Introduction to MCPCB Manufacturing
Metal Core Printed Circuit Boards (MCPCBs) are a specialized type of PCB that utilizes a metal substrate, typically aluminum, to enhance thermal conductivity and heat dissipation. This makes MCPCBs ideal for applications that generate significant amounts of heat, such as high-power LEDs, power electronics, and automotive systems. In this article, we will explore the world of MCPCB manufacturing, focusing on Aluminum PCB flex and rigid MCPCB production at a one-stop facility.
What is MCPCB?
An MCPCB is a printed circuit board that consists of a metal core, usually aluminum, sandwiched between a dielectric layer and a copper circuit layer. The metal core acts as a heat sink, efficiently transferring heat away from the components mounted on the PCB. This improved thermal management allows for higher power densities and increased reliability in electronic devices.
Advantages of MCPCB
MCPCBs offer several advantages over traditional FR-4 PCBs:
- Enhanced thermal conductivity
- Improved heat dissipation
- Higher power handling capability
- Increased reliability and longevity
- Reduced size and weight
Aluminum PCB Flex Manufacturing
Flexible aluminum PCBs combine the benefits of MCPCBs with the versatility of flexible circuits. These boards can be bent, folded, or shaped to fit into confined spaces or conform to unique product designs. Aluminum PCB flex manufacturing involves several key processes:
Substrate Preparation
The aluminum substrate is cleaned and treated to ensure proper adhesion of the dielectric layer. This may involve chemical etching, mechanical abrasion, or anodization to create a roughened surface that promotes bonding.
Dielectric Layer Application
A thin layer of dielectric material, such as polyimide or epoxy, is applied to the prepared aluminum substrate. This layer acts as an electrical insulator between the metal core and the copper circuit layer. The dielectric material is typically applied using a lamination process under controlled temperature and pressure conditions.
Circuit Layer Patterning
The copper circuit layer is laminated onto the dielectric layer and then patterned using photolithography and etching techniques. This process creates the desired conductive traces, pads, and vias that form the electrical interconnects of the PCB.
Cover Layer Application
A cover layer, also known as a solder mask, is applied over the patterned copper layer to protect the traces from oxidation and provide electrical insulation. The cover layer is usually a polymer material that is screen printed or photoimaged onto the PCB surface.
Finishing and Cutting
Finally, the aluminum PCB flex is finished with surface treatments such as ENIG (Electroless Nickel Immersion Gold) or OSP (Organic Solderability Preservative) to enhance solderability and protect the exposed copper. The board is then cut to its final shape using precision cutting methods like laser cutting or die cutting.
Rigid MCPCB Manufacturing
Rigid MCPCBs are designed for applications that require a sturdy, non-flexible board with excellent thermal management. The manufacturing process for rigid MCPCBs is similar to that of aluminum PCB flex, with a few key differences:
Substrate Selection
Rigid MCPCBs typically use thicker aluminum substrates to provide a more robust mechanical structure. The thickness of the aluminum core can range from 0.5mm to 3.0mm, depending on the application requirements.
Multilayer Lamination
For complex designs, multiple layers of dielectric and copper can be laminated together to create a multilayer MCPCB. This process involves careful alignment and bonding of the layers under high temperature and pressure.
Drilling and Plating
Holes are drilled through the rigid MCPCB to accommodate through-hole components and provide electrical interconnects between layers. These holes are then plated with copper to create conductive vias.
Finishing and Singulation
As with aluminum PCB flex, rigid MCPCBs undergo surface finishing treatments and are then singulated into individual boards using methods like routing or V-scoring.
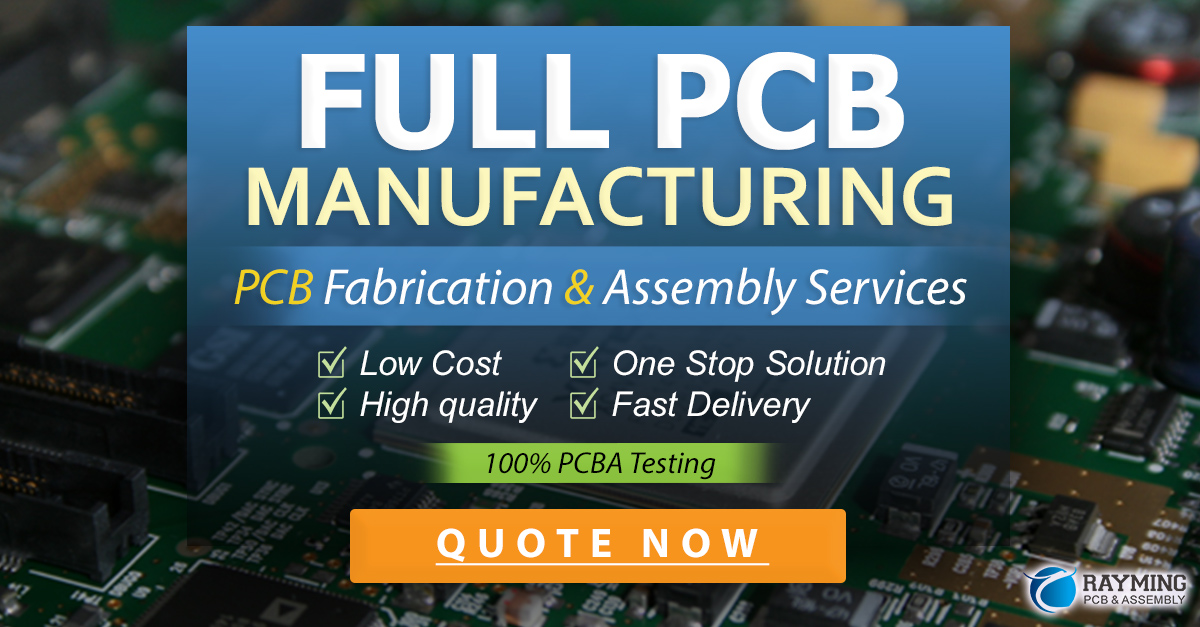
One-Stop MCPCB Manufacturing
One-stop MCPCB manufacturing refers to a facility that can handle all aspects of MCPCB production, from design and prototyping to full-scale production and assembly. This comprehensive approach offers several benefits:
- Streamlined communication and project management
- Reduced lead times and faster time-to-market
- Consistent quality control throughout the manufacturing process
- Cost savings through economies of scale
- Access to a wide range of manufacturing capabilities and expertise
MCPCB Design Considerations
When designing an MCPCB, several key factors must be considered to ensure optimal performance and manufacturability:
Thermal Management
The primary purpose of an MCPCB is to efficiently dissipate heat. Designers must carefully consider the thermal requirements of the application and select appropriate materials, layer thicknesses, and layout techniques to maximize heat transfer.
Dielectric Material Selection
The choice of dielectric material impacts the thermal conductivity, electrical insulation, and mechanical properties of the MCPCB. Common dielectric materials include polyimide, epoxy, and ceramic-filled polymers. Each material has its own set of advantages and limitations that must be evaluated based on the specific application needs.
Copper Thickness and Trace Geometry
The thickness of the copper layer and the geometry of the conductive traces affect both the electrical and thermal performance of the MCPCB. Thicker copper layers provide lower electrical resistance and better heat spreading, but may increase the overall board thickness and cost. Trace width and spacing must be carefully designed to maintain signal integrity and prevent excessive heat buildup.
Mechanical Considerations
For aluminum PCB flex designs, the mechanical properties of the board must be considered to ensure reliable operation under flexing and bending conditions. This includes selecting appropriate materials, designing suitable bend radii, and incorporating strain relief features where necessary.
MCPCB Manufacturing Challenges and Solutions
MCPCB manufacturing presents several unique challenges compared to traditional PCB production:
Thermal Expansion Mismatch
The difference in thermal expansion coefficients between the metal core, dielectric layer, and copper layer can lead to stress and delamination during temperature cycling. This issue can be mitigated by selecting materials with closely matched thermal expansion properties and using appropriate lamination techniques.
Adhesion and Bonding
Achieving strong and reliable bonding between the metal core, dielectric layer, and copper layer is critical for the long-term performance of the MCPCB. Surface preparation methods, such as chemical etching or mechanical abrasion, can improve adhesion. Additionally, using advanced lamination processes with controlled temperature and pressure profiles can ensure consistent and robust bonding.
Dimensional Stability
The high temperatures and pressures involved in MCPCB lamination can cause dimensional changes in the board, leading to misalignment of features and decreased manufacturing yields. This challenge can be addressed by using materials with low thermal expansion and high dimensional stability, as well as employing precise temperature and pressure control during lamination.
Cost Considerations
MCPCBs often have higher material and manufacturing costs compared to traditional FR-4 PCBs due to the specialized materials and processes involved. However, the improved thermal performance and reliability of MCPCBs can lead to lower system-level costs by reducing the need for additional heat sinking and improving product lifetimes. Designers must carefully balance the upfront costs with the long-term benefits when considering MCPCB solutions.
Future Trends in MCPCB Manufacturing
As electronic devices continue to push the boundaries of performance and miniaturization, MCPCB manufacturing technologies are evolving to meet these demands:
Advanced Materials
Researchers are developing new dielectric materials with higher thermal conductivity, lower thermal expansion, and improved mechanical properties. These materials, such as nanoceramic-filled polymers and boron nitride composites, promise to enhance the performance and reliability of MCPCBs in demanding applications.
Embedded Components
Integrating passive components, such as resistors and capacitors, directly into the MCPCB structure can save space, reduce assembly costs, and improve electrical performance. Advancements in embedded component technologies, such as printed resistors and embedded capacitor laminates, are enabling more compact and efficient MCPCB designs.
3D Printing
Additive manufacturing techniques, like 3D printing, are being explored for MCPCB fabrication. These methods could enable the creation of complex, three-dimensional MCPCB structures with enhanced thermal management capabilities and unique form factors.
High-Frequency Applications
As 5G wireless networks and other high-frequency applications become more prevalent, MCPCBs are being developed to meet the demanding requirements of these systems. This includes the use of low-loss dielectric materials, precision-controlled impedance traces, and advanced shielding techniques to maintain signal integrity and minimize electromagnetic interference.
Conclusion
Aluminum PCB flex and rigid MCPCB manufacturing at a one-stop facility offers numerous advantages for the production of high-performance, thermally-efficient electronic devices. By combining the benefits of metal core substrates with the flexibility of aluminum PCB flex or the robustness of rigid MCPCBs, designers can create innovative solutions for a wide range of applications.
As MCPCB technology continues to advance, with the development of new materials, manufacturing processes, and design techniques, the potential for even more compact, efficient, and reliable electronic products will continue to grow. By staying at the forefront of these advancements, one-stop MCPCB manufacturing facilities can provide customers with the cutting-edge solutions they need to succeed in an increasingly competitive market.
Frequently Asked Questions (FAQ)
- What is the difference between aluminum PCB flex and rigid MCPCB?
-
Aluminum PCB flex is a flexible MCPCB that can be bent or shaped to fit into confined spaces or conform to unique product designs. Rigid MCPCB, on the other hand, is a sturdy, non-flexible board designed for applications that require excellent thermal management and mechanical stability.
-
What are the main advantages of using MCPCBs over traditional FR-4 PCBs?
-
MCPCBs offer several advantages, including enhanced thermal conductivity, improved heat dissipation, higher power handling capability, increased reliability and longevity, and reduced size and weight compared to traditional FR-4 PCBs.
-
What materials are commonly used for the dielectric layer in MCPCBs?
-
Common dielectric materials used in MCPCBs include polyimide, epoxy, and ceramic-filled polymers. The choice of dielectric material depends on the specific application requirements, such as thermal conductivity, electrical insulation, and mechanical properties.
-
How does the thickness of the copper layer affect the performance of an MCPCB?
-
Thicker copper layers provide lower electrical resistance and better heat spreading, which can improve the electrical and thermal performance of the MCPCB. However, increasing the copper thickness may also increase the overall board thickness and cost.
-
What are some of the future trends in MCPCB manufacturing?
- Future trends in MCPCB manufacturing include the development of advanced materials with improved thermal and mechanical properties, the integration of embedded components to save space and reduce assembly costs, the exploration of 3D printing techniques for complex MCPCB structures, and the adaptation of MCPCB technology for high-frequency applications like 5G wireless networks.
Parameter | Aluminum PCB Flex | Rigid MCPCB |
---|---|---|
Flexibility | High | Low |
Thickness | Thin (typically 0.1mm to 0.3mm) | Thick (typically 0.5mm to 3.0mm) |
Thermal Conductivity | Good | Excellent |
Mechanical Stability | Moderate | High |
Typical Applications | Wearables, Automotive, Aerospace | Power Electronics, LED Lighting, Telecommunications |
Leave a Reply