What is Chemical Etching?
Chemical etching, also known as wet etching, is a process that uses liquid chemical etchants to remove material from a substrate surface. The substrate is immersed in an etchant solution, which selectively removes the exposed areas of the material while leaving the masked areas intact. The etching reaction occurs at the interface between the etchant and the material surface, resulting in the dissolution of the material.
Mechanism of Chemical Etching
The chemical etching process involves three main steps:
- Transport of the etchant species to the substrate surface
- Chemical reaction between the etchant and the material
- Removal of the reaction products from the surface
The etchant solution typically contains an oxidizing agent that reacts with the material surface, forming soluble reaction products. The reaction products are then dissolved in the etchant solution and transported away from the surface, allowing the etching process to continue.
Advantages of Chemical Etching
Chemical etching offers several advantages, including:
- High selectivity: Chemical etchants can be tailored to selectively etch specific materials while leaving others untouched. This selectivity is achieved by choosing etchants that have a high etch rate for the target material and a low etch rate for the mask and other materials on the substrate.
- Low cost: Chemical etching is generally less expensive than plasma etching, as it does not require sophisticated vacuum systems or plasma generators. The equipment and consumables used in chemical etching are relatively simple and inexpensive.
- Batch processing: Chemical etching allows for batch processing, where multiple substrates can be etched simultaneously in the same etchant bath. This increases throughput and reduces processing time.
- Isotropic etching: Chemical etching typically results in isotropic etching profiles, where the etching proceeds equally in all directions. This can be advantageous for creating rounded or undercut features.
Limitations of Chemical Etching
Despite its advantages, chemical etching also has some limitations:
- Undercutting: Due to the isotropic nature of chemical etching, it can result in significant undercutting of the mask, leading to larger feature sizes than intended. This can be problematic for high-resolution patterns.
- Disposal of hazardous waste: Chemical etching generates hazardous waste in the form of spent etchant solutions and reaction products. Proper handling, treatment, and disposal of these wastes are necessary to minimize environmental impact and comply with regulations.
- Limited aspect ratio: Chemical etching is limited in terms of the aspect ratio (depth to width ratio) of the features it can create. As the etching proceeds, the etchant can diffuse laterally, resulting in widening of the features and loss of vertical sidewalls.
- Material compatibility: Some materials may not be compatible with certain chemical etchants, limiting the choice of etchants available for a given material system.
What is Plasma Etching?
Plasma etching, also known as dry etching, is a process that uses a plasma (an ionized gas) to remove material from a substrate surface. The plasma is generated by applying a strong electromagnetic field to a low-pressure gas, which ionizes the gas molecules and creates reactive species. These reactive species interact with the substrate surface, leading to the etching of the material.
Mechanism of Plasma Etching
Plasma etching involves two main mechanisms:
- Chemical etching: The reactive species in the plasma chemically react with the material surface, forming volatile reaction products that are removed from the surface.
- Physical etching (sputtering): The energetic ions in the plasma bombard the substrate surface, physically dislodging material atoms through momentum transfer.
The balance between chemical and physical etching can be controlled by adjusting the plasma parameters, such as gas composition, pressure, and power. This allows for the optimization of the etching process for different materials and desired etch profiles.
Advantages of Plasma Etching
Plasma etching offers several advantages over chemical etching:
- Anisotropic etching: Plasma etching can achieve highly anisotropic etch profiles, where the etching proceeds vertically into the substrate with minimal lateral etching. This enables the creation of high-aspect-ratio features with vertical sidewalls.
- High resolution: Due to the anisotropic nature of plasma etching, it can achieve smaller feature sizes and higher resolution compared to chemical etching. This makes plasma etching suitable for patterning nanoscale structures.
- Dry process: Plasma etching is a dry process, eliminating the need for liquid etchants and the associated handling and disposal challenges. This simplifies the process flow and reduces the environmental impact.
- Versatility: Plasma etching can be used to etch a wide range of materials, including semiconductors, dielectrics, and metals. By adjusting the plasma chemistry and parameters, the etching process can be optimized for different material systems.
Limitations of Plasma Etching
Plasma etching also has some limitations:
- Equipment cost: Plasma etching requires sophisticated vacuum systems, plasma generators, and gas handling equipment, which can be expensive compared to chemical etching setups.
- Plasma damage: The energetic ions and reactive species in the plasma can cause damage to the substrate surface, such as lattice defects, contamination, or charge buildup. This can affect the electrical and optical properties of the etched materials.
- Etch rate uniformity: Achieving uniform etch rates across large substrates can be challenging in plasma etching due to the non-uniformity of the plasma distribution and the loading effect (where the etch rate depends on the exposed area of the material).
- Selectivity limitations: While plasma etching can achieve some level of selectivity by adjusting the plasma chemistry, it may not match the high selectivity offered by chemical etching for certain material combinations.
Comparison of Chemical and Plasma Etching
To better understand the differences between chemical and plasma etching, let’s compare them in terms of key characteristics:
Characteristic | Chemical Etching | Plasma Etching |
---|---|---|
Etchant | Liquid chemicals | Ionized gas (plasma) |
Mechanism | Chemical reaction | Chemical reaction and physical sputtering |
Etch profile | Isotropic | Anisotropic |
Selectivity | High | Moderate |
Resolution | Low to moderate | High |
Cost | Low | High |
Environmental impact | High (hazardous waste) | Low (dry process) |
Damage | Low | Moderate to high |
Throughput | High (batch processing) | Moderate |
As evident from the comparison, chemical etching and plasma etching have their own strengths and weaknesses. The choice between the two depends on the specific requirements of the application, such as the desired feature size, etch profile, material compatibility, and cost considerations.
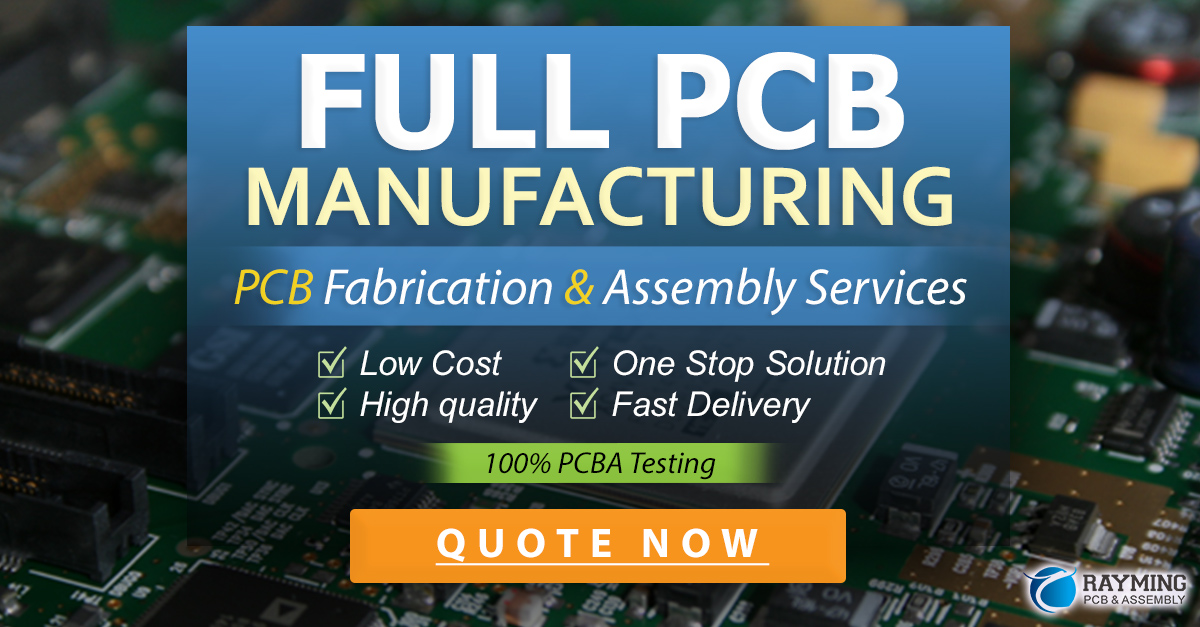
Applications of Chemical and Plasma Etching
Chemical and plasma etching find applications in various fields, including semiconductor manufacturing, MEMS (Micro-Electro-Mechanical Systems), and photonics. Here are some common applications of each etching process:
Applications of Chemical Etching
- Bulk micromachining: Chemical etching is widely used for bulk micromachining of silicon substrates to create MEMS structures, such as membranes, cantilevers, and channels.
- Wet cleaning: Chemical etching is employed for wet cleaning of substrates to remove contaminants, native oxides, or sacrificial layers.
- Metal patterning: Chemical etching is used to pattern metal layers, such as copper interconnects in printed circuit boards (PCBs) or aluminum contacts in semiconductor devices.
- Photoresist stripping: Chemical etching is utilized for removing photoresist layers after lithography or as a lift-off process for patterning deposited films.
Applications of Plasma Etching
- Semiconductor device fabrication: Plasma etching is extensively used in the fabrication of semiconductor devices, such as transistors, memory cells, and sensors. It enables the patterning of high-resolution features with precise control over the etch profile.
- Deep reactive ion etching (DRIE): DRIE is a specialized plasma etching technique used for creating high-aspect-ratio structures in silicon, such as through-silicon vias (TSVs) and MEMS devices.
- Dielectric etching: Plasma etching is employed for patterning dielectric layers, such as silicon dioxide and silicon nitride, in the fabrication of integrated circuits and MEMS.
- Photonic device fabrication: Plasma etching is used in the fabrication of photonic devices, such as waveguides, gratings, and photonic crystals, where precise control over the etch profile is crucial.
FAQ
-
Q: Can chemical and plasma etching be used together in a process flow?
A: Yes, chemical and plasma etching can be used in combination in a process flow. For example, chemical etching can be used for bulk material removal or selective etching, while plasma etching can be used for precise pattern transfer or high-aspect-ratio features. -
Q: What factors influence the choice between chemical and plasma etching?
A: The choice between chemical and plasma etching depends on various factors, such as the desired feature size, etch profile, material compatibility, selectivity requirements, throughput, and cost. The specific application and process constraints dictate which etching method is more suitable. -
Q: Can plasma etching achieve the same level of selectivity as chemical etching?
A: While plasma etching can achieve some level of selectivity by tuning the plasma chemistry and parameters, it may not match the high selectivity offered by chemical etching for certain material combinations. Chemical etchants can be highly selective to specific materials, making them advantageous when high selectivity is required. -
Q: What safety precautions are necessary when working with chemical and plasma etching?
A: Both chemical and plasma etching involve hazardous materials and processes. When working with chemical etching, proper handling, storage, and disposal of etchants and waste products are crucial. Personal protective equipment (PPE) should be worn to avoid contact with chemicals. In plasma etching, high voltages and RF power are used, so electrical safety measures must be followed. Adequate ventilation and exhaust systems are necessary to remove hazardous gases and byproducts. -
Q: How can the etch rate and profile be controlled in chemical and plasma etching?
A: In chemical etching, the etch rate and profile can be controlled by factors such as the etchant concentration, temperature, agitation, and additives. Selective etchants and etch stop layers can be used to control the etch depth and profile. In plasma etching, the etch rate and profile can be controlled by adjusting the plasma parameters, such as gas composition, pressure, power, and bias voltage. The use of passivation layers and cycling between etching and passivation steps (as in DRIE) can enable the formation of high-aspect-ratio features with vertical sidewalls.
Conclusion
Chemical and plasma etching are two fundamental processes used in the fabrication of semiconductor devices, MEMS, and photonic structures. While both methods aim to remove material from a substrate surface, they differ in their mechanisms, capabilities, and applications. Chemical etching relies on liquid etchants and offers high selectivity, low cost, and batch processing capabilities, but it is limited in terms of feature resolution and aspect ratio. Plasma etching, on the other hand, uses ionized gases and provides anisotropic etching, high resolution, and versatility, but it comes with higher equipment costs and potential plasma-induced damage.
The choice between chemical and plasma etching depends on the specific requirements of the application, such as the desired feature size, etch profile, material compatibility, and cost considerations. In many cases, a combination of both etching methods can be employed in a process flow to leverage their respective strengths.
As the demand for miniaturization and high-performance devices continues to grow, advances in chemical and plasma etching technologies will play a crucial role in enabling the fabrication of ever-smaller and more complex structures. Researchers and engineers continue to develop new etching chemistries, plasma sources, and process techniques to push the boundaries of what is possible in micro- and nanofabrication.
By understanding the differences between chemical and plasma etching and their respective advantages and limitations, engineers and researchers can make informed decisions when designing and optimizing Etching Processes for their specific applications. The continued development and refinement of etching technologies will undoubtedly shape the future of semiconductor manufacturing, MEMS, and photonics, enabling the realization of new and innovative devices that will drive technological advancements across various industries.
Leave a Reply