Ceramic PCBs, which are also described as a ceramic hybrid circuit device, is now the new standard for the industry for different electrical components. Though the technology was initially introduced by the ceramic capacitor that is now utilized in several applications.
Our ceramic materials’ properties are utilized in the process of manufacturing ceramic PCBs more reliable, durable, as well as an effective option to several electrical components. This isn’t the normal ceramic that could be seen in potteries, flooring, or decors, as the ceramic boards are manufactured from high-quality materials having metal cores.
Also, they might be referred to as green boards, not just due to the color, but due to the fact that they make use of a few toxic materials as well as have smaller carbon footprints compared to the traditional counterparts.
What are Ceramic PCB Substrates?
Ceramic PCB substrates are usually manufactured from ceramic materials, which are usually inorganic dielectric rather than epoxy resin bases or fiberglass. These are electronic circuit boards that are manufactured from a thin ceramic insulating layer featuring metal components.
Packages and substrates are usually needed for ICs so as to maintain and achieve reliability. These integrated circuits require insulating materials and both can serve the purpose. The packages would be then mounted onto the PCB.
Furthermore, ceramics are known for their great insulation properties. The advanced protection property of this ceramic material is a very important factor to be utilized as packages and substrates. This is exactly what makes the ceramic PCB stand out from the remaining.
As a result of its great gas tightness and heat conductivity performance, the ceramic PCB is widely utilized in hybrid microelectronics, power electronics, multi-chip modules, and electronics packaging. In addition, its great conductivity is very important in different applications like power generation, whereby large currents have to be passed into the material.
What are the Properties of the Ceramic PCB Substrate Material?
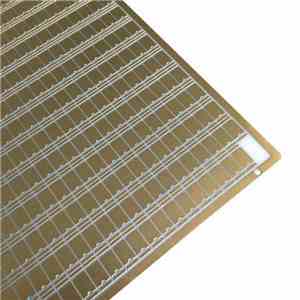
There are three common ceramic materials used for PCB manufacturing.
Aluminum Nitride (AlN)
AlN has a high thermal expansion coefficient as well as thermal conductivity, which makes it important as the ceramic pcb substrate material used in the printed circuit board industry. AlN’s thermal conductivity varies within the 170 W/mK and 220W/mK range. AlN’s coefficient of thermal expansion is similar to that of the silicon semiconductor chips that establishes great bonding between the both, thereby ensuring a reliable assembly.
In addition, AlN is utilized in automobile’ sensor circuits, as it has the ability to withstand any harsh and extreme temperature, vibration, and corrosion when offering sensitive, accurate, as well as efficient sensor signals.
Alumina (Al2O3)
The benefits of the Alumina compared to the other ceramic materials are their chemical stability, mechanical strength, electrical properties, and thermal conductivity. The raw material abundance makes the alumina a well-utilized ceramic pcb substrate material.
In addition, Al2O3 ceramic printed circuit boards are useful in shock absorbers, automobile sensor circuits, as well as engines. Al2o3 ceramic PCB’s great thermal stability helps in improving the thermal efficiency as well as performance of circuits utilized in automobiles.
Beryllium Oxide (BeO)
This is a well-known ceramic PCB substrate material having a nine time thermal conductivity of that of the Al2O3, as well as higher than the metal aluminum. Also, BeO features a more effective stability compared to the AlN substrate as well as a high electrical isolation in contrast to the Al2O3e.
Furthermore, BeO is utilized in different applications whereby a printed circuit board is subjected to extremely high temperatures as well as high density printed circuit boards that face space limitations for delivering liquid or air cooling.
Also, asides from its high electrical insulation property, it comes with a higher thermal conductivity compared to other non-metals, with diamond, the exception; even it surpasses the value some metals possess. Beryllium oxide features rigid bonds in-between the atoms like the diamond does. Also, it helps in the transmission of heat in the form of vibrations across the strong bonds and this is why the loss of energy is reduced.
Thermal Conductivity of the Ceramic PCB Substrate
High thermal conductivity of the ceramic PCB substrate is the main reason that more industries are now leaning towards ceramics during their PCBs as well as the packages since the base material features a better advantage over the traditional materials. Amore effective CTE matching as well as hermetic sealing would just add to these materials’ appeal.
The challenge of using ceramic base materials as well as the boards the PCB manufacturer creates out of them is that they are more expensive compared to traditional PCB materials. This could significantly add up over the period of the high-volume jobs. Moreover, ceramic boards come with great benefits and there is a need for a higher thermal conductivity that companies having the ability to afford ceramic boards would do this out of necessity.
What are the Benefits of the Ceramic PCB Substrate?
Dissipation of heat is one main benefit which ceramic possesses over extra conventional materials like metal clad PCBs and FR4. Due to the fact that the placement of components is done on the board directly, and no layer of isolation exists, the heat flow via the boards is much more efficient. Furthermore, ceramic materials could suffer from huge operating temperatures (reaching 350 degrees centigrade). Also, its CTE is quite low; this allows for more compatibility options for the PCB design.
In contrast to the traditional printed circuit boards having substrate materials as polyimide, epoxy glass fiber, phenol and polystyrene resin, ceramic printed circuit boards gave the properties below.
- Resists a chemical erosion
- Great thermal conductivity
- Mechanical intensity that is compatible
- CTA components compatibility
- Easy to execute high-density tracing
It is obvious why ceramic PCB has been very popular. Below are the reasons
Stability
Due to the utilization of ceramic, the dielectric property would be stable, and the balance will be able to change to a limited loss in radio frequency to ensure electronic device’s applicability. Furthermore, despite its outward toughness, this ceramic can resist the majority of chemicals utilized due to the PCB having a ceramic base. This is why, resisting chemicals would result in changes in the resistance to solvents, moisture, and consumables.
High thermal expansion
Ceramic PCBs are widely utilized in our electronic industry due to their high coefficient of thermal expansion. Also, the thermal conductivity of the ceramic base is very close to that of silicon, wholly underneath the majority of used connection metals. It could serve as great isolators. Therefore you can have optimum property for a great thermal conductivity even when under an elevated temperature to ensure its utilization in many devices.
Versatility
It’s clear that the integration of the metal core printed circuit board has the ability to work for many applications having high melting points. This notable metal paste could be unfailing conductors due to the sintering technology.
Therefore the utilization of ceramic PCBs will create the effect on becoming high processing temperatures whereby different devices exist for several operating temperatures. Another interesting fact is that it permits great thermal conductivity as well as heat distribution to the different positions of the device.
Adaptability
Another important reason for using ceramic PCB is the use of metal cores in the process of engineering. This could change and become rigid carriers, which offer mechanical stiffness, thereby ensuring that it can be easily used between solids and fluids as the wear resistance and roughness are great, therefore you can use it in different industrial positions.
Ideal Time to Use the Ceramic PCB Substrate
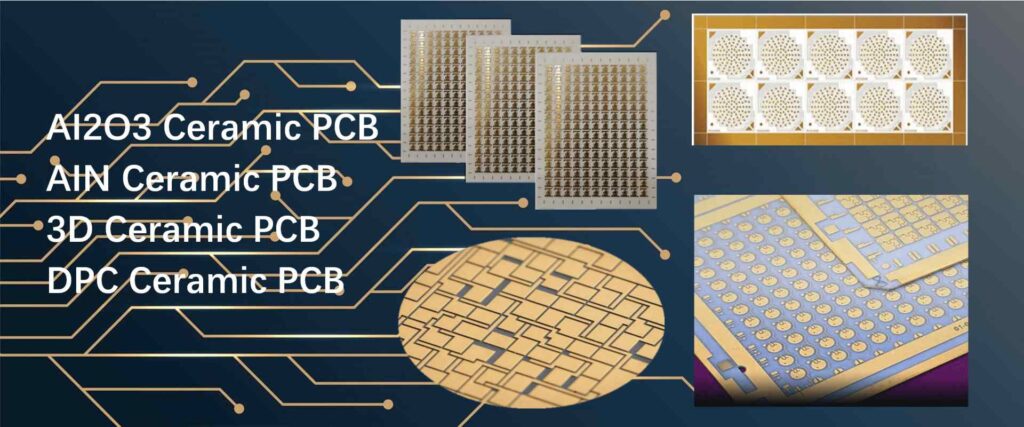
The ceramic PCB may be utilized in many different applications. However, they aren’t the best answer or solution for every case. Considering all factors, they might be inappropriate in some cases.
Understanding the factors determining if the ceramic PCB is appropriate for your applications or projects is essential. There are factors to look into when deciding if you should make use of ceramic PCBs include the thermal conductivity, weight, and cost.
Also, they are corrosion-resistant and come with low thermal expansion. In addition, they could be produced with high aspect ratios as well as extremely thin layers. Therefore, they are lighter, with better thermal conductivity. Thus makes them great for applications where heat transfer, weight, and size are important.
Whenever multilayer boards are needed, its high thermal conductivity would become very significant. The surface and inner layer(s) of the circuit would be spared from the hot spots. This is why they are great for applications whereby high temperatures will be a concern. These include aerospace or automotive.
Working with ceramic PCBs improves the reliability of your machinery greatly. This holds especially for those utilized inside the heavy equipment as well as military sectors.
Generally, ceramic PCBs are more expensive compared to the traditional ones. Considering cost, it gives the user great benefits which make them a great choice for specific applications.
Conclusion
The ceramic PCB substrate is known to deliver high pressure, high temperature, high insulation and high frequency performance. Its great analysis, simulation, design, and features are available. This allows us to assist the designer to design the printed circuit boards from all materials like ceramics.
Leave a Reply