What is a Carbon Ink PCB?
A carbon ink PCB is a printed circuit board where the conductive traces are made from carbon-based inks rather than the traditional copper. The carbon ink is printed onto the substrate material (usually a flexible plastic film) using methods like screen printing or inkjet printing to create the desired circuit pattern.
The key component is the carbon ink itself, which is composed of conductive carbon particles suspended in a liquid binder. When printed and cured, the ink forms conductive pathways that carry electrical signals, just like the copper traces on a standard PCB.
Composition of Carbon Inks
Carbon inks typically contain the following components:
- Conductive carbon particles (e.g., graphite, carbon nanotubes, or carbon black)
- Polymer binder (e.g., polyester, acrylic, or polyurethane)
- Solvents (e.g., water or organic solvents)
- Additives (e.g., dispersants, rheology modifiers, or crosslinking agents)
The specific formulation of the ink determines its properties, such as conductivity, flexibility, and durability. Researchers are continually developing new carbon ink formulations to improve performance and enable new applications.
How Carbon Ink PCBs Work
Carbon ink PCBs work on the same basic principles as traditional PCBs. The conductive carbon traces carry electrical signals between components mounted on the board. However, there are some key differences in how carbon ink PCBs are manufactured and how they perform compared to copper-based boards.
Manufacturing Process
The manufacturing process for carbon ink PCBs typically involves the following steps:
-
Substrate preparation: The flexible substrate (usually PET or PEN film) is cleaned and treated to improve ink adhesion.
-
Ink formulation: The carbon ink is prepared by mixing the conductive particles, binder, solvents, and additives according to the desired formulation.
-
Printing: The carbon ink is printed onto the substrate using a method like screen printing or inkjet printing. Multiple layers may be printed to achieve the desired thickness and conductivity.
-
Curing: The printed ink is cured using heat or UV light to evaporate the solvents and crosslink the binder, forming a solid conductive trace.
-
Component assembly: Electronic components are attached to the carbon ink traces using conductive adhesives or low-temperature soldering methods.
Compared to the manufacturing of Copper-Based PCBs, carbon ink PCBs can be made using simpler, less expensive equipment and fewer processing steps. This makes them potentially cheaper and faster to produce, especially for low-volume or prototype applications.
Electrical Performance
Carbon ink PCBs have higher electrical resistance than copper-based boards due to the lower conductivity of carbon compared to copper. The resistivity of carbon inks is typically in the range of 10-100 μΩ·cm, while copper’s resistivity is around 1.68 μΩ·cm.
This higher resistance can limit the current-carrying capacity and increase the voltage drop across the traces, which may impact the performance of some circuits. However, for many low-power applications, the conductivity of carbon inks is sufficient.
Carbon ink traces also have a higher capacitance and inductance than copper traces, which can affect high-frequency signal integrity. The exact electrical properties depend on the specific ink formulation and printing process used.
Benefits of Carbon Ink PCBs
Carbon ink PCBs offer several potential benefits over traditional copper-based boards:
-
Lower cost: Carbon inks are generally cheaper than copper, and the simpler manufacturing process can reduce production costs.
-
Flexibility: Carbon ink PCBs can be printed on flexible substrates, allowing for bendable and stretchable circuits that can conform to curved surfaces.
-
Rapid prototyping: The simpler manufacturing process enables faster turnaround times for prototype boards, reducing development cycles.
-
Environmentally friendly: Carbon inks are typically less toxic and more recyclable than the chemicals used in Copper PCB manufacturing.
-
Integration with printed electronics: Carbon inks are compatible with other printed electronic materials, enabling the creation of fully printed devices.
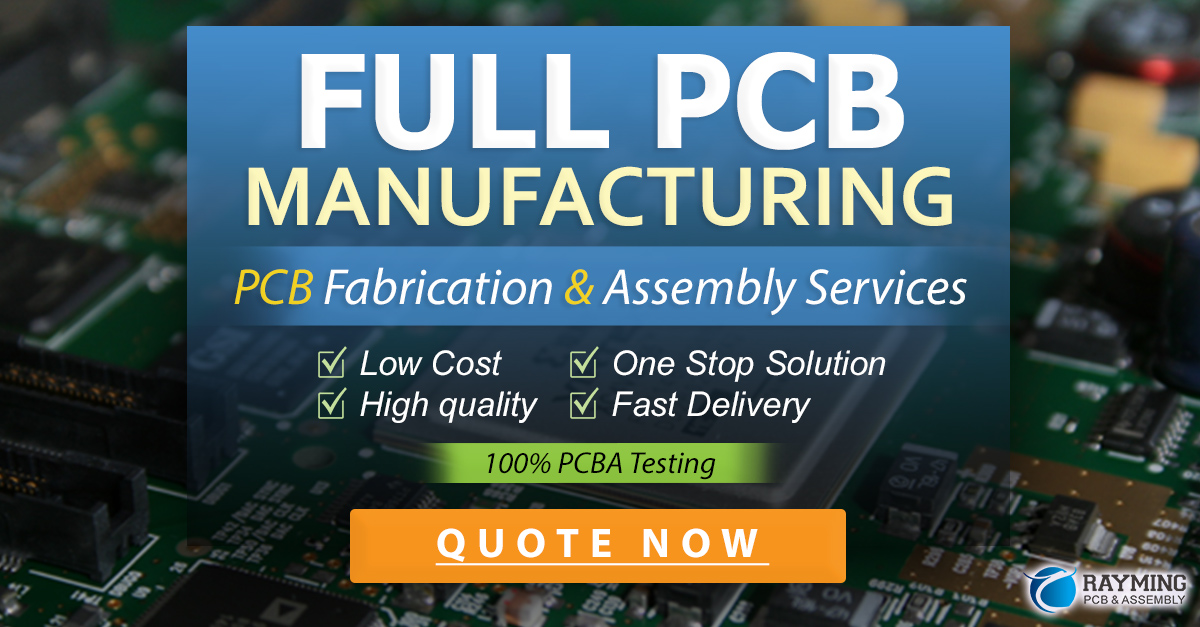
Drawbacks of Carbon Ink PCBs
Despite their benefits, carbon ink PCBs also have some limitations and drawbacks:
-
Lower conductivity: The higher resistance of carbon inks limits their use in high-power or high-frequency applications.
-
Durability: Carbon ink traces may be less durable than copper traces and more susceptible to wear or damage from environmental factors.
-
Limited component compatibility: Not all electronic components are suitable for attachment to carbon ink traces, potentially limiting design options.
-
Reduced thermal conductivity: Carbon inks have lower thermal conductivity than copper, which can impact heat dissipation in some applications.
-
Lack of standardization: As an emerging technology, there are fewer established standards and guidelines for carbon ink PCB design and manufacturing compared to copper-based boards.
Applications of Carbon Ink PCBs
Carbon ink PCBs are particularly well-suited for certain applications, such as:
-
Flexible electronics: The ability to print carbon inks on flexible substrates enables the creation of bendable and stretchable circuits for wearables, sensors, and other flexible devices.
-
Low-power devices: For applications with low current and power requirements, such as IoT sensors or disposable electronics, the lower conductivity of carbon inks may be sufficient.
-
Rapid prototyping: The faster turnaround times and lower costs of carbon ink PCBs make them attractive for prototyping and testing new designs.
-
Printed electronics: Carbon inks can be integrated with other printed electronic materials, such as conductive polymers or organic semiconductors, to create fully printed devices like solar cells, displays, or RFID tags.
-
Disposable electronics: The lower cost and environmental friendliness of carbon inks make them suitable for single-use or disposable electronic devices, such as medical sensors or packaging electronics.
As research continues and the technology matures, the range of applications for carbon ink PCBs is likely to expand.
Frequently Asked Questions (FAQ)
-
Are carbon ink PCBs as reliable as traditional copper PCBs?
While carbon ink PCBs can be reliable for certain applications, they may not be as durable or stable as copper PCBs in demanding environments. The reliability depends on factors like the ink formulation, printing process, and environmental conditions. -
Can carbon ink PCBs completely replace copper PCBs?
Currently, carbon ink PCBs are not a direct replacement for copper PCBs in all applications. They are best suited for specific use cases where their benefits (flexibility, low cost, rapid prototyping) outweigh their limitations (lower conductivity, reduced durability). -
How do the costs of carbon ink PCBs compare to copper PCBs?
The material costs for carbon inks are generally lower than for copper, and the simpler manufacturing process can reduce production costs. However, the exact cost comparison depends on factors like volume, design complexity, and specific ink formulation used. -
What are the environmental impacts of carbon ink PCBs?
Carbon ink PCBs are generally considered more environmentally friendly than copper PCBs, as they use fewer toxic chemicals in production and are potentially more recyclable. However, a full lifecycle assessment would be needed to quantify the environmental impacts. -
What is the future outlook for carbon ink PCB technology?
As research continues and the technology matures, carbon ink PCBs are likely to become more common in certain applications, particularly in flexible electronics and printed electronics. However, they are unlikely to completely replace copper PCBs in the near future, and will likely coexist as a complementary technology for specific use cases.
Conclusion
Carbon ink PCBs are an emerging technology that offers several potential benefits over traditional copper-based boards, including lower costs, flexibility, rapid prototyping, and environmental friendliness. While they have limitations in terms of conductivity and durability, they are well-suited for certain applications like flexible electronics, low-power devices, and printed electronics.
As research continues and the technology matures, carbon ink PCBs are likely to play an increasingly important role in the future of electronics manufacturing, particularly in enabling new form factors and applications. However, they are unlikely to completely replace copper PCBs in the near term, and will likely coexist as a complementary technology for specific use cases.
Understanding the properties, benefits, and limitations of carbon ink PCBs is essential for designers and engineers looking to leverage this emerging technology in their projects. By carefully considering the specific requirements and trade-offs of each application, they can determine whether carbon ink PCBs are a suitable choice and how to best design and manufacture them for optimal performance and reliability.
Word count: 1387
Leave a Reply