Introduction to PCB Surface Finishes
PCB Surface Finishes play a crucial role in ensuring the reliability, solderability, and longevity of printed circuit boards. The right surface finish can enhance the performance of a PCB, while an inappropriate finish can lead to manufacturing defects and premature failure. In this comprehensive article, we’ll explore the various types of PCB Prototype surface finishes and their characteristics, helping you make an informed decision for your next project.
What are PCB Surface Finishes?
PCB surface finishes are protective coatings applied to the exposed copper surfaces of a printed circuit board. These finishes serve several purposes:
- Protecting the copper from oxidation and corrosion
- Enhancing the solderability of components
- Improving the electrical conductivity of the board
- Providing a smooth, uniform surface for component placement
Why are Surface Finishes Important?
Surface finishes are essential for several reasons:
- Solderability: A suitable surface finish ensures that components can be easily soldered to the board, creating a strong and reliable connection.
- Corrosion resistance: Copper is prone to oxidation and corrosion, which can degrade the performance of the PCB over time. Surface finishes protect the copper from these harmful effects.
- Shelf life: Some surface finishes, such as immersion silver and OSP, have a limited shelf life. Choosing the right finish based on your production and storage requirements is crucial.
- Cost: Different surface finishes have varying costs, which can impact the overall budget of your project.
Types of PCB Surface Finishes
There are several types of PCB surface finishes, each with its own advantages and disadvantages. Let’s explore the most common options:
1. HASL (Hot Air Solder Leveling)
HASL is one of the most widely used surface finishes in the PCB industry. The process involves dipping the PCB into a molten solder bath and then using hot air to remove excess solder, creating a smooth, level surface.
Advantages of HASL:
- Excellent solderability
- Good shelf life
- Cost-effective
- Suitable for most applications
Disadvantages of HASL:
- Uneven surface due to solder pooling
- Not suitable for fine-pitch components
- High-temperature process can cause thermal stress on the PCB
2. ENIG (Electroless Nickel Immersion Gold)
ENIG is a two-layer surface finish that consists of a nickel underlay and a thin gold top layer. The nickel layer provides a barrier against copper migration, while the gold layer offers excellent solderability and corrosion resistance.
Advantages of ENIG:
- Excellent solderability
- Good shelf life (up to 12 months)
- Suitable for fine-pitch components
- Flat, uniform surface
Disadvantages of ENIG:
- Higher cost compared to other finishes
- Possibility of “black pad” defect due to nickel corrosion
- Gold can dissolve into solder, affecting joint strength
3. Immersion Silver
Immersion silver is a single-layer surface finish that involves depositing a thin layer of silver onto the copper surface through a chemical process. Silver offers excellent solderability and is a cost-effective alternative to ENIG.
Advantages of Immersion Silver:
- Excellent solderability
- Suitable for fine-pitch components
- Flat, uniform surface
- Cost-effective compared to ENIG
Disadvantages of Immersion Silver:
- Limited shelf life (3-6 months)
- Prone to tarnishing over time
- Not suitable for high-temperature applications
4. OSP (Organic Solderability Preservative)
OSP is a single-layer organic coating that is applied to the copper surface to protect it from oxidation. This finish is often used for quick-turn prototypes and low-cost production runs.
Advantages of OSP:
- Cost-effective
- Suitable for fine-pitch components
- Flat, uniform surface
- Environmentally friendly
Disadvantages of OSP:
- Limited shelf life (1-3 months)
- Requires special handling and storage conditions
- Not suitable for multiple reflow cycles
5. ENEPIG (Electroless Nickel Electroless Palladium Immersion Gold)
ENEPIG is a three-layer surface finish that consists of a nickel underlay, a palladium middle layer, and a thin gold top layer. This finish offers the benefits of ENIG while addressing some of its limitations.
Advantages of ENEPIG:
- Excellent solderability
- Good shelf life (up to 12 months)
- Suitable for fine-pitch components
- Flat, uniform surface
- Resistant to “black pad” defect
Disadvantages of ENEPIG:
- Higher cost compared to other finishes
- Complex and time-consuming process
- Gold can dissolve into solder, affecting joint strength
Comparison of PCB Surface Finishes
Surface Finish | Solderability | Shelf Life | Fine-Pitch Compatibility | Cost |
---|---|---|---|---|
HASL | Excellent | Good | Not suitable | Low |
ENIG | Excellent | Good | Suitable | High |
Immersion Silver | Excellent | Limited | Suitable | Moderate |
OSP | Good | Limited | Suitable | Low |
ENEPIG | Excellent | Good | Suitable | High |
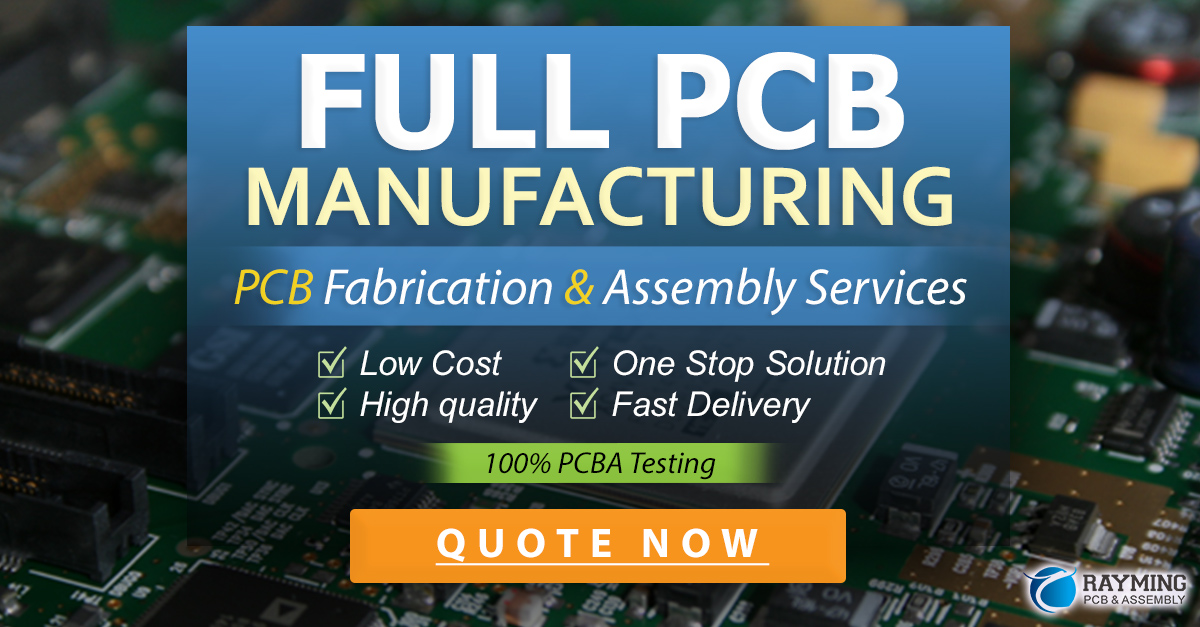
Frequently Asked Questions (FAQ)
1. What is the most cost-effective PCB surface finish?
HASL and OSP are the most cost-effective PCB surface finishes. However, they may not be suitable for all applications due to their limitations in fine-pitch compatibility and shelf life.
2. Which surface finish is best for fine-pitch components?
ENIG, Immersion Silver, and ENEPIG are all suitable for fine-pitch components due to their flat, uniform surfaces.
3. What is the shelf life of Immersion Silver?
The shelf life of Immersion Silver is typically 3-6 months, depending on storage conditions.
4. Can ENIG be used for high-temperature applications?
Yes, ENIG is suitable for high-temperature applications due to its excellent thermal stability.
5. What is the main disadvantage of ENEPIG?
The main disadvantage of ENEPIG is its higher cost compared to other surface finishes due to the complex and time-consuming process involved.
Conclusion
Choosing the right PCB surface finish is crucial for ensuring the reliability, solderability, and longevity of your printed circuit board. Each surface finish has its own advantages and disadvantages, and the best choice depends on your specific application, budget, and production requirements.
By understanding the characteristics of each surface finish and considering factors such as solderability, shelf life, fine-pitch compatibility, and cost, you can make an informed decision and select the most suitable finish for your PCB prototype project.
At RAYPCB, we offer a wide range of PCB surface finishes to meet the diverse needs of our customers. Our experienced team is ready to assist you in choosing the best finish for your project and ensuring the highest quality PCB manufacturing services.
Leave a Reply