Understanding the Factors Influencing PCB Costs
To effectively cut costs in PCB manufacturing, it is essential to understand the factors that contribute to the overall expenses. Some of the key elements that impact PCB costs include:
- Materials used (e.g., copper, substrate, solder mask)
- Board size and complexity
- Layer count and thickness
- Manufacturing process (e.g., etching, drilling, plating)
- Order quantity and lead time
- Quality control and testing requirements
By carefully analyzing these factors and making informed decisions, companies can optimize their PCB designs and manufacturing processes to achieve cost savings.
Strategies for Reducing PCB Manufacturing Costs
1. Optimize PCB Design
One of the most effective ways to cut PCB costs is by optimizing the board design. Here are some design considerations that can help reduce manufacturing expenses:
a. Minimize Board Size
Smaller PCBs require less material and are faster to manufacture, resulting in lower costs. Consider reducing the board size by:
- Using smaller components
- Arranging components efficiently
- Eliminating unnecessary features or spaces
b. Reduce Layer Count
Each additional layer in a PCB increases the manufacturing complexity and cost. Evaluate your design and determine if you can reduce the number of layers without compromising functionality. Strategies include:
- Combining power and ground planes
- Using blind and buried vias judiciously
- Optimizing component placement and routing
c. Standardize Materials and Processes
Using standard materials and manufacturing processes can help reduce costs by enabling bulk purchasing and streamlining production. Consider:
- Selecting commonly available substrate materials
- Using standard copper weights and thicknesses
- Adhering to industry-standard design rules and tolerances
2. Leverage Economies of Scale
Ordering larger quantities of PCBs can significantly reduce the per-unit cost. This is because the fixed costs associated with setup, tooling, and testing are spread across a larger number of boards. However, it is essential to balance the cost savings with the risk of obsolescence and storage costs.
Consider the following approaches:
- Consolidate multiple designs into a single panel
- Negotiate volume discounts with PCB Manufacturers
- Optimize order quantities based on demand forecasts and inventory management
3. Choose the Right PCB Manufacturer
Selecting a reliable and cost-effective PCB manufacturer is crucial for reducing overall expenses. When evaluating potential suppliers, consider the following factors:
- Manufacturing capabilities and expertise
- Quality control processes and certifications
- Pricing structure and volume discounts
- Lead times and delivery reliability
- Customer support and communication
Conducting thorough research, requesting quotes from multiple suppliers, and establishing long-term partnerships can help secure competitive pricing and high-quality PCB Services.
4. Implement Design for Manufacturing (DFM) Principles
Design for Manufacturing (DFM) is an approach that optimizes PCB designs to improve manufacturability and reduce costs. By incorporating DFM principles early in the design process, companies can avoid potential issues and unnecessary expenses. Some DFM techniques include:
- Adhering to manufacturer’s design guidelines
- Using standard component sizes and packages
- Providing adequate spacing between components
- Minimizing the use of vias and complex routing
- Incorporating testability features for efficient quality control
5. Optimize Testing and Quality Control
Effective testing and quality control processes are essential for ensuring the reliability and performance of PCBs. However, excessive or redundant testing can increase costs. To optimize testing and quality control, consider:
- Implementing automated testing systems
- Focusing on critical tests based on product requirements
- Leveraging statistical process control (SPC) techniques
- Collaborating with the PCB manufacturer to establish efficient testing protocols
Case Studies: Companies Successfully Reducing PCB Costs
To illustrate the effectiveness of cost-cutting strategies in PCB manufacturing, let’s examine a few real-world examples:
Company A: Redesigning for Cost Reduction
Company A, a consumer electronics manufacturer, faced increasing pressure to reduce the cost of their flagship product. By analyzing their PCB design, they identified several opportunities for optimization:
- Reducing the board size by 20% through efficient component placement
- Eliminating two layers by combining power and ground planes
- Standardizing the substrate material and copper thickness
As a result of these changes, Company A achieved a 25% reduction in PCB manufacturing costs without compromising product performance.
Company B: Strategic Sourcing and Volume Consolidation
Company B, a medical device manufacturer, relied on multiple PCB Suppliers for their various product lines. To streamline their supply chain and reduce costs, they implemented the following strategies:
- Conducted a comprehensive supplier evaluation and selected two strategic partners
- Consolidated PCB designs across product lines to increase order quantities
- Negotiated volume discounts and long-term pricing agreements
Through these efforts, Company B reduced their PCB Procurement costs by 18% and improved supplier relationships and delivery performance.
Company C: Implementing DFM and Automated Testing
Company C, an automotive electronics supplier, struggled with high PCB manufacturing costs due to design complexities and manual testing processes. To address these challenges, they:
- Collaborated with their PCB manufacturer to incorporate DFM principles in the design phase
- Simplified component placement and routing to improve manufacturability
- Invested in automated testing equipment and optimized test coverage
By implementing DFM and automated testing, Company C reduced their PCB manufacturing costs by 15% and improved product quality and reliability.
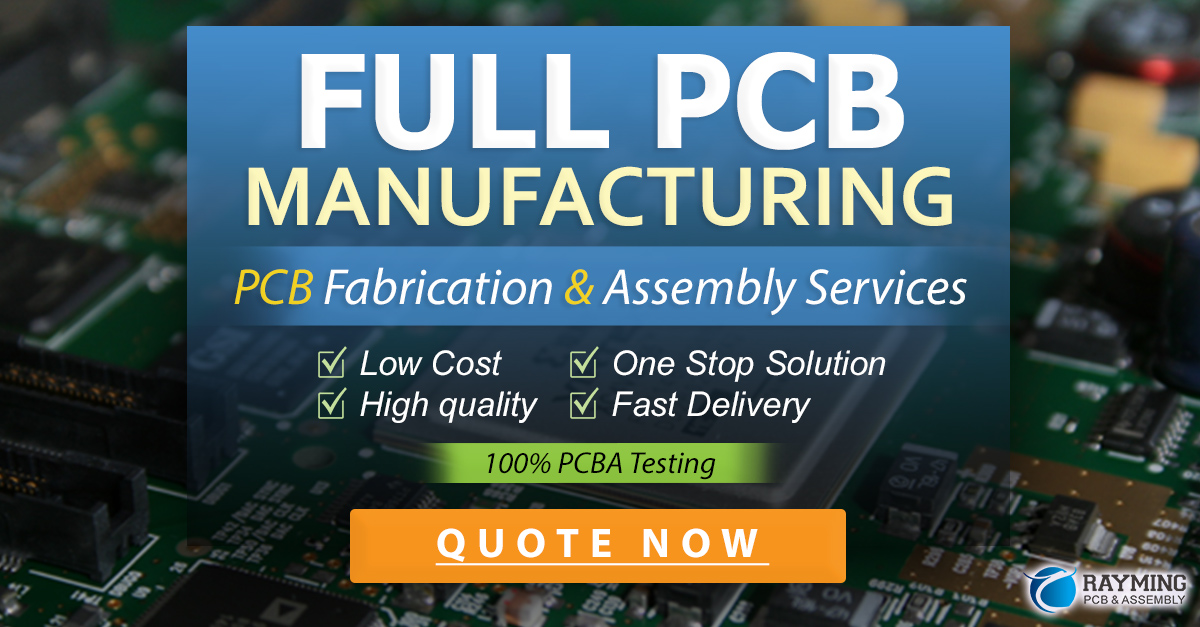
Frequently Asked Questions (FAQ)
-
Q: How can I determine if my PCB design is optimized for cost reduction?
A: Conduct a thorough design review with your PCB manufacturer or a DFM expert. They can provide insights on areas for optimization, such as board size reduction, layer count minimization, and component standardization. -
Q: Is it always better to order larger quantities of PCBs to reduce costs?
A: While ordering larger quantities can lead to cost savings, it is essential to consider factors such as demand forecasts, inventory holding costs, and the risk of obsolescence. Determine the optimal order quantity based on your specific business needs and market conditions. -
Q: How can I ensure the quality of PCBs while cutting costs?
A: Implement robust quality control processes, such as automated testing and statistical process control. Collaborate with your PCB manufacturer to establish clear quality requirements and testing protocols. Regularly monitor and analyze quality metrics to identify areas for improvement. -
Q: What are the risks associated with switching to a lower-cost PCB manufacturer?
A: Switching to a lower-cost manufacturer may come with risks such as lower quality, longer lead times, and communication challenges. Conduct thorough due diligence, request samples, and assess the manufacturer’s capabilities and reputation before making a switch. -
Q: How often should I review and update my PCB cost-cutting strategies?
A: Regularly review your PCB cost-cutting strategies, ideally on a quarterly or semi-annual basis. Stay informed about advancements in PCB manufacturing technologies, materials, and processes that could offer new opportunities for cost reduction.
Conclusion
Reducing PCB manufacturing costs is a critical objective for businesses aiming to remain competitive in today’s market. By understanding the factors influencing PCB costs and implementing effective strategies, companies can achieve significant savings without compromising on quality or performance.
Optimizing PCB designs, leveraging economies of scale, selecting the right manufacturer, implementing DFM principles, and optimizing testing and quality control are all essential elements of a comprehensive cost-cutting approach. By continually evaluating and refining these strategies, businesses can drive long-term cost savings and improve their bottom line.
As the electronic industry continues to evolve, staying proactive in identifying cost-cutting opportunities and adapting to new technologies and processes will be key to success. By embracing a culture of continuous improvement and collaboration with PCB manufacturing partners, companies can navigate the challenges of cost reduction and thrive in an increasingly competitive landscape.
Cost-Cutting Strategy | Description | Potential Cost Savings |
---|---|---|
Optimize PCB Design | Minimize board size, reduce layer count, standardize materials and processes | 10-30% reduction in PCB costs |
Economies of Scale | Consolidate designs, negotiate volume discounts, optimize order quantities | 15-25% reduction in per-unit cost |
Manufacturer Selection | Evaluate capabilities, pricing, quality control, lead times, and support | 10-20% reduction in overall costs |
Implement DFM Principles | Adhere to design guidelines, use standard components, minimize complexity | 10-15% reduction in manufacturing costs |
Optimize Testing and QC | Implement automated testing, focus on critical tests, leverage SPC techniques | 5-10% reduction in testing costs |
Note: The potential cost savings mentioned in the table are rough estimates and may vary depending on the specific circumstances and implementation of each strategy.
By combining multiple cost-cutting strategies and continuously monitoring and refining their approach, companies can maximize their PCB cost savings and maintain a strong competitive position in the market.
Leave a Reply