Introduction to Rigid PCBs
Rigid PCBs (Printed Circuit Boards) are the backbone of modern electronics. These boards provide a stable and reliable platform for mounting and interconnecting electronic components. Rigid PCBs are made from a solid substrate material, typically fiberglass or epoxy resin, which gives them their rigid structure. This rigidity allows for precise component placement and ensures the board maintains its shape even under stress.
What are Rigid PCBs?
Rigid PCBs are printed circuit boards that are made from a solid, non-flexible substrate material. They are the most common type of PCB and are used in a wide variety of electronic devices, from smartphones and computers to medical equipment and aerospace systems. Rigid PCBs provide a stable platform for mounting electronic components and allow for precise control over the electrical connections between them.
Advantages of Rigid PCBs
Rigid PCBs offer several advantages over other types of circuit boards:
- Durability: The solid substrate material makes rigid PCBs more durable and resistant to physical stress and damage.
- Precision: Rigid PCBs allow for precise component placement and routing of electrical connections, which is critical for high-performance electronic devices.
- Heat dissipation: The rigid structure of the board helps dissipate heat generated by electronic components, which can improve the overall reliability and lifespan of the device.
- Cost-effective: Rigid PCBs are generally less expensive to manufacture than flexible or rigid-flex PCBs, making them a cost-effective choice for many applications.
Rigid PCB Manufacturing Process
The manufacturing process for rigid PCBs involves several steps, each of which requires precision and attention to detail. Here’s a brief overview of the main steps involved:
- Design: The first step is to design the PCB using specialized software. The design includes the placement of components, routing of electrical connections, and creation of the PCB layout.
- Substrate preparation: The substrate material, typically fiberglass or epoxy resin, is cut to the desired size and shape.
- Copper lamination: A thin layer of copper is laminated onto the substrate material using heat and pressure.
- Drilling: Holes are drilled into the board to accommodate through-hole components and vias.
- Patterning: The copper layer is patterned using a photolithographic process to create the desired electrical connections.
- Etching: The unwanted copper is removed using a chemical etching process, leaving only the desired copper traces.
- Soldermask application: A soldermask layer is applied to the board to protect the copper traces and prevent short circuits.
- Silkscreen printing: Text and symbols are printed onto the board using a silkscreen process to aid in assembly and identification of components.
- Surface finish: A surface finish, such as HASL (Hot Air Solder Leveling) or ENIG (Electroless Nickel Immersion Gold), is applied to the exposed copper to prevent oxidation and improve solderability.
- Testing and inspection: The completed board is tested and inspected to ensure it meets the required specifications and quality standards.
Rigid PCB Materials
The choice of substrate material is critical to the performance and reliability of a rigid PCB. The most common materials used are:
- FR-4: A composite material made from woven fiberglass and epoxy resin. FR-4 is the most widely used substrate material for rigid PCBs due to its excellent mechanical and electrical properties, as well as its low cost.
- CEM-3: A composite material made from woven fiberglass and epoxy resin, with a lower glass-to-epoxy ratio than FR-4. CEM-3 is less expensive than FR-4 but has slightly lower mechanical and electrical properties.
- Polyimide: A high-performance polymer material that offers excellent thermal stability, chemical resistance, and mechanical strength. Polyimide is often used in high-temperature and high-reliability applications, such as aerospace and military systems.
- Alumina: A ceramic material that offers excellent thermal conductivity and electrical insulation properties. Alumina is often used in high-power and high-frequency applications, such as RF and microwave circuits.
Rigid PCB Fabricators and Manufacturers
Choosing the right rigid PCB fabricator or manufacturer is essential to ensure the quality and reliability of your electronic devices. Here are some key factors to consider when selecting a rigid PCB supplier:
Experience and Expertise
Look for a supplier with extensive experience in manufacturing rigid PCBs for your specific industry or application. They should have a deep understanding of the unique requirements and challenges involved, and be able to provide expert guidance and support throughout the design and manufacturing process.
Quality Control and Certifications
Ensure that the supplier has robust quality control processes in place, including regular inspections and testing at various stages of the manufacturing process. Look for suppliers with relevant certifications, such as ISO 9001, ISO 14001, and UL certification, which demonstrate their commitment to quality and environmental responsibility.
Manufacturing Capabilities
Consider the supplier’s manufacturing capabilities, including their ability to handle different board sizes, layer counts, and materials. They should have state-of-the-art equipment and processes to ensure consistent quality and reliability.
Turnaround Time and Pricing
Evaluate the supplier’s turnaround time and pricing to ensure they can meet your project deadlines and budget constraints. Keep in mind that while price is an important factor, it should not be the sole deciding factor, as quality and reliability are equally critical.
Customer Support and Communication
Choose a supplier that offers excellent customer support and communication throughout the design and manufacturing process. They should be responsive to your inquiries, provide regular updates on project status, and be willing to work closely with you to address any issues or concerns that may arise.
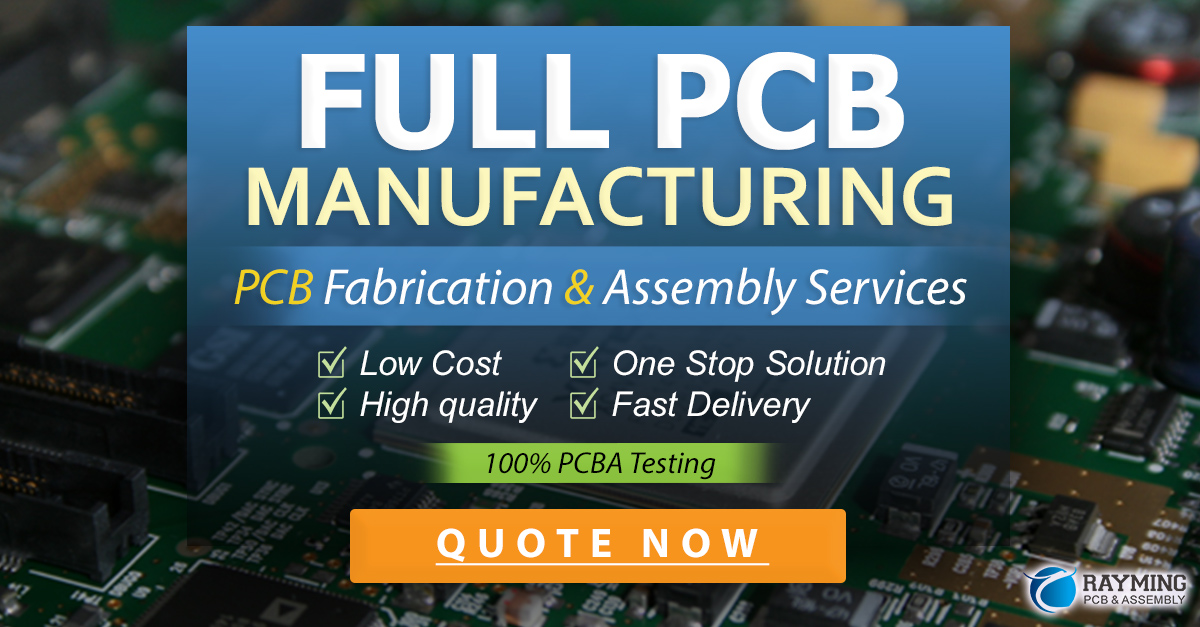
Rigid PCB Design Considerations
Designing a rigid PCB involves several key considerations to ensure optimal performance, reliability, and manufacturability. Here are some essential design factors to keep in mind:
Component Placement
Proper component placement is critical to ensure optimal signal integrity, thermal management, and manufacturability. Consider the size, shape, and orientation of components, as well as their proximity to other components and the board edge. Use design tools and simulations to optimize component placement and minimize signal interference.
Trace Routing
Trace routing involves designing the copper traces that connect components on the PCB. Consider factors such as trace width, spacing, and length to ensure adequate signal integrity and minimize crosstalk and electromagnetic interference (EMI). Use design rules and constraints to ensure manufacturability and avoid common issues such as acid traps and tombstoning.
Power and Ground Planes
Proper design of power and ground planes is essential to ensure stable power delivery and minimize noise and EMI. Use dedicated power and ground planes, and consider techniques such as split planes and stitching vias to improve signal integrity and reduce EMI.
Thermal Management
Thermal management is critical to ensure the long-term reliability and performance of electronic components. Consider factors such as component power dissipation, board material thermal conductivity, and ambient temperature when designing the PCB. Use thermal simulations and design techniques such as thermal vias and heatsinks to manage heat dissipation effectively.
Design for Manufacturing (DFM)
Designing for manufacturability involves considering the limitations and capabilities of the PCB manufacturing process during the design phase. This includes factors such as minimum trace width and spacing, hole size and spacing, and soldermask and silkscreen design. Use DFM tools and guidelines to ensure your design can be manufactured reliably and cost-effectively.
Rigid PCB Testing and Inspection
Thorough testing and inspection are critical to ensure the quality and reliability of rigid PCBs. Here are some common testing and inspection methods used in the PCB industry:
Automated Optical Inspection (AOI)
AOI uses high-resolution cameras and image processing software to inspect the PCB for defects such as missing or misaligned components, solder bridges, and incorrect component polarity. AOI can quickly and accurately detect defects that may be difficult to spot with manual inspection.
X-Ray Inspection
X-ray inspection uses X-ray imaging to inspect the internal structure of the PCB, including solder joints and vias. This method can detect defects that may be hidden from view, such as voids in solder joints or broken vias.
In-Circuit Testing (ICT)
ICT involves using a bed-of-nails fixture to make electrical contact with the PCB and test the functionality of individual components and circuits. ICT can quickly identify defects such as open or short circuits, incorrect component values, and missing or damaged components.
Functional Testing
Functional testing involves testing the PCB under real-world operating conditions to ensure it performs as intended. This may include testing the board’s response to various inputs and outputs, as well as its behavior under different environmental conditions such as temperature and humidity.
Rigid PCB Applications
Rigid PCBs are used in a wide range of electronic devices and systems across various industries. Here are some common applications of rigid PCBs:
- Consumer electronics: Smartphones, tablets, laptops, gaming consoles, and home appliances.
- Automotive electronics: Engine control units, infotainment systems, and advanced driver assistance systems (ADAS).
- Medical devices: Diagnostic equipment, patient monitoring systems, and implantable devices.
- Industrial automation: Programmable logic controllers (PLCs), sensors, and motor drives.
- Aerospace and defense: Avionics, radar systems, and satellite communications equipment.
- Telecommunications: Routers, switches, and base stations for wireless networks.
FAQ
1. What is the difference between a rigid PCB and a flexible PCB?
A rigid PCB is made from a solid, non-flexible substrate material, typically fiberglass or epoxy resin. In contrast, a flexible PCB is made from a thin, flexible polymer material such as polyimide. Rigid PCBs offer greater durability and stability, while flexible PCBs offer greater flexibility and conformability for applications with limited space or moving parts.
2. What are the most common materials used for rigid PCB substrates?
The most common materials used for rigid PCB substrates are FR-4 (a composite of woven fiberglass and epoxy resin), CEM-3 (a lower-cost alternative to FR-4), polyimide (a high-performance polymer), and alumina (a ceramic material used in high-power and high-frequency applications).
3. What is the typical turnaround time for rigid PCB manufacturing?
The turnaround time for rigid PCB manufacturing can vary depending on the complexity of the design, the quantity ordered, and the manufacturer’s capabilities. Typical turnaround times range from a few days to several weeks, with expedited options available for urgently needed boards.
4. What is the minimum feature size that can be achieved with rigid PCB manufacturing?
The minimum feature size that can be achieved with rigid PCB manufacturing depends on the specific manufacturing process and equipment used. Typically, modern PCB manufacturers can achieve minimum trace widths and spacings of around 3-4 mils (0.075-0.1 mm) for standard designs, with even smaller features possible for advanced designs using specialized processes.
5. How can I ensure the quality and reliability of my rigid PCBs?
To ensure the quality and reliability of your rigid PCBs, choose a reputable manufacturer with a proven track record of quality and reliability. Look for manufacturers with relevant certifications such as ISO 9001 and UL, and ensure they have robust quality control processes in place. Work closely with your manufacturer throughout the design and manufacturing process to ensure your requirements are met, and consider using advanced testing and inspection methods such as AOI, X-ray, and functional testing to identify and correct any defects.
Conclusion
Rigid PCBs are the foundation of modern electronics, providing a stable and reliable platform for mounting and interconnecting electronic components. With their durability, precision, and cost-effectiveness, rigid PCBs are used in a wide range of applications across various industries, from consumer electronics to aerospace and defense.
Choosing the right rigid PCB manufacturer is critical to ensure the quality and reliability of your electronic devices. Look for a supplier with extensive experience, robust quality control processes, advanced manufacturing capabilities, competitive pricing, and excellent customer support.
When designing rigid PCBs, consider factors such as component placement, trace routing, power and ground planes, thermal management, and design for manufacturability to ensure optimal performance and reliability. Thorough testing and inspection using methods such as AOI, X-ray, ICT, and functional testing can help identify and correct any defects before the boards are assembled into the final product.
As electronic devices continue to evolve and become more complex, the demand for high-quality rigid PCBs will only continue to grow. By staying up-to-date with the latest manufacturing processes, design techniques, and testing methods, rigid PCB manufacturers and designers can help drive innovation and ensure the continued success of the electronics industry.
Leave a Reply