Introduction to cEDM
cEDM, which stands for Electronics Design & Manufacturing, refers to the end-to-end process of designing and producing electronic products and components. This encompasses everything from the initial product concept and schematic design, to sourcing components, fabricating printed circuit boards (PCBs), assembling and testing the final product.
The cEDM process has evolved significantly in recent decades, driven by advances in computer-aided design (CAD) software, manufacturing automation, and the globalization of electronics supply chains. Today, most electronics are designed digitally using Electronic Design Automation (EDA) tools and manufactured in large volumes by specialized factories, many of which are located in Asia.
Key Stages of the cEDM Process
The cEDM process can be broken down into several key stages:
1. Product Concept and Requirements Definition
The first step is to define the product concept and requirements. This involves understanding the target market, desired features and functionality, cost and performance targets, and any regulatory or certification requirements the product must meet. The output of this stage is typically a product requirements document (PRD) that guides the subsequent design and development.
2. Schematic Design
The next step is to create the schematic design, which is a diagram showing how the electronic components are connected together. This is done using EDA software such as Altium Designer, OrCAD, or KiCad. The schematic captures the logical connections between components but does not specify their physical layout.
Key considerations during schematic design include:
- Selecting the right components to meet the product requirements
- Ensuring proper power supply and signal integrity
- Minimizing electromagnetic interference (EMI)
- Allowing for testability and debuggability
3. PCB Layout and Routing
Once the schematic is complete, the next step is to create the physical layout of the PCB. This involves placing the components on the board and routing the copper traces to connect them according to the schematic.
Modern PCBs often have multiple layers, with components mounted on both sides of the board. Proper layout and routing is critical to ensure signal integrity, power delivery, and manufacturability. Specialized PCB layout software is used for this task.
4. Bill of Materials (BOM) and Sourcing
In parallel with PCB design, the Bill of Materials (BOM) is created listing all the components needed to build the product. The BOM typically includes the manufacturer part number, description, quantity, and cost for each component.
Sourcing the components often involves working with distributors to find parts that meet the specifications and are available in the quantities needed. For custom parts like the PCB and enclosure, quotes are obtained from manufacturers.
5. Prototyping and Testing
Before committing to full-scale production, prototypes are built and tested to verify the design. This may involve multiple iterations to debug issues and optimize performance.
Various types of testing are performed, including:
- Power-on and functional testing
- Signal integrity analysis
- Thermal testing
- EMI/EMC testing
- Reliability and stress testing
- Compliance testing to relevant standards
6. Manufacturing and Assembly
Once the design is finalized and tested, it moves into manufacturing. For PCBs, the usual process is:
-
Fabrication – the bare PCBs are manufactured based on the Gerber files generated from the PCB layout software.
-
SMT Assembly – surface mount components are placed and soldered onto the PCB using automated pick-and-place machines and reflow ovens.
-
THT Assembly – through-hole components are inserted and soldered, often by hand.
-
Inspection and Test – the assembLED PCBs are inspected visually and tested electrically to catch any defects.
Other parts like the enclosure, cabling, packaging, etc. are also manufactured and the final product is assembled, configured, and tested.
7. Certification and Compliance
Depending on the type of product and the target markets, various certifications may be required before the product can be sold. Common examples include:
- FCC certification for electromagnetic compatibility (EMC)
- UL or CE safety certifications
- RoHS certification for restriction of hazardous substances
- Wireless certifications for products with radio functions
Obtaining these certifications involves submitting samples for 3rd party lab testing and providing detailed documentation.
8. Sustaining and End-of-Life
Once in production, the focus shifts to sustaining engineering – managing the product through its lifecycle. This includes handling field failures and returns, implementing cost reductions, and eventually planning for the product’s end-of-life.
Key Considerations in cEDM
Supply Chain Management
Electronics manufacturing is heavily globalized, with a complex network of suppliers and sub-contractors spanning many countries. Effective supply chain management is critical to ensure continuity of supply, quality, and cost control.
Key aspects of supply chain management in cEDM include:
- Strategic sourcing to select and qualify suppliers
- Negotiating pricing and terms
- Forecasting and inventory management
- Logistics and transportation
- Managing supplier quality and performance
Many companies use specialized Supply Chain Management (SCM) software to manage these processes.
Design for Manufacturing (DFM)
Design for Manufacturing (DFM) is the practice of designing products in a way that optimizes their manufacturability. This involves considering the capabilities and limitations of the manufacturing processes during the design stage itself.
Some key DFM considerations in electronics include:
- Selecting components that are readily available and easy to assemble
- Providing adequate spacing and symmetry for automated assembly
- Optimizing the PCB layout for ease of fabrication and test
- Minimizing the number of unique parts and using standard packaging
- Designing the enclosure for ease of assembly and disassembly
Effective DFM can significantly reduce manufacturing cost and improve product quality and reliability.
Test and Quality Strategy
Testing and quality assurance are critical in electronics manufacturing to catch defects and ensure the product meets its specifications. A comprehensive test and quality strategy typically involves:
- Incoming quality control (IQC) to inspect and test components before assembly
- In-circuit testing (ICT) to verify the assembled PCB
- Functional testing of the complete product
- Burn-in and stress testing to weed out early failures
- Statistical process control (SPC) to monitor process parameters
- Outgoing quality assurance (OQA) to verify product quality before shipment
The goal is to catch defects as early in the process as possible, as the cost of fixing a defect increases tenfold at each stage.
Regulatory Compliance
Electronic products are subject to a host of regulations around safety, electromagnetic compatibility (EMC), hazardous substances, and environmental impact. Key regulations include:
Regulation | Scope |
---|---|
FCC Part 15 | Regulates EMC for electronic products sold in the US |
CE Marking | Safety, health, and environmental protection standards for products sold in the EU |
RoHS | Restricts the use of certain hazardous substances in electronics |
WEEE | Mandates collection and recycling of waste electrical and electronic equipment |
Compliance with these regulations is mandatory to sell the product in the respective markets. Non-compliance can result in hefty fines and product recalls.
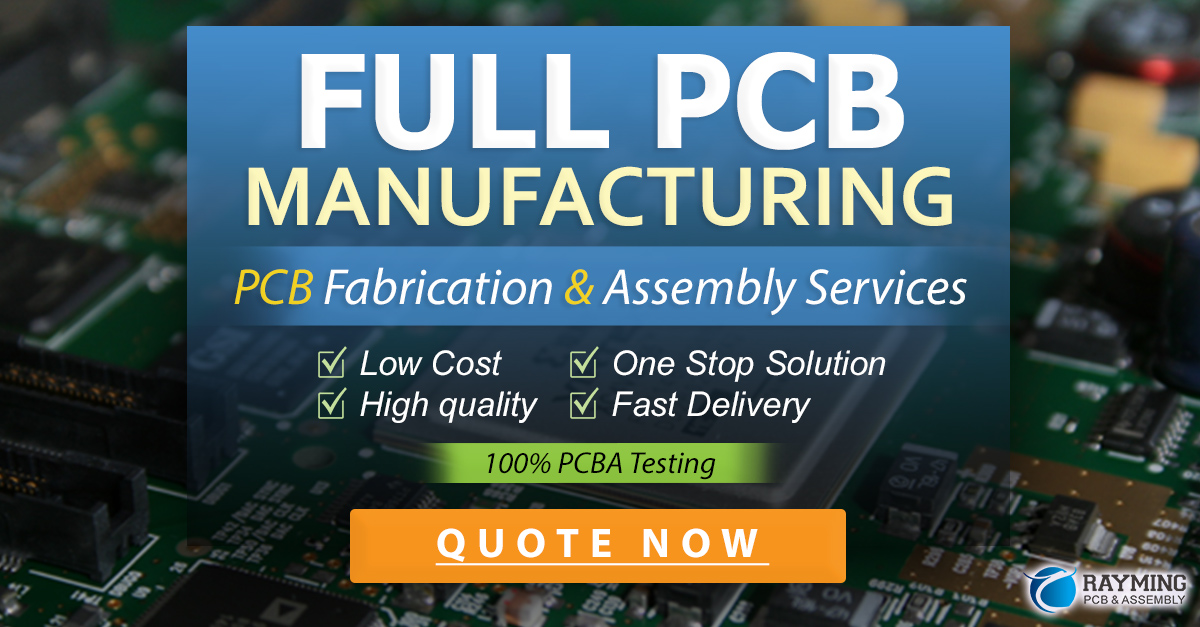
The Future of cEDM
The cEDM landscape is continually evolving, driven by technological advancements and changing market demands. Some key trends shaping the future of cEDM include:
Digitalization and Industry 4.0
The increasing digitalization of manufacturing, often referred to as Industry 4.0, is transforming cEDM. This involves the use of cyber-physical systems, Internet of Things (IoT), cloud computing, and artificial intelligence (AI) to create “smart factories”.
Benefits of Industry 4.0 in cEDM include:
- Increased automation and efficiency
- Real-time monitoring and control of processes
- Predictive maintenance to reduce downtime
- Improved traceability and quality control
- Faster response to changes in demand
Miniaturization and Advanced Packaging
The trend towards miniaturization continues unabated in electronics, driven by the demand for smaller, lighter, and more portable devices. This is enabled by advances in semiconductor technology, allowing more functions to be integrated into a single chip.
Advanced packaging technologies are also playing a key role, allowing multiple chips to be integrated in a single package. Examples include:
Packaging Technology | Description |
---|---|
System-in-Package (SiP) | Multiple chips integrated in a single package |
Package-on-Package (PoP) | Stacking of packaged chips |
3D Integrated Circuits | Vertical stacking of chip layers |
These technologies allow for higher density and performance, but also pose new challenges for manufacturing and testing.
Sustainable Electronics
There is growing awareness and demand for sustainable electronics – products that are designed and manufactured in an environmentally responsible way. This involves considerations such as:
- Design for reuse and recycling
- Use of renewable and biodegradable materials
- Reduction of energy and water use in manufacturing
- Responsible sourcing of raw materials
- Reduction of waste and emissions
Many companies are now incorporating sustainability goals into their cEDM strategies, not just for compliance but also for competitive advantage.
FAQ
What is cEDM?
cEDM stands for Electronics Design & Manufacturing. It refers to the end-to-end process of designing and producing electronic products and components, from the initial product concept to the final manufactured product.
What are the key stages in the cEDM process?
The key stages in the cEDM process are:
- Product Concept and Requirements Definition
- Schematic Design
- PCB Layout and Routing
- Bill of Materials (BOM) and Sourcing
- Prototyping and Testing
- Manufacturing and Assembly
- Certification and Compliance
- Sustaining and End-of-Life
What is DFM and why is it important?
DFM stands for Design for Manufacturing. It is the practice of designing products in a way that optimizes their manufacturability, by considering the capabilities and limitations of the manufacturing processes during the design stage. Effective DFM can significantly reduce manufacturing cost and improve product quality and reliability.
What are some key regulations that electronic products must comply with?
Some key regulations for electronic products include:
- FCC Part 15 for electromagnetic compatibility in the US
- CE Marking for safety, health, and environmental protection in the EU
- RoHS for restriction of hazardous substances
- WEEE for waste electrical and electronic equipment
Compliance with these regulations is mandatory to sell the product in the respective markets.
What are some key trends shaping the future of cEDM?
Some key trends shaping the future of cEDM include:
- Digitalization and Industry 4.0, using technologies like IoT, AI, and cloud computing to create “smart factories”
- Miniaturization and advanced packaging, allowing for higher density and performance
- Sustainable electronics, with a focus on environmentally responsible design and manufacturing
Companies are adapting to these trends to stay competitive in the rapidly evolving cEDM landscape.
Leave a Reply