Of recent years, there has been a lot of advancement in the PCB industry. One of the best developments in this industry is the use of ceramics in producing electronic boards. Ceramics is a material well known for its superior quality and exceptional performance. Due to these attributes, many circuit board producers have opted for this choice of material.
In ceramic boards, polyimide is often used as the solder paste while the base material is made of ceramics. This circuit board has replaced many conventional circuit boards whose base is FR-4 glass epoxy. Although the ceramics PCB market seems to be in its infancy stage, there has been some rapid growth. These boards are a cost effective option for a wide range of electronic projects. Compared to the traditional FR4 boards, ceramic circuit boards have better thermal conductivity, higher thermal shock withstand, exceptional chemical resistance, and great electrical insulation. Also, these boards stand out among other PCB types.
They have proved their usefulness in military and aerospace devices. Even in consumer electronics, these boards are performing well. This article takes an in-depth look into ceramic circuit boards and how they have impacted the electronics industry.
What is a Ceramic PCB?
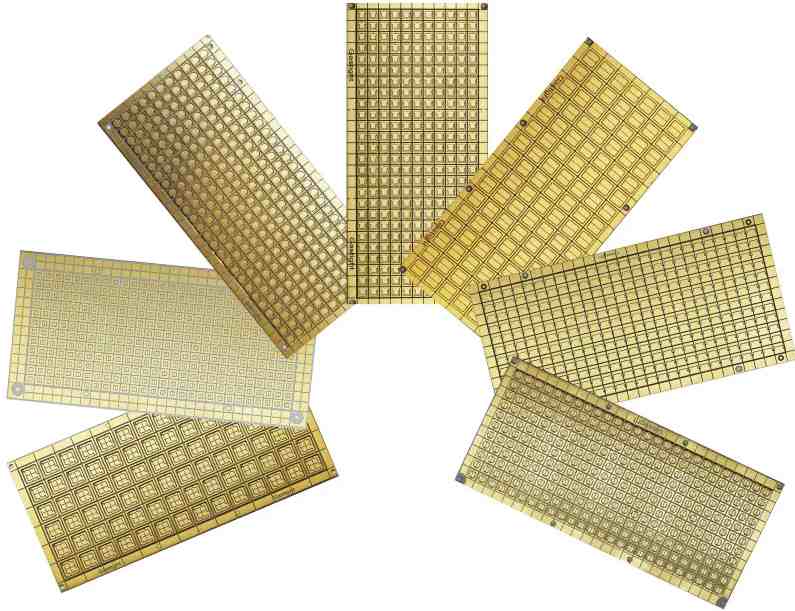
This is a type of printed circuit board whose base material is made up of ceramics. The conductive pathway of these boards is printed on ceramic base. Ceramics have good thermal, mechanical, and dielectric characteristics. Ceramics used for these boards are completely different from those used in floors. This ceramic comprises various chemical substances for certain uses.
A ceramic circuit board has metal cores with a thin insulating layer of ceramic to establish circuitry. The ceramics used in this board can be beryllium oxide, aluminum nitride or alumina. However, the most popular ceramic material used is alumina, although all of these materials have good heat conduction capabilities.
Ceramic boards are very ideal for high power density applications like the automotive and aerospace industries. Also, these boards comprise inorganic materials which play a significant role in their longevity and durability. As a reliable material, ceramics offer good insulating properties which offers protection to components.
The heat conductivity of ceramic boards contributes to their wide use in hybrid microelectronics, power electronics, and multi-chip modules. Also, ceramic boards can handle high frequency due to their low CTE and dimensional stability. In as much as the manufacturing costs of these boards are higher than traditional boards, their advantages make them a good investment for applications where long term reliability and durability is crucial.
Types of Ceramic PCB Materials
There are different types of ceramic materials used for ceramic circuit boards. The aluminum nitride (AIN) and alumina are the two major types. These materials offer more advanced thermal performance since they require no electric layer between the circuits and the core. Let discuss more details about these two ceramic board types.
Alumina
The alumina circuit board is a more popular option since it is less expensive than aluminum nitride. It is wholly made of aluminum oxide and features thermal conductivity within the range of 18 to 36 W/mK. One of the reasons why alumina is popularly used is its availability. Alumina is an abundant raw material with low cost. It is a recommended material for PCBs used in automobile sensor circuits, engines, and even shock absorbers.
Aluminum nitride
Also popularly known as AIN, this ceramic material has a thermal conductivity more than 150 W/mK. Asides from this, it offers other properties like good dielectric constant, low CTE, and more. Aluminum nitride is a more costly option compared to alumina. Many PCB manufacturers opt for the latter due to its cost effectiveness.
Aluminum nitride ceramic board has a CTE that matches with that of silicon semiconductor chips. There is a great binding between the chip and circuit due to this. AIN is a safe option for automobiles since it can tolerate vibration, shock, and even high temperatures.
Beryllium Oxide
Although the two most popular ceramic materials are aluminum nitride and aluminum, beryllium oxide is also a good material. This less popular option has a very high thermal conductivity which is almost ten times that of alumina. Beryllium oxide functions well in circuit boards that are exposed to high temperatures. Also, it is great for producing boards that are used in space sectors.
Benefits of Ceramic Circuit Boards
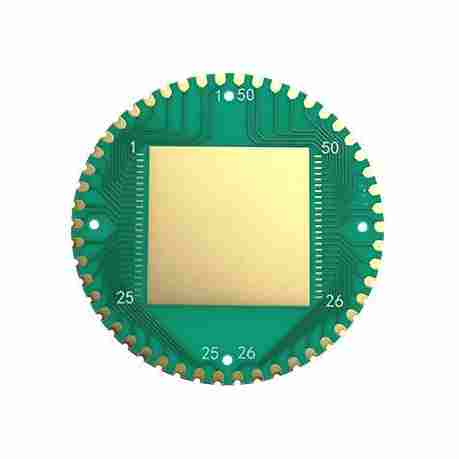
The benefits of ceramic PCBs are numerous in such a way that they surpass their drawbacks. Over time, ceramic boards become more popular due to the wide range of benefits electronic device producers gain from them. These boards have high-temperature resistance and electrical insulation that prevent electrical devices from damaging. Ceramic boards are considered a good option in applications that require:
High pressure
One of the best things about Ceramic boards is their adaptability. These boards can tolerate the highest pressure while still maintaining good quality. Therefore, it is a go-to-option got heavy-duty applications. Regardless of amount of pressure you subject a ceramic board to, it still delivers good results.
High insulation
Due to its high electrical insulation properties, heat will less likely get to this substrate. The components in this board will hardly get damaged since heat can’t pass through them easily.
High Voltage & Signal Integrity
Ceramic circuit boards function well in applications where signal integrity and high voltage is of great concern. These boards are capable of handling extremely high voltages without any form of leakage. As a result of this, they have been found useful in electric vehicles, power electronics, and some applications. Ceramics possess great signal propagation and low dielectric loss which help in minimizing signal distortion and maintaining signal integrity.
High temperature
Ceramic board can survive any temperature. This board remains functional even in very extreme and harsh weather. Their performance isn’t hindered by changes in temperature. Due to this, manufacturers see them as a more reliable option for different sectors.
Reliability and Durability
Ceramic boards have moisture resistance, high mechanical strength, and great thermal conductivity which contribute to their durability and reliability. Also, they can offer long-lasting performance in demanding applications.
Properties of Ceramic PCB
The properties of ceramic circuit boards make them stand out among other circuit boards.
Excellent thermal conductivity
Ceramic boards have good thermal conductivity which makes them discharge heat at a faster rate. Electronic components usually generate heat and there is a great need to dissipate this heat. Otherwise, this could lead to component failure. Ceramics have the capability to manage thermal heat. This property is beneficial for applications that require thermal management. Also, proper thermal management helps to avoid overheating and enable maximum performance.
Low CTE
In a ceramic PCB, the coefficient of thermal expansion is very low. This means the board can tolerate high temperatures without expanding in size. The solid and interatomic bonds in ceramic PCBs contribute to its thermal stability. Regardless of the temperature, ceramic circuit boards function well and remain sturdy.
Great thermal insulation
Ceramic boards offer thermal insulation which helps to prevent heat from flowing via the substrate. This property protects the components on the circuit board from damaging. Excessive heat can cause damages to components on a circuit board. This is why it is advisable to use materials that provide thermal insulation.
Low moisture absorption
Another property of ceramic boards is their low rate of absorbing moisture. These boards can function well in humid areas. Low moisture absorption is a property electronic manufacturers look out for in circuit boards.
Types of Ceramic Circuit Boards
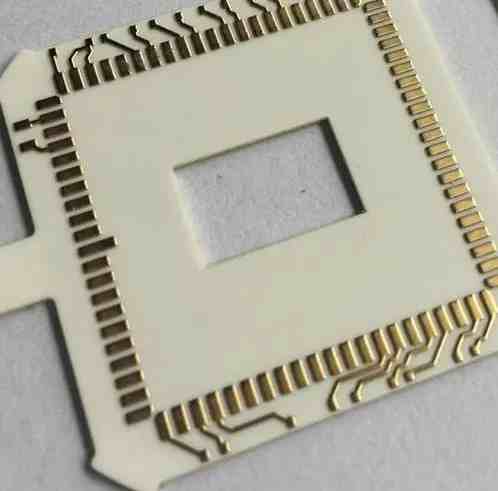
Based on the manufacturing process, we classify ceramic circuit boards into different types. These are:
Low-temperature co-fired ceramic board
This type of board comprises a glass material and an adhesive substrate. The glass material makes up about 50% of this board. Manufacturers laminate low-temperature co-fired ceramic boards and place them in an oven that is about 900oC. One of the advantages of this ceramic board is its shrink resistance and minimized warpage. As a result of these properties, they have improved thermal conductivity and mechanical strength. These boards are suitable for applications where heat dissipation is a major concern.
High-temperature co-fired ceramic board
High-temperature co-fired ceramic boards are made of ceramics combined with adhesives, aluminum oxide, and solvents. These boards can withstand high-temperature and as well maintain structural integrity. Even under extreme temperature, these boards ensure good electrical performance.
High-temperature co-fired ceramic (HTCC) boards are great for use in the production of automotive, power, and aerospace electronics. The manufacturing process employed here enables durability and contributes to their capability to tolerate harsh environments. Electronics manufacturers prefer HTCC boards for demanding applications.
Thick film ceramic board
The conductor layer of thick film ceramic boards features thickness beyond 10 microns, but not above 13 microns. Also, the surface of these boards has a conductor layer in which precious metals are imprinted. For a thick film ceramic board, it is necessary to use dielectric and gold pastes on the base material. After this, the board goes through a baking procedure at below 1000oC. The use of thick film ceramic board has become so popular among circuit board manufacturers.
This ceramic board has better advantage over traditional boards due to their properties. Therefore, manufacturers find them as a much better alternative for use compared to traditional boards.
Disadvantages of Ceramic Boards
Ceramic boards have their limitations despite their numerous benefits. Although, their benefits outweigh their disadvantages, they are not a considerate choice for some applications. It is crucial to know what these disadvantages are:
Higher cost
The production process of ceramic boards is more demanding and complex than that of tradition boards like FR4. Due to the complexity of involved in their manufacturing, it requires more cost. The cost of the ceramic materials also contributes to the high cost of these boards.
Manufacturing complexity
Thick-film ceramic boards and high-temperature co-fire ceramic boards require a specialized production process which contributes to their complexity. In the long run, this will increase manufacturing cost. Also, skilled technicians handle the manufacturing of these boards. The cost of hiring skilled workers and the specialized facilities used all contribute to their costs.
Applications of Ceramic Circuit Board
Ceramic circuit boards are useful in applications exposed to high pressure and high temperature. The ability of these boards to withstand corrosion and vibration is an important factor to consider in critical applications. A wide range of applications rely on these boards.
Automotive
Ceramic boards are used in producing automotive parts and components. You will find them in engines, brake systems, and more. Their ability to withstand heat contributes to their wide usage in the automotive industry.
Consumer electronics
A lot of consumer electronics feature ceramic boards. These boards function well and deliver good results in consumer electronics.
Aerospace
High critical applications like the aerospace sector make use of ceramic boards. This is because of the unique properties and benefits of ceramic PCBs. Devices used in aerospace sectors are sometimes exposed to harsh weather conditions. Also, vibration and shocks are some of the conditions these devices are subjected to. Therefore, it is crucial to use circuit boards that can withstand all these conditions.
Defense
In the defense industry, ceramic boards have gained wide popularity. This is a result of their distinguishing characteristics. A wide range of military devices are often used in varying temperatures. One of the benefits of ceramic boards is thermal management abilities. These boards can survive rigorous use in varying temperatures.
Telecommunication
Telecommunication devices require high-frequency boards. Ceramic boards are a popular option for applications that require electrical signal transmission and high-frequency data. Also, these boards are a cost efficient option unlike other PCBs.
Conclusion
Ceramic PCBs might not be the best option in some applications, but they are widely used in several applications. With all the properties they offer, they are appropriate for most applications. These boards possess better thermal conductivity, low thermal expansion, and improved thermal resistance. Also, they are resistance to corrosion, vibration, and shocks.
Their ability to transfer heat at a much faster rate contributes to their popular use in the electronics industry. Although ceramic boards may be a more expensive alternative compared to FR4 boards, they offer better benefits.
Leave a Reply