Introduction to Polygon pours in Altium Designer
Polygon pours are a powerful feature in Altium Designer that allow you to fill large areas of your PCB with copper. They are commonly used for power and ground planes, shielding, and creating custom copper shapes. However, when working with Rigid-Flex Designs, polygon pours can sometimes break along the split lines between the rigid and flexible sections of the board. In this article, we will explore the causes of this issue and provide solutions to ensure proper polygon pour behavior in your rigid-flex designs.
Understanding Rigid-Flex PCB Design
What is a Rigid-Flex PCB?
A rigid-flex PCB is a type of printed circuit board that combines both rigid and flexible substrates in a single design. The rigid sections provide structural support and house the majority of the components, while the flexible sections allow the board to bend or fold, enabling unique form factors and improved packaging density.
Advantages of Rigid-Flex PCBs
- Space Savings: Rigid-flex PCBs can be folded or bent to fit into tight spaces, reducing the overall size of the device.
- Reduced Weight: By eliminating the need for connectors and cables between rigid sections, rigid-flex PCBs can significantly reduce the weight of the assembly.
- Improved Reliability: With fewer interconnects and a more integrated design, rigid-flex PCBs offer higher reliability compared to traditional multi-board solutions.
- Enhanced Signal Integrity: The continuous copper traces in rigid-flex PCBs minimize signal reflections and impedance discontinuities, resulting in better signal integrity.
Polygon Pour Challenges in Rigid-Flex Designs
Split Lines and Copper Continuity
In a rigid-flex PCB, the transition between the rigid and flexible sections is defined by split lines. These lines indicate where the board will be separated during the manufacturing process to allow for flexibility. However, split lines can also cause issues with polygon pours, as the copper may not properly flow across the boundary.
Factors Affecting Polygon Pour Continuity
Several factors can contribute to polygon pour breaks along split lines:
- Split Line Geometry: The shape and placement of the split lines can impact the polygon pour behavior. Sharp angles or narrow regions near the split lines may cause the pour to break.
- Clearance Settings: Inadequate clearance settings between the polygon pour and the split lines can result in copper discontinuity.
- Manufacturing Constraints: The capabilities and limitations of the PCB Manufacturer can also influence the polygon pour continuity. Some manufacturers may require additional spacing or have specific requirements for copper flow across split lines.
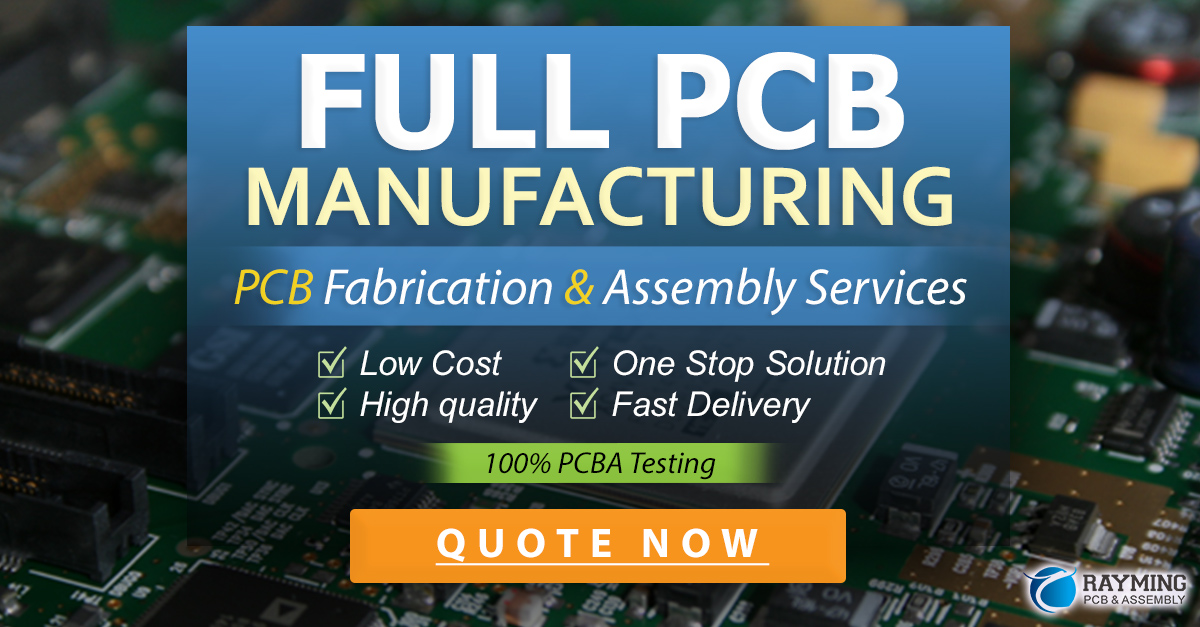
Best Practices for Polygon Pours in Rigid-Flex Designs
Designing Split Lines for Optimal Copper Flow
To minimize polygon pour breaks, consider the following guidelines when designing split lines:
- Use smooth, gradual transitions between the rigid and flexible sections. Avoid sharp angles or abrupt changes in the split line geometry.
- Provide adequate spacing between the split lines and other design elements, such as components, traces, and vias.
- If possible, orient the split lines perpendicular to the direction of the polygon pour. This can help maintain copper continuity across the boundary.
Adjusting Clearance Settings
Ensure that the clearance settings for your polygon pours are appropriate for your rigid-flex design:
- Set the clearance between the polygon pour and the split lines to a value that allows for proper copper flow. This may require collaboration with your PCB manufacturer to determine the optimal clearance based on their capabilities.
- Consider using the “Remove Dead Copper” option in Altium Designer to eliminate isolated copper areas that may occur near the split lines.
Collaborating with Your PCB Manufacturer
Effective communication with your PCB manufacturer is crucial for successful rigid-flex designs:
- Discuss your design intent and requirements with the manufacturer early in the design process. They can provide valuable insights and recommendations based on their experience and capabilities.
- Provide clear and detailed documentation, including the location and geometry of the split lines, to ensure accurate manufacturing.
- Request a design review or feedback from the manufacturer to identify any potential issues or improvements related to polygon pours and split lines.
Troubleshooting Polygon Pour Breaks
Identifying Polygon Pour Issues
If you encounter polygon pour breaks in your rigid-flex design, follow these steps to identify the problem:
- Visually inspect the polygon pour in Altium Designer. Look for gaps or discontinuities along the split lines.
- Use the “3D View” feature in Altium Designer to examine the polygon pour from different angles and identify any areas of concern.
- Generate Gerber files and review them in a Gerber viewer to ensure the polygon pour is consistent with your design intent.
Resolving Polygon Pour Breaks
Once you have identified the polygon pour breaks, consider the following solutions:
- Adjust the split line geometry: Modify the shape or placement of the split lines to improve copper flow. Smooth out sharp angles and ensure adequate spacing from other design elements.
- Modify clearance settings: Increase the clearance between the polygon pour and the split lines to allow for better copper continuity. Consult with your PCB manufacturer to determine the appropriate clearance value.
- Add copper thieving: Copper thieving involves adding small copper dots or shapes near the split lines to promote even Copper Distribution during the plating process. This technique can help minimize polygon pour breaks.
- Use solid copper connections: In some cases, it may be necessary to use solid copper connections, such as traces or copper pours, to bridge the gap between the rigid and flexible sections. This ensures a continuous electrical connection across the split lines.
Conclusion
Polygon pour breaks along split lines in rigid-flex designs can be a challenging issue, but with proper design techniques and collaboration with your PCB manufacturer, you can minimize their occurrence. By following best practices for split line design, adjusting clearance settings, and using appropriate troubleshooting methods, you can ensure reliable and continuous polygon pours in your rigid-flex PCBs.
Frequently Asked Questions (FAQ)
-
Q: What is the purpose of a polygon pour in PCB Design?
A: Polygon pours are used to fill large areas of a PCB with copper, typically for power and ground planes, shielding, or creating custom copper shapes. They help ensure proper electrical connectivity and provide a low-impedance path for current flow. -
Q: Why do polygon pours break along split lines in rigid-flex designs?
A: Polygon pours can break along split lines due to various factors, such as the geometry of the split lines, inadequate clearance settings, or manufacturing constraints. The transition between the rigid and flexible sections can disrupt the copper flow, causing discontinuities in the polygon pour. -
Q: How can I prevent polygon pour breaks in my rigid-flex design?
A: To prevent polygon pour breaks, design smooth and gradual split lines, provide adequate spacing between the split lines and other design elements, and adjust clearance settings to allow for proper copper flow. Collaborate with your PCB manufacturer to ensure your design meets their capabilities and requirements. -
Q: What should I do if I encounter polygon pour breaks in my rigid-flex PCB?
A: If you encounter polygon pour breaks, visually inspect the design in Altium Designer, use the 3D view to examine the pour from different angles, and review the Gerber files. To resolve the breaks, adjust the split line geometry, modify clearance settings, add copper thieving, or use solid copper connections to bridge the gap between the rigid and flexible sections. -
Q: How can my PCB manufacturer help with polygon pour issues in rigid-flex designs?
A: Your PCB manufacturer can provide valuable insights and recommendations based on their experience and capabilities. They can review your design, suggest appropriate clearance settings, and offer guidance on split line placement and geometry to minimize polygon pour breaks. Early collaboration with your manufacturer is key to successful rigid-flex designs.
Rigid-Flex PCB Design Considerations | Description |
---|---|
Split Line Geometry | Design smooth, gradual transitions between rigid and flexible sections. Avoid sharp angles or abrupt changes. |
Clearance Settings | Set appropriate clearance between polygon pours and split lines to allow for proper copper flow. |
Manufacturing Constraints | Collaborate with the PCB manufacturer to understand their capabilities and limitations regarding polygon pours and split lines. |
Copper Thieving | Add small copper dots or shapes near split lines to promote even copper distribution during plating. |
Solid Copper Connections | Use traces or copper pours to bridge the gap between rigid and flexible sections, ensuring continuous electrical connectivity. |
By understanding the challenges of polygon pours in rigid-flex designs and implementing best practices, you can create reliable and high-quality PCBs that meet your design requirements. Altium Designer provides the tools and features necessary to address polygon pour breaks and ensure optimal performance in your rigid-flex designs.
Leave a Reply