Introduction to High-Speed PCB Design
High-speed PCB design is a complex process that requires careful consideration of various factors to ensure optimal performance and reliability. As technology advances and electronic devices become more sophisticated, the demand for high-speed PCBs continues to grow. However, designing high-speed PCBs comes with its own set of challenges and considerations that must be addressed to ensure a successful project outcome.
In this article, we will explore the key challenges and top considerations for high-speed PCB design, providing valuable insights and best practices to help you navigate the complexities of this process.
Understanding the Challenges of High-Speed PCB Design
Signal Integrity Issues
One of the primary challenges in high-speed PCB design is maintaining signal integrity. As signal frequencies increase, the potential for signal distortion, crosstalk, and electromagnetic interference (EMI) also increases. These issues can lead to data corruption, system malfunctions, and overall performance degradation.
To mitigate signal integrity issues, designers must carefully consider factors such as trace routing, impedance matching, and proper termination techniques. Additionally, the use of advanced simulation tools and analysis methods can help identify and address potential signal integrity problems early in the design process.
Power Integrity Concerns
Another critical challenge in high-speed PCB design is ensuring power integrity. As high-speed devices consume more power and operate at lower voltages, the risk of power supply noise and voltage fluctuations increases. These issues can lead to signal jitter, false switching, and reduced system reliability.
To maintain power integrity, designers must implement proper power distribution networks, including the use of decoupling capacitors, voltage regulators, and power planes. It is also essential to minimize the inductance and resistance of power delivery paths to reduce voltage drops and ensure stable power supply to all components.
Thermal Management
High-speed PCBs often generate significant amounts of heat due to the increased power consumption and higher operating frequencies. Inadequate thermal management can lead to component failure, reduced performance, and shortened product lifespan.
Effective thermal management strategies include the use of heat sinks, thermal vias, and proper component placement to facilitate heat dissipation. Additionally, designers should consider the thermal properties of PCB materials and use thermal simulation tools to predict and optimize the thermal performance of the board.
EMI and EMC Compliance
Electromagnetic interference (EMI) and electromagnetic compatibility (EMC) are critical concerns in high-speed PCB design. High-frequency signals can generate unwanted emissions that interfere with other electronic devices and violate regulatory standards.
To achieve EMI and EMC compliance, designers must incorporate appropriate shielding techniques, such as the use of ground planes, shielded connectors, and proper grounding practices. Additionally, conducting EMI/EMC testing and simulations can help identify and mitigate potential issues before the final production stage.
Top Considerations for Successful High-Speed PCB Design
Material Selection
The choice of PCB materials plays a vital role in high-speed design. The dielectric constant (Dk) and dissipation factor (Df) of the material directly impact signal propagation, impedance, and loss characteristics.
When selecting PCB materials for high-speed applications, designers should consider factors such as:
- Low Dk and Df values to minimize signal loss and distortion
- Consistent dielectric properties over the desired frequency range
- Thermal stability and mechanical strength to withstand manufacturing processes and operating conditions
Common high-speed PCB materials include FR-4, Rogers, and Isola laminates, each with their own advantages and limitations.
Stackup Design
The PCB stackup design is another critical consideration in high-speed design. The arrangement of signal, power, and ground layers can significantly impact signal integrity, power distribution, and EMI performance.
When designing the stackup, designers should:
- Use dedicated power and ground planes to provide low-impedance power distribution and reduce noise coupling
- Maintain consistent dielectric thickness between signal layers to control impedance and minimize signal reflections
- Use symmetrical stackups to balance copper distribution and minimize warpage during manufacturing
- Consider the use of shielding layers and guard traces to isolate sensitive signals and reduce crosstalk
Trace Routing and Impedance Control
Proper trace routing and impedance control are essential for maintaining signal integrity in high-speed PCBs. Traces should be routed to minimize signal reflections, crosstalk, and EMI while maintaining the desired characteristic impedance.
Key considerations for trace routing and impedance control include:
- Using controlled impedance traces, such as microstrip or stripline, to match the impedance of the source and load
- Minimizing trace lengths and avoiding sharp bends or discontinuities to reduce signal reflections and distortion
- Providing adequate spacing between traces to minimize crosstalk and EMI
- Using differential pair routing for high-speed signals to improve noise immunity and reduce EMI
Via Design and Placement
Vias are essential for interconnecting different layers of a PCB, but they can also introduce signal integrity and EMI issues in high-speed designs. Poorly designed or placed vias can cause impedance discontinuities, signal reflections, and radiated emissions.
To optimize via design and placement, designers should:
- Minimize the number of vias in high-speed signal paths to reduce discontinuities and reflections
- Use controlled-depth vias, such as blind or buried vias, to reduce stub lengths and improve signal integrity
- Provide adequate via-to-via spacing to minimize crosstalk and EMI
- Consider the use of via stitching or shielding to reduce radiated emissions and improve EMI performance
Simulation and Analysis
Simulation and analysis tools are essential for predicting and optimizing the performance of high-speed PCBs before manufacturing. These tools can help designers identify and address potential signal integrity, power integrity, and EMI issues early in the design process.
Common simulation and analysis techniques for high-speed PCB design include:
- Signal integrity simulation: Analyzing signal propagation, reflections, and crosstalk using tools such as SPICE or S-parameter models
- Power integrity simulation: Evaluating power distribution networks, voltage drops, and decoupling capacitor placement using tools such as SPICE or finite element analysis (FEA)
- EMI/EMC simulation: Predicting radiated emissions and identifying potential EMI issues using tools such as full-wave electromagnetic solvers or finite-difference time-domain (FDTD) methods
- Thermal simulation: Analyzing the thermal performance of the PCB and identifying potential hotspots using tools such as computational fluid dynamics (CFD) or FEA
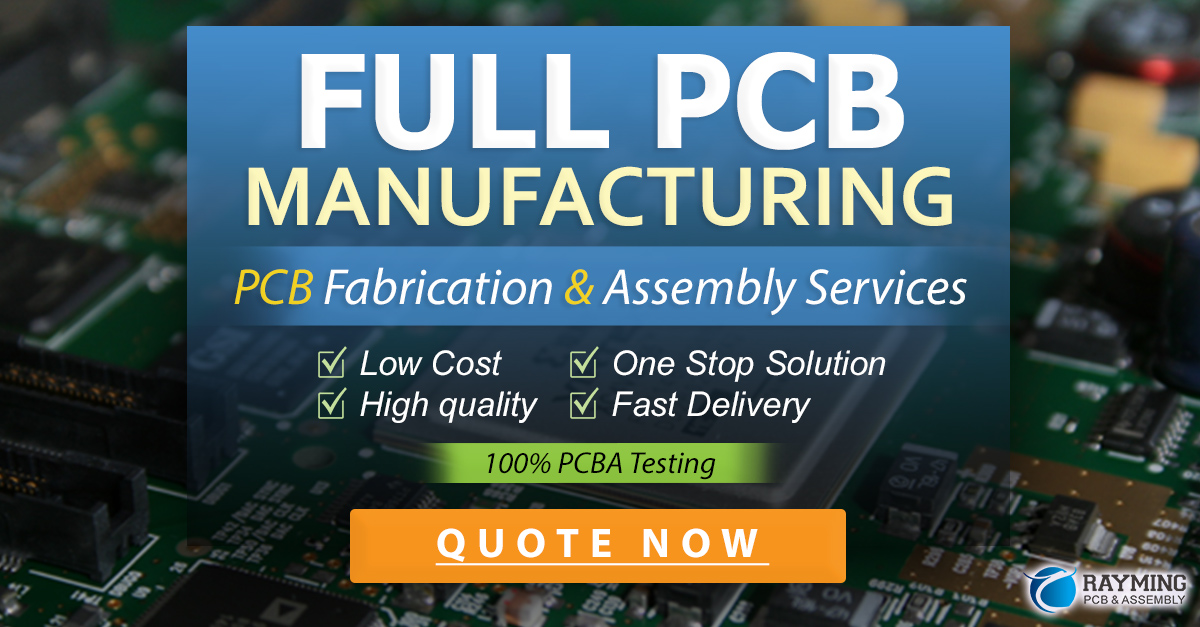
Frequently Asked Questions (FAQ)
1. What are the most common signal integrity issues in high-speed PCB design?
The most common signal integrity issues in high-speed PCB design include signal reflections, crosstalk, and attenuation. These issues can be caused by factors such as improper trace routing, impedance mismatches, and inadequate via design.
2. How can I ensure power integrity in my high-speed PCB design?
To ensure power integrity in high-speed PCB design, you should use dedicated power and ground planes, optimize decoupling capacitor placement, and minimize the inductance and resistance of power delivery paths. Additionally, conducting power integrity simulations can help identify and address potential issues.
3. What are the key considerations for selecting PCB materials for high-speed applications?
When selecting PCB materials for high-speed applications, you should consider factors such as low dielectric constant (Dk) and dissipation factor (Df) values, consistent dielectric properties over the desired frequency range, and thermal stability and mechanical strength. Common high-speed PCB materials include FR-4, Rogers, and Isola laminates.
4. How can I minimize EMI in my high-speed PCB design?
To minimize EMI in high-speed PCB design, you can use shielding techniques such as ground planes, shielded connectors, and proper grounding practices. Additionally, conducting EMI/EMC simulations and testing can help identify and mitigate potential issues before the final production stage.
5. What are the benefits of using simulation and analysis tools in high-speed PCB design?
Simulation and analysis tools can help designers predict and optimize the performance of high-speed PCBs before manufacturing. These tools can identify and address potential signal integrity, power integrity, and EMI issues early in the design process, reducing the risk of costly redesigns and improving overall product quality and reliability.
Conclusion
Designing high-speed PCBs is a complex and challenging process that requires careful consideration of various factors to ensure optimal performance and reliability. By understanding the key challenges and implementing the top considerations discussed in this article, designers can navigate the complexities of high-speed PCB design and create successful projects.
From material selection and stackup design to trace routing and simulation techniques, each aspect of high-speed PCB design plays a critical role in achieving the desired performance and meeting the ever-increasing demands of modern electronic devices.
By staying up-to-date with the latest best practices, utilizing advanced tools and methodologies, and collaborating with experienced professionals, designers can overcome the challenges of high-speed PCB design and deliver innovative, reliable, and high-performing products to the market.
Leave a Reply