Introduction to PCBs
Printed Circuit Boards (PCBs) are the backbone of modern electronics. These flat boards, made from insulating materials like fiberglass or composite epoxy, have conductive pathways etched or printed onto their surface to create circuits. Components like resistors, capacitors, and integrated circuits are soldered onto the PCB to create a complete Electronic Assembly.
PCBs have revolutionized electronics manufacturing by allowing for the mass production of consistent, compact, and complex circuits. They are used in virtually every electronic device, from smartphones and computers to medical equipment and aerospace systems.
The Early Days of PCBs
The concept of the printed circuit board can be traced back to the early 20th century. In 1903, German inventor Albert Hanson filed a patent for a method of creating an electrical connection by bonding wire to a flat surface. This laid the groundwork for the development of PCBs.
In the 1920s, Charles Ducas of the United States patented a method for electroplating circuit patterns onto an insulated surface. This was followed by the development of the “printed wire” method by Austrian engineer Paul Eisler in the 1930s. Eisler’s method involved printing conductive ink onto a non-conductive base material.
During World War II, the demand for compact, reliable electronic equipment for military applications drove further advancements in PCB technology. The United States National Bureau of Standards (now the National Institute of Standards and Technology) developed a process for printing electrical circuits onto a ceramic substrate.
The Rise of Modern PCBs
The 1950s saw the emergence of the modern PCB as we know it today. The U.S. Army Signal Corps sponsored a project that used Eisler’s printed wire method to create circuits on a plastic substrate. This project led to the development of the “Auto-Sembly” process by the U.S. company Photocircuits, which used a photographic method to etch copper patterns onto a phenolic base material.
In the 1960s, the introduction of through-hole technology allowed for the drilling of holes through the PCB to accommodate leaded components. This enabled the creation of double-sided PCBs, which had circuitry on both sides of the board.
The 1970s brought the development of Multilayer PCBs, which stacked multiple double-sided boards with insulating layers in between. This allowed for even more complex circuits in a compact space.
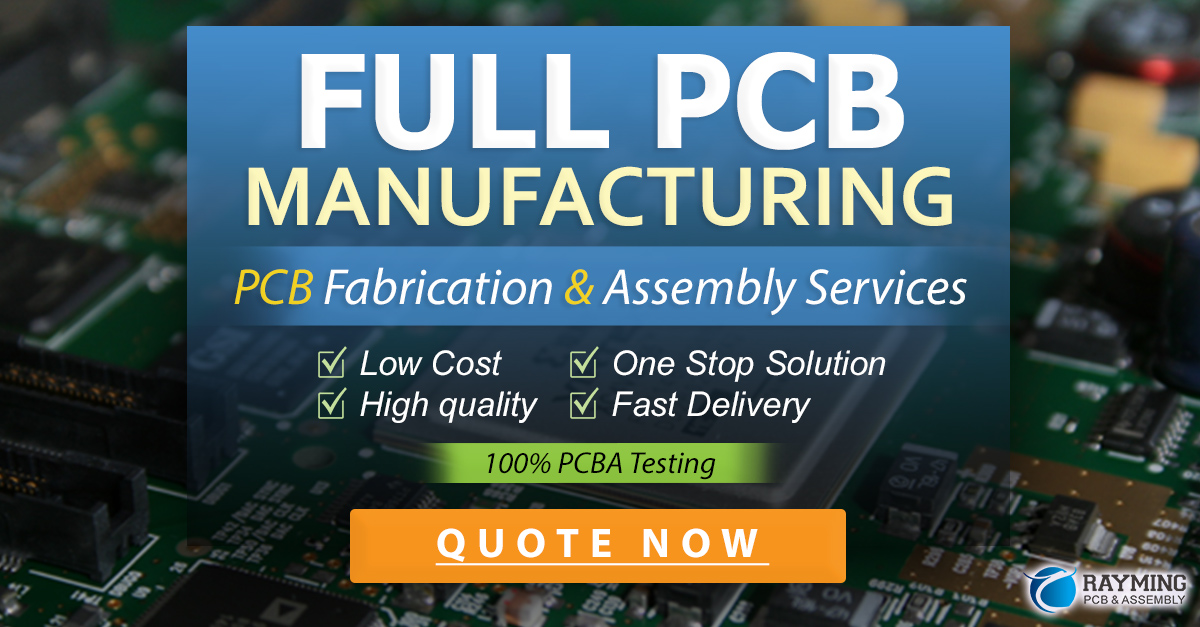
PCB Manufacturing Processes
The manufacturing of PCBs involves several key steps:
- Design: The circuit is designed using Electronic Design Automation (EDA) software.
- Printing: The circuit pattern is printed onto the copper-clad board using a photoresist and exposure to UV light.
- Etching: The unwanted copper is etched away, leaving only the desired circuit pattern.
- Drilling: Holes are drilled into the board to accommodate through-hole components.
- Plating: The holes are plated with a conductive material to create electrical connections between layers.
- Soldering: Components are soldered onto the board.
- Testing: The completed board is tested for functionality.
Step | Process | Description |
---|---|---|
1 | Design | Circuit design using EDA software |
2 | Printing | Circuit pattern printed onto copper-clad board |
3 | Etching | Unwanted copper etched away |
4 | Drilling | Holes drilled for through-hole components |
5 | Plating | Holes plated with conductive material |
6 | Soldering | Components soldered onto board |
7 | Testing | Completed board tested for functionality |
Types of PCBs
PCBs can be categorized based on the number of conductive layers:
- Single-sided: Conductive material on only one side of the board.
- Double-sided: Conductive material on both sides of the board.
- Multilayer: Multiple double-sided boards stacked with insulating layers in between.
They can also be categorized based on the type of components they accommodate:
- Through-hole: Components with wire leads that are inserted into holes drilled through the board.
- Surface-mount: Components that are soldered directly onto the surface of the board.
Type | Description |
---|---|
Single-sided | Conductive material on one side |
Double-sided | Conductive material on both sides |
Multilayer | Multiple double-sided boards stacked |
Through-hole | Components inserted into holes |
Surface-mount | Components soldered onto surface |
Recent Trends in PCB Technology
High Density Interconnect (HDI) PCBs
HDI PCBs feature finer lines and spaces, smaller vias, and higher connection pad density than traditional PCBs. This allows for more complex circuits in a smaller space, which is essential for modern, compact electronic devices.
Flexible PCBs
Flexible PCBs are made from flexible, high-temperature plastic substrates. They can be bent and shaped to fit into tight spaces or conform to the shape of a device. They are increasingly used in wearable electronics, medical devices, and aerospace applications.
Rigid-Flex PCBs
Rigid-flex PCBs combine rigid and flexible PCB technologies. They consist of rigid PCBs connected by flexible circuits, allowing for three-dimensional configurations and improved vibration resistance.
Embedded Components
Embedded component PCBs have passive components like resistors and capacitors embedded within the layers of the board, rather than soldered onto the surface. This saves space and improves reliability.
Increased Use of Advanced Materials
The demand for high-performance PCBs has led to the increased use of advanced materials like polyimide, PTFE (Teflon), and ceramic substrates. These materials offer superior thermal, mechanical, and electrical properties compared to traditional FR-4 fiberglass.
Trend | Description |
---|---|
HDI PCBs | Finer lines, smaller vias, higher pad density |
Flexible PCBs | Made from flexible plastic, can be bent and shaped |
Rigid-Flex PCBs | Combines rigid and flexible PCBs |
Embedded Components | Passive components embedded within layers |
Advanced Materials | Use of polyimide, PTFE, ceramic substrates |
Future Outlook for PCBs
The future of PCBs is closely tied to the future of electronics. As electronic devices continue to become smaller, more powerful, and more complex, PCB technology will need to evolve to keep pace.
Some key areas of focus for the future of PCBs include:
- Increased miniaturization: The demand for smaller, more compact electronic devices will drive the development of even finer lines, smaller vias, and higher component densities.
- Advanced materials: The use of advanced materials like graphene and carbon nanotubes could lead to PCBs with superior electrical and thermal properties.
- 3D printing: The development of 3D printing technologies for PCBs could enable rapid prototyping and the creation of complex, three-dimensional circuit structures.
- Artificial Intelligence (AI) in design: The use of AI and machine learning in PCB design could help optimize circuit layouts, reduce design time, and catch potential issues early in the design process.
- Environmental sustainability: There will be a growing emphasis on developing PCB materials and manufacturing processes that are more environmentally friendly and sustainable.
Future Focus | Description |
---|---|
Miniaturization | Finer lines, smaller vias, higher densities |
Advanced Materials | Use of graphene, carbon nanotubes |
3D Printing | Rapid prototyping, complex 3D structures |
AI in Design | Optimized layouts, reduced design time |
Sustainability | Eco-friendly materials and processes |
FAQ
1. What are the advantages of using PCBs over other wiring methods?
PCBs offer several advantages over other wiring methods:
– Consistency: PCBs are manufactured to precise specifications, ensuring consistency between boards.
– Compact size: PCBs allow for complex circuits to be fitted into a small space.
– Reliability: The solid connections on a PCB are more reliable than loose wires or point-to-point soldering.
– Mass production: PCBs are designed for automated assembly, enabling mass production.
2. What’s the difference between through-hole and surface-mount PCBs?
Through-hole PCBs have components with wire leads that are inserted into holes drilled through the board. Surface-mount PCBs have components that are soldered directly onto the surface of the board. Surface-mount technology allows for smaller components and higher component density compared to through-hole.
3. What are multilayer PCBs and why are they used?
Multilayer PCBs are made by stacking multiple double-sided PCBs with insulating layers in between. They allow for even more complex circuits in a compact space. Multilayer PCBs are used in applications that require high component density and complex connectivity, such as smartphones, computers, and aerospace systems.
4. What are flexible PCBs and what are their advantages?
Flexible PCBs are made from flexible, high-temperature plastic substrates. They can be bent and shaped to fit into tight spaces or conform to the shape of a device. Flexible PCBs offer several advantages:
– Space savings: They can be fitted into tight, irregularly shaped spaces.
– Vibration resistance: Their flexibility provides better resistance to vibration and shock compared to rigid PCBs.
– Weight reduction: Flexible PCBs are generally lighter than equivalent rigid PCBs.
5. What is the future outlook for PCB technology?
The future of PCB technology is focused on increased miniaturization, the use of advanced materials, the adoption of 3D printing for rapid prototyping and complex structures, the integration of AI in the design process, and a growing emphasis on environmental sustainability. As electronic devices continue to evolve, PCB technology will need to advance to support the development of smaller, more powerful, and more complex electronics.
Conclusion
PCBs have come a long way since their early days in the early 20th century. From simple printed wire methods to today’s complex multilayer, HDI, and flexible designs, PCBs have continually evolved to meet the demands of the electronics industry.
As we look to the future, PCB technology will continue to advance, driven by the need for smaller, more powerful, and more environmentally friendly electronic devices. With ongoing developments in materials, manufacturing processes, design tools, and sustainability initiatives, PCBs are set to remain the backbone of the electronics world for the foreseeable future.
Leave a Reply