The Importance of Electrical Testing in PCB Manufacturing
Electrical testing is vital in PCB manufacturing for several reasons:
- Ensuring the functionality of the PCB
- Identifying and rectifying defects early in the manufacturing process
- Verifying the compliance with design specifications and industry standards
- Improving the overall quality and reliability of the end product
By conducting thorough electrical testing, manufacturers can minimize the risk of product failures, reduce costs associated with rework and repairs, and enhance customer satisfaction.
Types of Electrical Tests in PCB Manufacturing
There are various types of electrical tests performed during PCB manufacturing, each focusing on different aspects of the board’s electrical performance. Some of the key electrical tests include:
1. Continuity Testing
Continuity testing is performed to ensure that all the intended electrical connections on the PCB are intact and there are no open circuits. This test is typically carried out using a multimeter or a dedicated continuity tester. The test probes are placed on the relevant test points, and the resistance between them is measured. A low resistance value indicates a proper connection, while a high resistance or open circuit suggests a problem that needs to be addressed.
2. Short Circuit Testing
Short circuit testing is conducted to identify any unintended electrical connections between different points on the PCB. Short circuits can occur due to manufacturing defects, such as solder bridges or conductive debris, and can lead to malfunctions or even damage to the components. Short circuit testing is performed using specialized equipment that applies a voltage to the test points and measures the current flow. If the current exceeds a predetermined threshold, it indicates the presence of a short circuit.
3. Insulation Resistance Testing
Insulation resistance testing measures the resistance between different conductive parts of the PCB that should be electrically isolated from each other. This test ensures that there is sufficient insulation between these parts to prevent leakage currents and maintain the integrity of the electrical signals. Insulation resistance testing is typically performed using a high-voltage insulation tester, which applies a specified voltage between the test points and measures the resulting resistance.
4. Dielectric Withstand Testing
Dielectric withstand testing, also known as hipot (high potential) testing, is performed to verify the insulation integrity of the PCB and its ability to withstand high voltages without breakdown. This test is crucial for ensuring the safety and reliability of the end product, especially in applications where high voltages are involved. During the test, a high voltage is applied between the conductive parts of the PCB and the ground plane, and the leakage current is monitored. If the leakage current exceeds a specified limit, it indicates a breakdown in the insulation, and the PCB fails the test.
5. Functional Testing
Functional testing is performed to verify that the PCB operates as intended and meets the specified performance requirements. This test involves powering up the board and testing its various functions, such as signal processing, communication, and input/output operations. Functional testing can be performed manually or using automated test equipment (ATE) that follows a predetermined test sequence and compares the results with expected values.
Test Coverage and Sampling
When conducting electrical testing in PCB manufacturing, it is important to consider the test coverage and sampling strategy. Test coverage refers to the extent to which the various aspects of the PCB’s electrical performance are tested. A higher test coverage provides greater assurance of the board’s quality and reliability but also increases the testing time and cost.
Sampling is the process of selecting a representative subset of the manufactured PCBs for testing, rather than testing every single board. The sampling strategy depends on factors such as the production volume, the criticality of the application, and the acceptable quality level (AQL). Common sampling methods include:
- 100% testing: Every PCB is tested, providing the highest level of assurance but also the highest testing cost and time.
- Lot sampling: A random sample of PCBs from each production lot is tested, providing a balance between testing cost and quality assurance.
- Periodic sampling: PCBs are tested at regular intervals, such as every nth board or every nth hour of production.
The choice of sampling method should be based on a risk assessment and the specific requirements of the end product.
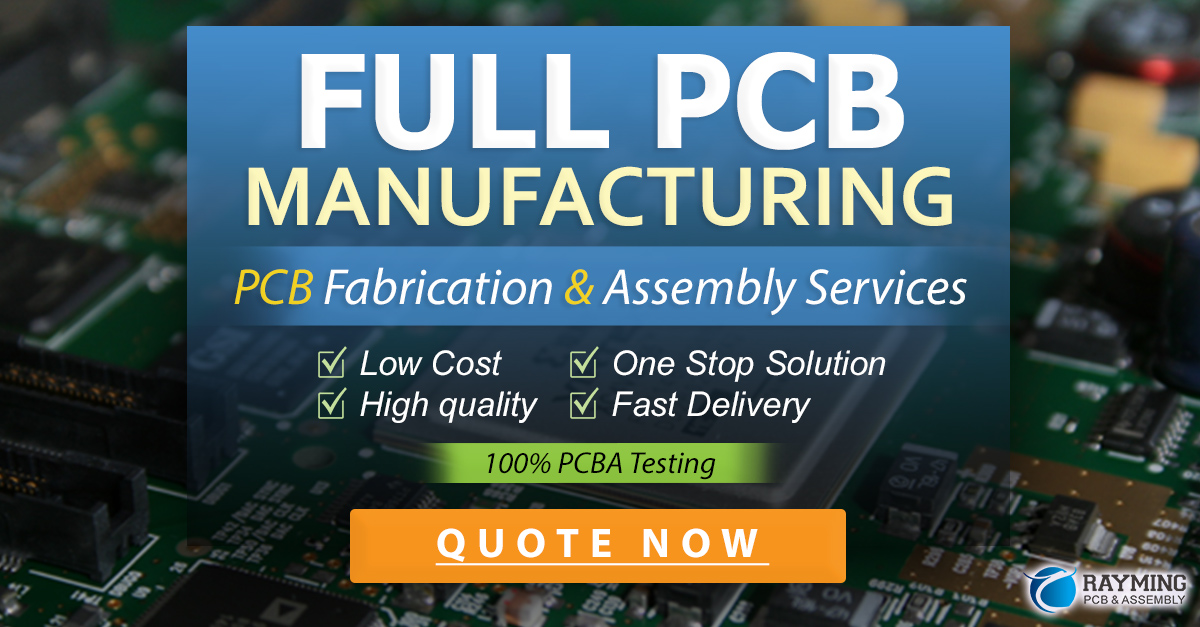
Test Equipment and Automation
Electrical testing in PCB manufacturing relies on various types of test equipment, ranging from basic tools like multimeters and oscilloscopes to advanced automated test equipment (ATE). ATE systems are computer-controlled test platforms that can perform a wide range of electrical tests on PCBs with high speed, accuracy, and repeatability.
Some common types of ATE used in PCB Testing include:
- In-circuit testers (ICT): ICT systems use a bed-of-nails fixture to make direct electrical contact with the test points on the PCB and perform a variety of tests, such as continuity, short circuit, and component value measurements.
- Flying probe testers: Flying probe testers use movable test probes that can access different points on the PCB without the need for a dedicated test fixture. They offer flexibility and are suitable for low-volume or prototype testing.
- Boundary scan testers: Boundary scan testers rely on a built-in test access port (TAP) on the PCB and the boundary scan architecture (IEEE 1149.1) to test the interconnections and functionality of the board’s digital components.
Automated testing offers several advantages over manual testing, including:
- Faster test execution and higher throughput
- Improved test consistency and repeatability
- Reduced human error and operator fatigue
- Automatic data logging and report generation
However, automated testing also requires a higher initial investment in equipment and programming and may not be cost-effective for low-volume production or simple PCB designs.
Test Data Analysis and Reporting
Electrical testing in PCB manufacturing generates a large amount of data that needs to be analyzed and reported to ensure proper process control and continuous improvement. Test data analysis involves:
- Reviewing test results to identify patterns, trends, and anomalies
- Comparing test results with specified limits and thresholds
- Calculating key performance indicators (KPIs) such as first-pass yield, defect density, and test coverage
- Identifying the root causes of failures and implementing corrective actions
Test data should be stored in a centralized database and made accessible to relevant stakeholders, such as quality engineers, process engineers, and management. Regular reporting of test results and KPIs helps monitor the performance of the manufacturing process and drive continuous improvement initiatives.
Best Practices for Electrical Testing in PCB Manufacturing
To ensure the effectiveness and efficiency of electrical testing in PCB manufacturing, consider the following best practices:
- Develop a comprehensive test plan that covers all the relevant electrical tests and defines the test coverage, sampling strategy, and acceptance criteria.
- Design for testability by incorporating test points, boundary scan architecture, and other features that facilitate electrical testing.
- Use appropriate test equipment and automation to maximize test speed, accuracy, and consistency.
- Establish a robust test data management system to store, analyze, and report test results effectively.
- Regularly review and update test programs to keep pace with changes in product design, manufacturing processes, and quality requirements.
- Train and certify operators on the proper use of test equipment and procedures to ensure consistent and reliable test execution.
- Foster a culture of continuous improvement by encouraging the sharing of test data, root cause analysis, and the implementation of corrective and preventive actions.
Frequently Asked Questions (FAQ)
- What is the difference between continuity testing and short circuit testing?
-
Continuity testing verifies that intended electrical connections are intact, while short circuit testing identifies unintended connections between different points on the PCB.
-
How often should PCBs be tested during the manufacturing process?
-
The frequency of testing depends on factors such as production volume, product complexity, and quality requirements. A combination of sampling methods, such as lot sampling and periodic sampling, is often used to balance testing cost and quality assurance.
-
What is the purpose of dielectric withstand testing?
-
Dielectric withstand testing verifies the insulation integrity of the PCB and its ability to withstand high voltages without breakdown, ensuring the safety and reliability of the end product.
-
What are the advantages of using automated test equipment (ATE) for PCB testing?
-
ATE offers faster test execution, improved consistency and repeatability, reduced human error, and automatic data logging and reporting. However, it requires a higher initial investment and may not be cost-effective for low-volume production or simple PCB designs.
-
How can test data analysis contribute to continuous improvement in PCB manufacturing?
- Test data analysis helps identify patterns, trends, and anomalies in test results, calculate key performance indicators, and identify the root causes of failures. Regular reporting of test results and KPIs helps monitor the performance of the manufacturing process and drive continuous improvement initiatives.
Conclusion
Electrical testing is a critical aspect of PCB manufacturing that ensures the quality, reliability, and functionality of the end product. By conducting a range of electrical tests, such as continuity, short circuit, insulation resistance, dielectric withstand, and functional testing, manufacturers can identify and rectify defects early in the process, verify compliance with design specifications, and improve overall product quality.
Effective electrical testing in PCB manufacturing requires careful consideration of test coverage, sampling strategies, test equipment, and automation. By following best practices and fostering a culture of continuous improvement, manufacturers can optimize their testing processes, reduce costs, and enhance customer satisfaction.
As PCB technology continues to evolve, with increasing complexity and miniaturization, the importance of comprehensive and efficient electrical testing will only grow. By staying up-to-date with the latest testing methods, equipment, and standards, PCB manufacturers can position themselves to meet the ever-growing demands of the electronics industry and deliver high-quality, reliable products to their customers.
Test Type | Purpose | Equipment |
---|---|---|
Continuity Testing | Verify intended electrical connections | Multimeter, continuity tester |
Short Circuit Testing | Identify unintended electrical connections | Short circuit tester |
Insulation Resistance Testing | Measure resistance between isolated parts | High-voltage insulation tester |
Dielectric Withstand Testing | Verify insulation integrity and high-voltage withstand | Hipot tester |
Functional Testing | Verify PCB operation and performance | Manual or automated test equipment |
Leave a Reply