Introduction to PCB component placement
Printed Circuit Board (PCB) component placement is a crucial step in the electronics manufacturing process. It involves the precise positioning and orientation of electronic components on the PCB Substrate. The primary goal of PCB component placement is to ensure optimal electrical performance, mechanical stability, and manufacturability of the final product.
The Importance of Proper Component Placement
Proper component placement is essential for several reasons:
- Signal Integrity: Optimal placement of components minimizes signal interference, crosstalk, and noise, ensuring the desired electrical performance of the circuit.
- Thermal Management: Strategic placement of heat-generating components, such as power transistors or Voltage Regulators, allows for efficient heat dissipation and prevents thermal-related issues.
- Mechanical Stability: Correct placement of components, especially heavy or tall ones, reduces mechanical stress on the PCB and minimizes the risk of component damage during assembly or operation.
- Manufacturing Efficiency: Well-planned component placement facilitates automated assembly processes, reduces assembly time, and minimizes the likelihood of assembly errors.
PCB Component Placement Considerations
When placing components on a PCB, several factors must be taken into account to ensure optimal performance and manufacturability.
1. Electrical Considerations
a. Signal Integrity
Signal integrity is a critical aspect of PCB design, and component placement plays a significant role in maintaining the quality of signals. High-speed digital circuits, analog circuits, and RF circuits require special attention to component placement to minimize signal degradation, crosstalk, and noise.
Here are some guidelines for component placement to ensure signal integrity:
- Place components with high-speed signals close to their respective connectors or drivers to minimize trace lengths and signal reflections.
- Separate digital and analog components to avoid interference between the two domains.
- Use ground planes and power planes to provide low-impedance return paths for signals and to shield sensitive traces from noise.
- Route critical signal traces away from potential noise sources, such as switching power supplies or high-current traces.
b. Power Distribution
Proper power distribution is essential for the reliable operation of the circuit. Component placement should consider the power requirements of each component and the overall power distribution network on the PCB.
Here are some guidelines for component placement related to power distribution:
- Place power supply components, such as voltage regulators, close to the power input connector to minimize the resistance and inductance of the power path.
- Locate decoupling capacitors close to the power pins of ICs to provide a stable power supply and reduce high-frequency noise.
- Distribute power and ground planes evenly across the PCB to minimize voltage drops and ensure uniform power distribution to all components.
2. Thermal Considerations
Thermal management is crucial for the long-term reliability and performance of electronic components. Proper component placement can help dissipate heat efficiently and prevent thermal-related issues.
a. Heat Generation and Dissipation
Some components, such as power transistors, voltage regulators, and high-speed processors, generate significant amounts of heat during operation. Placing these components strategically can help dissipate heat effectively.
Here are some guidelines for component placement related to heat generation and dissipation:
- Place heat-generating components near the edge of the PCB or close to mounting holes to allow for better airflow and heat dissipation.
- Provide sufficient spacing between heat-generating components to avoid thermal coupling and localized hot spots.
- Use thermal vias or heat sinks to conduct heat away from components and into the ambient environment or other cooling solutions.
b. Thermal Expansion and Contraction
PCBs and components undergo thermal expansion and contraction due to temperature changes during operation. This can lead to mechanical stress and potential failure of solder joints or components.
To minimize the impact of thermal expansion and contraction, consider the following:
- Place components with similar thermal expansion coefficients close to each other to minimize relative movement.
- Avoid placing large, heavy components near the corners of the PCB, where the maximum stress occurs due to thermal expansion.
- Use flexible mounting techniques, such as elastomeric connectors or underfill materials, to absorb thermal stresses in critical areas.
3. Mechanical Considerations
Component placement also affects the mechanical stability and reliability of the PCB Assembly.
a. Component Footprint and Orientation
The footprint and orientation of components on the PCB should be carefully considered to ensure proper soldering, inspection, and rework.
Here are some guidelines for component footprint and orientation:
- Align component footprints with the PCB grid to facilitate automated assembly and inspection processes.
- Orient polarized components, such as electrolytic capacitors or diodes, consistently to avoid assembly errors.
- Provide adequate spacing between components to allow for solder fillets and visual inspection of solder joints.
b. PCB Mounting and Vibration
Component placement should consider the mechanical stresses that the PCB may experience during mounting and operation, especially in environments with high vibration or shock.
To minimize the impact of mechanical stresses, consider the following:
- Place heavy components near mounting holes or support structures to reduce PCB deflection and vibration.
- Avoid placing tall components near the edges of the PCB, where they are more susceptible to mechanical damage.
- Use strain relief techniques, such as cable ties or adhesives, to secure cables and connectors and prevent mechanical stress on the PCB.
PCB Component Placement Techniques
Several techniques can be employed to optimize component placement on a PCB. These techniques help to balance the various electrical, thermal, and mechanical considerations discussed earlier.
1. Placement by Circuit Function
One approach to component placement is to group components by their circuit function. This technique helps to minimize signal trace lengths, reduce crosstalk, and simplify the overall PCB layout.
Here are some examples of placement by circuit function:
- Group power supply components, such as voltage regulators, capacitors, and inductors, near the power input section of the PCB.
- Place analog components, such as op-amps, transistors, and sensors, in a separate section of the PCB, away from digital components.
- Locate high-speed digital components, such as processors, memory, and interface ICs, close to their respective connectors or peripherals.
2. Placement by Component Size and Height
Another technique is to place components based on their size and height. This approach helps to optimize the use of PCB space, improve manufacturability, and minimize the impact of mechanical stresses.
Here are some guidelines for placement by component size and height:
- Place larger components, such as connectors and transformers, near the edges of the PCB to maximize available space for smaller components.
- Group components with similar heights together to facilitate automated assembly processes and minimize the risk of component damage during handling.
- Place taller components, such as electrolytic capacitors or heatsinks, away from the edges of the PCB to reduce the risk of mechanical damage.
3. Placement by Assembly Process
Component placement should also consider the assembly process used in manufacturing the PCB. Different assembly techniques, such as surface-mount technology (SMT) or through-hole technology (THT), have specific requirements for component placement.
Here are some guidelines for placement by assembly process:
- For SMT components, place them on the same side of the PCB to minimize the number of assembly steps and reduce manufacturing costs.
- For THT components, place them on the opposite side of the PCB from SMT components to facilitate Wave Soldering or manual assembly processes.
- Provide sufficient clearance around components to allow for automated pick-and-place machines or manual soldering tools to access the component pads.
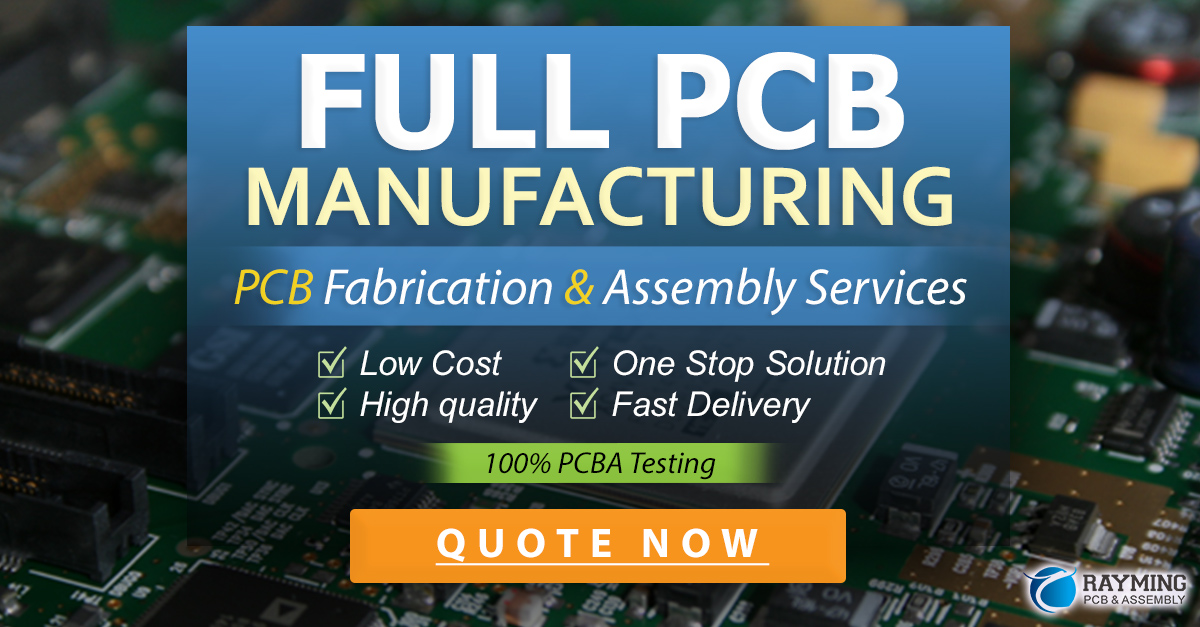
PCB Component Placement Tools and Software
To aid in the component placement process, various tools and software solutions are available. These tools help designers to optimize component placement, analyze potential issues, and generate manufacturing files.
1. PCB Design Software
PCB design software, such as Altium Designer, KiCad, or Eagle, provides a comprehensive environment for schematic capture, component placement, and PCB layout. These tools offer features like:
- Libraries of component footprints and symbols
- Automated component placement algorithms
- Design rule checking (DRC) to ensure compliance with manufacturing constraints
- 3D visualization of the PCB assembly
- Generation of manufacturing files, such as Gerber files and bill of materials (BOM)
2. Simulation Tools
Simulation tools help designers to analyze the performance of the PCB and identify potential issues before fabrication. Some common simulation tools include:
- SPICE simulators for analog and mixed-signal circuits
- Signal integrity simulators for high-speed digital circuits
- Thermal simulators for analyzing heat dissipation and thermal management
- Electromagnetic compatibility (EMC) simulators for assessing the PCB’s susceptibility to electromagnetic interference (EMI)
3. Collaboration and Version Control
Collaborative tools and version control systems help teams to work together efficiently on PCB designs and track changes throughout the development process. Some examples include:
- Git or SVN for version control of design files
- Cloud-based platforms for real-time collaboration and design review
- Project management tools for tracking tasks, issues, and deadlines
Best Practices for PCB Component Placement
To ensure optimal performance, manufacturability, and reliability of the PCB assembly, consider the following best practices for component placement:
- Start with a well-organized schematic: A clear and well-structured schematic helps to identify circuit blocks and guides the component placement process.
- Consider the PCB Stackup: The arrangement of copper layers and dielectric materials in the PCB stackup affects signal integrity, power distribution, and EMC. Plan the component placement accordingly.
- Use a modular approach: Divide the PCB into functional blocks and place components within each block to minimize signal trace lengths and simplify the layout.
- Follow manufacturer recommendations: Consult component datasheets and application notes for specific placement guidelines, such as required clearances or thermal management techniques.
- Iterate and refine: Component placement is an iterative process. Analyze the placement, identify potential issues, and refine the design until an optimal solution is achieved.
- Collaborate with stakeholders: Engage with mechanical engineers, manufacturing experts, and other stakeholders to ensure that the component placement meets all requirements and constraints.
- Document and communicate: Maintain clear documentation of the component placement decisions and rationale. Communicate the placement strategy to the team and stakeholders to ensure alignment and facilitate future revisions.
Factor | Consideration | Guidelines |
---|---|---|
Electrical | Signal integrity, power distribution | – Place high-speed components close to connectors or drivers – Separate digital and analog components |
Thermal | Heat generation and dissipation, thermal expansion and contraction | – Place heat-generating components near edges or mounting holes – Use thermal vias or heat sinks |
Mechanical | Component footprint and orientation, PCB mounting and vibration | – Align components with PCB grid – Place heavy components near mounting holes or support structures |
Frequently Asked Questions (FAQ)
-
Q: What is the importance of component placement in PCB design?
A: Component placement is crucial for ensuring optimal electrical performance, thermal management, mechanical stability, and manufacturability of the PCB assembly. Proper placement minimizes signal interference, reduces thermal issues, and facilitates automated assembly processes. -
Q: How does component placement affect signal integrity?
A: Component placement affects signal integrity by influencing trace lengths, crosstalk, and noise. Placing high-speed components close to their connectors or drivers, separating digital and analog components, and using ground and power planes help to maintain signal integrity. -
Q: What are some thermal considerations in component placement?
A: Thermal considerations include placing heat-generating components near the edge of the PCB or close to mounting holes for better heat dissipation, providing sufficient spacing between components to avoid thermal coupling, and using thermal vias or heat sinks to conduct heat away from components. -
Q: How can component placement impact the mechanical stability of a PCB?
A: Component placement can impact mechanical stability by affecting the distribution of mechanical stresses on the PCB. Placing heavy components near mounting holes or support structures, avoiding tall components near the edges, and using strain relief techniques for cables and connectors help to improve mechanical stability. -
Q: What are some common tools and software used for PCB component placement?
A: PCB design software, such as Altium Designer, KiCad, or Eagle, is commonly used for component placement. These tools offer features like component libraries, automated placement algorithms, and design rule checking. Simulation tools for signal integrity, thermal analysis, and EMC are also used to analyze the performance of the PCB assembly.
Conclusion
PCB component placement is a critical aspect of electronics manufacturing that directly impacts the performance, reliability, and manufacturability of the final product. By considering electrical, thermal, and mechanical factors, and employing various placement techniques and tools, designers can optimize the component placement to ensure the best possible outcome.
Following best practices, such as starting with a well-organized schematic, using a modular approach, and collaborating with stakeholders, can further enhance the quality and efficiency of the component placement process.
As PCB technology continues to advance, with increasing complexity and miniaturization of components, the importance of proper component placement will only grow. Designers who master the art and science of PCB component placement will be well-equipped to create high-performance, reliable, and cost-effective electronic products.
Leave a Reply