What is Automatic X-ray inspection (AXI)?
Automatic X-ray Inspection (AXI) is a non-destructive testing method used to inspect the internal structure of manufactured products, particularly in the electronics industry. AXI systems utilize high-resolution X-ray imaging to detect defects, such as voids, cracks, and foreign objects, that may not be visible through other inspection methods. This advanced technology has become increasingly important in ensuring the quality and reliability of electronic components and assemblies.
How AXI Works
AXI systems consist of an X-ray source, a detector, and a motion control system. The X-ray source emits high-energy photons that penetrate the object being inspected. As the X-rays pass through the object, they are attenuated based on the density and thickness of the materials they encounter. The detector captures the resulting X-ray image, which is then processed by specialized software to identify any anomalies or defects.
The motion control system allows for precise positioning of the object relative to the X-ray source and detector, enabling the capture of multiple views and angles. This is particularly important for inspecting complex, multi-layered electronic assemblies, such as printed circuit boards (PCBs).
Advantages of AXI
- Non-destructive: AXI allows for the inspection of internal structures without damaging the product.
- High-resolution imaging: AXI systems can detect minute defects that may be missed by other inspection methods.
- Increased efficiency: Automated inspection reduces the time and labor required for manual inspection.
- Improved quality control: AXI helps identify defects early in the manufacturing process, reducing the risk of faulty products reaching customers.
- Cost-effective: By catching defects early, AXI can help reduce the costs associated with rework and product failures.
Applications of AXI in the Electronics Industry
Printed Circuit Board (PCB) Inspection
AXI is widely used in the inspection of PCBs, which are the backbone of most electronic devices. PCBs consist of multiple layers of conductive and insulating materials, with components mounted on the surface or embedded within the layers. AXI can detect a variety of defects in PCBs, including:
- Solder joint defects: Voids, cracks, or insufficient solder in the connections between components and the PCB.
- Component placement errors: Misaligned or missing components.
- Trace defects: Breaks or shorts in the conductive pathways.
- Foreign object detection: Identifying debris or contaminants that may cause short circuits or other issues.
PCB inspection Process
The AXI process for PCB inspection typically involves the following steps:
- Loading: The PCB is placed on a conveyor or fixture and automatically fed into the AXI system.
- Scanning: The PCB is exposed to X-rays from multiple angles, creating a series of high-resolution images.
- Analysis: Specialized software processes the X-ray images, comparing them to a reference model or design data to identify any discrepancies or defects.
- Reporting: The system generates a detailed report of the inspection results, highlighting any areas of concern and providing information for further analysis or repair.
Semiconductor Package Inspection
AXI is also used to inspect semiconductor packages, such as ball grid arrays (BGAs), chip scale packages (CSPs), and flip chips. These packages house integrated circuits (ICs) and provide electrical connections to the PCB. AXI can detect defects in the internal structure of the package, as well as the connections between the package and the PCB.
Common defects detected by AXI in semiconductor packages include:
- Void formation: Air pockets or gaps in the solder joints or underfill material.
- Cracks: Fractures in the package substrate or interconnects.
- Delamination: Separation of the layers within the package.
- Bridging: Unintended connections between adjacent solder joints or pins.
Counterfeit Component Detection
AXI can also be used to identify counterfeit electronic components, which pose a significant risk to the reliability and safety of electronic devices. Counterfeit components may have internal structures that differ from genuine parts, such as missing or altered die, incorrect wire bonding, or non-standard packaging materials. By comparing X-ray images of suspect components to known genuine parts, AXI can help detect and prevent the use of counterfeit components in electronic assemblies.
Advancements in AXI Technology
Computed Tomography (CT) Scanning
Computed tomography (CT) scanning is an advanced form of X-ray imaging that provides three-dimensional (3D) views of the internal structure of an object. In CT scanning, multiple X-ray images are taken from different angles and then combined using sophisticated algorithms to create a detailed 3D model. This technology allows for even more comprehensive inspection of complex electronic assemblies, enabling the detection of defects that may be obscured in traditional 2D X-ray images.
Artificial Intelligence (AI) and Machine Learning (ML)
The integration of artificial intelligence (AI) and machine learning (ML) techniques into AXI systems is revolutionizing the field of automated inspection. AI and ML algorithms can be trained to recognize patterns and anomalies in X-ray images, improving the speed and accuracy of defect detection. These algorithms can also adapt and learn over time, continuously enhancing their performance as they are exposed to more data.
Some examples of AI and ML applications in AXI include:
- Automated defect classification: AI algorithms can automatically categorize defects based on their characteristics, reducing the need for manual review and interpretation.
- Predictive maintenance: ML models can analyze inspection data to predict the likelihood of future defects or failures, enabling proactive maintenance and reducing downtime.
- Adaptive inspection: AI-powered AXI systems can adjust inspection parameters in real-time based on the characteristics of the product being inspected, optimizing the inspection process for each unique assembly.
Inline AXI Integration
Traditionally, AXI has been performed as a standalone process, with products being removed from the production line for inspection and then reintroduced after the analysis is complete. However, recent advancements have enabled the integration of AXI systems directly into the production line, allowing for real-time inspection and feedback.
Inline AXI integration offers several benefits, including:
- Reduced cycle time: By eliminating the need to remove products from the line for inspection, inline AXI can significantly reduce the overall production cycle time.
- Early defect detection: Inline AXI allows for the identification of defects as soon as they occur, enabling immediate corrective action and minimizing the production of faulty products.
- Increased automation: Inline AXI systems can be fully automated, reducing the need for manual handling and inspection.
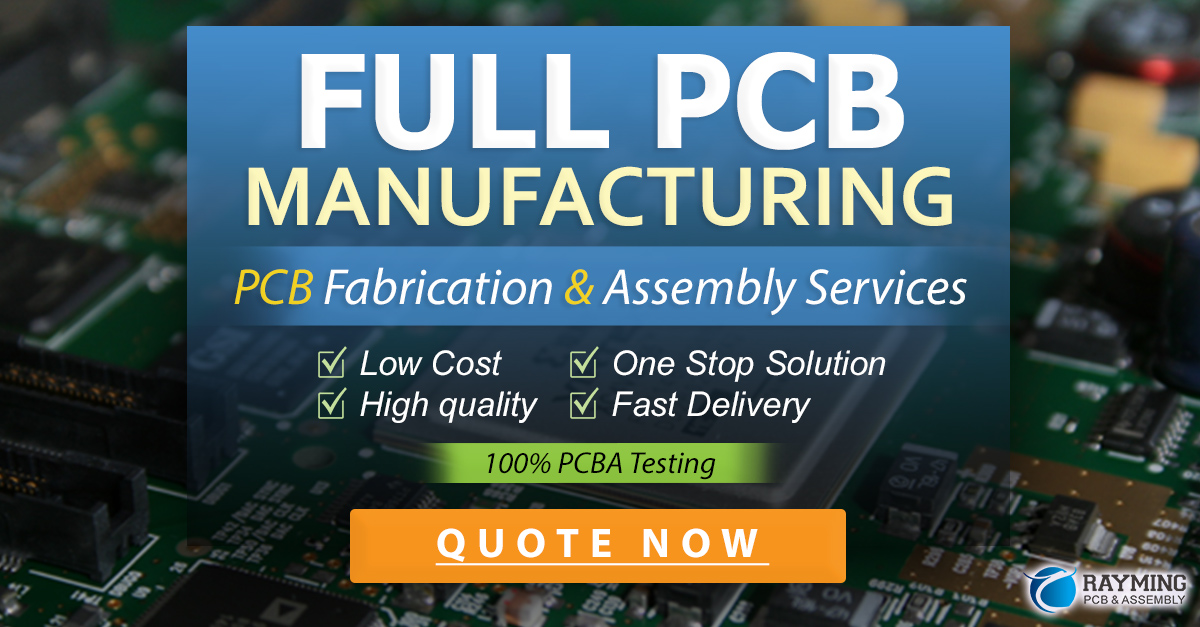
Challenges and Considerations in Implementing AXI
Cost
AXI systems can be a significant investment for manufacturers, with costs ranging from tens of thousands to several hundred thousand dollars, depending on the complexity and capabilities of the system. However, the long-term benefits of improved quality control and reduced defect-related costs often justify the initial investment.
Radiation Safety
X-ray radiation can be harmful to human health if not properly managed. AXI systems must be designed and operated in compliance with strict radiation safety regulations to ensure the protection of workers and the environment. This includes proper shielding, monitoring, and training for personnel working with or near the equipment.
Data Management and Analysis
AXI systems generate vast amounts of data, including high-resolution images and inspection reports. Managing and analyzing this data effectively requires robust data management systems and skilled personnel. Manufacturers must invest in the necessary infrastructure and expertise to fully leverage the insights provided by AXI data.
Integration with Existing Processes
Implementing AXI into existing manufacturing processes can be challenging, particularly when integrating inline systems. Manufacturers must carefully plan and execute the integration to minimize disruption to production and ensure a smooth transition. This may involve modifications to existing equipment, changes to process flows, and training for personnel.
Frequently Asked Questions (FAQ)
-
Q: How does AXI differ from other inspection methods, such as automated optical inspection (AOI)?
A: AXI uses X-rays to inspect the internal structure of products, while AOI uses visible light to inspect the surface. AXI can detect defects that are hidden from view, such as voids or cracks within solder joints, which AOI cannot detect. -
Q: Can AXI be used to inspect non-electronic products?
A: Yes, AXI can be used to inspect a wide range of products, including mechanical assemblies, castings, and 3D-printed parts. However, the electronics industry is the primary user of AXI technology due to the complexity and high-reliability requirements of electronic assemblies. -
Q: How long does an AXI inspection take?
A: The duration of an AXI inspection depends on factors such as the size and complexity of the product, the resolution of the X-ray images, and the number of views required. A typical PCB inspection can take anywhere from a few seconds to several minutes. -
Q: Can AXI detect all types of defects?
A: While AXI is a powerful inspection tool, it cannot detect all types of defects. Some defects, such as surface contamination or subtle material changes, may not be visible in X-ray images. Additionally, the detection capability of an AXI system depends on factors such as the resolution of the X-ray source and detector, and the quality of the image analysis software. -
Q: How much training is required to operate an AXI system?
A: Operating an AXI system requires specialized knowledge and skills. Training typically covers topics such as X-ray safety, system operation, image interpretation, and data analysis. The duration and depth of training depend on the complexity of the system and the operator’s role. Most manufacturers provide comprehensive training for their AXI systems, which can range from a few days to several weeks.
Leave a Reply