What is a Wire Harness?
A wire harness, also known as a cable harness or wiring assembly, is a collection of wires, cables, and connectors that are bundled together to transmit signals or electrical power. Wire harnesses are used in various industries, including automotive, aerospace, telecommunications, and consumer electronics. They simplify the installation process, reduce the risk of wiring errors, and improve the overall efficiency of electrical systems.
Components of a Wire Harness
A typical wire harness consists of several components:
- Wires: The main component of a wire harness, wires are used to transmit electrical signals or power.
- Connectors: Connectors are used to join wires to other components or to other wire harnesses.
- Terminals: Terminals are used to provide a connection point for wires and connectors.
- Insulation: Insulation is used to protect wires from damage and to prevent short circuits.
- Shielding: Shielding is used to protect wires from electromagnetic interference (EMI) and radio frequency interference (RFI).
Types of Wire Harnesses
There are several types of wire harnesses, each designed for specific applications:
Type | Description | Applications |
---|---|---|
Automotive | Used in vehicles to connect electrical components | Engine, dashboard, lighting, audio systems |
Aerospace | Used in aircraft and spacecraft to connect electrical components | Avionics, control systems, in-flight entertainment |
Telecommunications | Used in telecommunications equipment to connect components | Routers, switches, servers |
Consumer Electronics | Used in consumer devices to connect components | Smartphones, computers, televisions |
Wire Harness Assembly Process
The wire harness assembly process typically involves the following steps:
1. Design
The first step in the wire harness assembly process is to design the harness. This involves creating a schematic diagram that shows the layout of the wires, connectors, and other components. The design must take into account factors such as the intended application, the environment in which the harness will be used, and any relevant industry standards.
2. Material Selection
Once the design is complete, the next step is to select the appropriate materials for the wire harness. This includes choosing the right type and gauge of wire, as well as the appropriate connectors and terminals. The materials must be able to withstand the intended application and environment.
3. Cutting and Stripping
After the materials have been selected, the next step is to cut the wires to the appropriate lengths and strip the insulation from the ends. This is typically done using specialized cutting and stripping machines.
4. Crimping and Soldering
Once the wires have been cut and stripped, the next step is to attach the connectors and terminals. This is typically done using crimping or soldering techniques. Crimping involves using a specialized tool to compress the connector or terminal onto the wire, while soldering involves using heat to melt a metal alloy onto the wire and connector.
5. Routing and Bundling
After the connectors and terminals have been attached, the next step is to route and bundle the wires. This involves arranging the wires in a specific pattern and securing them together using cable ties, tape, or other fastening methods. The routing and bundling process must take into account factors such as the intended application, the environment in which the harness will be used, and any relevant industry standards.
6. Testing and Inspection
Once the wire harness has been assembled, the next step is to test and inspect it to ensure that it meets the required specifications. This typically involves using specialized testing equipment to verify the continuity and insulation resistance of the wires, as well as visual inspection to check for any defects or damage.
7. Packaging and Shipping
After the wire harness has been tested and inspected, the final step is to package and ship it to the customer. The packaging must be designed to protect the harness during transportation and storage, and must include any necessary documentation or labeling.
Benefits of Using Wire Harnesses
Using wire harnesses offers several benefits over traditional point-to-point wiring methods:
- Simplified Installation: Wire harnesses are pre-assembled and tested, which simplifies the installation process and reduces the risk of wiring errors.
- Improved Reliability: Wire harnesses are designed to withstand the intended application and environment, which improves the overall reliability of the electrical system.
- Reduced Maintenance: Wire harnesses are easier to maintain and troubleshoot than traditional point-to-point wiring, which reduces downtime and maintenance costs.
- Space Savings: Wire harnesses are bundled together, which saves space compared to individual wires and cables.
- Cost Savings: Wire harnesses are typically less expensive than point-to-point wiring methods, due to reduced installation and maintenance costs.
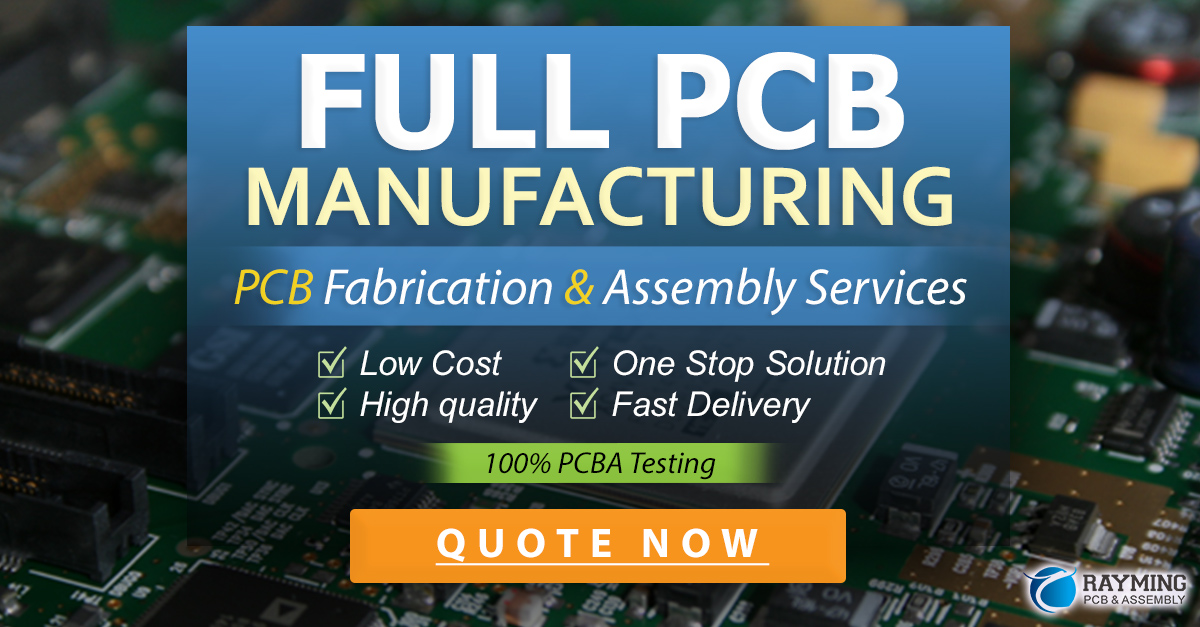
Applications of Wire Harnesses
Wire harnesses are used in a wide range of applications across various industries:
Automotive Industry
In the automotive industry, wire harnesses are used to connect various electrical components, such as the engine control unit, sensors, and actuators. They are also used to connect the dashboard, lighting, and audio systems. Automotive wire harnesses must be designed to withstand extreme temperatures, vibration, and exposure to chemicals.
Aerospace Industry
In the aerospace industry, wire harnesses are used to connect avionics, control systems, and in-flight entertainment systems. Aerospace wire harnesses must be designed to withstand extreme temperatures, pressure changes, and vibration, and must meet strict safety and reliability standards.
Telecommunications Industry
In the telecommunications industry, wire harnesses are used to connect routers, switches, and servers. Telecommunications wire harnesses must be designed to handle high data rates and to withstand the heat generated by the equipment.
Consumer Electronics Industry
In the consumer electronics industry, wire harnesses are used to connect components in devices such as smartphones, computers, and televisions. Consumer electronics wire harnesses must be designed to fit within tight spaces and to withstand daily use and handling.
Future Trends in Wire Harness Assembly
The wire harness assembly industry is constantly evolving to meet the changing needs of customers and to take advantage of new technologies. Some of the future trends in wire harness assembly include:
- Miniaturization: As devices become smaller and more compact, wire harnesses must also become smaller and more flexible.
- Increased Automation: Automated assembly methods, such as robotics and machine vision, are becoming more common in wire harness assembly to improve efficiency and reduce costs.
- Wireless Technology: Wireless technology is being incorporated into wire harnesses to enable remote monitoring and control of electrical systems.
- Sustainable Materials: There is a growing demand for wire harnesses made from sustainable materials, such as biodegradable plastics and recycled metals.
Frequently Asked Questions (FAQ)
1. What is the difference between a wire harness and a cable assembly?
A wire harness is a collection of wires, cables, and connectors that are bundled together to transmit signals or electrical power. A cable assembly, on the other hand, is a single cable or group of cables that are terminated with connectors on one or both ends. Cable assemblies are typically used for simpler applications, while wire harnesses are used for more complex applications that require multiple wires and connectors.
2. How are wire harnesses typically manufactured?
Wire harnesses are typically manufactured using a combination of manual and automated processes. The wires are cut to the appropriate lengths, stripped, and terminated with connectors or terminals using crimping or soldering techniques. The wires are then bundled together and secured using cable ties, tape, or other fastening methods. Finally, the completed harness is tested and inspected to ensure that it meets the required specifications.
3. What are some common materials used in wire harness assembly?
Common materials used in wire harness assembly include copper wire, PVC insulation, nylon connectors, and heat-shrink tubing. The specific materials used will depend on the intended application and environment, as well as any relevant industry standards.
4. How can I ensure the reliability of my wire harness?
To ensure the reliability of your wire harness, it is important to follow best practices for design, material selection, and manufacturing. This includes using high-quality materials, adhering to industry standards and regulations, and performing thorough testing and inspection. It is also important to work with a reputable wire harness manufacturer that has experience in your specific industry and application.
5. What are some common challenges in wire harness assembly?
Some common challenges in wire harness assembly include managing complex designs, ensuring consistent quality, and meeting tight deadlines. Other challenges may include sourcing materials, complying with regulations and standards, and adapting to changing customer requirements. To overcome these challenges, it is important to have a well-defined design and manufacturing process, as well as strong project management and communication skills.
Conclusion
Wire harness assembly is a critical process in the manufacturing of electrical systems for various industries, including automotive, aerospace, telecommunications, and consumer electronics. By bundling wires, cables, and connectors together into a single unit, wire harnesses simplify the installation process, improve reliability, and reduce costs compared to traditional point-to-point wiring methods.
The wire harness assembly process involves several steps, including design, material selection, cutting and stripping, crimping and soldering, routing and bundling, testing and inspection, and packaging and shipping. Each step must be performed with precision and attention to detail to ensure the final product meets the required specifications and can withstand the intended application and environment.
As the demand for more complex and compact electrical systems continues to grow, the wire harness assembly industry must adapt to new technologies and trends, such as miniaturization, automation, wireless technology, and sustainable materials. By staying at the forefront of these trends and continually improving their processes and products, wire harness manufacturers can meet the evolving needs of their customers and remain competitive in the marketplace.
Leave a Reply