Introduction to Plating in Electronics Manufacturing
Plating is a crucial process in the manufacturing of printed circuit boards (PCBs) and electronic components. It involves the deposition of a thin layer of metal onto the surface of a substrate, such as a PCB or a component lead. Plating serves multiple purposes, including improving electrical conductivity, enhancing solderability, providing corrosion resistance, and improving the overall aesthetic appearance of the product.
In the context of PCB manufacturing, two primary types of plating are commonly used: board plating and hole plating. Board plating refers to the process of applying a layer of metal onto the surface of the PCB, while hole plating involves depositing metal inside the drilled holes of the PCB to create electrical connections between layers.
The Importance of Board Plating
Board plating is an essential step in the PCB manufacturing process, as it provides several key benefits:
1. Improved Electrical Conductivity
One of the primary purposes of board plating is to improve the electrical conductivity of the PCB. By applying a layer of highly conductive metal, such as copper, onto the surface of the board, the electrical signals can travel more efficiently between components. This is particularly important for high-speed and high-frequency applications, where signal integrity is critical.
2. Enhanced Solderability
Plating the surface of the PCB with a solderable metal, such as tin or silver, improves the solderability of the board. This means that components can be easily and reliably soldered onto the board during the assembly process. Good solderability ensures strong mechanical and electrical connections between the components and the PCB.
3. Corrosion Resistance
Certain metals, such as gold and nickel, are often used in board plating to provide corrosion resistance. These metals form a protective layer on the surface of the PCB, preventing oxidation and corrosion of the underlying copper traces. This is particularly important in harsh environments where the PCB may be exposed to moisture, chemicals, or other corrosive agents.
4. Improved Aesthetic Appearance
Board plating can also enhance the aesthetic appearance of the PCB. By applying a uniform layer of metal onto the surface of the board, the overall look of the PCB can be improved. This is especially relevant for consumer electronics, where the visual appeal of the product is important.
The Significance of Hole Plating
Hole plating is another critical aspect of PCB manufacturing, as it enables the creation of electrical connections between the layers of a multi-layer PCB.
1. Electrical Connectivity Between Layers
In a multi-layer PCB, the drilled holes, also known as vias, are used to connect the different layers of the board. By plating the inside of these holes with a conductive metal, such as copper, electrical signals can travel between the layers, allowing for more complex and compact circuit designs.
2. Mechanical Reinforcement
Hole plating also provides mechanical reinforcement to the PCB. The plated metal inside the holes helps to strengthen the connection between the layers, making the board more durable and less susceptible to delamination or other mechanical failures.
3. Thermal Management
Plated through-holes can also serve as thermal vias, helping to dissipate heat from components on the surface of the PCB to the inner layers or the opposite side of the board. This is particularly important for high-power components that generate significant amounts of heat, as it helps to prevent overheating and ensures the reliable operation of the circuit.
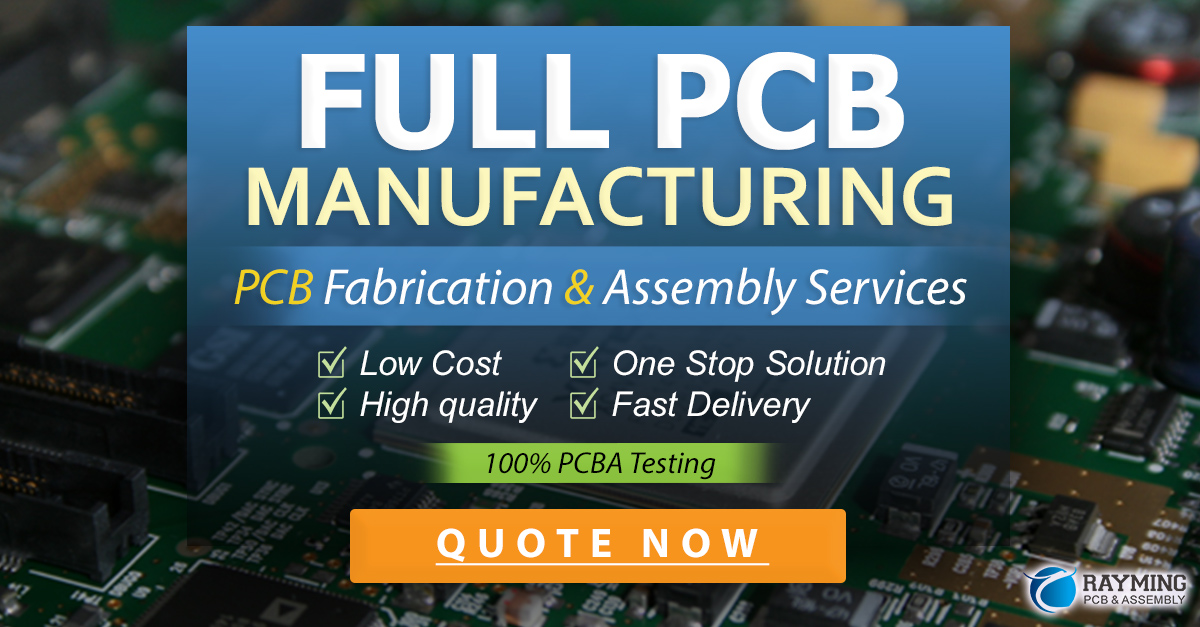
The Plating Process
The plating process typically involves several steps, which may vary depending on the specific requirements of the PCB and the type of metal being deposited.
1. Surface Preparation
Before plating can begin, the surface of the PCB must be properly prepared. This usually involves cleaning the board to remove any contaminants, such as dirt, grease, or oxide layers. The cleaning process may include mechanical abrasion, chemical etching, or a combination of both.
2. Electroless Plating
Electroless plating is a chemical process that deposits a thin layer of metal onto the surface of the PCB without the use of an external electrical current. This process is often used to deposit a layer of copper onto the non-conductive surfaces of the PCB, such as the drilled holes, to provide a conductive base for subsequent electroplating.
3. Electrolytic Plating
Electrolytic plating, also known as electroplating, is the process of depositing a layer of metal onto the surface of the PCB using an electrical current. The PCB is placed in an electrolytic bath containing a solution of the metal to be deposited, and an electrical current is applied. The metal ions in the solution are attracted to the surface of the PCB, where they are reduced and deposited as a solid layer of metal.
4. Final Finishing
After the plating process is complete, the PCB may undergo additional finishing steps, such as surface coating or solder mask application. These steps help to protect the plated surfaces and improve the overall durability and functionality of the PCB.
Common Plating Materials
Several metals are commonly used in PCB plating, each with its own unique properties and advantages.
1. Copper
Copper is the most widely used metal in PCB plating, as it provides excellent electrical conductivity and is relatively inexpensive. Copper is typically used as the base layer for board plating and hole plating, and it is often covered with additional layers of other metals for protection or enhanced functionality.
2. Tin
Tin is often used as a final finish for PCBs, as it provides good solderability and protects the underlying copper from oxidation. Tin plating is commonly used in the HASL (Hot Air Solder Leveling) process, where the PCB is dipped in molten tin to create a uniform solder coating.
3. Nickel
Nickel is often used as an undercoat for other plating materials, such as gold or silver. It provides good corrosion resistance and acts as a barrier layer to prevent the diffusion of the base metal into the final finish. Nickel plating is commonly used in the ENIG (Electroless Nickel Immersion Gold) process.
4. Gold
Gold plating is used in high-reliability applications, such as aerospace, military, and medical devices. Gold provides excellent corrosion resistance, solderability, and electrical conductivity. However, it is also one of the most expensive plating materials.
5. Silver
Silver plating is sometimes used as an alternative to gold, as it provides similar benefits at a lower cost. Silver offers excellent electrical conductivity and good solderability, but it is less resistant to corrosion compared to gold.
Quality Control in Plating
To ensure the quality and reliability of plated PCBs, several quality control measures are employed throughout the manufacturing process.
1. Thickness Measurement
The thickness of the plated metal layer is a critical parameter that affects the performance and reliability of the PCB. Thickness measurements are typically performed using non-destructive methods, such as X-ray fluorescence (XRF) or beta backscatter, to ensure that the plating meets the specified requirements.
2. Adhesion Testing
Adhesion testing is performed to ensure that the plated metal layer is securely bonded to the surface of the PCB. This is typically done using a peel test, where a strip of adhesive tape is applied to the plated surface and then peeled off at a specified angle and speed. The amount of metal that is peeled off with the tape is used to assess the adhesion of the plating.
3. Solderability Testing
Solderability testing is used to evaluate the ability of the plated surface to be wetted by molten solder. This is typically done using a wetting balance test, where a sample of the plated surface is dipped into molten solder, and the force required to remove it is measured. The time required for the solder to wet the surface and the percentage of the surface that is wetted are used to assess the solderability of the plating.
4. Porosity Testing
Porosity testing is used to detect any voids or pinholes in the plated metal layer that could compromise the electrical or mechanical integrity of the PCB. This is typically done using a dye penetrant test, where a colored dye is applied to the surface of the plating and then washed off. Any pores or defects in the plating will retain the dye, making them visible for inspection.
Challenges and Advancements in Plating Technology
As the electronics industry continues to evolve, so do the challenges and advancements in plating technology.
1. Miniaturization
The trend towards miniaturization in electronics has led to smaller and more densely packed PCBs, which require more precise and uniform plating. This has driven the development of advanced plating techniques, such as electrochemical deposition (ECD) and electroless nickel electroless palladium immersion gold (ENEPIG), which can provide high-quality plating for fine-pitch components and high-density interconnects.
2. Environmental Concerns
Traditional plating processes often involve the use of hazardous chemicals, such as lead and hexavalent chromium, which can have negative impacts on the environment and human health. In response to these concerns, the electronics industry has been developing and adopting more environmentally friendly plating technologies, such as trivalent chromium and lead-free solders.
3. High-Frequency Applications
The increasing demand for high-frequency and high-speed electronics, such as 5G wireless devices and high-performance computing systems, has led to new challenges in PCB plating. At higher frequencies, the electrical properties of the plated surfaces become more critical, as they can affect signal integrity and electromagnetic compatibility (EMC). This has driven the development of advanced plating materials and techniques, such as low-loss dielectrics and embedded shielding, to meet the demanding requirements of these applications.
Frequently Asked Questions (FAQ)
1. What is the difference between electroless and electrolytic plating?
Electroless plating is a chemical process that deposits a thin layer of metal onto a surface without the use of an external electrical current. In contrast, electrolytic plating (also known as electroplating) uses an electrical current to deposit metal ions from a solution onto the surface of a substrate. Electroless plating is often used to provide a conductive base layer for subsequent electroplating, while electrolytic plating is used to deposit thicker layers of metal for improved conductivity, solderability, or corrosion resistance.
2. Why is copper commonly used as a base layer in PCB plating?
Copper is widely used as a base layer in PCB plating due to its excellent electrical conductivity, relative affordability, and ease of deposition. Copper provides a conductive foundation for subsequent layers of plating, such as nickel, gold, or tin, which can enhance the solderability, corrosion resistance, or aesthetic appearance of the PCB. Additionally, copper is compatible with both electroless and electrolytic plating processes, making it a versatile choice for PCB manufacturing.
3. What are the advantages of using gold plating in high-reliability applications?
Gold plating offers several advantages for high-reliability applications, such as aerospace, military, and medical devices. Gold provides excellent corrosion resistance, as it does not oxidize or tarnish in normal environmental conditions. This helps to maintain the electrical and mechanical integrity of the plated surfaces over extended periods. Gold also offers superior solderability, ensuring strong and reliable connections between components and the PCB. Additionally, gold’s excellent electrical conductivity makes it suitable for high-frequency and high-speed applications, where signal integrity is critical.
4. How does hole plating contribute to the mechanical strength of a PCB?
Hole plating plays a crucial role in enhancing the mechanical strength of a PCB, particularly in multi-layer boards. By depositing a layer of metal (usually copper) inside the drilled holes, or vias, the plating creates a strong mechanical bond between the layers of the PCB. This helps to prevent delamination, where the layers of the board separate due to stress or thermal cycling. The plated holes also provide anchoring points for components, further improving the overall mechanical stability of the assembled PCB.
5. What are some of the environmental concerns associated with traditional plating processes, and how is the industry addressing them?
Traditional plating processes often involve the use of hazardous chemicals, such as lead and hexavalent chromium, which can have negative impacts on the environment and human health. Lead, for example, is a toxic metal that can accumulate in the body and cause serious health problems, while hexavalent chromium is a known carcinogen. To address these concerns, the electronics industry has been developing and adopting more environmentally friendly plating technologies. These include the use of trivalent chromium, which is less toxic than hexavalent chromium, and the adoption of lead-free solders, which eliminate the need for lead in the plating process. Additionally, many manufacturers are implementing stricter waste management and disposal practices to minimize the environmental impact of their plating operations.
Conclusion
Board plating and hole plating are essential processes in the manufacturing of printed circuit boards and electronic components. They serve critical functions, such as improving electrical conductivity, enhancing solderability, providing corrosion resistance, and ensuring mechanical integrity. As the electronics industry continues to evolve, driven by trends such as miniaturization, high-frequency applications, and environmental sustainability, plating technologies must adapt to meet these challenges. By understanding the fundamental principles, materials, and quality control measures involved in PCB plating, engineers and manufacturers can design and produce high-quality, reliable electronic products that meet the ever-increasing demands of the market.
Leave a Reply