Introduction to Copper PCBs
Printed Circuit Boards (PCBs) are the backbone of modern electronics. They provide the electrical connectivity and mechanical support for electronic components in devices ranging from smartphones and laptops to industrial control systems and medical equipment. Among the various types of PCBs, copper PCBs stand out for their excellent electrical conductivity, thermal management, and durability.
Copper PCBs are made by laminating copper foil onto an insulating substrate, typically fiberglass or polyimide. The copper layer is then etched to create the desired circuit pattern. Copper’s high electrical conductivity allows for efficient signal transmission and low resistance, making it an ideal material for PCBs. Additionally, copper’s thermal conductivity helps dissipate heat generated by electronic components, preventing overheating and ensuring reliable performance.
Advantages of Copper PCBs
- High electrical conductivity
- Excellent thermal management
- Durability and resistance to corrosion
- Cost-effective compared to other materials
- Compatibility with a wide range of manufacturing processes
Copper PCB Manufacturing Process
The manufacturing process for copper PCBs involves several steps, each requiring precision and adherence to industry standards. Here’s an overview of the key stages in copper PCB fabrication:
1. PCB Design and Layout
The first step in creating a copper PCB is designing the circuit layout using specialized software such as Altium Designer, Eagle, or KiCad. The design must consider factors like component placement, trace width, spacing, and layer stackup. The output of this stage is a set of Gerber files that contain the necessary information for manufacturing.
2. Copper Lamination
The insulating substrate, usually FR-4 fiberglass, is laminated with copper foil on one or both sides. The copper thickness can vary depending on the application, with common options being 1 oz (35 μm), 2 oz (70 μm), and 4 oz (140 μm). The lamination process involves applying heat and pressure to bond the copper foil to the substrate.
3. Drilling and Hole Plating
Holes are drilled through the PCB to accommodate through-hole components and provide electrical connections between layers. The drilling process uses high-speed CNC machines with carbide drill bits. After drilling, the holes are plated with copper to ensure electrical continuity and prevent corrosion.
4. Etching and Patterning
The copper layer is selectively removed to create the desired circuit pattern. This is typically done using a photolithography process, where a photoresist layer is applied, exposed to UV light through a mask, and developed to reveal the areas to be etched. The exposed copper is then removed using a chemical etching solution, leaving behind the circuit traces.
5. Solder Mask Application
A solder mask layer is applied to the PCB to protect the copper traces from oxidation and prevent accidental short circuits during soldering. The solder mask is usually green but can be other colors as well. Openings in the solder mask are left for component pads and exposed copper areas.
6. Silkscreen Printing
A silkscreen layer is printed onto the PCB to add text, logos, and component identifiers. This helps with assembly and troubleshooting. The silkscreen is typically white but can be other colors for better visibility or aesthetic purposes.
7. Surface Finish
A surface finish is applied to the exposed copper areas to prevent oxidation and enhance solderability. Common surface finishes include:
- Hot Air Solder Leveling (HASL)
- Electroless Nickel Immersion Gold (ENIG)
- Immersion Silver (IAg)
- Organic Solderability Preservative (OSP)
The choice of surface finish depends on the application, cost, and compatibility with the assembly process.
8. Electrical Testing and Inspection
The completed PCBs undergo electrical testing and visual inspection to ensure they meet the required specifications. Automated optical inspection (AOI) systems check for manufacturing defects, while electrical testing verifies the continuity and isolation of the circuits. Boards that pass the testing are packaged and shipped to the customer.
Types of Copper PCBs
Copper PCBs can be classified based on the number of layers, the type of substrate, and the manufacturing process. Here are some common types of copper PCBs:
Single-Layer PCBs
Single-layer PCBs have copper on one side of the substrate and are used for simple, low-cost applications. They are easy to design and manufacture but have limited routing options and lower component density compared to multi-layer boards.
Double-Layer PCBs
Double-layer PCBs have copper on both sides of the substrate, allowing for more complex circuits and higher component density. They are the most common type of PCB and are used in a wide range of applications, from consumer electronics to industrial control systems.
Multi-Layer PCBs
Multi-layer PCBs have three or more layers of copper, separated by insulating layers. They offer the highest component density and routing options but are more expensive and complex to manufacture. Multi-layer PCBs are used in advanced applications like smartphones, laptops, and aerospace systems.
Flexible PCBs
Flexible PCBs use a flexible substrate, such as polyimide, instead of rigid fiberglass. They can bend and fold to fit into tight spaces or conform to curved surfaces. Flexible PCBs are used in applications that require flexibility, such as wearable devices, medical implants, and automotive electronics.
High-Frequency PCBs
High-frequency PCBs are designed for applications that operate at high frequencies, such as RF and microwave circuits. They use specialized substrates with low dielectric constant and loss tangent, as well as controlled impedance traces to minimize signal distortion and loss. High-frequency PCBs are used in telecommunications, radar, and satellite systems.
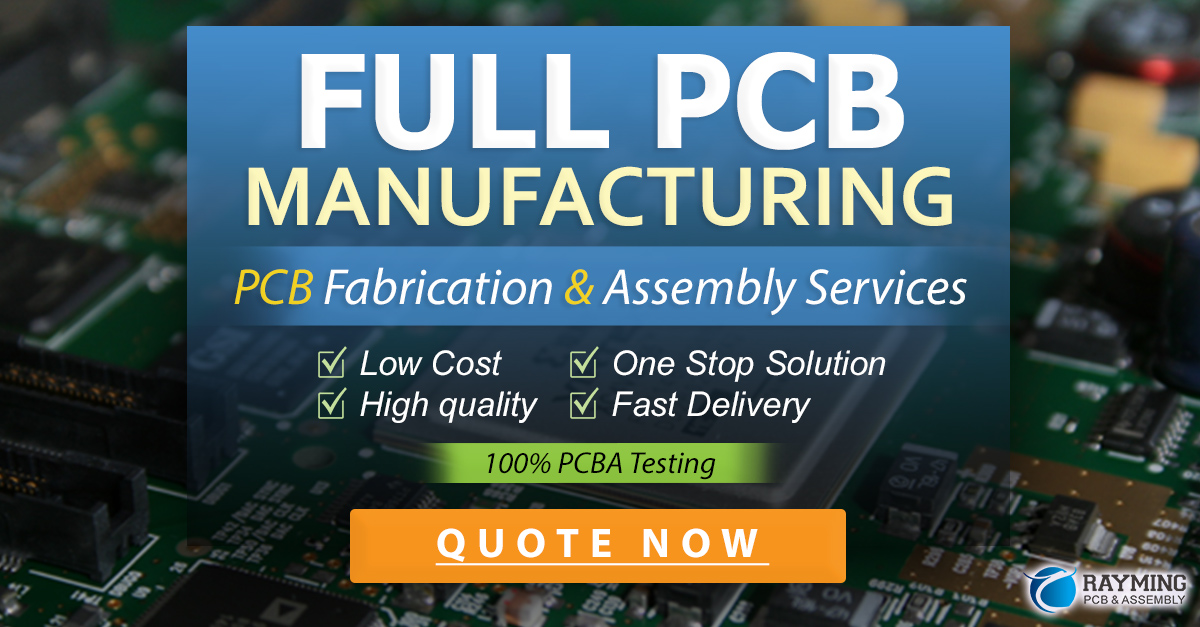
Copper PCB Manufacturers and Fabricators
Choosing the right copper PCB manufacturer or fabricator is crucial for ensuring the quality, reliability, and cost-effectiveness of your products. Here are some factors to consider when selecting a copper PCB supplier:
1. Technical Capabilities
Ensure that the manufacturer has the technical capabilities to meet your requirements, such as:
- Minimum feature size and trace width
- Layer count and thickness
- Material and surface finish options
- Impedance control and high-frequency design
- Certifications and standards compliance (e.g., IPC, UL, RoHS)
2. Quality Control
Look for manufacturers that have robust quality control systems in place, such as:
- Automated optical inspection (AOI)
- X-ray inspection
- Electrical testing
- Statistical process control (SPC)
- ISO 9001 certification
3. Lead Time and Capacity
Consider the manufacturer’s lead time and production capacity to ensure they can meet your delivery schedules and volume requirements. Look for suppliers with quick-turn prototyping services for faster product development.
4. Cost and Pricing
Compare pricing from multiple manufacturers, but don’t compromise on quality for the lowest price. Consider total cost of ownership, including shipping, duties, and potential rework costs.
5. Customer Support and Communication
Choose a manufacturer that offers responsive customer support and clear communication. They should be able to provide technical assistance, answer your questions promptly, and keep you informed of project status.
Top Copper PCB Manufacturers and Fabricators
Here’s a table of some top copper PCB manufacturers and fabricators, along with their key features and locations:
Manufacturer | Location | Key Features |
---|---|---|
Kinwong Electronic | China | – High-volume production – Multilayer and HDI PCBs – Automotive and medical certifications |
Shenzhen Dragon Bridge | China | – Flexible and rigid-flex PCBs – Quick-turn prototyping – ISO 9001 and ISO 14001 certified |
Würth Elektronik GmbH & Co. KG | Germany | – High-frequency and high-current PCBs – Embedded components – Controlled impedance and RF design |
Advanced Circuits | USA | – Online quoting and ordering – Free design for manufacturability (DFM) checks – IPC Class 2 and 3 certified |
Technotronix | India | – High-mix, low-volume production – Aluminum and copper-clad laminates – UL and RoHS compliant |
FAQ
1. What is the difference between copper thickness and copper weight?
Copper thickness is the physical thickness of the copper layer, measured in microns (μm) or mils (1 mil = 25.4 μm). Copper weight is the amount of copper per unit area, expressed in ounces per square foot (oz/ft²). The standard copper weights are 1 oz (35 μm), 2 oz (70 μm), and 4 oz (140 μm).
2. Can I mix different copper weights on the same PCB?
Yes, it is possible to have different copper weights on different layers of the same PCB. This is called a mixed-copper design and is often used to provide higher current carrying capacity on power layers while using thinner copper on signal layers to reduce cost and improve routing density.
3. What is the minimum trace width and spacing for copper PCBs?
The minimum trace width and spacing depend on the PCB manufacturer’s capabilities and the copper thickness. For standard 1 oz copper, a typical minimum trace width and spacing is 0.005″ (0.13 mm). Smaller features can be achieved with thinner copper or advanced manufacturing processes like HDI (high-density interconnect).
4. How does copper thickness affect PCB performance?
Thicker copper layers have lower resistance and higher current carrying capacity, which is beneficial for power distribution and high-current applications. However, thicker copper is more expensive and can make routing and manufacturing more challenging. Thinner copper is cheaper and allows for finer pitch traces but has higher resistance and lower current capacity.
5. What are the environmental considerations for copper PCBs?
Copper PCBs can have environmental impacts during manufacturing and disposal. Some key considerations are:
- Using lead-free solder and RoHS-compliant materials
- Properly handling and disposing of chemical etchants and wastewater
- Recycling scrap copper and other materials
- Complying with environmental regulations like REACH and WEEE
Look for manufacturers that have environmental certifications like ISO 14001 and follow best practices for sustainability.
Conclusion
Copper PCBs are a critical component in modern electronics, offering excellent electrical and thermal performance, durability, and cost-effectiveness. Understanding the manufacturing process, types of copper PCBs, and key considerations for selecting a manufacturer can help you make informed decisions and ensure the success of your projects.
When choosing a copper PCB manufacturer or fabricator, prioritize technical capabilities, quality control, lead time, cost, and customer support. By partnering with a reliable and experienced supplier, you can bring your designs to life with high-quality copper PCBs that meet your performance, reliability, and sustainability goals.
As technology continues to advance, copper PCBs will remain a fundamental building block for electronic devices across industries. Staying up-to-date with the latest developments in materials, manufacturing processes, and design tools will be essential for staying competitive in the fast-paced world of electronics.
Leave a Reply