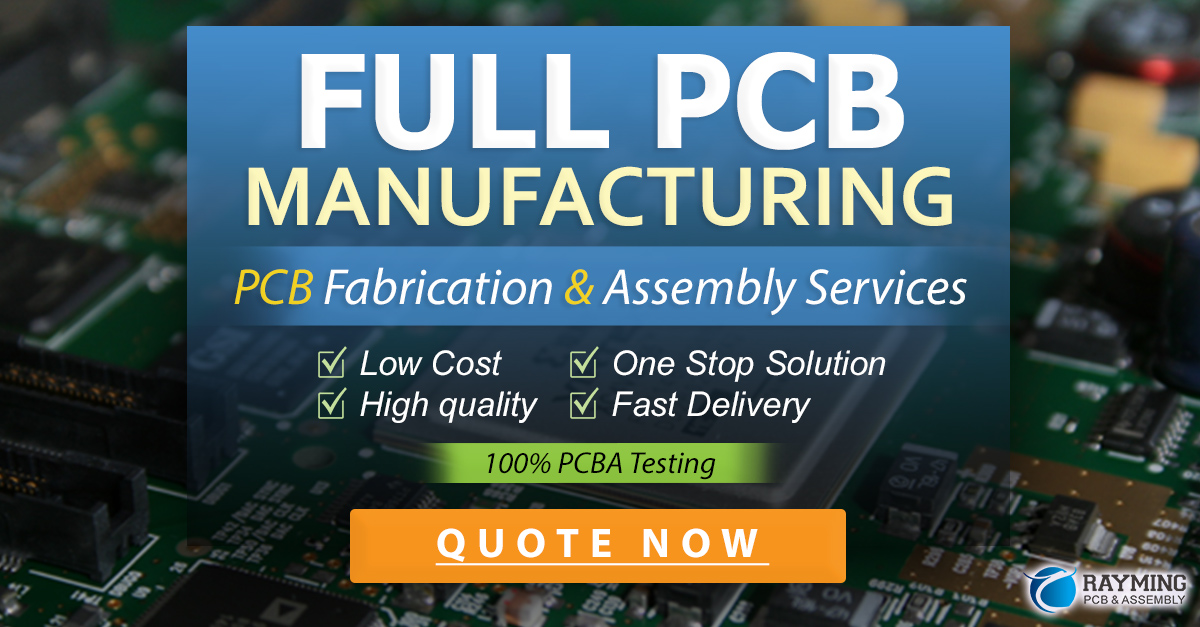
Advanced Features of EAGLE and DesignLink
Schematic and PCB Library Management
EAGLE provides a powerful library management system that allows you to organize and customize your component libraries. You can create your own libraries, add new components, and modify existing ones to suit your design needs. DesignLink enhances this functionality by providing real-time component information and ensuring that your libraries are always up to date.
To manage your libraries in EAGLE:
- Open the “Control Panel” and navigate to the “Libraries” tab.
- Use the “New Library” button to create a new library or the “Open Library” button to open an existing one.
- Use the “New Package” or “New Symbol” buttons to add new components to your library.
- Use the “Edit” button to modify existing components.
- Use the “Update” button to sync your libraries with DesignLink and retrieve the latest component information.
Hierarchical Schematic Design
EAGLE supports hierarchical schematic design, which allows you to break down complex designs into smaller, more manageable sub-circuits. This approach improves readability, reusability, and organization of your schematic.
To create a hierarchical schematic:
- Create a new schematic file for each sub-circuit.
- Design the sub-circuits using components and nets, just like in a regular schematic.
- In the main schematic, place a “Module” component that represents the sub-circuit.
- Use the “Invoke” command to link the module to the corresponding sub-circuit schematic file.
- Repeat steps 1-4 for each sub-circuit in your design.
Scripting and Automation
EAGLE provides a scripting language called User Language Programs (ULPs) that allows you to automate repetitive tasks and extend the functionality of the software. ULPs can be written in a C-like syntax and can interact with the EAGLE data structures, such as the schematic and PCB layouts.
Some common use cases for ULPs include:
- Generating custom reports, such as BOMs or component lists.
- Automating design tasks, such as creating multiple variations of a PCB layout.
- Integrating EAGLE with external tools or databases.
- Customizing the user interface or adding new commands.
To create and run a ULP:
- Open the EAGLE text editor and create a new file with a .ulp extension.
- Write your ULP script using the EAGLE scripting language.
- Save the ULP file in the EAGLE ulp directory.
- In EAGLE, click on the “File” menu and select “Run ULP.”
- Choose your ULP file from the list and click “Open” to run the script.
Integration with Version Control Systems
EAGLE designs can be easily integrated with version control systems (VCS) like Git or Subversion. This allows multiple designers to collaborate on the same project, track changes, and manage revisions effectively.
To integrate EAGLE with a VCS:
- Create a new repository for your EAGLE project in your preferred VCS.
- Add the EAGLE project files (.sch, .brd, .lbr) to the repository.
- Commit the initial version of the project to the repository.
- As you make changes to the project, regularly commit your updates to the repository.
- Use the VCS features, such as branching and merging, to manage parallel development and integrate changes from multiple designers.
Frequently Asked Questions (FAQ)
1. Can I use EAGLE and DesignLink for free?
EAGLE offers a free version called EAGLE Free, which has limitations on the PCB size and number of schematic sheets. DesignLink provides a limited free plan with access to basic component information. For more advanced features and larger designs, you need to purchase a paid license for EAGLE and subscribe to a paid plan for DesignLink.
2. Are EAGLE and DesignLink compatible with other PCB design software?
EAGLE uses its own file formats (.sch for schematics and .brd for PCB layouts), which are not directly compatible with other PCB design software. However, EAGLE can import and export files in various industry-standard formats, such as Gerber, DXF, and IDF, which can be used to exchange data with other tools. DesignLink is specifically designed to integrate with EAGLE and may not be compatible with other PCB design software.
3. How often are the component libraries in EAGLE and DesignLink updated?
The component libraries in EAGLE and DesignLink are regularly updated to include new components and maintain accuracy. The frequency of updates may vary depending on the library and the component manufacturer. EAGLE typically releases library updates every few months, while DesignLink strives to provide real-time component information by syncing with component distributors and manufacturers daily.
4. Can I create custom components in EAGLE?
Yes, EAGLE allows you to create custom components by designing your own symbols and footprints. You can use the library editor in EAGLE to create new components from scratch or modify existing ones to suit your specific requirements. Custom components can be saved in your personal libraries and reused across multiple projects.
5. Is there a community or forum where I can get help with EAGLE and DesignLink?
Yes, there is a large and active community of EAGLE and DesignLink users who share their knowledge and experience through various online platforms. Some popular resources include:
- Autodesk EAGLE Forum: https://forums.autodesk.com/t5/eagle/ct-p/eagle
- EAGLE Subreddit: https://www.reddit.com/r/eagle/
- EAGLE User Groups and Meetups: https://www.meetup.com/topics/eagle/
- DesignLink Support Portal: https://support.designlink.com/
These platforms provide a space for users to ask questions, seek guidance, share tips and tricks, and collaborate on projects.
Conclusion
EAGLE and DesignLink are powerful tools that streamline the PCB design process and provide valuable information about electronic components. By leveraging the extensive component libraries, real-time data, and automation features, designers can create high-quality PCBs efficiently and accurately.
This article has covered the key aspects of using EAGLE and DesignLink, from installation and configuration to schematic design, PCB layout, and generating manufacturing files. It has also explored advanced features such as library management, hierarchical design, scripting, and version control integration.
Whether you are a beginner or an experienced PCB designer, EAGLE and DesignLink offer a comprehensive solution for your design needs. By following the guidelines and best practices outlined in this article, you can unlock the full potential of these tools and create PCBs that meet your functional and manufacturing requirements.
As you embark on your PCB design journey with EAGLE and DesignLink, remember to stay updated with the latest software versions, library updates, and industry trends. Engage with the EAGLE and DesignLink community, seek guidance when needed, and continuously refine your skills to become a proficient and innovative PCB designer.
Leave a Reply