Introduction
Printed Circuit Board (PCB) manufacturing is a rapidly evolving industry driven by advancements in technology and changing market demands. Keeping up with the latest PCB Manufacturing Trends is essential for companies looking to stay competitive, reduce costs, and improve product quality. In this article, we will explore some of the key trends shaping the PCB manufacturing landscape and discuss how businesses can leverage these trends to save time and energy.
The Importance of Staying Current with PCB Manufacturing Trends
Staying current with PCB manufacturing trends offers several benefits:
- Improved Efficiency: Adopting new technologies and processes can streamline PCB production, reducing lead times and increasing output.
- Cost Savings: Implementing cost-effective materials and manufacturing techniques can help lower production costs without compromising quality.
- Enhanced Product Performance: Leveraging advanced PCB design and manufacturing capabilities enables the creation of high-performance products that meet evolving customer requirements.
- Competitive Advantage: Companies that stay ahead of the curve can differentiate themselves from competitors and capture new market opportunities.
Key PCB Manufacturing Trends
1. Miniaturization and High-Density Interconnect (HDI) PCBs
One of the most significant trends in PCB manufacturing is the increasing demand for miniaturized and high-density interconnect (HDI) PCBs. As electronic devices continue to shrink in size while offering more features and functionality, PCB designers must find ways to pack more components into smaller spaces. HDI PCBs achieve this by utilizing advanced manufacturing techniques, such as:
- Microvias: Tiny holes drilled through individual PCB layers to create interconnections between layers.
- Buried and blind vias: Vias that are hidden within the PCB stack or only visible on one side of the board.
- Fine-pitch components: Components with very small spacing between pins or pads.
By adopting HDI PCB manufacturing capabilities, companies can create more compact and powerful electronic devices while reducing material costs and improving signal integrity.
2. Flexible and Rigid-Flex PCBs
Another trend gaining traction in the PCB industry is the increased use of flexible and rigid-flex PCBs. These types of PCBs offer several advantages over traditional rigid PCBs:
- Space savings: Flexible PCBs can be bent, folded, or rolled to fit into tight spaces, making them ideal for wearable devices, smartphones, and other compact electronics.
- Improved reliability: Flexible PCBs can withstand repeated bending and flexing without breaking or losing connectivity, enhancing product durability.
- Reduced assembly costs: Rigid-flex PCBs combine rigid and flexible sections into a single board, eliminating the need for separate connectors and cables, thus simplifying assembly and reducing costs.
As the demand for smaller, more reliable, and cost-effective electronics grows, flexible and rigid-flex PCBs will likely become increasingly popular in various industries.
3. Additive Manufacturing and 3D Printing
Additive manufacturing, also known as 3D printing, is a relatively new technology that is beginning to make inroads in the PCB industry. Unlike traditional subtractive manufacturing methods, which involve removing material to create the desired shape, additive manufacturing builds objects layer by layer using materials such as polymers, metals, or ceramics.
In the context of PCB manufacturing, additive manufacturing offers several potential benefits:
- Rapid prototyping: 3D printing enables quick and cost-effective production of PCB prototypes, allowing designers to test and refine their designs before committing to full-scale production.
- Customization: Additive manufacturing allows for the creation of complex geometries and unique PCB shapes that may be difficult or impossible to achieve with traditional manufacturing methods.
- Reduced waste: Because additive manufacturing only uses the material necessary to build the PCB, it generates less waste compared to subtractive methods.
While additive manufacturing is still in its early stages for PCB production, it holds promise for creating innovative PCB designs and streamlining the prototyping process.
4. Advanced Materials
PCB manufacturers are continuously exploring new materials to improve the performance, reliability, and environmental sustainability of their products. Some of the advanced materials gaining attention in the industry include:
- Low-loss materials: These materials, such as modified polyimides and hydrocarbon ceramics, offer lower dielectric loss and higher thermal conductivity compared to traditional FR-4 laminates. Low-loss materials are particularly useful for high-frequency applications, such as 5G wireless networks and automotive radar systems.
- Halogen-free materials: As environmental regulations become more stringent, many PCB manufacturers are transitioning to halogen-free materials to reduce the use of hazardous substances in their products. Halogen-free PCBs are made using materials that do not contain brominated or chlorinated flame retardants, which can release toxic fumes when burned.
- Metal core PCBs: Metal core PCBs feature a metal substrate, typically aluminum, that provides excellent thermal conductivity and heat dissipation properties. These PCBs are well-suited for high-power applications, such as LED lighting and power electronics, where efficient heat management is critical.
By staying informed about the latest advancements in PCB materials, manufacturers can select the most appropriate options for their specific applications, ensuring optimal performance and compliance with environmental regulations.
5. Automation and Industry 4.0
The fourth industrial revolution, or Industry 4.0, is transforming the manufacturing sector, and the PCB industry is no exception. Automation and smart factory technologies are increasingly being adopted to improve efficiency, reduce costs, and enhance product quality. Some key areas where automation is making an impact in PCB manufacturing include:
- Automated optical inspection (AOI): AOI systems use high-resolution cameras and advanced image processing algorithms to detect defects and anomalies in PCBs, such as missing components, solder bridges, or incorrect component placement. By automating the inspection process, manufacturers can quickly identify and correct issues, reducing the risk of defective products reaching customers.
- Robotic assembly: Collaborative robots, or cobots, are being employed in PCB assembly lines to perform tasks such as component placement, soldering, and material handling. These robots can work alongside human operators, improving productivity and consistency while reducing the risk of errors and injuries.
- Data analytics and machine learning: Smart factories generate vast amounts of data from sensors, machines, and production systems. By leveraging data analytics and machine learning tools, PCB manufacturers can gain valuable insights into their processes, identify bottlenecks, and optimize their operations for maximum efficiency.
Embracing automation and Industry 4.0 technologies can help PCB manufacturers stay competitive in an increasingly digital and connected world, enabling them to respond more quickly to changing market demands and deliver high-quality products at lower costs.
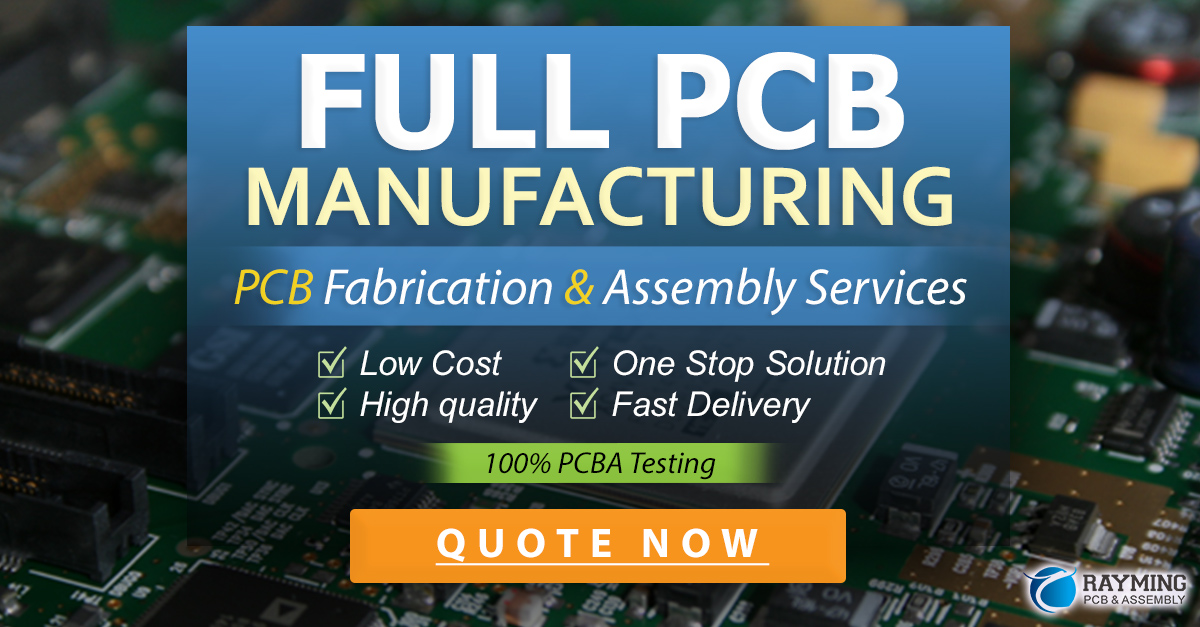
Implementing PCB Manufacturing Trends in Your Business
To take advantage of the latest PCB manufacturing trends and stay ahead of the competition, consider the following strategies:
- Invest in training and education: Ensure that your staff is well-versed in the latest PCB design and manufacturing techniques by providing regular training and educational opportunities.
- Collaborate with suppliers and partners: Work closely with your PCB suppliers and technology partners to stay informed about new materials, processes, and equipment that can benefit your business.
- Adopt a continuous improvement mindset: Regularly assess your PCB manufacturing operations to identify areas for improvement and implement changes that can enhance efficiency, quality, and cost-effectiveness.
- Embrace digital transformation: Invest in digital technologies, such as automation, data analytics, and cloud computing, to streamline your processes, improve decision-making, and enhance customer experiences.
By staying proactive and adaptable in the face of evolving PCB manufacturing trends, your business can remain competitive and thrive in the dynamic electronics industry.
FAQ
1. What are the benefits of keeping up with PCB manufacturing trends?
Keeping up with PCB manufacturing trends can help businesses improve efficiency, reduce costs, enhance product performance, and gain a competitive advantage in the market.
2. What is the importance of miniaturization and HDI PCBs in the electronics industry?
Miniaturization and HDI PCBs are essential for creating compact, high-performance electronic devices that meet the growing demand for smaller, more feature-rich products. By adopting these technologies, companies can reduce material costs, improve signal integrity, and create innovative designs.
3. How can flexible and rigid-flex PCBs benefit my business?
Flexible and rigid-flex PCBs offer several advantages, including space savings, improved reliability, and reduced assembly costs. These benefits make them ideal for applications such as wearable devices, smartphones, and other compact electronics.
4. Is additive manufacturing a viable option for PCB production?
While additive manufacturing is still in its early stages for PCB production, it holds promise for rapid prototyping, customization, and waste reduction. As the technology advances, it may become a more viable option for full-scale PCB manufacturing.
5. How can my business implement PCB manufacturing trends effectively?
To effectively implement PCB manufacturing trends, consider investing in training and education for your staff, collaborating with suppliers and partners, adopting a continuous improvement mindset, and embracing digital transformation. By staying proactive and adaptable, your business can successfully navigate the evolving PCB manufacturing landscape.
[PCB Manufacturing Trends Comparison]
Trend | Key Benefits | Applications |
---|---|---|
Miniaturization and HDI PCBs | Space savings, improved signal integrity, reduced material costs | Compact electronic devices, smartphones, wearables |
Flexible and Rigid-Flex PCBs | Space savings, improved reliability, reduced assembly costs | Wearable devices, smartphones, compact electronics |
Additive Manufacturing and 3D Printing | Rapid prototyping, customization, reduced waste | PCB Prototyping, unique PCB shapes and geometries |
Advanced Materials | Improved performance, reliability, and environmental sustainability | High-frequency applications (5G, automotive radar), high-power applications (LED lighting, power electronics), halogen-free PCBs |
Automation and Industry 4.0 | Improved efficiency, reduced costs, enhanced product quality | Automated optical inspection, robotic assembly, data analytics, and machine learning for process optimization |
Conclusion
In the fast-paced world of PCB manufacturing, staying current with the latest trends and technologies is crucial for businesses looking to remain competitive and meet the evolving demands of the electronics industry. By understanding and adopting key trends such as miniaturization, HDI PCBs, flexible and rigid-flex PCBs, additive manufacturing, advanced materials, and automation, companies can save time and energy while delivering high-quality, innovative products to their customers.
To successfully navigate the changing landscape of PCB manufacturing, businesses must be proactive in their approach, investing in education and training, collaborating with suppliers and partners, fostering a culture of continuous improvement, and embracing digital transformation. By doing so, they can position themselves for long-term success and growth in the dynamic and exciting field of PCB manufacturing.
Leave a Reply