Printed circuit boards form the background on which electronic components are mounted and they create connections between these components. Therefore, this necessitates the need to choose good materials for producing these boards. However, the choice of the PCB Substrate material to use can be quite challenging among PCB designers.
Since there are a huge array of materials like ceramics, metals, and FR4, PCB manufacturers are often concerned with what to use and what not to use. Ceramics such as aluminum nitride, alumina, and aluminum oxide have been used in the production of PCBs. Every material has its own advantages, properties, and features. This undermines the decision of designers to get a good understanding when making some choices.
One of the most commonly used materials for producing PCB Substrate is Alumina. Although there are two types of substrate used for ceramic boards, alumina is a more effective material compared to aluminum nitride (ALN or AIN). Due to the major properties of alumina substrate PCB, it is mostly used in applications that require great thermal conductivity and extraordinary strength. Also, this material has excellent electrical properties and good hermeticity.
Due to the constant improvement in Alumina substrate PCB it has become one of the most reliable materials for circuit boards. Its proven track record makes it of worthy importance in electronics production.
Why is Alumina Substrate PCB Useful?
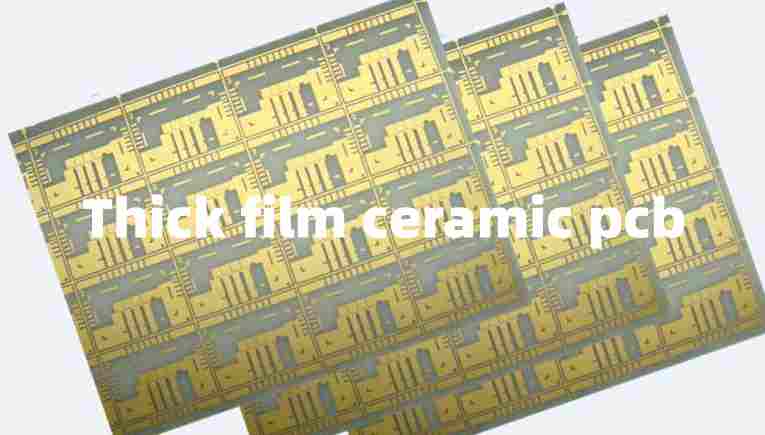
Since alumina substrate PCBs are not wholly made of alumina, they are categorized based on their components. There are three types of the Alumina substrate PCB which are 99.6% alumina substrate, 99.5% alumina substrate PCB and 96% alumina substrate.
These substrates all have their unique potentials and the capabilities to make them worthy of use in several applications. In the electronics industry, one of the highly preferred PCB substrates is the Rogers and alumina. Al203 or aluminum oxide substrate is a ceramic board that has outstanding properties, hence, its fragility makes it more daunting to process. However, it is a better choice for some PCB manufacturers due to its exceptional thermal and electrical characteristics.
Alumina substrate PCBs have great heat dissipation capabilities which help to extend the lifespan of electronic devices. These boards are particularly useful in large-scale LED lighting applications. In LED applications, the components on the circuit board produce an amount of heat as a result of high flow of current. There can be PCB burnout or component overload problems when the temperature goes beyond the normal threshold.
Another great properties of the Alumina substrate PCB is its thermal conductivity which always stays within the range between 20-30 W/m·K. Staying within this range enables better thermal management and heat transfer within the system.
Alumina substrate PCB has similar dielectric constant properties of ceramic boards. This helps to enhance the energy storage capacity and charge polarization in the electric field. The dielectric constant of alumina substrate PCB is within 8 to 10. Due to this property, this substrate is applicable for use in military, automotive, power, and some other high-performance applications. In applications where signal integrity is of great importance, the alumina substrate PCB is a top choice.
Advantages of Alumina PCB Substrate
The alumina PCB substrate has a lot of advantages. In the above section, we discussed the usefulness of this substrate in some applications. Below are some their benefits:
- It offers a good level of electrical insulation
- Alumina PCB has a good compressive strength.
- The operating temperature of this board is very high. It is between 350¡Cto1500¡C
- Also, the expansion coefficient of alumina PCB is 6-8 ppm/¡C. This value causes less stress on solder joints
- It performs exceptionally in high-frequency electronic projects.
- The texture and the makeup of these materials help in ensuring a good level of thermal conductivity.
- This substrate offers low density and excellent gliding properties.
- The package size of this substrate is very small, hence, it is integrated in multilayer applications.
- It is less expensive than other types of metal.
- The hermetic packages of alumina PCB allow 0% of water absorption.
- Also, this substrate is made of strong material which contributes to its durability.
Types of Alumina PCB Substrate
Alumina substrate PCB is available in three different types.
96% Alumina PCB
The96% alumina substrate is a popular board majorly used in developing hybrid microelectronic circuits. The majority of microelectronic applications need alumina PCB due to its availability and high technical quality.
99.5% alumina substrate
This is another type of alumina substrate. 99.5% alumina substrate PCB is a great option for smaller size applications. Engineers usually prefer to use this material for non-critical applications. Furthermore, the flexural strength, dielectric constant, and thermal conductivity of this substrate is lower compared to other alumina substrates. You can find this substrate in more improved thickness and larger sizes.
99.6% alumina substrate
This Substrate has a standardized thin-film which makes it a popular option among PCB manufacturers. With a high level of purity and a smaller grain size, this substrate offers a smooth surface and less defects. Therefore, it is recommended for use in evaporated and sputtered deposited metals.
The 99.6% alumina substrate PCB has low thermal conductivity, excellent mechanical performance, and exceptional electrical insulation. Other properties of this substrate include good dielectric constant and wear-resistant.
Characteristics of Alumina PCB
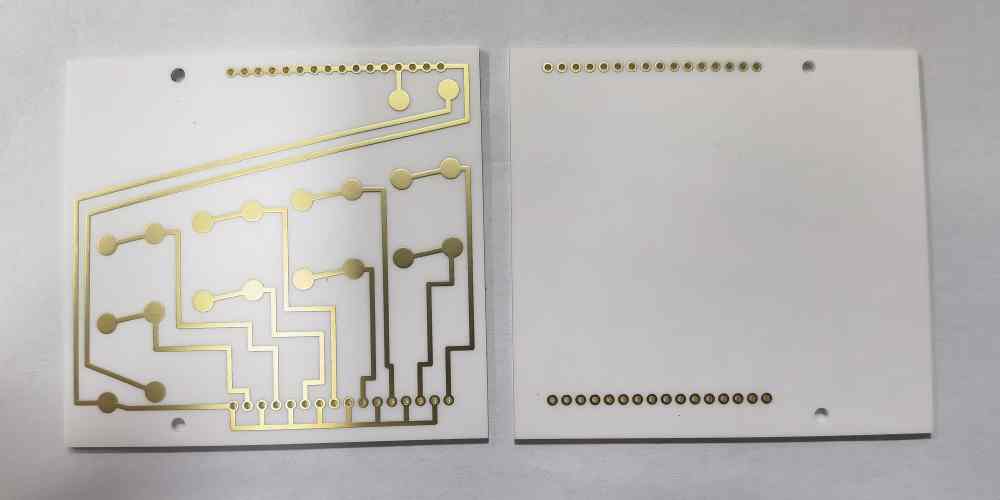
Alumina substrate PCB has a high purity. This material features isomorphic crystals and uses a-AI2O3. Since there are different types of alumina substrates, they differ in terms of their characteristics. Substrates with higher purity appear denser and have a smoother surface. Also, these substrates are more expensive. Some PCB manufacturers strike a balance between cost and quality. In order to maintain high quality while producing affordable substrates, the 96% alumina substrates are a better choice for producing alumina boards.
The thermal conductivity of this substrate is between 15W/mK to 50W/mK and as such, it helps with thermal management in electronic devices. When IC produces a high amount of heat, this heat quickly transfers to the alumina board. This board doesn’t usually require an insulating layer since it offers an excellent thermal dissipation.
High thermal resistance is a great characteristic manufacturers always look out for in PCBs. The melting point of 99% alumina is 1600 degrees Celsius while that of 96% is 1400 degrees Celsius.
In some cases, the overall maximum using temperature of the board reduces if it is multilayer and polypropylene is used in linking the two alumina layers. This happens due to the low melting temperature of polypropylene. The thermal resistance of the board won’t be affected if a high temperature sintering lamination method is adopted. In such scenarios, the two ceramic layers will bond well. Irrespective of the manufacturing process or lamination method adopted, an alumina board can function well at 300°C.
Alumina is a safe material unlike other ceramic boards that have beryllium oxide (BeO) and aluminum nitride. The thermal conductivity of BeO is higher compared to alumina, however, it is harmful. On the other hand, alumina features a high level of biocompatibility which ensures safety.
Applications of Alumina PCB
The alumina oxide is a popular material used for producing ceramic PCB substrates. It is ideal for designing prototypes and creating samples due to its cost effectiveness and low volume. Some applications find alumina boards very useful as it has accelerated and upgraded their level of production.
Also, these boards are of great use in high-performance applications since they have outstanding mechanical and thermal properties. For instance, alumina PCB substrates are an ideal choice for industrial devices, electronic equipment used in the military, and a wide range of automotive parts and components.
You will find alumina boards in:
- Solar cell
- Telecommunication devices like receiving systems and lasers.
- Street lights
- High power semiconductor electronic module like electric heaters
- LED lighting products and LED chip
- Smart power modules like solid-state relays
- Transmitter modules
- Braking system
- Resistor card
- Injection system
- Automotive parts like shock absorbers, sensors, and engine
Alumina PCB Thermal Conductivity
One of the key reasons alumina boards gained wide popularity in the electronic industries is their thermal management capabilities. The thermal conductivity of this board contributes to its exceptional thermal performance. Therefore, the PCB industry keeps banking on the use of alumina for circuit board manufacturing.
This material has much better properties compared to traditional materials. Also, it features better CTE and hermetic sealing, which adds to the performance of this material.
The increased thermal conductivity of ceramic boards is a big advantage over other boards. Alumina boards have a thermal conductivity from 20-30 W/mK. Other ceramic boards like aluminum oxide and aluminum nitride also have a good level of thermal conductivity. The thermal conductivity of these boards falls within the range of 18 and 36 W/mK.
Conclusion
Alumina substrate PCBs are one of the many great options for producing electronic devices. These boards are greatly utilized in a wide range of applications due to the several properties they feature. Due to their benefits and properties, they have become a popular choice for producing a wide range of electronic devices.
Leave a Reply