Introduction to Automotive PCBs
Automotive printed circuit boards (PCBs) are essential components in modern vehicles, controlling and connecting various electrical systems. As vehicles become more advanced and reliant on electronics, the demand for high-quality, reliable automotive PCBs continues to rise. Designing PCBs for automotive applications presents unique challenges due to the harsh environmental conditions and strict safety requirements.
This guide aims to provide a comprehensive overview of automotive PCB design best practices, addressing key aspects such as material selection, layout considerations, testing, and compliance with industry standards. By following these guidelines, designers can create robust and reliable PCBs that meet the demanding requirements of the automotive industry.
Challenges in Automotive PCB Design
Designing PCBs for automotive applications comes with several challenges that must be addressed to ensure optimal performance and reliability:
-
Harsh environmental conditions: Automotive PCBs are exposed to extreme temperatures, vibrations, and moisture, which can cause component failure and reduce the overall lifespan of the board.
-
Electromagnetic interference (EMI): With numerous electronic systems in close proximity, automotive PCBs must be designed to minimize EMI and ensure proper functioning of all components.
-
Limited space: As vehicles become more compact and feature-rich, PCB designers must work within tight space constraints while maintaining optimal performance.
-
Safety and reliability: Automotive PCBs play a critical role in vehicle safety systems, necessitating stringent design and testing practices to ensure reliable operation under all conditions.
Material Selection for Automotive PCBs
Choosing the right materials for automotive PCBs is crucial for ensuring reliable performance in harsh environments. Key considerations include:
PCB Substrate Materials
Material | Advantages | Disadvantages |
---|---|---|
FR-4 | Low cost, widely available | Limited temperature range, moisture absorption |
High Tg FR-4 | Improved thermal stability | Higher cost compared to standard FR-4 |
Polyimide | Excellent thermal stability, low moisture absorption | High cost, challenging to process |
Ceramic | High thermal conductivity, low CTE | Brittle, expensive |
Copper Thickness and Trace Width
Selecting the appropriate copper thickness and trace width is essential for ensuring adequate current carrying capacity and minimizing voltage drop. The following table provides general guidelines:
Current (A) | Trace Width (mm) | Copper Thickness (oz) |
---|---|---|
0.5 | 0.2 | 0.5 |
1.0 | 0.3 | 0.7 |
2.0 | 0.5 | 1.0 |
5.0 | 1.0 | 2.0 |
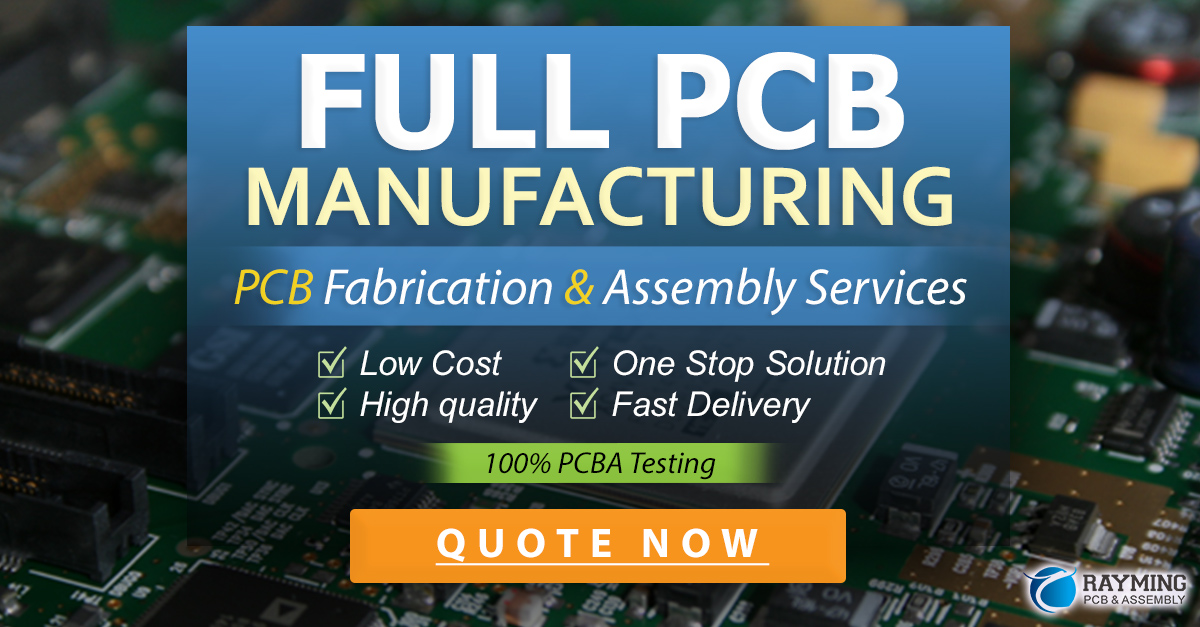
Layout Considerations for Automotive PCBs
Proper PCB layout is critical for ensuring optimal performance and reliability in automotive applications. Key considerations include:
Component Placement
- Place temperature-sensitive components away from heat sources
- Group components with similar functions together
- Minimize the distance between related components to reduce trace lengths
Trace Routing
- Use 45° angles instead of 90° angles to minimize reflections and improve signal integrity
- Provide adequate clearance between traces to prevent short circuits
- Use ground planes to minimize EMI and improve signal quality
Thermal Management
- Incorporate thermal relief pads for components with high power dissipation
- Use thermal vias to transfer heat from components to the opposite side of the board
- Consider using metal-core PCBs (MCPCBs) for improved thermal performance
EMI Reduction Techniques
Minimizing EMI is crucial for ensuring the proper functioning of automotive electronic systems. Some effective techniques include:
-
Proper grounding: Implement a solid ground plane and use multiple ground connections to minimize ground loops and reduce EMI.
-
Shielding: Utilize shielding materials, such as conductive coatings or metal enclosures, to protect sensitive components from external EMI sources.
-
Filtering: Incorporate low-pass, high-pass, or band-pass filters to attenuate unwanted frequencies and reduce EMI.
-
Decoupling capacitors: Place decoupling capacitors close to power pins of ICs to minimize high-frequency noise and prevent EMI propagation.
Testing and Validation
Rigorous testing and validation are essential for ensuring the reliability and safety of automotive PCBs. Key aspects include:
Environmental Testing
- Temperature cycling: Expose PCBs to alternating high and low temperatures to assess their ability to withstand thermal stress.
- Vibration testing: Subject PCBs to vibrations at various frequencies and amplitudes to ensure they can withstand the harsh automotive environment.
- Humidity testing: Expose PCBs to high humidity levels to evaluate their resistance to moisture ingress.
Functional Testing
- In-circuit testing (ICT): Verify the proper assembly and functionality of individual components on the PCB.
- Boundary scan testing: Utilize JTAG (Joint Test Action Group) interfaces to test interconnects and functionality of digital components.
- Functional testing: Perform system-level tests to ensure the PCB meets the required specifications and functions as intended.
Compliance with Automotive Standards
Automotive PCBs must comply with various industry standards to ensure safety, reliability, and compatibility. Some key standards include:
-
ISO 26262: This standard provides guidelines for functional safety in automotive electrical and electronic systems, covering aspects such as risk assessment, design, and validation.
-
AEC-Q100: The Automotive Electronics Council (AEC) defines qualification requirements for integrated circuits used in automotive applications, ensuring their reliability and robustness.
-
IATF 16949: This standard specifies quality management system requirements for automotive production and relevant service parts organizations, focusing on continuous improvement and defect prevention.
-
J-STD-020: The IPC J-STD-020 standard provides guidelines for moisture/reflow sensitivity classification for non-hermetic surface mount devices, ensuring proper handling and assembly of components.
FAQ
Q1: What are the main differences between automotive PCBs and standard PCBs?
A1: Automotive PCBs are designed to withstand harsher environmental conditions, such as extreme temperatures, vibrations, and moisture. They also have stricter requirements for reliability, safety, and EMI reduction compared to standard PCBs.
Q2: How can I ensure my automotive PCB design meets the necessary industry standards?
A2: To ensure compliance with industry standards, familiarize yourself with the relevant standards (e.g., ISO 26262, AEC-Q100, IATF 16949) and consult with experienced automotive PCB designers. Perform thorough testing and validation to verify that your design meets the required specifications.
Q3: What are some effective methods for reducing EMI in automotive PCBs?
A3: Some effective methods for reducing EMI in automotive PCBs include proper grounding, shielding sensitive components, incorporating filtering techniques, and using decoupling capacitors near power pins of ICs.
Q4: How do I select the right materials for my automotive PCB?
A4: When selecting materials for your automotive PCB, consider factors such as the expected operating temperature range, moisture resistance, and cost. High Tg FR-4, polyimide, and ceramic substrates are common choices for automotive applications due to their improved thermal stability and low moisture absorption.
Q5: What are the key layout considerations for automotive PCBs?
A5: Key layout considerations for automotive PCBs include proper component placement (e.g., grouping similar functions, minimizing distances), trace routing (e.g., using 45° angles, providing adequate clearances), and thermal management (e.g., using thermal relief pads, metal-core PCBs). Following best practices in these areas can help ensure optimal performance and reliability.
Conclusion
Designing automotive PCBs requires careful consideration of the unique challenges and requirements posed by the automotive industry. By selecting the right materials, implementing proper layout techniques, and adhering to industry standards, designers can create robust and reliable PCBs that meet the demanding needs of modern vehicles.
This comprehensive guide has covered key aspects of automotive PCB design, including material selection, layout considerations, EMI reduction, testing, and compliance with industry standards. By following these guidelines and best practices, designers can minimize the risk of component failure, ensure optimal performance, and contribute to the development of safer, more advanced automotive electronic systems.
Leave a Reply