What is a Drill File?
A drill file, also known as a fabrication file or manufacturing file, is an essential component in the electronics manufacturing process, particularly in the production of printed circuit boards (PCBs). It contains the necessary information for CNC machines to accurately drill holes in the PCB substrate, allowing for the proper placement and connection of electronic components.
Drill files are typically generated from PCB design software, such as Altium Designer, Eagle, or KiCad, and are exported in a specific format, most commonly Excellon or Gerber. These files contain precise coordinates, sizes, and tolerances for each hole to be drilled in the PCB.
Key Components of a Drill File
- Drill Sizes: The file specifies the diameter of each hole to be drilled, usually measured in inches or millimeters.
- Coordinates: The X and Y coordinates of each hole are listed, indicating their precise location on the PCB.
- Tolerances: Acceptable deviations from the specified drill sizes and coordinates are included to ensure proper manufacturing.
- Plated and Non-Plated Holes: The file distinguishes between holes that require plating (for electrical connections) and those that do not (for mounting or alignment purposes).
The Importance of Accurate Drill Files
Generating accurate drill files is crucial for several reasons:
- Ensuring proper component placement and alignment
- Maintaining the integrity of electrical connections
- Preventing short circuits and other manufacturing defects
- Reducing waste and minimizing production costs
- Facilitating efficient and timely PCB fabrication
Inaccurate drill files can lead to a range of problems, from minor alignment issues to complete PCB failure. As such, it is essential to follow best practices and perform thorough checks when generating and verifying drill files.
Generating Drill Files: Step by Step
Step 1: Design the PCB
The first step in generating a drill file is to design the PCB using appropriate software. During this process, you will:
- Create the schematic diagram
- Layout the components and traces
- Define the PCB Stackup and dimensions
- Specify the drill sizes and locations for each hole
It is crucial to adhere to design guidelines and manufacturing constraints throughout this process to ensure the PCB can be fabricated successfully.
Step 2: Define Drill Sizes and Locations
When designing the PCB, you must define the drill sizes and locations for each hole. This includes:
- Vias: Small holes that connect different layers of the PCB
- Component holes: Used for mounting and connecting components to the PCB
- Mounting holes: Used for securing the PCB to an enclosure or chassis
- Alignment holes: Used for aligning the PCB during the assembly process
Consider the specific requirements of your components and the manufacturing capabilities of your chosen PCB fabricator when selecting drill sizes and locations.
Step 3: Generate the Drill File
Once the PCB design is complete, you can generate the drill file. The exact process may vary depending on your design software, but the general steps are:
- Select the appropriate drill file format (e.g., Excellon or Gerber)
- Choose the desired units (inches or millimeters)
- Specify the drill tolerance and minimum drill size
- Select the layers to include in the drill file (e.g., top, bottom, or both)
- Generate the file and save it in a designated location
Some software may allow you to generate separate drill files for plated and non-plated holes, which can be useful for certain manufacturing processes.
Step 4: Verify the Drill File
Before submitting the drill file to your PCB fabricator, it is essential to verify its accuracy. This can be done using various methods, such as:
- Visual inspection: Review the drill file in your PCB design software or a dedicated viewer to ensure holes are placed correctly and sized appropriately.
- Automated checks: Use built-in tools or third-party software to check for common errors, such as overlapping holes, incorrect sizes, or missing holes.
- Fabricator feedback: Some PCB Fabricators offer free file verification services, providing feedback on potential issues or improvements.
Verifying the drill file can help catch errors early, saving time and money in the long run.
Step 5: Submit the Drill File for Manufacturing
Once you have verified the accuracy of your drill file, you can submit it to your chosen PCB fabricator along with the other necessary files (e.g., Gerber files, BOM, and assembly instructions). Be sure to communicate any special requirements or preferences clearly to ensure a smooth manufacturing process.
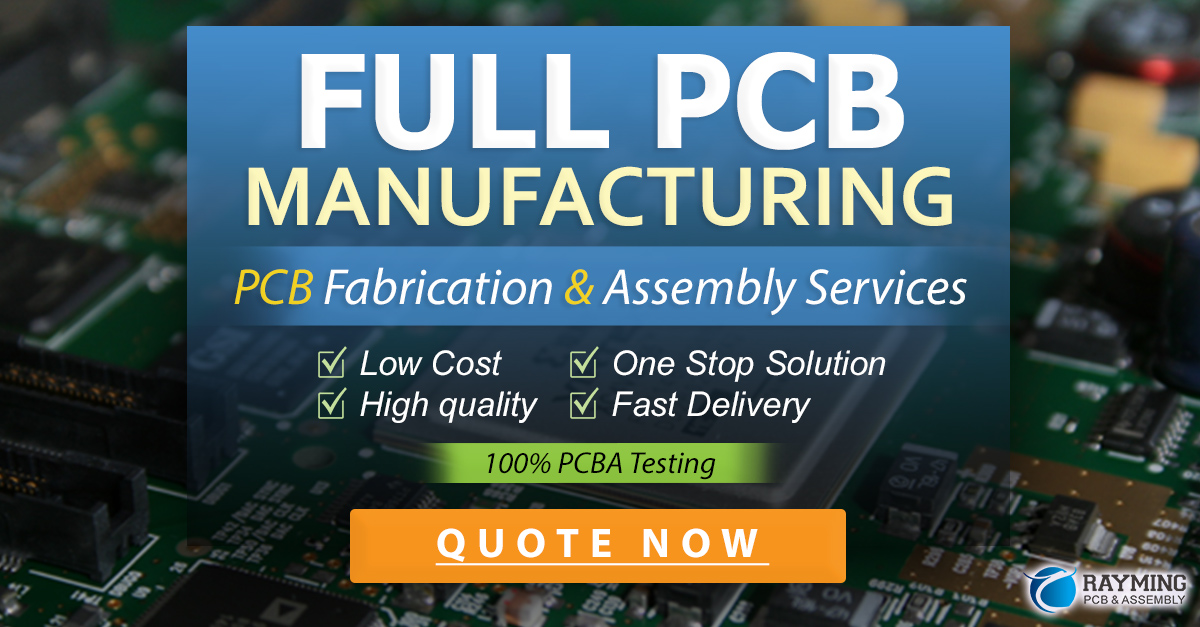
Best Practices for Generating Drill Files
To ensure the best possible results when generating drill files, consider the following best practices:
- Use a consistent naming convention for your files to avoid confusion and errors.
- Adhere to your PCB fabricator’s design guidelines and manufacturing constraints.
- Use standard drill sizes whenever possible to reduce tooling costs and lead times.
- Minimize the number of unique drill sizes to simplify the manufacturing process.
- Ensure adequate spacing between holes to maintain the structural integrity of the PCB.
- Clearly distinguish between plated and non-plated holes in your design and drill files.
- Perform thorough checks and verifications before submitting files for manufacturing.
- Communicate openly with your PCB fabricator to address any concerns or special requirements.
By following these best practices, you can generate accurate, reliable drill files that facilitate the successful manufacturing of your PCBs.
Common Challenges and Solutions
Despite best efforts, challenges can arise when generating drill files. Some common issues and their solutions include:
-
Incorrect hole sizes: Double-check your component requirements and update your design accordingly. Verify hole sizes in your drill file before submitting for manufacturing.
-
Misaligned holes: Ensure your components are placed correctly in your PCB design software. Use alignment tools and snap-to-grid features to maintain precision.
-
Overlapping holes: Perform automated checks to detect and resolve overlapping holes. Adjust component placement or drill sizes as needed.
-
Incompatible file formats: Confirm your PCB fabricator’s preferred file format and settings. Convert or re-generate files as necessary to ensure compatibility.
-
Missing holes: Perform visual inspections and automated checks to identify missing holes. Update your design and regenerate the drill file as needed.
By being aware of these common challenges and implementing the appropriate solutions, you can minimize errors and delays in the PCB manufacturing process.
Frequently Asked Questions (FAQ)
- What is the difference between Excellon and Gerber drill file formats?
-
Excellon and Gerber are both widely used formats for drill files. Excellon is a specialized format specifically for drilling information, while Gerber is a more general format that can include drill data alongside other PCB manufacturing information. Most PCB fabricators accept both formats, but it’s always best to confirm their preferred format before submitting your files.
-
How do I determine the appropriate drill sizes for my PCB?
-
The appropriate drill sizes for your PCB depend on several factors, including the specific requirements of your components, the thickness of your PCB, and the manufacturing capabilities of your chosen PCB fabricator. Consult your component datasheets and your fabricator’s design guidelines to determine the optimal drill sizes for your project.
-
Can I use the same drill file for multiple PCB designs?
-
While it may be tempting to reuse drill files across different PCB designs to save time, it is generally not recommended. Each PCB design is unique, with its own component requirements, layout, and manufacturing constraints. Reusing drill files can lead to errors, incompatibilities, and potential manufacturing issues. It’s best to generate a new drill file specific to each PCB design to ensure accuracy and reliability.
-
What should I do if my PCB fabricator reports issues with my drill file?
-
If your PCB fabricator reports issues with your drill file, the first step is to communicate with them to understand the specific nature of the problem. They may provide feedback or suggestions for resolving the issue. Review your drill file and PCB design to identify and correct any errors, then regenerate and resubmit the file. If necessary, seek guidance from your design software’s support resources or consult with a more experienced PCB designer.
-
How can I ensure the accuracy of my drill files?
- To ensure the accuracy of your drill files, follow best practices throughout the PCB design and file generation process. This includes adhering to design guidelines, using appropriate software settings, performing visual inspections and automated checks, and verifying your files before submitting them for manufacturing. Regularly communicate with your PCB fabricator and be open to their feedback to continuously improve the accuracy and reliability of your drill files.
Element | Description |
---|---|
Drill Sizes | The diameter of each hole to be drilled, usually measured in inches or millimeters. |
Coordinates | The X and Y coordinates of each hole, indicating their precise location on the PCB. |
Tolerances | Acceptable deviations from the specified drill sizes and coordinates. |
Plated Holes | Holes that require plating for electrical connections. |
Non-Plated Holes | Holes that do not require plating, used for mounting or alignment purposes. |
By understanding the key components of a drill file and following best practices for their generation, you can ensure the successful manufacturing of your PCBs and bring your electronic designs to life.
Leave a Reply