What is Curtain Coating?
Curtain coating is a high-speed, non-contact coating method used to apply a thin, uniform layer of liquid onto a moving substrate. In this process, a continuous curtain of coating liquid freely falls onto the substrate which is moving underneath the curtain. As the substrate passes through the falling curtain, it becomes coated with an even layer of the liquid material.
Curtain coating offers several advantages over other coating methods:
- High coating speeds (up to 600 m/min)
- Ability to apply very thin coatings (<10 microns)
- Excellent coating uniformity and smoothness
- Minimal waste of coating material
- Versatility to coat a wide range of substrates and liquids
Some common applications of curtain coating include applying functional coatings onto flexible substrates like plastic films, paper, textiles, metal foils, as well as coating solar cells, battery electrodes, optical films and more.
How Curtain Coating Works
In a curtain coating setup, the coating liquid is pumped from a reservoir and fed into a precision coating head which has a slot die or slide die configuration. As the liquid exits the coating head, it forms a thin, free-falling vertical curtain.
The substrate to be coated, such as a plastic film or paper web, is continuously transported on rollers and passed through the liquid curtain at a controlled speed. As the substrate intersects the curtain, it picks up an even layer of coating. The coated substrate then passes through a drying oven or UV curing station to dry/cure the wet coating.
Key components of a curtain coater include:
- Coating head – distributes coating evenly and forms uniform curtain
- Coating liquid delivery system – precisely meters and pumps coating fluid
- Substrate unwinding and rewinding units
- Web handling and steering units to control substrate transport
- Drying/curing unit – oven, UV lamps, electron beam, etc.
The coating thickness is controlled by parameters such as:
- Curtain flow rate
- Coating liquid properties (viscosity, density, surface tension)
- Substrate speed
- Coating gap (distance between coating head and substrate)
Advantages of Curtain Coating for LPI Application
LPI (Liquid Photoimageable) solder masks are polymer coatings used in printed circuit board (PCB) manufacturing to protect the copper circuits against corrosion and provide electrical insulation. Curtain coating is an attractive method for high-volume application of LPI solder masks onto PCBs due to its high productivity and coating quality.
Traditional screen printing of solder masks has limitations in terms of resolution, coating speed and material utilization. Curtain coating overcomes these challenges and offers benefits such as:
High Coating Speeds
Curtain coating can apply LPI solder masks at line speeds up to 150 m/min, which is 5-10 times faster than screen printing. This high productivity makes curtain coating suitable for high-volume PCB production.
Excellent Coating Uniformity
The free-falling curtain coats the PCB surface with a highly uniform layer, without any mesh marks, pinholes or other defects associated with screen printing. The smooth LPI coating provides reliable insulation and corrosion protection.
Wide Coating Thickness Range
By adjusting the curtain flow rate and line speed, a wide range of LPI coating thicknesses can be achieved, from <10 microns to >50 microns. Thin coatings enable finer circuit resolution, while thicker coatings provide greater protection in harsh environments.
Material Savings
Curtain coating is a low-waste process as almost all the coating liquid ends up on the substrate with minimal loss. In screen printing, a significant amount of solder mask paste sticks to the mesh and is wasted. Curtain coating can reduce material consumption by 30-50%.
Versatility
Curtain coating can handle a variety of solder mask types such as liquid photoimageable (LPI), dry film photoimageable (DFPI), and thermal curing masks. It can coat rigid FR-4 boards as well as flexible circuits. The coating rheology can be optimized for each material and application.
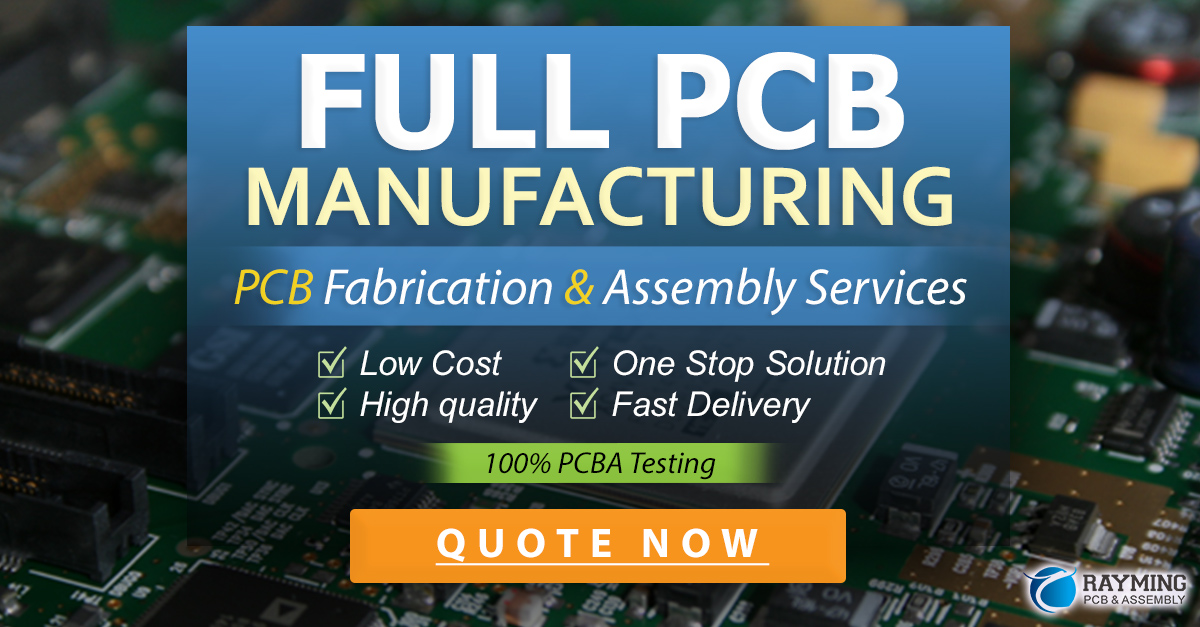
Challenges and Solutions in LPI Curtain Coating
While curtain coating offers compelling benefits for LPI application, there are also some technical challenges that need to be addressed for successful implementation:
Curtain Stability
Maintaining a stable, uniform coating curtain is critical for defect-free coating. Factors such as air currents, vibrations, and surface tension variations can cause curtain instability and breakup. Strategies to enhance curtain stability include:
- Using a precision coating head with optimized die geometry
- Maintaining laminar flow of coating liquid with minimal pulsations
- Controlling room air flow and installing curtain shields
- Adjusting coating rheology with additives to improve curtain rigidity
Edge Bead Reduction
Due to surface tension effects, curtain coated PCBs tend to have thicker coating deposits along the edges, known as edge beads. Edge beads can cause issues in downstream processes such as solder mask exposure, development and final assembly. Edge bead reduction methods include:
- Precision curtain edge guides to minimize coating overflow
- Adjustable coating dies to vary curtain width
- Selective edge maskants to prevent coating buildup
- Optimizing coating rheology to promote uniform spreading
Coating Defects
Curtain coated LPI solder masks can be prone to certain defects such as pinholes, fisheyes, and voids if the process parameters are not well controlled. Defect prevention measures include:
- Thorough cleaning and surface treatment of PCBs before coating
- Filtration of coating liquid to remove particles and bubbles
- Precise control of coating flow rate, viscosity and temperature
- Optimized drying/curing conditions to avoid solvent entrapment
LPI Curtain Coating Process Flow
A typical process flow for curtain coating of LPI solder masks onto PCBs is shown below:
Step | Process | Description |
---|---|---|
1 | PCB cleaning | Preclean boards to remove contaminants |
2 | Surface treatment | Microetching or plasma treatment for better adhesion |
3 | LPI curtain coating | Apply uniform LPI coating layer on PCB surface |
4 | Pre-drying | Partially dry coating to prevent sticking |
5 | Tack drying | Further dry coating to achieve handleability |
6 | Photoimaging | UV exposure and development to form solder mask pattern |
7 | Final curing | Thermal or UV curing to fully crosslink solder mask |
8 | Post-baking (optional) | Additional bake for enhanced properties |
9 | Final inspection | Automated optical or manual inspection of solder mask |
The LPI curtain coating process is compatible with standard PCB photoimaging and offers a high-speed, reliable method for solder mask application.
Equipment and Material Considerations
To implement LPI curtain coating, the following equipment and material factors should be considered:
Curtain Coater
A precision curtain coating machine is the heart of the LPI coating line. Key features to look for include:
- Slot die or slide die coating head for uniform curtain formation
- Precision flow control system for consistent coating delivery
- Adjustable coating width and gap settings
- Stable web handling and tensioning system
- Modular drying/curing units for different LPI types
- Automatic edge guide and thickness control
- Cleanroom compatibility for high-quality coating
LPI Solder Mask
The choice of LPI solder mask material is critical for successful curtain coating. The LPI should have:
- Rheological properties suitable for stable curtain formation
- Good wetting and leveling on PCB surface for uniform coverage
- Fast drying and curing characteristics for high productivity
- Excellent photoimaging resolution and edge definition
- Strong adhesion to copper and laminate surfaces
- Compliance with industry standards (IPC-SM-840, UL, RoHS, etc.)
Close collaboration between the LPI supplier and curtain coating equipment vendor is recommended to optimize the material-machine compatibility.
FAQ
What is the typical coating speed for LPI curtain coating?
LPI curtain coating can achieve line speeds of 100-150 m/min, depending on the coating thickness and curing requirements. This is much faster than traditional screen printing methods.
How thin can LPI curtain coatings be applied?
Curtain coating can apply LPI layers as thin as 5-10 microns in a single pass. Multiple passes can be used to build up the thickness if needed. The minimum thickness is limited by the curtain stability and coating rheology.
Is curtain coating suitable for both rigid and flexible PCBs?
Yes, curtain coating is applicable for both rigid FR-4 type PCBs and flexible circuits. The coating parameters and LPI material may need to be optimized for each substrate type to ensure good adhesion and coverage.
How does curtain coating compare with other solder mask application methods?
Compared to screen printing, curtain coating offers higher speed, better resolution, and lower material waste. It also provides a smoother, defect-free coating compared to roller coating or spray coating methods.
What is the typical capital investment for a curtain coating line?
The capital cost for a curtain coating line can vary widely depending on the throughput, substrate size, and automation level. A basic system may cost $500K-$1M, while a high-end, fully automated line can be $2M-$5M or more. The investment can be justified by the productivity gains and material savings compared to traditional methods.
Conclusion
Curtain coating is a high-speed, efficient method for applying LPI solder masks onto PCBs. It offers advantages such as excellent coating uniformity, wide thickness range, material savings, and versatility compared to traditional methods. While there are challenges such as curtain stability and edge bead control, these can be overcome with proper equipment design and process optimization.
As the electronics industry demands higher productivity and quality, curtain coating is poised to become the preferred method for LPI solder mask application. With its compelling benefits and continuous technological advancements, curtain coating will enable PCB manufacturers to meet the ever-increasing demands of the market.
Leave a Reply