Introduction to Electrostatic Powder Spray
Electrostatic powder spray is a coating process that uses electrically charged particles to create a uniform and durable finish on various surfaces. This technology has gained popularity in recent years due to its numerous benefits, including improved efficiency, reduced waste, and enhanced coating quality. In this article, we will explore the advantages and disadvantages of electrostatic powder spray, providing a comprehensive overview of this innovative coating method.
How Does Electrostatic Powder Spray Work?
The Electrostatic Powder Spray Process
The electrostatic powder spray process involves the following steps:
- Powder preparation: The coating powder is mixed and loaded into the spray gun’s hopper.
- Electrostatic charging: The spray gun applies a high-voltage electrostatic charge to the powder particles as they exit the nozzle.
- Powder application: The charged powder particles are attracted to the grounded workpiece, creating a uniform coating on the surface.
- Curing: The coated workpiece is then heated in an oven, allowing the powder to melt, flow, and form a smooth, durable finish.
Components of an Electrostatic Powder Spray System
A typical electrostatic powder spray system consists of the following components:
- Powder spray gun
- Powder feed hopper
- High-voltage power supply
- Compressed air source
- Powder recovery system
- Curing oven
Advantages of Electrostatic Powder Spray
1. Improved Coating Efficiency
One of the primary advantages of electrostatic powder spray is its high coating efficiency. The electrostatic charge ensures that the powder particles are attracted to the workpiece, resulting in minimal overspray and waste. This efficiency can lead to significant cost savings in terms of material usage and disposal.
2. Enhanced Coating Uniformity
The electrostatic attraction between the charged powder particles and the grounded workpiece ensures a uniform coating thickness across the entire surface. This uniformity is essential for achieving consistent appearance and performance of the coated product.
3. Durability and Corrosion Resistance
Powder coatings applied through electrostatic spray offer excellent durability and corrosion resistance. The cured coating forms a tough, protective barrier that can withstand exposure to various environmental factors, such as UV radiation, moisture, and chemicals. This durability translates to longer-lasting products and reduced maintenance costs.
4. Environmentally Friendly
Electrostatic powder spray is an environmentally friendly coating process. Unlike liquid paints, powder coatings contain no solvents or volatile organic compounds (VOCs), which can be harmful to the environment and human health. Additionally, the high transfer efficiency of electrostatic spray means less waste and reduced energy consumption during the curing process.
5. Wide Range of Finishes and Colors
Powder coatings used in electrostatic spray come in a vast array of finishes and colors, providing designers and manufacturers with ample options to achieve the desired aesthetic. From glossy to matte, smooth to textured, and solid colors to metallics, electrostatic powder spray can accommodate various design requirements.
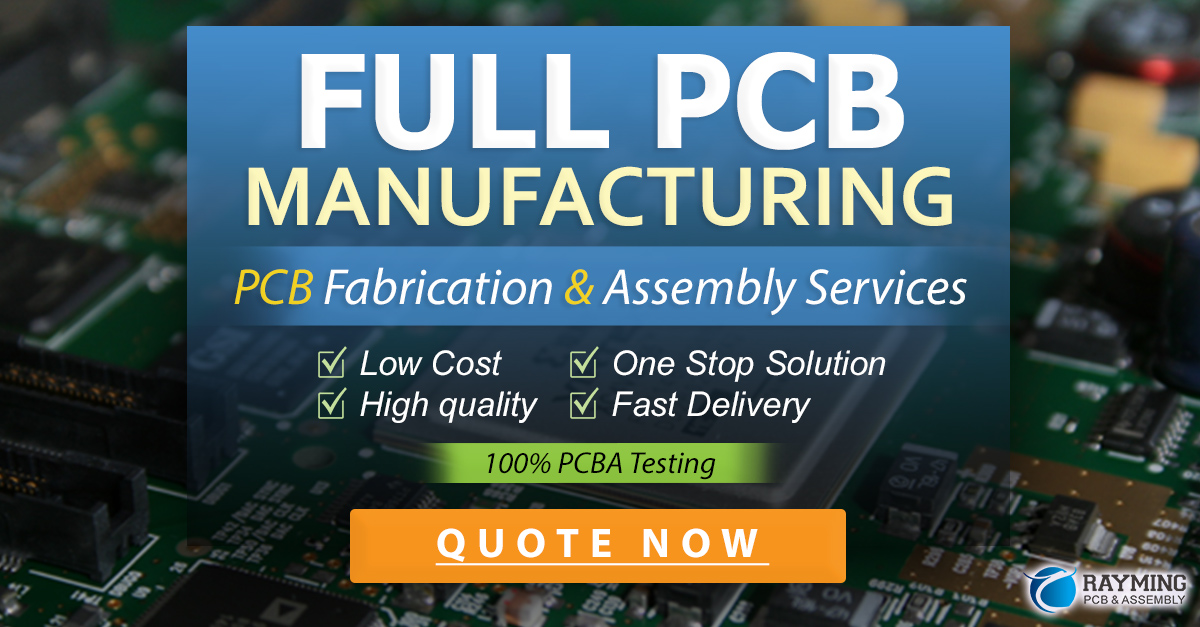
Disadvantages of Electrostatic Powder Spray
1. Initial Investment Costs
Setting up an electrostatic powder spray system requires a significant initial investment. The equipment, including the spray gun, power supply, and curing oven, can be costly compared to traditional liquid painting methods. However, the long-term cost savings from improved efficiency and reduced waste often outweigh the initial investment.
2. Limited Substrate Compatibility
Electrostatic powder spray is primarily suitable for conductive substrates, such as metals. Non-conductive materials, like plastics and wood, may require special pretreatment or the use of conductive primers to ensure proper adhesion of the powder coating. This limitation can restrict the range of applications for electrostatic powder spray.
3. Difficulty in Achieving Thin Coatings
Achieving very thin coatings with electrostatic powder spray can be challenging. The powder particles have a minimum thickness that can be applied, which may not be suitable for applications requiring ultra-thin coatings. In such cases, liquid painting methods may be more appropriate.
4. Powder Recovery and Color Change Challenges
Powder recovery systems are essential for minimizing waste and ensuring cost-effectiveness. However, these systems can be complex and require regular maintenance. Additionally, changing colors in an electrostatic powder spray system can be time-consuming, as the equipment needs to be thoroughly cleaned to prevent cross-contamination between different powder colors.
Applications of Electrostatic Powder Spray
Electrostatic powder spray finds applications in various industries, including:
- Automotive: Body panels, wheels, and engine components
- Appliances: Refrigerators, washing machines, and kitchen appliances
- Furniture: Office furniture, outdoor furniture, and shelving systems
- Architecture: Window frames, doors, and façade elements
- Agricultural equipment: Tractors, harvesters, and irrigation systems
Industry | Applications |
---|---|
Automotive | Body panels, wheels, engine components |
Appliances | Refrigerators, washing machines, kitchen appliances |
Furniture | Office furniture, outdoor furniture, shelving systems |
Architecture | Window frames, doors, façade elements |
Agricultural | Tractors, harvesters, irrigation systems |
Frequently Asked Questions (FAQ)
1. Is electrostatic powder spray suitable for coating plastic parts?
Coating plastic parts with electrostatic powder spray can be challenging, as most plastics are non-conductive. However, special pretreatment methods, such as plasma treatment or the use of conductive primers, can be employed to enable the successful application of powder coatings on plastic surfaces.
2. How does the durability of electrostatic powder coatings compare to liquid paint?
Electrostatic powder coatings generally offer superior durability compared to liquid paint. The cured powder coating forms a strong, cross-linked polymer structure that provides excellent resistance to chipping, scratching, fading, and corrosion. This durability translates to longer-lasting protection and reduced maintenance requirements.
3. Can electrostatic powder spray be used for intricate or complex-shaped parts?
Yes, electrostatic powder spray can be used for coating intricate or complex-shaped parts. The electrostatic attraction between the charged powder particles and the grounded workpiece ensures that the powder adheres even to hard-to-reach areas, providing uniform coverage. However, for very deep recesses or cavities, additional manual touch-up may be required.
4. Are there any health and safety concerns associated with electrostatic powder spray?
When using electrostatic powder spray, it is essential to follow proper health and safety guidelines. Powder coatings can create dust that, if inhaled, may cause respiratory irritation. Operators should wear appropriate personal protective equipment (PPE), such as dust masks and protective eyewear. Additionally, the high-voltage equipment used in the process requires proper grounding and safety measures to prevent electrical hazards.
5. How does the cost of electrostatic powder spray compare to traditional liquid painting?
While the initial investment in electrostatic powder spray equipment can be higher than traditional liquid painting, the long-term cost benefits are significant. The high transfer efficiency of electrostatic spray results in reduced material waste, lower energy consumption during curing, and minimal VOC emissions. These factors, combined with the superior durability of powder coatings, often make electrostatic powder spray a more cost-effective choice in the long run.
Conclusion
Electrostatic powder spray is a versatile and efficient coating process that offers numerous advantages over traditional liquid painting methods. With its improved coating efficiency, enhanced uniformity, and excellent durability, electrostatic powder spray has become a popular choice for various industries. Although there are some limitations and initial investment costs to consider, the long-term benefits of this technology often outweigh the drawbacks.
As industries continue to prioritize sustainability and cost-effectiveness, the adoption of electrostatic powder spray is likely to grow. By understanding the advantages and disadvantages of this coating process, manufacturers can make informed decisions and harness the potential of electrostatic powder spray to improve their products and processes.
Leave a Reply