What is PCB Corrosion?
PCB corrosion is the gradual degradation of the metal surfaces on a printed circuit board due to chemical reactions with the environment. This process can affect the copper traces, solder joints, and other metal components on the PCB. Corrosion can lead to the formation of nonconductive substances, such as oxides and sulfides, which can impede electrical conductivity and cause various issues in the functioning of the electronic device.
Causes of PCB Corrosion
Several factors can contribute to the corrosion of PCBs. Understanding these causes is crucial for implementing effective prevention measures.
Environmental Factors
Humidity and Moisture
One of the primary causes of PCB corrosion is exposure to humidity and moisture. When PCBs are exposed to high levels of humidity, the moisture can condense on the surface of the board, creating an electrolytic solution that facilitates corrosion. This is particularly problematic in environments with fluctuating temperatures, as the repeated condensation and evaporation cycles can accelerate the corrosion process.
Atmospheric Pollutants
Atmospheric pollutants, such as sulfur dioxide, nitrogen oxides, and chlorine, can contribute to PCB corrosion. These pollutants can react with moisture on the PCB surface to form corrosive compounds, such as sulfuric acid or hydrochloric acid. Industrial environments and areas with high levels of air pollution are more susceptible to this type of corrosion.
Temperature Fluctuations
Temperature fluctuations can also play a role in PCB corrosion. Rapid changes in temperature can cause condensation on the PCB surface, leading to moisture-related corrosion. Additionally, high temperatures can accelerate chemical reactions and increase the rate of corrosion.
Material Factors
Dissimilar Metals
When dissimilar metals are in contact on a PCB, galvanic corrosion can occur. Galvanic corrosion happens when two different metals with varying electrode potentials are electrically connected in the presence of an electrolyte (such as moisture). In this scenario, the more active metal (anode) will corrode, while the less active metal (cathode) remains protected. Common examples of dissimilar metal pairs on PCBs include copper-tin, copper-silver, and copper-gold.
Flux Residues
Flux is a chemical cleaning agent used during the soldering process to remove oxides and promote the formation of a strong solder joint. However, if the flux residues are not properly cleaned after soldering, they can absorb moisture and become corrosive. Acidic flux residues are particularly harmful and can lead to rapid corrosion of the metal surfaces on the PCB.
Solder Mask Defects
Solder mask is a protective coating applied to the PCB to insulate the copper traces and prevent short circuits. However, defects in the solder mask, such as pinholes, cracks, or incomplete coverage, can expose the underlying metal to the environment, making it vulnerable to corrosion.
Design Factors
Inadequate Spacing and Clearance
Proper spacing and clearance between components and traces on a PCB are essential for preventing corrosion. If the components are placed too close together or the traces are too narrow, it can lead to increased moisture retention and difficulty in cleaning, which can promote corrosion.
Poor Ventilation
Inadequate ventilation can contribute to PCB corrosion by allowing the accumulation of moisture and corrosive gases. If the electronic device or enclosure does not have proper ventilation, the trapped moisture and pollutants can create a corrosive environment that accelerates the degradation of the PCB.
Preventing PCB Corrosion
To mitigate the risk of PCB corrosion and ensure the long-term reliability of electronic devices, several preventive measures can be implemented.
Design Considerations
Material Selection
Choosing the right materials for PCB Construction is crucial for minimizing corrosion risk. Consider using corrosion-resistant materials, such as gold plating for connectors and high-quality solder masks with good adhesion and coverage. When selecting dissimilar metals, refer to the galvanic series to choose combinations with minimal potential difference to reduce galvanic corrosion.
Spacing and Clearance
Ensure adequate spacing and clearance between components and traces on the PCB. Follow the recommended design guidelines for minimum spacing and trace widths to facilitate proper cleaning and reduce moisture retention. Use design for manufacturability (DFM) principles to optimize the layout for corrosion prevention.
Ventilation
Incorporate proper ventilation in the electronic device or enclosure to prevent the accumulation of moisture and corrosive gases. Use vents, fans, or other methods to promote air circulation and minimize the risk of corrosion.
Manufacturing Processes
Cleaning
Thorough cleaning of the PCB after soldering is essential to remove flux residues and other contaminants that can promote corrosion. Use appropriate cleaning agents and methods, such as aqueous cleaning or solvent cleaning, depending on the type of flux and the PCB materials. Ensure complete removal of cleaning agents and dry the PCB thoroughly before further assembly or packaging.
Conformal Coating
Applying a conformal coating to the PCB can provide an additional layer of protection against corrosion. Conformal coatings, such as acrylic, silicone, or urethane, form a thin protective film over the PCB surface, shielding it from moisture, dust, and other contaminants. Choose a conformal coating that is compatible with the PCB materials and the operating environment.
Storage and Packaging
Proper storage and packaging of PCBs can help prevent corrosion during transportation and storage. Use moisture-barrier bags or desiccant packs to control humidity levels and minimize moisture exposure. Store PCBs in a cool, dry place away from direct sunlight and sources of contamination.
Environmental Control
Humidity Control
Maintaining appropriate humidity levels in the operating environment can significantly reduce the risk of PCB corrosion. Use dehumidifiers, air conditioners, or humidity control systems to keep the relative humidity within the recommended range for electronic devices, typically below 60%.
Pollution Control
In industrial environments or areas with high levels of atmospheric pollutants, implementing pollution control measures can help mitigate the risk of PCB corrosion. Use air filtration systems, fume extractors, or positive air pressure to minimize the exposure of PCBs to corrosive gases and particles.
Temperature Control
Controlling the temperature of the operating environment can help prevent condensation and reduce the rate of corrosion. Maintain a stable temperature within the recommended range for electronic devices and avoid rapid temperature fluctuations.
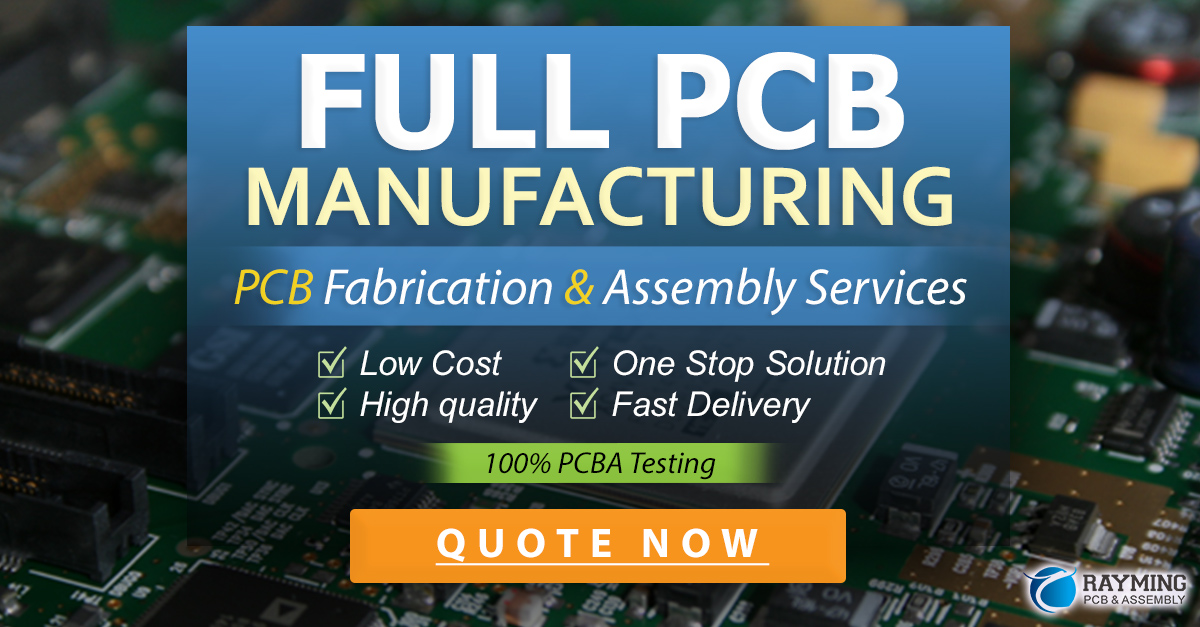
FAQ
What are the signs of PCB corrosion?
Signs of PCB corrosion include:
– Discoloration or tarnishing of metal surfaces
– Presence of green or white crystalline growths on the PCB
– Flaking or peeling of solder mask
– Increased resistance or open circuits in electrical connections
– Intermittent or complete failure of the electronic device
Can PCB corrosion be repaired?
In some cases, minor PCB corrosion can be repaired by cleaning the affected area and applying a protective coating. However, if the corrosion has caused significant damage to the metal surfaces or the PCB substrate, repair may not be feasible, and replacement of the PCB may be necessary.
How often should PCBs be inspected for corrosion?
The frequency of PCB corrosion inspections depends on the operating environment and the criticality of the electronic device. In general, it is recommended to perform visual inspections at regular intervals, such as every 6 months to a year, or more frequently in harsh environments. Automated inspection methods, such as automated optical inspection (AOI) or X-ray inspection, can also be used for more detailed analysis.
Can conformal coating completely prevent PCB corrosion?
Conformal coating provides an additional layer of protection against corrosion, but it is not a complete solution. While conformal coating can significantly reduce the risk of corrosion by shielding the PCB from moisture and contaminants, it is not impenetrable. Proper design, manufacturing processes, and environmental control measures should still be implemented in conjunction with conformal coating for optimal corrosion prevention.
What are the most common types of PCB corrosion?
The most common types of PCB corrosion include:
– Galvanic corrosion: Occurs when dissimilar metals are in contact in the presence of an electrolyte
– Atmospheric corrosion: Caused by exposure to humidity, moisture, and atmospheric pollutants
– Flux residue corrosion: Results from improper cleaning of flux residues after soldering
– Electrolytic corrosion: Happens when an electrical current flows through an electrolyte, causing metal dissolution
Type of Corrosion | Causes | Prevention |
---|---|---|
Galvanic corrosion | Dissimilar metals in contact | Material selection, spacing, and clearance |
Atmospheric corrosion | Humidity, moisture, and pollutants | Environmental control, conformal coating |
Flux residue corrosion | Improper cleaning of flux residues | Thorough cleaning, compatible cleaning agents |
Electrolytic corrosion | Electrical current and electrolyte | Proper insulation, conformal coating |
By understanding the causes of PCB corrosion and implementing appropriate prevention measures, designers and manufacturers can significantly improve the reliability and longevity of electronic devices. Proper material selection, design considerations, manufacturing processes, and environmental control are key elements in combating PCB corrosion and ensuring the optimal performance of printed circuit boards.
Leave a Reply