Introduction to PCB Drilling
Printed Circuit Board (PCB) drilling is a crucial step in the PCB fabrication process. It involves creating holes in the PCB substrate to allow for the connection of electronic components and the routing of electrical signals. Precise drilling is essential for ensuring the reliability and functionality of the final PCB product.
In this article, we will explore the basics of PCB drilling, the importance of precise drilling, and how it can help reduce the cost of PCB fabrication.
Types of PCB Drilling
There are two main types of PCB drilling:
-
Mechanical Drilling: This is the most common method of PCB drilling. It involves using a drill bit to create holes in the PCB substrate. The drill bit is typically made of carbide or diamond and is mounted on a high-speed spindle that rotates at speeds up to 200,000 RPM.
-
Laser Drilling: This method uses a laser beam to create holes in the PCB substrate. Laser drilling is typically used for creating smaller holes (less than 0.1mm in diameter) and for drilling in hard-to-reach areas.
Comparison of Mechanical and Laser Drilling
Parameter | Mechanical Drilling | Laser Drilling |
---|---|---|
Hole Size | > 0.1mm | < 0.1mm |
Drilling Speed | Fast | Slow |
Cost | Low | High |
Accuracy | High | Very High |
Flexibility | Limited | High |
Importance of Precise Drilling
Precise drilling is critical for several reasons:
-
Signal Integrity: Precise drilling ensures that the holes are the correct size and in the correct location. This is important for maintaining signal integrity and preventing signal loss or interference.
-
Component Placement: Precise drilling ensures that the holes are correctly aligned with the pads on the PCB. This is important for accurate component placement and for ensuring a good solder joint.
-
Reliability: Precise drilling helps to prevent defects such as drill wander, which can cause the drill bit to deviate from its intended path. This can lead to shorts or opens in the circuit and can reduce the reliability of the final product.
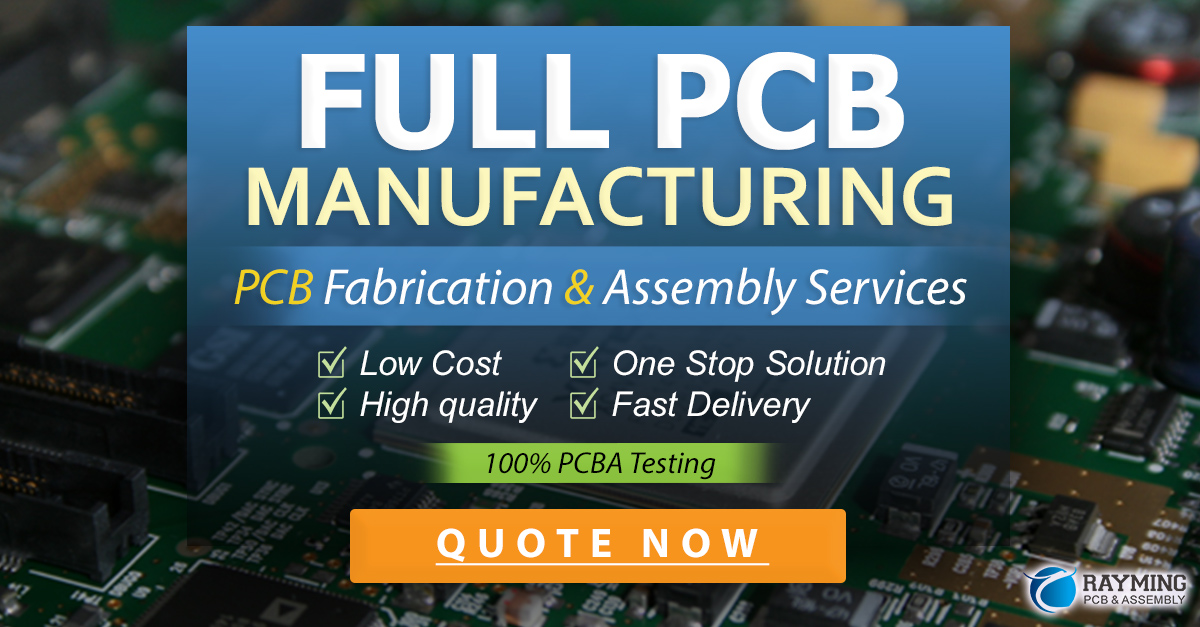
How Precise Drilling Can Reduce PCB fabrication costs
Precise drilling can help to reduce the cost of PCB fabrication in several ways:
-
Reduced Scrap: Precise drilling helps to reduce the number of defective PCBs that need to be scrapped. This can significantly reduce material costs and improve production efficiency.
-
Faster Production: Precise drilling allows for faster production speeds, as there is less need for manual inspection and rework. This can help to reduce labor costs and improve overall throughput.
-
Fewer Iterations: Precise drilling helps to reduce the number of design iterations required to achieve the desired functionality. This can help to reduce design and prototyping costs.
-
Improved Yield: Precise drilling helps to improve the overall yield of the PCB fabrication process. This means that more PCBs can be produced from a given amount of raw material, reducing the cost per unit.
Best Practices for PCB Drilling
To ensure precise drilling and minimize costs, there are several best practices that should be followed:
-
Use High-Quality Drill Bits: Using high-quality drill bits can help to reduce wear and tear on the drilling equipment and improve the accuracy of the drilling process.
-
Optimize Drilling Parameters: Optimizing drilling parameters such as feed rate, spindle speed, and depth of cut can help to improve drilling accuracy and reduce cycle time.
-
Implement Quality Control Measures: Implementing quality control measures such as visual inspection and electrical testing can help to identify defects early in the process and reduce the need for rework.
-
Use Automated Drilling Equipment: Using automated drilling equipment can help to improve drilling accuracy and consistency, while also reducing labor costs.
Conclusion
PCB drilling is a critical step in the PCB fabrication process, and precise drilling is essential for ensuring the reliability and functionality of the final product. By following best practices and implementing precise drilling techniques, manufacturers can reduce the cost of PCB fabrication while improving product quality and reliability.
Frequently Asked Questions (FAQ)
-
What is the difference between mechanical drilling and laser drilling?
Mechanical drilling uses a physical drill bit to create holes in the PCB substrate, while laser drilling uses a laser beam. Laser drilling is typically used for creating smaller holes and for drilling in hard-to-reach areas. -
Why is precise drilling important for signal integrity?
Precise drilling ensures that the holes are the correct size and in the correct location, which is important for maintaining signal integrity and preventing signal loss or interference. -
How can precise drilling help to reduce PCB fabrication costs?
Precise drilling can help to reduce PCB fabrication costs by reducing scrap, improving production efficiency, reducing the number of design iterations required, and improving overall yield. -
What are some best practices for PCB drilling?
Some best practices for PCB drilling include using high-quality drill bits, optimizing drilling parameters, implementing quality control measures, and using automated drilling equipment. -
What are the advantages of using automated drilling equipment?
Automated drilling equipment can help to improve drilling accuracy and consistency, while also reducing labor costs. It can also help to reduce the risk of operator error and improve overall production efficiency.
Leave a Reply