What is Trace Width?
Trace width refers to the width of the conductive paths, or traces, on a PCB. These traces are responsible for carrying electrical signals between components on the board. The width of a trace is typically measured in mils (thousandths of an inch) or microns (micrometers).
Factors Affecting Trace Width
Several factors influence the choice of trace width in PCB design:
-
Current Carrying Capacity: The amount of current a trace can carry without overheating depends on its width. Wider traces can handle higher currents, while narrower traces are suitable for lower currents.
-
Signal Integrity: Trace width plays a role in maintaining signal integrity. High-speed signals require specific trace widths to minimize signal reflections and maintain proper impedance matching.
-
Manufacturing Constraints: The minimum trace width achievable depends on the manufacturing capabilities of the PCB fabrication facility. Advanced manufacturing processes allow for narrower traces, while standard processes have limitations.
-
PCB Size and Density: The available space on a PCB and the desired component density influence trace width. Smaller PCBs and high-density designs often require narrower traces to accommodate all the necessary connections.
Trace Width Calculation
To determine the appropriate trace width for a given current and temperature rise, designers can use trace width calculators or refer to industry standards. The IPC-2221 standard provides guidelines for trace width sizing based on factors such as copper thickness, temperature rise, and current requirements.
Here’s an example table showing the relationship between trace width, copper thickness, and current carrying capacity:
Trace Width (mils) | Copper Thickness (oz) | Current Capacity (A) |
---|---|---|
10 | 1 | 0.5 |
20 | 1 | 1.0 |
30 | 1 | 1.5 |
40 | 1 | 2.0 |
Note: The values in this table are for illustrative purposes only and may vary based on specific design requirements and environmental conditions.
What is Trace Tolerance?
Trace tolerance refers to the acceptable variation in the width of a trace during the manufacturing process. It is the difference between the designed trace width and the actual trace width on the fabricated PCB.
Factors Affecting Trace Tolerance
Several factors can impact trace tolerance:
-
Manufacturing Process: Different PCB manufacturing processes have varying levels of precision and accuracy. Advanced processes, such as high-density interconnect (HDI) PCBs, offer tighter tolerances compared to standard processes.
-
Copper Thickness: The thickness of the copper layer on the PCB affects trace tolerance. Thicker copper allows for better control over trace width and reduces the impact of etching variations.
-
Etching Process: The etching process used to remove unwanted copper from the PCB can introduce variations in trace width. Factors such as etchant concentration, temperature, and etching time can affect trace tolerance.
-
Artwork Quality: The quality of the artwork files used for PCB fabrication plays a role in trace tolerance. High-resolution artwork with clear and accurate trace definitions helps minimize variations during manufacturing.
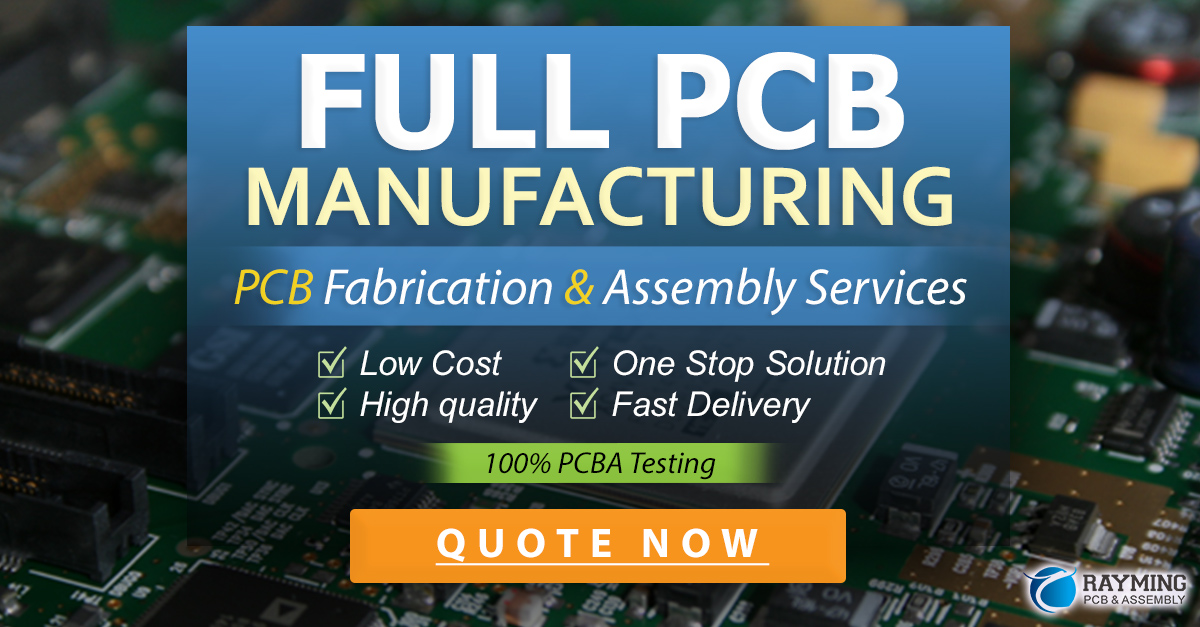
Trace Tolerance Standards
Industry standards, such as IPC-6012, provide guidelines for acceptable trace tolerances based on the specific class of PCBs. Here’s a table showing the trace tolerance requirements for different PCB classes:
PCB Class | Trace Tolerance |
---|---|
Class 1 | ± 20% |
Class 2 | ± 10% |
Class 3 | ± 5% |
Note: These values are based on the IPC-6012 standard and may vary depending on the specific standard or manufacturer.
Best Practices for Trace Width and Tolerance
To ensure optimal PCB performance and manufacturability, consider the following best practices:
-
Follow Industry Standards: Adhere to industry standards and guidelines, such as IPC-2221 and IPC-6012, when designing trace widths and specifying tolerances.
-
Consider Current Requirements: Select trace widths based on the expected current carrying requirements of each net. Use trace width calculators or consult with the PCB manufacturer for guidance.
-
Account for Manufacturing Capabilities: Understand the manufacturing capabilities of the chosen PCB fabrication facility and design trace widths and tolerances accordingly.
-
Use Appropriate Copper Thickness: Choose an appropriate copper thickness for the desired trace width and tolerance. Thicker copper allows for better control and reduces the impact of etching variations.
-
Provide Clear Artwork: Ensure that the artwork files provided to the PCB manufacturer are of high quality, with clear and accurate trace definitions to minimize variations during fabrication.
-
Collaborate with PCB Manufacturers: Work closely with PCB manufacturers to understand their capabilities, limitations, and recommendations for trace width and tolerance. Their expertise can help optimize the design for manufacturability.
Frequently Asked Questions (FAQ)
-
What happens if the trace width is too narrow?
If a trace width is too narrow, it may not be able to carry the required current without overheating. This can lead to signal integrity issues, voltage drops, and potential reliability problems. -
Can I use different trace widths on the same PCB?
Yes, it is common to use different trace widths on the same PCB depending on the current requirements and signal integrity needs of each net. However, it’s important to consider the manufacturing capabilities and ensure that the chosen trace widths are achievable. -
How does the PCB material affect trace width and tolerance?
The choice of PCB material can impact trace width and tolerance. Some high-frequency materials have specific dielectric properties that require adjustments to trace widths to maintain proper impedance. Additionally, the thermal characteristics of the material can influence the current carrying capacity of traces. -
What is the minimum trace width achievable?
The minimum trace width achievable depends on the manufacturing capabilities of the PCB fabrication facility. Advanced processes, such as HDI PCBs, can achieve trace widths as narrow as 2-3 mils (50-75 microns). However, for standard PCB processes, the minimum trace width is typically around 5-6 mils (125-150 microns). -
How can I ensure that my PCB meets the specified trace tolerances?
To ensure that your PCB meets the specified trace tolerances, follow industry standards, provide clear and accurate artwork files, and collaborate closely with your PCB manufacturer. Discuss your requirements and tolerances with the manufacturer and seek their guidance on design and manufacturability aspects.
Conclusion
Trace width and tolerance are critical aspects of PCB design that directly impact the performance, reliability, and manufacturability of electronic devices. By understanding the factors that influence trace width and tolerance, adhering to industry standards, and following best practices, designers can create PCBs that meet the desired specifications and ensure optimal functionality.
When designing PCBs, it’s essential to consider current requirements, signal integrity needs, manufacturing capabilities, and the specific standards and guidelines relevant to the project. Collaborating closely with PCB manufacturers and leveraging their expertise can help streamline the design process and achieve the best possible results.
By carefully selecting trace widths, specifying appropriate tolerances, and working with reliable manufacturing partners, designers can create high-quality PCBs that power the electronic devices we rely on every day.
Leave a Reply