Introduction to 3D-Printed PCBs
The world of electronics has been revolutionized by the advent of 3D printing technology. One of the most exciting developments in this field is the ability to create 3D-printed circuit boards (PCBs) using additive manufacturing processes. This innovative approach to PCB fabrication offers numerous advantages over traditional methods, including faster prototyping, increased design flexibility, and reduced waste.
In this article, we will explore the concept of 3D-printed PCBs in depth, discussing their manufacturing process, benefits, and potential applications. We will also examine the current state of the technology and its future prospects.
What is a 3D-Printed PCB?
A 3D-printed PCB is a printed circuit board that is fabricated using additive manufacturing techniques, specifically 3D printing. Unlike traditional PCB manufacturing methods, which involve subtractive processes such as etching and drilling, 3D printing builds the PCB layer by layer, depositing conductive and insulating materials as needed.
This additive approach allows for greater design freedom, enabling the creation of complex geometries and multi-layer structures that would be difficult or impossible to achieve with conventional methods. Additionally, 3D printing enables the rapid prototyping of PCBs, reducing the time and cost associated with traditional manufacturing processes.
How are 3D-Printed PCBs Manufactured?
The manufacturing process for 3D-printed PCBs involves several key steps:
-
Design: The PCB design is created using computer-aided design (CAD) software, which generates a 3D model of the board. This model includes the conductive traces, insulating layers, and any other necessary features.
-
Slicing: The 3D model is then “sliced” into thin layers using specialized software. These layers represent the cross-sections of the PCB that will be printed one at a time.
-
Printing: The sliced model is sent to a 3D printer, which begins depositing the materials layer by layer. The printer typically uses a combination of conductive and insulating materials, such as conductive filaments or inks and insulating thermoplastics.
-
Curing: After each layer is printed, it may need to undergo a curing process to solidify the materials and ensure proper adhesion between layers. This can be done using heat, UV light, or other methods, depending on the materials used.
-
Post-processing: Once the printing is complete, the PCB may require additional post-processing steps, such as cleaning, sanding, or the application of protective coatings.
Step | Description |
---|---|
Design | Create 3D model of PCB using CAD software |
Slicing | Divide 3D model into thin layers for printing |
Printing | Deposit materials layer by layer using 3D printer |
Curing | Solidify materials and ensure adhesion between layers |
Post-processing | Clean, sand, or apply protective coatings as needed |
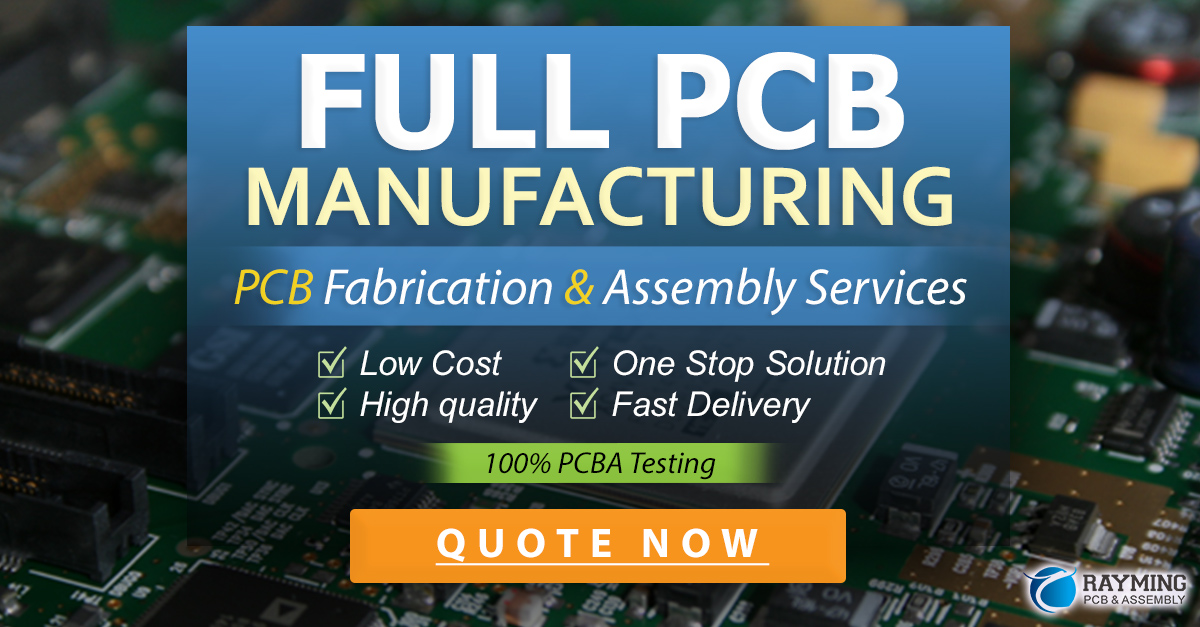
Benefits of 3D-Printed PCBs
3D-printed PCBs offer several significant advantages over traditionally manufactured boards:
-
Rapid prototyping: 3D printing allows for the quick and easy creation of PCB Prototypes, enabling designers to test and refine their designs much more efficiently than with traditional methods.
-
Design flexibility: The additive nature of 3D printing enables the creation of complex geometries and multi-layer structures that would be challenging or impossible to achieve with conventional PCB manufacturing techniques.
-
Reduced waste: Because 3D printing only deposits the materials needed to create the PCB, there is significantly less waste compared to subtractive manufacturing methods, which generate excess material that must be discarded.
-
Customization: 3D printing allows for the creation of highly customized PCBs tailored to specific applications or devices, without the need for expensive tooling or setup costs.
-
Cost-effectiveness: For low-volume production or prototyping, 3D printing can be more cost-effective than traditional PCB manufacturing methods, as it eliminates the need for expensive tooling and setup costs.
Applications of 3D-Printed PCBs
3D-printed PCBs have a wide range of potential applications across various industries:
-
Aerospace: 3D-printed PCBs can be used to create lightweight, compact, and highly customized electronic systems for aerospace applications, such as satellites, drones, and aircraft.
-
Medical devices: The ability to create complex geometries and integrate multiple functions into a single PCB makes 3D printing well-suited for the development of advanced medical devices, such as implantable sensors and diagnostic tools.
-
Wearable technology: 3D printing can be used to create flexible and conformable PCBs that can be integrated into wearable devices, such as smartwatches, fitness trackers, and health monitoring systems.
-
Internet of Things (IoT): The rapid prototyping capabilities of 3D printing can accelerate the development of IoT devices, enabling designers to quickly iterate and refine their designs for smart homes, industrial automation, and other connected applications.
-
Education and research: 3D-printed PCBs can be used as educational tools to teach students about electronics and circuit design, as well as for research purposes in fields such as materials science and additive manufacturing.
Current State and Future Prospects
While 3D-printed PCBs are still an emerging technology, significant progress has been made in recent years. Researchers and companies have developed new materials, printing techniques, and post-processing methods to improve the performance and reliability of 3D-printed PCBs.
However, there are still challenges to be addressed, such as the limited resolution and conductivity of current 3D printing technologies compared to traditional PCB manufacturing methods. Additionally, the long-term reliability and durability of 3D-printed PCBs need to be further investigated and optimized.
Despite these challenges, the future of 3D-printed PCBs looks promising. As the technology continues to advance, it is expected that 3D printing will become an increasingly viable option for PCB fabrication, particularly for low-volume production, prototyping, and highly customized applications.
FAQs
-
What materials are used to create 3D-printed PCBs?
3D-printed PCBs typically use a combination of conductive and insulating materials, such as conductive filaments or inks (e.g., silver-filled thermoplastics or conductive pastes) and insulating thermoplastics (e.g., PLA or ABS). -
Can 3D-printed PCBs achieve the same level of performance as traditionally manufactured PCBs?
Currently, 3D-printed PCBs may not achieve the same level of performance as traditionally manufactured PCBs in terms of resolution, conductivity, and reliability. However, as the technology advances, the performance gap is expected to narrow. -
How long does it take to 3D print a PCB?
The time required to 3D print a PCB varies depending on the size and complexity of the design, as well as the specific printing technology used. However, in general, 3D printing can significantly reduce the time required for PCB Prototyping compared to traditional manufacturing methods. -
Are 3D-printed PCBs suitable for high-volume production?
At present, 3D-printed PCBs are more suitable for low-volume production and prototyping due to the slower printing speeds and higher costs compared to traditional high-volume PCB manufacturing methods. -
What are the environmental benefits of 3D-printed PCBs?
3D-printed PCBs generate less waste compared to traditional subtractive manufacturing methods, as the additive process only deposits the materials needed to create the board. This can lead to a reduction in environmental impact and material consumption.
Conclusion
3D-printed PCBs represent an exciting development in the world of electronics, offering numerous benefits such as rapid prototyping, design flexibility, and reduced waste. As the technology continues to advance, it is expected that 3D printing will play an increasingly important role in PCB fabrication, particularly for low-volume production, customized applications, and research purposes.
While there are still challenges to be addressed, such as improving the resolution, conductivity, and reliability of 3D-printed PCBs, the potential for this technology is vast. As researchers and companies continue to innovate and refine the materials, printing techniques, and post-processing methods, the future of 3D-printed PCBs looks bright.
Leave a Reply