What is PCB Milling?
PCB milling is a process used in the fabrication of printed circuit boards (PCBs) where a computer-controlled machine, known as a PCB milling machine or a PCB router, is used to remove unwanted copper from a copper-clad substrate. This process is also referred to as PCB routing or PCB Etching. PCB milling is an alternative to the more traditional method of PCB fabrication, which involves using chemicals to etch away the unwanted copper.
Advantages of PCB Milling
PCB milling offers several advantages over traditional PCB fabrication methods:
-
Faster turnaround times: PCB milling can produce PCBs much faster than traditional etching methods, as it does not require the use of chemicals and the associated processing time.
-
Cost-effective for small batches: For small-scale production or prototyping, PCB milling is more cost-effective than traditional etching methods, as it does not require the creation of expensive masks or the use of chemicals.
-
Environmentally friendly: PCB milling is an environmentally friendly process, as it does not involve the use of harmful chemicals and produces less waste compared to traditional etching methods.
-
Increased design flexibility: PCB milling allows for greater design flexibility, as it can easily accommodate last-minute design changes without the need for new masks or additional setup time.
How Does PCB Milling Work?
PCB milling involves the following steps:
-
Design creation: The PCB design is created using computer-aided design (CAD) software, such as Eagle, KiCad, or Altium Designer.
-
G-code generation: The CAD design is then converted into a machine-readable format, typically G-code, which contains the instructions for the PCB milling machine to follow.
-
Machine setup: The copper-clad substrate is loaded into the PCB milling machine, and the appropriate milling tools are selected and installed.
-
Milling process: The PCB milling machine follows the G-code instructions, moving the milling tool along the surface of the substrate to remove the unwanted copper, leaving behind the desired circuit pattern.
-
Cleaning and inspection: Once the milling process is complete, the PCB is cleaned to remove any debris and inspected for quality control purposes.
Types of PCB Milling Machines
There are two main types of PCB milling machines:
-
Desktop PCB milling machines: These are small, compact machines designed for personal use or small-scale production. They are typically less expensive and offer a smaller working area compared to industrial machines. Examples include the Bantam Tools Desktop PCB Milling Machine and the Prometheus PCB Milling Machine.
-
Industrial PCB milling machines: These are larger, more robust machines designed for high-volume production and larger PCB sizes. They offer higher precision, speed, and automation compared to desktop machines. Examples include the LPKF ProtoMat S series and the Accurate A-Series CNC PCB Routers.
PCB Milling Tools and Materials
Milling Tools
PCB milling machines use various types of milling tools, depending on the specific requirements of the PCB design. The most common types of milling tools include:
-
End mills: Used for creating large, general-purpose cuts and traces.
-
Drill bits: Used for creating holes for through-hole components and vias.
-
V-shaped bits: Used for creating isolation channels and cutting out the PCB outline.
The milling tools are typically made from carbide or high-speed steel (HSS) and come in various sizes and shapes to accommodate different design requirements.
Copper-Clad Substrates
PCB milling machines work with copper-clad substrates, which consist of a non-conductive base material, such as FR-4 or Rogers, laminated with a thin layer of copper on one or both sides. The thickness of the copper layer can vary, with common thicknesses being 0.5 oz, 1 oz, and 2 oz copper per square foot.
When selecting a copper-clad substrate for PCB milling, consider factors such as:
-
Base material: Choose a base material that suits your application’s requirements, such as temperature stability, dielectric constant, and mechanical strength.
-
Copper thickness: Select a copper thickness that balances current-carrying capacity, trace width, and milling tool compatibility.
-
Substrate thickness: Choose a substrate thickness that provides the necessary mechanical stability and fits your application’s size constraints.
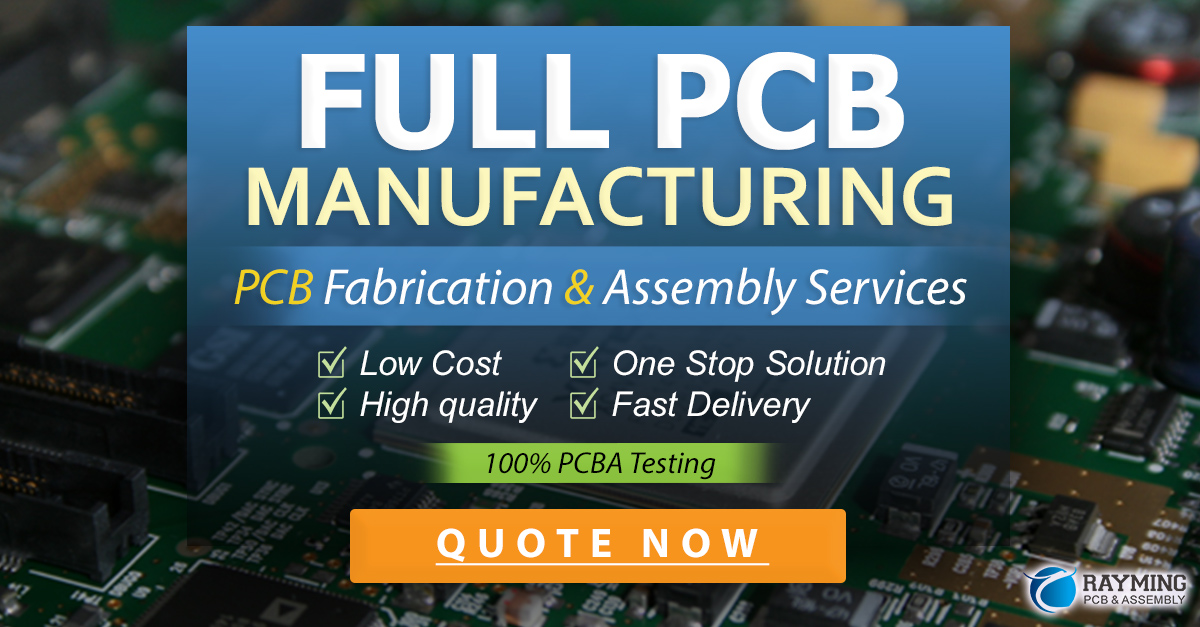
PCB Milling Design Considerations
When designing PCBs for milling, there are several key considerations to keep in mind:
-
Trace width and spacing: Ensure that your trace widths and spacing are compatible with the capabilities of your PCB milling machine and the milling tools you plan to use. Smaller trace widths and spacing require more precise machines and smaller milling tools.
-
Pad size and hole diameter: Select pad sizes and hole diameters that are appropriate for your components and the milling tools available. Larger pads and holes are easier to mill and provide more tolerance for alignment errors.
-
Copper pour and ground planes: When using copper pour or ground planes, ensure that there is sufficient clearance around traces and pads to avoid short circuits and milling tool breakage.
-
Design rule checking (DRC): Use the DRC features in your CAD software to check your design for potential issues, such as trace width violations, spacing violations, and unconnected traces.
PCB Milling Best Practices
To ensure the best results when milling PCBs, follow these best practices:
-
Use sharp, high-quality milling tools: Dull or low-quality milling tools can lead to poor-quality cuts, excessive burring, and tool breakage.
-
Properly secure the copper-clad substrate: Ensure that the substrate is securely fastened to the machine bed to prevent shifting during the milling process, which can lead to misalignment and inaccurate cuts.
-
Regularly clean and maintain your PCB milling machine: Keep your machine clean and well-maintained to ensure optimal performance and longevity.
-
Follow the manufacturer’s recommended settings: Use the recommended feed rates, spindle speeds, and depth of cut settings for your specific machine and milling tools to achieve the best results.
-
Double-check your design before milling: Carefully review your PCB design and G-code before starting the milling process to catch any potential errors or issues.
Troubleshooting Common PCB Milling Issues
Despite following best practices, you may encounter issues when milling PCBs. Some common problems and their solutions include:
-
Inaccurate or misaligned cuts: This can be caused by a loose or improperly secured substrate, worn or damaged milling tools, or incorrect machine settings. Double-check your setup and replace any worn or damaged components.
-
Excessive burring: Burring can occur when using dull milling tools or incorrect feed rates and spindle speeds. Use sharp, high-quality tools and adjust your machine settings as needed.
-
Broken milling tools: Milling tool breakage can be caused by excessive depth of cut, incorrect feed rates, or hitting obstacles on the substrate. Adjust your settings and ensure that your design has proper clearances around traces and pads.
-
Incomplete cuts or lifted traces: This can happen when the depth of cut is too shallow or the milling tool is worn. Increase the depth of cut incrementally and replace worn tools as needed.
Frequently Asked Questions (FAQ)
-
What is the difference between PCB milling and PCB etching?
PCB milling uses a computer-controlled machine to mechanically remove unwanted copper from a copper-clad substrate, while PCB etching uses chemicals to dissolve the unwanted copper. Milling is faster and more environmentally friendly, while etching can produce finer details and is better suited for high-volume production. -
Can I mill double-sided PCBs?
Yes, you can mill double-sided PCBs using a PCB milling machine. However, you will need to create alignment holes or fiducial marks to ensure that the two sides of the PCB are properly aligned when flipping the board over to mill the second side. -
What is the smallest trace width and spacing that can be achieved with PCB milling?
The minimum trace width and spacing achievable with PCB milling depend on the capabilities of your specific machine and the milling tools you are using. Generally, desktop PCB milling machines can achieve trace widths and spacing down to about 0.2 mm (8 mil), while industrial machines can produce even finer details. -
How do I choose the right milling tools for my PCB design?
When selecting milling tools, consider factors such as the trace widths and spacing in your design, the type of cuts you need to make (e.g., traces, holes, or isolation channels), and the material you are working with. Consult your machine’s documentation or the milling tool manufacturer’s recommendations for guidance. -
Can I mill PCBs with non-FR-4 substrates, such as aluminum or plastic?
Yes, PCB milling machines can work with a variety of substrates beyond traditional FR-4, including aluminum, brass, and certain plastics. However, you may need to adjust your machine settings and use specialized milling tools to accommodate these materials. Always consult your machine’s documentation and the substrate manufacturer’s guidelines for specific recommendations.
Conclusion
PCB milling is a versatile and efficient method for fabricating printed circuit boards, offering several advantages over traditional etching methods, such as faster turnaround times, cost-effectiveness for small batches, and environmental friendliness. By understanding the PCB milling process, selecting the right tools and materials, and following best practices and design considerations, you can produce high-quality PCBs for your projects and applications.
As you gain experience with PCB milling, continue to refine your techniques, experiment with new materials and tools, and stay up-to-date with the latest advancements in the field. With practice and perseverance, you can master the art of PCB milling and bring your electronic designs to life.
Leave a Reply