Introduction
In the world of electronics, two terms that are often used interchangeably are PCB (Printed Circuit Board) and IC (Integrated Circuit). While both are essential components in electronic devices, they serve different purposes and have distinct characteristics. In this article, we will explore the differences between PCB and IC, their functions, manufacturing processes, and applications.
What is a PCB?
A Printed Circuit Board, or PCB, is a flat board made of insulating material, such as fiberglass or plastic, with conductive copper traces printed on its surface. These traces connect various electronic components, such as resistors, capacitors, and ICs, to form a complete circuit. PCBs provide a stable and organized platform for electronic components to be mounted and interconnected, enabling the efficient functioning of electronic devices.
Types of PCBs
There are several types of PCBs, each designed to meet specific requirements and applications:
-
Single-sided PCB: A single-sided PCB has conductive traces on only one side of the board. These boards are simple, cost-effective, and suitable for low-density designs.
-
Double-sided PCB: Double-sided PCBs have conductive traces on both sides of the board, allowing for higher component density and more complex designs. The two sides are connected through holes called vias.
-
Multi-layer PCB: Multi-layer PCBs consist of multiple layers of conductive traces separated by insulating layers. These boards offer the highest component density and are used in complex electronic devices, such as smartphones and computers.
-
Flexible PCB: Flexible PCBs are made of thin, flexible materials that can bend and conform to various shapes. They are often used in wearable electronics and applications where space is limited.
-
Rigid-Flex PCB: Rigid-Flex PCBs combine the features of rigid and flexible PCBs, providing both stability and flexibility in a single board. They are used in applications that require the board to fit into tight spaces or withstand repeated flexing.
PCB Manufacturing Process
The manufacturing process of a PCB involves several steps:
-
Design: The PCB design is created using specialized software, such as Altium Designer or Eagle. The design includes the placement of components, routing of traces, and creation of solder masks and silkscreens.
-
Printing: The design is printed onto a transparent film or directly onto the copper-clad board using a photoplotter or direct imaging machine.
-
Etching: The exposed copper is removed using a chemical etching process, leaving only the desired conductive traces on the board.
-
Drilling: Holes are drilled into the board to accommodate through-hole components and create vias for multi-layer boards.
-
Plating: The holes are plated with copper to ensure electrical connectivity between layers.
-
Solder Mask and Silkscreen: A solder mask is applied to protect the copper traces from oxidation and prevent solder bridges. A silkscreen is added to provide labels and markings for components.
-
Surface Finishing: The exposed copper is coated with a protective layer, such as HASL (Hot Air Solder Leveling), ENIG (Electroless Nickel Immersion Gold), or OSP (Organic Solderability Preservative), to prevent oxidation and improve solderability.
-
Assembly: Electronic components are mounted onto the PCB using various techniques, such as through-hole mounting or surface-mount technology (SMT).
-
Testing: The assembled PCB undergoes various tests, such as automated optical inspection (AOI) and in-circuit testing (ICT), to ensure proper functionality and quality.
What is an Integrated Circuit?
An Integrated Circuit, or IC, is a miniaturized electronic circuit that consists of numerous components, such as transistors, resistors, capacitors, and diodes, fabricated onto a single semiconductor substrate, typically silicon. ICs are designed to perform specific functions, such as amplification, signal processing, memory storage, or microprocessor operations. The integration of multiple components onto a single chip enables the creation of complex electronic systems in a compact and efficient manner.
Types of Integrated Circuits
There are several types of integrated circuits, each designed for specific applications:
-
Analog ICs: Analog ICs process continuous signals, such as voltage or current, and are used in applications such as audio amplifiers, power management, and sensors.
-
Digital ICs: Digital ICs process discrete signals, represented by binary digits (0 and 1), and are used in applications such as logic gates, microprocessors, and memory devices.
-
Mixed-signal ICs: Mixed-signal ICs combine both analog and digital circuits on a single chip, enabling the processing of both continuous and discrete signals. They are used in applications such as data converters and communication systems.
-
Memory ICs: Memory ICs store digital data and are classified into two main categories: volatile memory (e.g., RAM) and non-volatile memory (e.g., ROM, EEPROM, and flash memory).
-
Microprocessor ICs: Microprocessor ICs are complex digital circuits that execute instructions and perform arithmetic and logical operations. They are the central processing units (CPUs) of computers and other digital devices.
IC Manufacturing Process
The manufacturing process of an integrated circuit is known as the semiconductor fabrication process, which involves several steps:
-
Wafer fabrication: A high-purity silicon wafer is created using the Czochralski process, which involves growing a single crystal of silicon from a melt.
-
Photolithography: The wafer is coated with a light-sensitive material called photoresist. A pattern representing the IC design is projected onto the photoresist using ultraviolet light, causing the exposed areas to harden.
-
Etching: The unexposed photoresist is removed, and the exposed areas are etched away using chemicals or plasma, creating a three-dimensional structure on the wafer.
-
Doping: Impurities, such as boron or phosphorus, are introduced into the etched areas to modify the electrical properties of the silicon, creating p-type and n-type regions.
-
Insulation and metallization: Layers of insulating materials, such as silicon dioxide and silicon nitride, are deposited onto the wafer to isolate the components. Metal connections, such as aluminum or copper, are added to create conductive paths between components.
-
Packaging: The wafer is cut into individual ICs, which are then packaged into protective enclosures, such as ceramic or plastic packages, with external pins or solder balls for connection to a PCB.
-
Testing: The packaged ICs undergo various tests to ensure proper functionality, performance, and reliability.
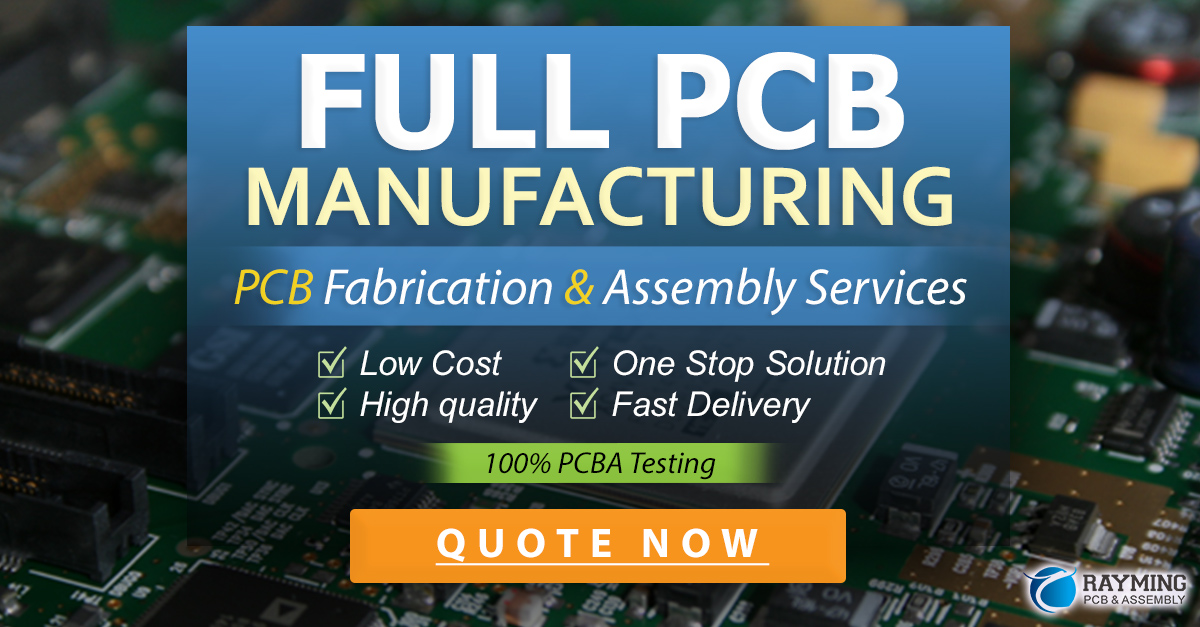
PCB vs IC: Key Differences
Characteristic | PCB | IC |
---|---|---|
Definition | A board that provides a platform for electronic components to be mounted and interconnected | A miniaturized electronic circuit that integrates multiple components onto a single semiconductor substrate |
Function | Provides a stable and organized platform for electronic components | Performs specific functions, such as amplification, signal processing, or memory storage |
Components | Passive components (resistors, capacitors) and active components (ICs) | Transistors, resistors, capacitors, and diodes |
Manufacturing Process | Printing, etching, drilling, plating, and assembly | Wafer fabrication, photolithography, etching, doping, insulation, metallization, and packaging |
Size | Larger, ranging from a few square centimeters to several square meters | Smaller, typically a few square millimeters |
Complexity | Less complex, with fewer components and simpler interconnections | Highly complex, with thousands to billions of components integrated onto a single chip |
Customization | Easier to customize and modify | More difficult to customize, requiring changes to the semiconductor fabrication process |
Cost | Lower cost for low-volume production | Higher cost for low-volume production, but lower cost for high-volume production |
Applications | Used in a wide range of electronic devices, from simple to complex | Used in specific applications, such as amplifiers, processors, and memory devices |
Applications of PCBs and ICs
PCBs and ICs are used in a wide range of electronic devices and systems, spanning various industries and applications.
PCB Applications
- Consumer electronics: Smartphones, laptops, televisions, and home appliances
- Automotive electronics: Engine control units, infotainment systems, and advanced driver assistance systems (ADAS)
- Medical devices: Diagnostic equipment, monitoring systems, and implantable devices
- Industrial automation: Process control systems, robotics, and machine vision
- Aerospace and defense: Avionics, communication systems, and weapon systems
IC Applications
- Computing: Microprocessors, memory devices, and graphics processing units (GPUs)
- Communication: RF and wireless ICs, modems, and network interface controllers
- Automotive: Power management ICs, sensors, and driver ICs for displays and lighting
- Consumer electronics: Audio and video ICs, power management ICs, and interface ICs
- Industrial: Motor control ICs, power management ICs, and sensor interface ICs
Frequently Asked Questions (FAQ)
-
Can a PCB function without an IC?
Yes, a PCB can function without an IC if it only consists of passive components, such as resistors and capacitors. However, most modern electronic devices require the use of ICs to perform complex functions. -
Are all ICs mounted on PCBs?
Most ICs are mounted on PCBs to provide a stable and organized platform for interconnection with other components. However, some ICs, such as those used in hybrid circuits or multi-chip modules (MCMs), may not be directly mounted on a PCB. -
What is the difference between a PCB and a breadboard?
A breadboard is a prototyping tool used to create temporary circuits for testing and experimentation. It does not require soldering and allows for easy modification of the circuit. In contrast, a PCB is a permanent and more reliable solution for electronic circuits, requiring soldering of components and offering better performance and durability. -
Can PCBs be recycled?
Yes, PCBs can be recycled to recover valuable materials, such as copper, gold, and palladium. However, the recycling process is complex and requires specialized facilities to handle the hazardous materials present in PCBs, such as lead and brominated flame retardants. -
What is the future of PCBs and ICs?
The future of PCBs and ICs is driven by the increasing demand for smaller, faster, and more powerful electronic devices. Emerging technologies, such as 5G, artificial intelligence, and the Internet of Things (IoT), are expected to drive the development of advanced PCBs and ICs. Some key trends include: -
High-Density Interconnect (HDI) PCBs: HDI PCBs offer higher component density and improved signal integrity, enabling the creation of smaller and more complex electronic devices.
-
System-on-Chip (SoC) ICs: SoCs integrate multiple functions, such as processing, memory, and communication, onto a single chip, reducing the size and power consumption of electronic devices.
-
3D IC packaging: 3D IC packaging technologies, such as through-silicon vias (TSVs) and chip stacking, allow for the vertical integration of multiple ICs, enabling higher performance and smaller form factors.
-
Flexible and stretchable electronics: The development of flexible and stretchable PCBs and ICs is enabling the creation of wearable and implantable electronic devices, as well as conformable electronics for various applications.
Conclusion
In conclusion, while PCBs and ICs are both essential components in electronic devices, they serve different purposes and have distinct characteristics. PCBs provide a stable and organized platform for electronic components to be mounted and interconnected, while ICs are miniaturized electronic circuits that perform specific functions. Understanding the differences between PCBs and ICs, their manufacturing processes, and their applications is crucial for anyone involved in the design, production, or use of electronic devices. As technology continues to advance, the development of innovative PCBs and ICs will play a vital role in shaping the future of electronics.
Leave a Reply