Introduction to PCB Anti-interference
Printed Circuit Boards (PCBs) are the foundation of modern electronics. They provide a platform for mounting and interconnecting electronic components to create functional circuits. However, as circuits become more complex and operate at higher frequencies, they become more susceptible to electromagnetic interference (EMI). EMI can cause signal integrity issues, leading to malfunctions or even complete system failure. Therefore, it is crucial to implement effective anti-interference methods in PCB circuit design.
In this article, we will explore various techniques and strategies for minimizing interference in PCB circuits. We will discuss the sources of interference, the impact of interference on circuit performance, and the best practices for designing PCBs with high immunity to interference.
Understanding Electromagnetic Interference (EMI) in PCBs
Electromagnetic Interference (EMI) is the disruption of the normal operation of an electronic device due to unwanted electromagnetic energy. EMI can be generated by various sources, both internal and external to the PCB. Some common sources of EMI include:
- Power supply noise
- Digital clock signals
- High-speed data lines
- Electrostatic Discharge (ESD)
- Radio Frequency Interference (RFI) from nearby electronic devices
EMI can manifest in two forms: conducted and radiated. Conducted EMI propagates through the physical connections between components, such as power lines, signal traces, and ground planes. Radiated EMI, on the other hand, propagates through the air as electromagnetic waves.
The impact of EMI on PCB circuits can be severe. It can cause signal integrity issues, such as crosstalk, signal distortion, and timing errors. In extreme cases, EMI can lead to complete system failure or even permanent damage to components.
PCB Layout Techniques for Minimizing Interference
Proper PCB layout is essential for minimizing interference in circuits. By following best practices in PCB layout, designers can reduce the coupling of unwanted signals and improve the overall immunity of the circuit to EMI. Some key PCB layout techniques for minimizing interference include:
1. Ground Plane Design
A solid ground plane is one of the most effective ways to reduce EMI in PCB circuits. A ground plane provides a low-impedance return path for high-frequency currents, minimizing the coupling of unwanted signals between components. When designing a ground plane, consider the following:
- Use a continuous ground plane covering as much of the PCB area as possible.
- Avoid splitting the ground plane unnecessarily, as this can create high-impedance paths for return currents.
- Use multiple vias to connect components to the ground plane, minimizing the inductance of the return path.
2. Power Supply Decoupling
Power supply noise is a common source of EMI in PCB circuits. To minimize the impact of power supply noise, it is essential to implement proper decoupling techniques. Decoupling capacitors should be placed as close as possible to the power pins of ICs, providing a local reservoir of charge and minimizing the inductance of the power supply traces.
Consider the following when implementing power supply decoupling:
- Use a combination of bulk and ceramic capacitors to provide both high-frequency and low-frequency decoupling.
- Place decoupling capacitors as close as possible to the power pins of ICs.
- Use multiple decoupling capacitors in parallel to reduce the effective series inductance (ESL) and improve high-frequency performance.
3. Signal Trace Routing
Proper signal trace routing is critical for minimizing crosstalk and other signal integrity issues in PCB circuits. When routing signal traces, consider the following:
- Keep signal traces as short as possible to minimize the loop area and reduce the potential for EMI coupling.
- Avoid running signal traces parallel to each other for long distances, as this can increase crosstalk.
- Use ground shields between sensitive signal traces to reduce coupling.
- Avoid routing signal traces near the edges of the PCB, as this can increase the potential for EMI radiation.
4. Component Placement
Component placement plays a crucial role in minimizing interference in PCB circuits. Proper component placement can reduce the coupling of unwanted signals and improve the overall signal integrity of the circuit. When placing components, consider the following:
- Group components based on their function and signal type to minimize the coupling of unwanted signals.
- Place sensitive analog components away from noisy digital components to reduce the potential for EMI coupling.
- Orient components to minimize the loop area formed by their connections, reducing the potential for EMI coupling.
Here’s an example of a table summarizing the key PCB layout techniques for minimizing interference:
Technique | Description |
---|---|
Ground Plane Design | Use a continuous ground plane to provide a low-impedance return path |
Power Supply Decoupling | Place decoupling capacitors close to IC power pins to minimize power supply noise |
Signal Trace Routing | Keep traces short, avoid parallel routing, and use ground shields |
Component Placement | Group components by function, separate analog and digital, and minimize loop area |
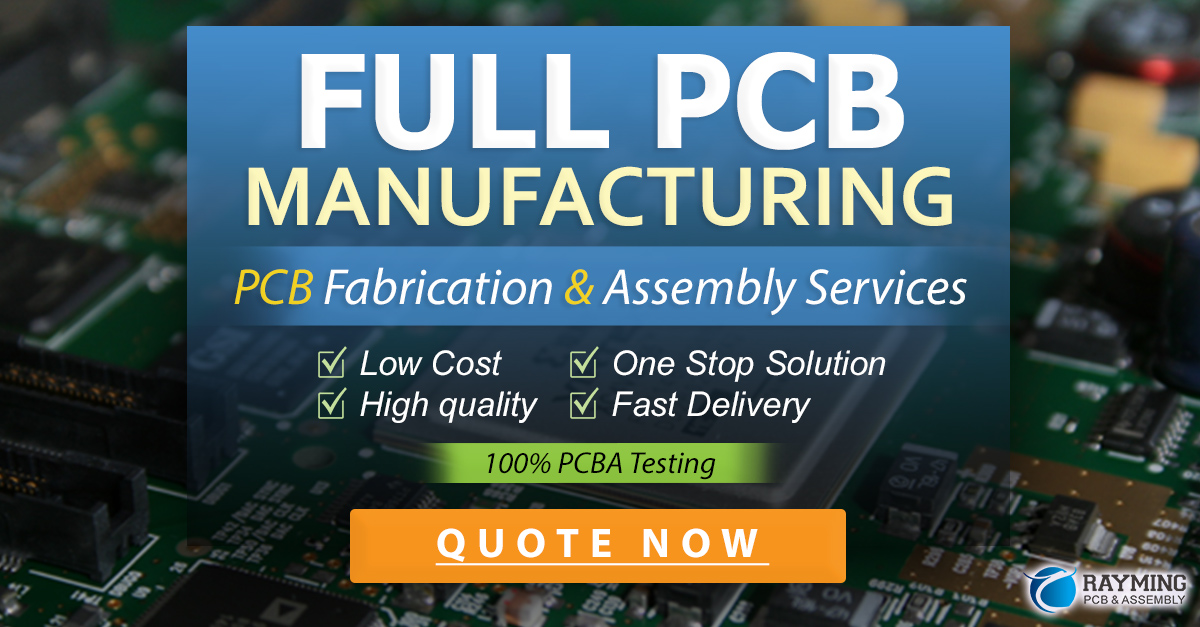
EMI Shielding Techniques
In addition to proper PCB layout, EMI shielding techniques can be employed to further reduce the impact of interference on PCB circuits. EMI shielding involves enclosing sensitive components or entire circuits in a conductive enclosure to block unwanted electromagnetic fields. Some common EMI shielding techniques include:
1. Faraday Cages
A Faraday cage is a conductive enclosure that blocks external electromagnetic fields. By placing sensitive components or circuits inside a Faraday cage, designers can effectively shield them from external EMI sources. Faraday cages can be constructed using metal enclosures, conductive gaskets, or conductive coatings.
2. Shielding Materials
Various shielding materials can be used to block EMI in PCB circuits. Some common shielding materials include:
- Metal foils: Copper, aluminum, or other metal foils can be applied to the surface of the PCB to provide shielding.
- Conductive elastomers: These materials combine the flexibility of elastomers with the conductivity of metals, making them suitable for shielding applications that require a conformable seal.
- Conductive coatings: Conductive paints or sprays can be applied to the surface of the PCB or enclosure to provide shielding.
3. Shielded Connectors and Cables
When signals must be transmitted between different parts of a system, it is essential to use shielded connectors and cables to minimize EMI coupling. Shielded connectors and cables feature a conductive outer layer that prevents the penetration of external electromagnetic fields.
Here’s an example table comparing the effectiveness of different EMI shielding materials:
Material | Shielding Effectiveness (dB) |
---|---|
Copper Foil | 80-120 |
Aluminum Foil | 60-100 |
Conductive Elastomers | 40-80 |
Conductive Coatings | 30-60 |
Filtering Techniques for EMI Suppression
Filtering is another effective technique for suppressing EMI in PCB circuits. By using filters, designers can attenuate unwanted high-frequency signals while allowing desired signals to pass through unaffected. Some common filtering techniques include:
1. Low-Pass Filters
Low-pass filters are designed to attenuate high-frequency signals while allowing low-frequency signals to pass through. They are commonly used to suppress high-frequency noise in power supply lines and signal traces. Low-pass filters can be implemented using passive components such as resistors, capacitors, and inductors.
2. Ferrite Beads
Ferrite beads are passive components that act as high-frequency absorbers. They are often used in series with power supply lines or signal traces to suppress high-frequency noise. Ferrite beads have a high impedance at high frequencies, effectively blocking unwanted signals while allowing DC and low-frequency signals to pass through.
3. Common Mode Chokes
Common mode chokes are transformers designed to suppress common mode noise in differential signal pairs. They are commonly used in high-speed digital interfaces, such as USB or Ethernet, to reduce EMI emissions. Common mode chokes work by presenting a high impedance to common mode currents while allowing differential signals to pass through unaffected.
Here’s an example table comparing the attenuation characteristics of different filtering components:
Component | Attenuation (dB) at 100 MHz |
---|---|
Low-Pass Filter | 20-40 |
Ferrite Bead | 10-30 |
Common Mode Choke | 20-50 |
Grounding and Shielding Strategies
Proper grounding and shielding strategies are essential for minimizing EMI in PCB circuits. A well-designed grounding and shielding scheme can effectively reduce the coupling of unwanted signals and improve the overall EMI performance of the system. Some key grounding and shielding strategies include:
1. Star Grounding
Star grounding is a technique where all ground connections are made to a single point, known as the star point. This approach minimizes the ground loop area and reduces the potential for ground bounce and other noise-related issues. In a star grounding scheme, each subsystem or component has its own dedicated ground connection to the star point.
2. Hybrid Grounding
Hybrid grounding combines the benefits of star grounding and multi-point grounding. In a hybrid grounding scheme, sensitive analog circuits use a star grounding approach, while digital circuits use a multi-point grounding approach. This allows for the isolation of sensitive analog circuits from noisy digital circuits while still providing a low-impedance ground return path for high-frequency currents.
3. Shielding Gaskets
Shielding gaskets are conductive materials used to ensure a continuous electrical connection between two conductive surfaces, such as a PCB and its enclosure. Shielding gaskets help to prevent the leakage of electromagnetic fields through gaps or seams in the shielding enclosure. Common types of shielding gaskets include:
- Conductive elastomers
- Conductive foam
- Fingerstock gaskets
- Wire mesh gaskets
Here’s an example table comparing the shielding effectiveness of different gasket materials:
Gasket Material | Shielding Effectiveness (dB) |
---|---|
Conductive Elastomers | 60-100 |
Conductive Foam | 50-80 |
Fingerstock Gaskets | 80-120 |
Wire Mesh Gaskets | 60-100 |
Frequently Asked Questions (FAQ)
1. What is the difference between conducted and radiated EMI?
Conducted EMI propagates through physical connections, such as power lines and signal traces, while radiated EMI propagates through the air as electromagnetic waves.
2. How does a ground plane help to reduce EMI in PCB circuits?
A ground plane provides a low-impedance return path for high-frequency currents, minimizing the coupling of unwanted signals between components.
3. What is the purpose of decoupling capacitors in PCB circuits?
Decoupling capacitors are used to minimize power supply noise by providing a local reservoir of charge and reducing the inductance of power supply traces.
4. What are the benefits of using shielded connectors and cables in PCB circuits?
Shielded connectors and cables feature a conductive outer layer that prevents the penetration of external electromagnetic fields, minimizing EMI coupling between different parts of a system.
5. How does star grounding differ from multi-point grounding?
In a star grounding scheme, all ground connections are made to a single point, minimizing ground loop area and reducing noise. Multi-point grounding, on the other hand, connects components to the ground plane at multiple points, providing a low-impedance return path for high-frequency currents.
Conclusion
Designing PCB circuits with high immunity to electromagnetic interference is a critical aspect of modern electronics. By understanding the sources and impact of EMI, and employing effective anti-interference techniques, designers can ensure the reliable operation of their circuits in the presence of unwanted electromagnetic energy.
This article has covered a wide range of anti-interference methods, including PCB layout techniques, EMI shielding, filtering, grounding, and shielding strategies. By applying these techniques and following best practices in PCB design, engineers can minimize the impact of EMI on their circuits and improve overall system performance.
As electronic systems continue to increase in complexity and operate at higher frequencies, the importance of effective EMI mitigation will only continue to grow. By staying up-to-date with the latest techniques and strategies for PCB anti-interference, designers can ensure that their circuits remain reliable and robust in the face of evolving electromagnetic environments.
Leave a Reply