What is the Dielectric Constant?
The dielectric constant, also known as the relative permittivity (εr), is a dimensionless quantity that describes the ability of a material to store electrical energy in an electric field. It is the ratio of the permittivity of a material to the permittivity of free space (ε0). The dielectric constant of a material determines how much the electric field is reduced within the material compared to the electric field in a vacuum.
Mathematically, the dielectric constant is expressed as:
εr = ε / ε0
where:
– εr is the dielectric constant (relative permittivity)
– ε is the permittivity of the material
– ε0 is the permittivity of free space (8.85 × 10^-12 F/m)
A higher dielectric constant indicates that the material has a greater ability to store electrical energy, while a lower dielectric constant means that the material has a lesser ability to store electrical energy.
Importance of the Dielectric Constant in FR-4 Material
The dielectric constant of FR-4 material is a critical property that influences several aspects of PCB design and performance. Some of the key reasons why the dielectric constant is important in FR-4 include:
Signal Integrity
The dielectric constant of FR-4 affects the speed and quality of signal transmission through the PCB. A higher dielectric constant results in slower signal propagation, which can lead to signal integrity issues, such as increased propagation delay, signal reflections, and crosstalk. On the other hand, a lower dielectric constant allows for faster signal propagation and better signal integrity.
Impedance Control
The dielectric constant of FR-4 plays a vital role in determining the characteristic impedance of transmission lines on the PCB. The characteristic impedance (Z0) is a function of the dielectric constant, trace width, trace thickness, and the height of the trace above the ground plane. Maintaining a consistent dielectric constant is essential for achieving the desired impedance and ensuring proper impedance matching throughout the PCB.
Capacitance and Inductance
The dielectric constant of FR-4 affects the capacitance and inductance of the traces on the PCB. A higher dielectric constant results in higher capacitance between adjacent traces, which can lead to increased crosstalk and signal distortion. Similarly, the dielectric constant influences the inductance of the traces, which can impact the high-frequency performance of the circuit.
Electromagnetic Compatibility (EMC)
The dielectric constant of FR-4 can impact the electromagnetic compatibility (EMC) of the PCB. A higher dielectric constant can result in increased electromagnetic interference (EMI) and reduced electromagnetic immunity (EMI) of the circuit. Proper selection of the FR-4 material with an appropriate dielectric constant can help minimize EMC issues and ensure compliance with regulatory standards.
Factors Affecting the Dielectric Constant of FR-4
Several factors can influence the dielectric constant of FR-4 material. Understanding these factors is essential for selecting the appropriate FR-4 grade and ensuring consistent performance across different production batches. Some of the key factors affecting the dielectric constant of FR-4 include:
Glass Fiber Content
The glass fiber content in FR-4 material significantly impacts its dielectric constant. As the glass fiber content increases, the dielectric constant of the material also increases. This is because glass fibers have a higher dielectric constant compared to the epoxy resin matrix. Typical glass fiber content in FR-4 ranges from 50% to 70% by weight, with higher glass fiber content resulting in a higher dielectric constant.
Resin Composition
The composition of the epoxy resin used in FR-4 material can also affect its dielectric constant. Different epoxy resin formulations have varying dielectric properties, and the choice of the resin system can influence the overall dielectric constant of the FR-4 laminate. Some specialized FR-4 grades may use modified epoxy resins with lower dielectric constants to achieve better high-frequency performance.
Manufacturing Process
The manufacturing process of FR-4 material can introduce variations in the dielectric constant. Factors such as the curing temperature, pressure, and duration can impact the crosslinking density of the epoxy resin and the distribution of the glass fibers, which in turn can affect the dielectric constant. Consistent manufacturing processes and quality control measures are essential to minimize variations in the dielectric constant across different production batches.
Frequency and Temperature
The dielectric constant of FR-4 material is not constant across all frequencies and temperatures. As the frequency increases, the dielectric constant of FR-4 tends to decrease slightly. This is due to the dielectric relaxation phenomena, where the polarization of the material lags behind the applied electric field at higher frequencies. Similarly, the dielectric constant of FR-4 can also vary with temperature, with higher temperatures generally resulting in a slight increase in the dielectric constant.
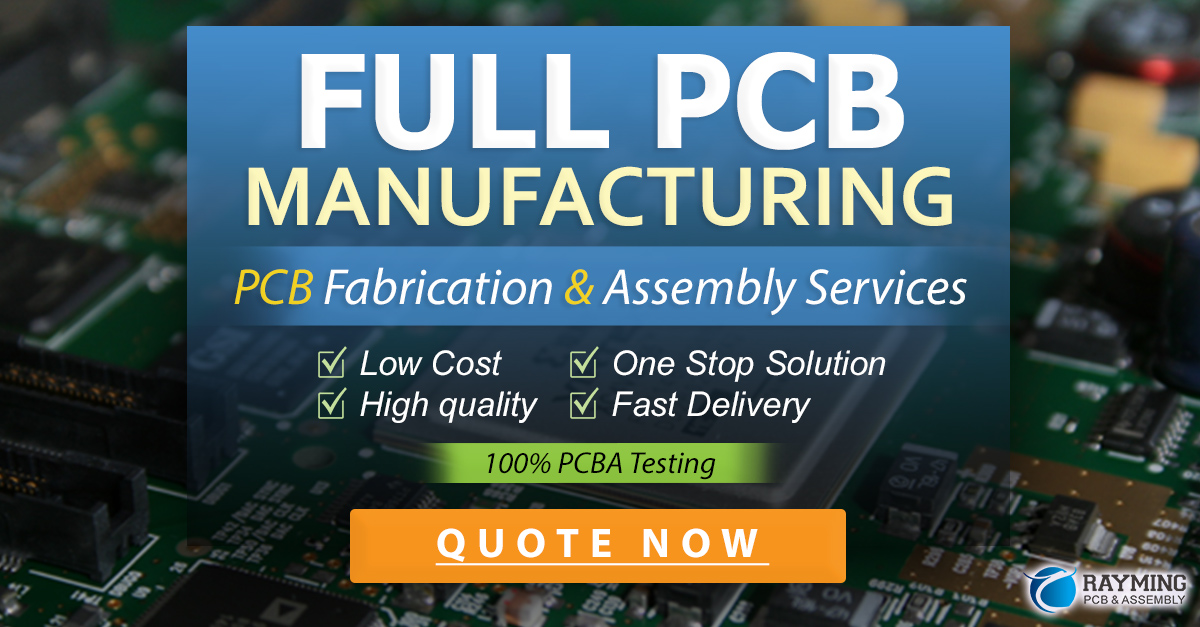
Typical Dielectric Constant Values for FR-4
The dielectric constant of FR-4 material can vary depending on the specific grade and manufacturer. However, most standard FR-4 grades have a dielectric constant ranging from 4.2 to 4.6 at 1 MHz frequency. Some common FR-4 grades and their typical dielectric constant values are listed in the table below:
FR-4 Grade | Dielectric Constant (1 MHz) |
---|---|
Standard FR-4 | 4.2 – 4.6 |
High Tg FR-4 | 4.3 – 4.7 |
Low Dk FR-4 | 3.8 – 4.2 |
Halogen-Free FR-4 | 4.0 – 4.4 |
It is important to note that the dielectric constant values provided by manufacturers are typically nominal values and may have a certain tolerance range. It is always recommended to consult the specific datasheet or work with the FR-4 supplier to obtain accurate dielectric constant values for the material being used in a particular application.
Applications of FR-4 Material
FR-4 material is widely used in various industries due to its excellent mechanical, thermal, and electrical properties. Some of the common applications of FR-4 include:
Printed Circuit Boards (PCBs)
FR-4 is the most commonly used substrate material for manufacturing PCBs. Its good mechanical strength, dimensional stability, and dielectric properties make it suitable for a wide range of electronic applications, from consumer electronics to industrial control systems.
High-Speed Digital Circuits
FR-4 material is often used in high-speed digital circuits, such as computer motherboards, network switches, and telecommunications equipment. The dielectric constant of FR-4 is an important consideration in these applications to ensure proper signal integrity and minimize signal distortion at high frequencies.
Automotive Electronics
FR-4 is used in various automotive electronic systems, such as engine control units (ECUs), infotainment systems, and advanced driver assistance systems (ADAS). The material’s thermal stability and flame-retardant properties make it suitable for the harsh operating conditions encountered in automotive environments.
Aerospace and Defense
FR-4 material finds applications in aerospace and defense electronics, where reliability and performance under extreme conditions are critical. The material’s ability to withstand high temperatures and its resistance to moisture and chemicals make it a preferred choice for military-grade PCBs and avionics systems.
Medical Devices
FR-4 is used in the manufacturing of medical electronic devices, such as patient monitoring systems, diagnostic equipment, and implantable devices. The biocompatibility and sterilization compatibility of FR-4 make it suitable for medical applications, where patient safety and device reliability are paramount.
Frequently Asked Questions (FAQ)
-
What is the typical dielectric constant value for standard FR-4 material?
Standard FR-4 material typically has a dielectric constant value ranging from 4.2 to 4.6 at 1 MHz frequency. -
How does the glass fiber content affect the dielectric constant of FR-4?
As the glass fiber content in FR-4 material increases, the dielectric constant of the material also increases. This is because glass fibers have a higher dielectric constant compared to the epoxy resin matrix. -
Can the dielectric constant of FR-4 vary with frequency and temperature?
Yes, the dielectric constant of FR-4 material can vary slightly with frequency and temperature. As the frequency increases, the dielectric constant tends to decrease slightly due to dielectric relaxation phenomena. Higher temperatures can also result in a slight increase in the dielectric constant. -
Why is the dielectric constant important in high-speed digital circuits?
The dielectric constant of FR-4 is important in high-speed digital circuits because it affects the speed and quality of signal transmission. A lower dielectric constant allows for faster signal propagation and better signal integrity, which is crucial for maintaining proper circuit performance at high frequencies. -
Are there any specialized FR-4 grades with lower dielectric constants?
Yes, there are specialized FR-4 grades, such as Low Dk FR-4, which have lower dielectric constants compared to standard FR-4. These grades are designed to achieve better high-frequency performance and are often used in applications where signal integrity and low signal distortion are critical.
Conclusion
The dielectric constant value of FR-4 material is a crucial property that significantly influences the performance and reliability of electronic circuits built on PCBs. Understanding the factors that affect the dielectric constant, such as glass fiber content, resin composition, and manufacturing process, is essential for selecting the appropriate FR-4 grade and ensuring consistent performance across different production batches.
Typical dielectric constant values for standard FR-4 range from 4.2 to 4.6 at 1 MHz frequency, with specialized grades offering lower dielectric constants for high-frequency applications. FR-4 material finds extensive use in various industries, including consumer electronics, automotive, aerospace, defense, and medical devices, due to its excellent mechanical, thermal, and electrical properties.
When designing PCBs using FR-4 material, it is crucial to consider the impact of the dielectric constant on signal integrity, impedance control, capacitance, inductance, and electromagnetic compatibility. Proper selection of the FR-4 grade and close collaboration with the material supplier can help optimize the PCB design and ensure reliable performance in the intended application.
As technology advances and the demand for high-speed, high-frequency electronics continues to grow, the development of new FR-4 grades with improved dielectric properties will remain an active area of research and innovation in the electronics industry.
Leave a Reply