Introduction to PCB Layout Design
PCB (Printed Circuit Board) layout design is a crucial step in the process of creating electronic devices. It involves arranging the components and routing the connections on a circuit board to ensure proper functionality, reliability, and manufacturability. Designing a PCB layout requires knowledge of electronic design principles, PCB manufacturing techniques, and the specific requirements of the project at hand.
In this comprehensive guide, we will cover everything you need to know about designing a PCB layout. From understanding the basics of PCB design to advanced techniques and best practices, this article will provide you with the knowledge and tools to create high-quality PCB layouts.
Understanding the Basics of PCB Design
Before diving into the specifics of PCB layout design, it’s essential to understand the fundamentals of PCB design. A PCB consists of several layers of conductive material, typically copper, separated by insulating layers. The components are mounted on the top or bottom layer of the PCB, and the connections between them are routed through the conductive layers.
PCB Layers
A typical PCB can have anywhere from one to multiple layers, depending on the complexity of the design. The most common PCB layer stackups are:
- Single-layer PCB: A single conductive layer on one side of the insulating substrate.
- Double-layer PCB: Two conductive layers, one on each side of the insulating substrate.
- Multi-layer PCB: Three or more conductive layers, with insulating layers between them.
Layer Type | Description |
---|---|
Signal | Used for routing signals between components |
Power | Provides power to the components |
Ground | Serves as a reference point for signals and helps reduce noise |
PCB Components
PCBs can accommodate a wide range of electronic components, including:
- Resistors
- Capacitors
- Inductors
- Integrated Circuits (ICs)
- Connectors
- Switches
- LEDs
- Transistors
Each component has specific requirements for placement, orientation, and connection to other components. It’s crucial to consider these requirements when designing the PCB layout.
PCB Layout Design Process
The PCB layout design process typically follows these steps:
- Schematic Design: Create a schematic diagram of the circuit, specifying the components and their connections.
- Component Placement: Arrange the components on the PCB, considering factors such as signal integrity, heat dissipation, and mechanical constraints.
- Routing: Connect the components using conductive traces, following design rules and guidelines to ensure proper functionality and manufacturability.
- Design Rule Check (DRC): Verify that the PCB layout meets the specified design rules, such as minimum trace width, clearance, and drill sizes.
- Manufacturing Preparation: Generate the necessary files for PCB fabrication, including Gerber files, drill files, and assembly drawings.
Schematic Design
The schematic design is the first step in the PCB layout design process. It involves creating a diagram that represents the electrical connections between the components. The schematic should be clear, well-organized, and follow standard conventions for symbols and labeling.
Component Placement
Once the schematic is complete, the next step is to place the components on the PCB. The placement should consider several factors, including:
- Signal integrity: Place components to minimize the length of critical signal paths and avoid crosstalk.
- Thermal management: Arrange components to ensure proper heat dissipation and avoid hot spots.
- Mechanical constraints: Consider the mechanical requirements of the enclosure, connectors, and user interface.
- Manufacturing feasibility: Ensure that the component placement allows for efficient assembly and testing.
Routing
Routing is the process of connecting the components using conductive traces. The goal of routing is to create a reliable and efficient connection between the components while minimizing signal integrity issues and manufacturing challenges.
Routing Guidelines
- Use appropriate trace widths based on the current requirements and manufacturing capabilities.
- Maintain proper clearance between traces and components to avoid short circuits and manufacturing defects.
- Minimize the length of critical signal paths to reduce signal integrity issues.
- Avoid sharp angles and use smooth curves to improve signal integrity and manufacturability.
- Use ground planes and power planes to provide a low-impedance return path for signals and reduce noise.
Routing Techniques
- Manual routing: Manually place and route traces using PCB design software tools.
- Autorouting: Use automated routing algorithms to generate trace connections based on design rules and constraints.
- Differential pair routing: Route pairs of signals with equal and opposite polarity to minimize electromagnetic interference (EMI) and improve signal integrity.
- Length matching: Ensure that the length of critical signal paths is matched to maintain signal integrity and timing.
Design Rule Check (DRC)
After completing the component placement and routing, it’s essential to perform a Design Rule Check (DRC) to verify that the PCB layout meets the specified design rules. The DRC checks for issues such as:
- Minimum trace width and clearance
- Minimum drill sizes and annular rings
- Solder mask and silkscreen clearance
- Component placement and orientation
Resolving DRC errors ensures that the PCB layout is manufacturable and meets the required specifications.
Manufacturing Preparation
The final step in the PCB layout design process is to prepare the necessary files for manufacturing. This typically includes:
- Gerber files: A set of files that describe the PCB layers, including copper, solder mask, and silkscreen.
- Drill files: A file that specifies the location, size, and type of holes to be drilled in the PCB.
- Assembly drawings: Detailed drawings that show the component placement, orientation, and labeling for assembly purposes.
These files are sent to the PCB fabrication and assembly service provider to manufacture the physical PCB.
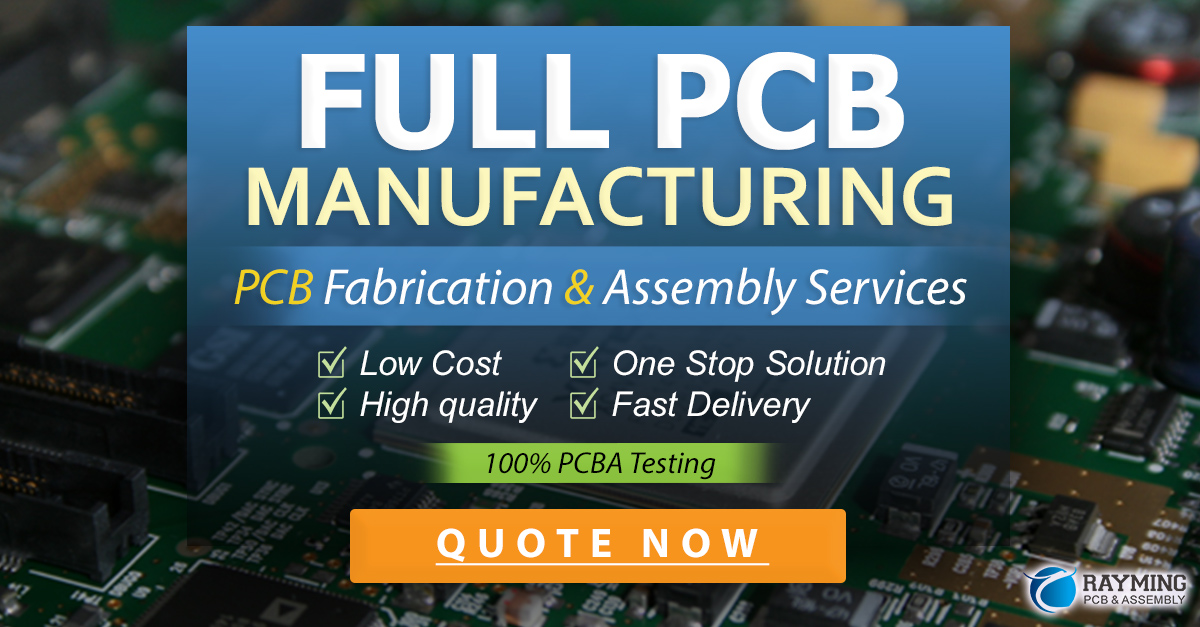
Advanced PCB Layout Techniques
In addition to the basic PCB layout design process, there are several advanced techniques that can help optimize the performance, reliability, and manufacturability of the PCB.
High-Speed Design Considerations
When designing PCBs for high-speed applications, such as high-frequency digital circuits or RF circuits, additional considerations are necessary to ensure signal integrity and minimize EMI. Some high-speed design techniques include:
- Impedance matching: Match the impedance of the traces to the source and load impedances to minimize reflections and signal distortion.
- Termination: Use appropriate termination techniques, such as series termination or parallel termination, to minimize reflections and improve signal quality.
- Shielding: Use shielding techniques, such as ground planes or shielded cables, to reduce EMI and crosstalk.
- Decoupling: Place decoupling capacitors close to power pins of ICs to reduce power supply noise and improve signal integrity.
Thermal Management
Proper thermal management is crucial for the reliability and longevity of the PCB. Some thermal management techniques include:
- Thermal vias: Use thermal vias to transfer heat from components to the ground plane or heatsink.
- Copper pours: Use large copper pours on the PCB layers to dissipate heat and improve thermal conductivity.
- Component placement: Place heat-generating components away from temperature-sensitive components and provide adequate spacing for heat dissipation.
- Heatsinks: Use heatsinks to dissipate heat from high-power components, such as voltage regulators or power transistors.
EMC and EMI Considerations
Electromagnetic Compatibility (EMC) and Electromagnetic Interference (EMI) are important considerations in PCB layout design to ensure that the electronic device does not interfere with other devices and meets regulatory requirements. Some EMC and EMI techniques include:
- Grounding: Provide a low-impedance ground path for high-frequency currents and use ground planes to reduce EMI.
- Filtering: Use filters, such as ferrite beads or pi-filters, to suppress high-frequency noise and prevent EMI.
- Shielding: Use shielding techniques, such as metal enclosures or shielded cables, to contain EMI and prevent interference.
- Layout techniques: Use layout techniques, such as minimizing loop areas, separating sensitive signals, and avoiding parallel traces, to reduce EMI.
Design for Manufacturability (DFM)
Design for Manufacturability (DFM) is the practice of designing PCBs to optimize the manufacturing process, reduce costs, and improve reliability. Some DFM techniques include:
- Standard component sizes: Use standard component sizes and packages to reduce costs and improve availability.
- Minimum feature sizes: Adhere to the minimum trace width, clearance, and drill sizes specified by the PCB fabrication service provider.
- Panelization: Design the PCB to fit efficiently into a standard panel size to reduce manufacturing costs.
- Testability: Include test points and access to critical signals to facilitate testing and debugging during manufacturing.
PCB Layout Design Software
There are several PCB layout design software tools available in the market, ranging from free and open-source to commercial and enterprise-level solutions. Some popular PCB layout design software include:
- Autodesk Eagle
- KiCad
- Altium Designer
- Cadence OrCAD
- Mentor Graphics PADS
These software tools provide a wide range of features and capabilities, including schematic capture, component libraries, routing tools, 3D visualization, and manufacturing file generation.
Conclusion
Designing a PCB layout is a complex process that requires knowledge of electronic design principles, PCB manufacturing techniques, and the specific requirements of the project. By understanding the basics of PCB design, following best practices for component placement and routing, and applying advanced techniques for high-speed design, thermal management, and EMC/EMI, you can create high-quality PCB layouts that meet the functional and manufacturing requirements of your electronic device.
Frequently Asked Questions (FAQ)
-
What is the difference between a schematic and a PCB layout?
A schematic is a diagram that represents the electrical connections between components, while a PCB layout is the physical arrangement of components and traces on a circuit board. -
What are the most common PCB layer stackups?
The most common PCB layer stackups are single-layer, double-layer, and multi-layer PCBs. Single-layer PCBs have one conductive layer, double-layer PCBs have two conductive layers (one on each side), and multi-layer PCBs have three or more conductive layers with insulating layers between them. -
What is the purpose of a Design Rule Check (DRC)?
A Design Rule Check (DRC) is performed to verify that the PCB layout meets the specified design rules, such as minimum trace width, clearance, and drill sizes. It helps ensure that the PCB layout is manufacturable and meets the required specifications. -
What are some high-speed design considerations for PCB layout?
Some high-speed design considerations for PCB layout include impedance matching, termination, shielding, and decoupling. These techniques help ensure signal integrity, minimize reflections and signal distortion, and reduce electromagnetic interference (EMI) and crosstalk. -
What is Design for Manufacturability (DFM) in PCB layout design?
Design for Manufacturability (DFM) is the practice of designing PCBs to optimize the manufacturing process, reduce costs, and improve reliability. It involves using standard component sizes, adhering to minimum feature sizes, designing for efficient panelization, and including features for testability and debugging during manufacturing.
Leave a Reply