Introduction to PCB Soldering
Printed Circuit Board (PCB) soldering is a crucial process in electronics manufacturing that involves joining electronic components to the copper pads on a PCB using molten solder. One important aspect of PCB soldering is creating good solder balls, which ensure strong and reliable connections between components and the board. In this comprehensive guide, we will explore the techniques, tools, and best practices for making high-quality PCB solder balls.
What is a PCB Solder Ball?
A PCB solder ball is a small sphere of solder that is used to create electrical and mechanical connections between electronic components and the copper pads on a printed circuit board. Solder balls are typically made from a tin-lead (SnPb) alloy or lead-free alternatives like tin-silver-copper (SAC) alloys. The size of the solder ball depends on the specific application and the size of the components being soldered.
Advantages of Using Solder Balls in PCB Assembly
Using solder balls in PCB assembly offers several advantages:
- Improved connection reliability: Solder balls create strong and reliable connections between components and the PCB, reducing the risk of connection failures.
- Enhanced thermal and electrical conductivity: The spherical shape of solder balls allows for better thermal and electrical conductivity compared to other connection methods.
- Increased manufacturing efficiency: Solder balls enable automated assembly processes, such as ball grid array (BGA) and chip scale package (CSP) mounting, which improve production speed and consistency.
- Space-saving design: Solder balls allow for high-density component placement, enabling smaller and more compact PCB designs.
Common Solder Ball Sizes and Alloys
Solder balls come in various sizes and alloys to suit different PCB assembly requirements. The following table lists some common solder ball sizes and their applications:
Solder Ball Diameter | Application |
---|---|
0.25mm to 0.40mm | Chip Scale Packages (CSP) and ultra-fine pitch BGA |
0.50mm to 0.60mm | Fine pitch BGA and QFN packages |
0.76mm to 1.00mm | Standard BGA packages |
1.27mm to 1.50mm | High-power BGA packages and through-hole components |
The most common solder ball alloys used in PCB assembly are:
- Tin-Lead (SnPb): Traditionally used for its excellent wetting properties and low melting point. However, it is being phased out due to environmental and health concerns.
- Tin-Silver-Copper (SAC): Lead-free alloys, such as SAC305 (96.5% Sn, 3% Ag, 0.5% Cu) and SAC405 (95.5% Sn, 4% Ag, 0.5% Cu), are becoming increasingly popular as a replacement for SnPb alloys.
Preparing the PCB for Soldering
Before creating solder balls and soldering components onto the PCB, it is essential to properly prepare the board for the soldering process:
PCB Cleaning
- Remove any dirt, grease, or contaminants from the PCB surface using isopropyl alcohol (IPA) and a lint-free cloth.
- For stubborn contaminants, use a mild abrasive cleaner like a glass fiber pen or a soft-bristled brush.
- Ensure the PCB is completely dry before proceeding with the soldering process.
Applying Solder Paste
- Apply solder paste to the copper pads using a stencil or a syringe dispenser.
- Ensure the solder paste is evenly distributed and covers the entire pad area.
- Inspect the solder paste application for any defects, such as bridging or insufficient coverage.
Component Placement
- Place the components on the PCB, aligning them with their respective pads.
- Use tweezers or a vacuum pick-up tool to handle small components and ensure precise placement.
- Double-check component orientation and alignment before proceeding with the soldering process.
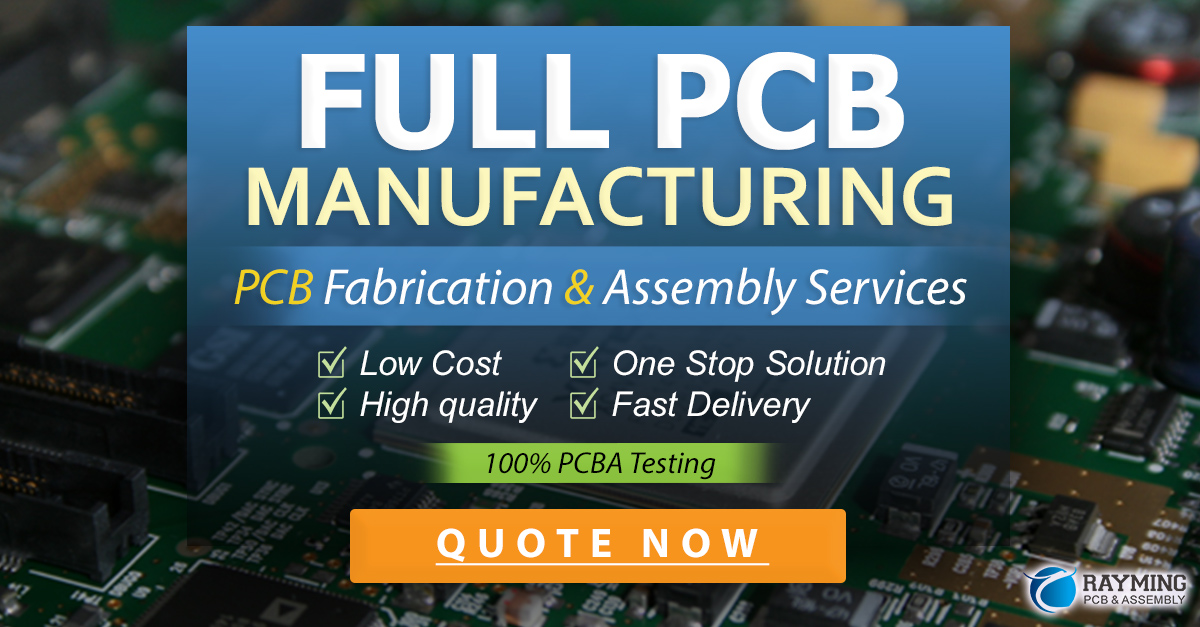
Creating High-Quality Solder Balls
To create high-quality solder balls for PCB assembly, consider the following techniques and best practices:
Solder Ball Formation Methods
- Stencil Printing: Use a stencil with pre-defined apertures to deposit solder paste onto the PCB pads. The solder paste will form into balls during the reflow process.
- Solder Preforms: Place pre-formed solder balls onto the PCB pads using a pick-and-place machine or tweezers. This method ensures consistent solder ball size and shape.
- Solder Jetting: Use a specialized solder jetting machine to dispense precise amounts of molten solder directly onto the PCB pads, creating uniform solder balls.
Factors Affecting Solder Ball Quality
Several factors can influence the quality of solder balls during the PCB assembly process:
- Solder Paste Composition: Use high-quality solder paste with the appropriate alloy composition and particle size for the specific application.
- Stencil Design: Ensure the stencil apertures are correctly sized and shaped to deposit the desired amount of solder paste onto the pads.
- Reflow Profile: Optimize the reflow oven temperature profile to ensure proper solder melting, wetting, and solidification.
- PCB Surface Finish: Choose a suitable PCB surface finish, such as Organic Solderability Preservative (OSP) or Electroless Nickel Immersion Gold (ENIG), to promote good solder wetting and adhesion.
Inspecting and Testing Solder Balls
After the soldering process, inspect and test the solder balls to ensure their quality and reliability:
- Visual Inspection: Use a magnifying glass or microscope to visually inspect the solder balls for defects, such as bridging, insufficient wetting, or voids.
- X-Ray Inspection: Employ X-ray imaging to detect hidden solder ball defects, such as voids or cracks, that are not visible through visual inspection.
- Electrical Testing: Perform continuity and resistance tests to verify the electrical integrity of the solder ball connections.
Troubleshooting Common Solder Ball Issues
Despite following best practices, solder ball issues may still arise during the PCB assembly process. Here are some common problems and their potential solutions:
Solder Ball Bridging
Causes:
– Excessive solder paste deposition
– Incorrect stencil aperture size or shape
– Insufficient space between pads
Solutions:
– Adjust solder paste deposition volume
– Modify stencil design to reduce aperture size or change shape
– Increase pad spacing or redesign PCB layout
Insufficient Solder Ball Wetting
Causes:
– Contaminated or oxidized PCB pads
– Incorrect reflow temperature profile
– Poor solder paste quality
Solutions:
– Clean and prepare PCB pads before soldering
– Optimize reflow temperature profile
– Use fresh, high-quality solder paste
Solder Ball Voids
Causes:
– Trapped flux or gases during reflow
– Incorrect reflow temperature profile
– Contaminated or low-quality solder paste
Solutions:
– Optimize reflow temperature profile to allow for proper outgassing
– Use solder paste with appropriate flux composition
– Ensure solder paste is stored and handled correctly
Solder Ball Shape Irregularities
Causes:
– Uneven solder paste deposition
– Incorrect stencil aperture design
– Poor PCB pad surface finish
Solutions:
– Ensure consistent solder paste deposition
– Modify stencil aperture design for better solder ball formation
– Choose a suitable PCB surface finish for improved solder wetting
FAQ
-
Q: What is the difference between lead-based and lead-free solder balls?
A: Lead-based solder balls, typically made from tin-lead (SnPb) alloys, have been traditionally used in PCB assembly for their excellent wetting properties and low melting point. However, due to environmental and health concerns, lead-free solder balls, such as tin-silver-copper (SAC) alloys, are becoming increasingly popular as a replacement for lead-based solder balls. -
Q: How do I choose the right solder ball size for my PCB assembly?
A: The choice of solder ball size depends on the specific application and the size of the components being soldered. Smaller solder balls (0.25mm to 0.60mm) are used for fine-pitch components like chip scale packages (CSP) and ball grid arrays (BGA), while larger solder balls (0.76mm to 1.50mm) are used for standard BGA packages and through-hole components. -
Q: What is the purpose of applying solder paste before placing components on the PCB?
A: Solder paste serves two primary purposes in PCB assembly: First, it provides a temporary adhesive to hold components in place during the soldering process. Second, it contains the solder alloy and flux necessary to create a strong and reliable solder joint when heated during the reflow process. -
Q: How can I prevent solder ball bridging during the PCB assembly process?
A: To prevent solder ball bridging, ensure that the solder paste deposition volume is appropriate for the pad size and spacing. Adjust the stencil aperture size and shape to control the amount of solder paste deposited. Additionally, ensure sufficient spacing between pads and redesign the PCB layout if necessary. -
Q: What are the advantages of using X-ray inspection for solder ball quality control?
A: X-ray inspection allows for the detection of hidden solder ball defects, such as voids or cracks, that are not visible through visual inspection. This non-destructive testing method provides a comprehensive view of the solder ball quality, enabling better quality control and ensuring the reliability of the PCB assembly.
Conclusion
Creating high-quality PCB solder balls is essential for ensuring strong, reliable connections between electronic components and the printed circuit board. By understanding the techniques, tools, and best practices involved in solder ball formation, PCB designers and assembly technicians can optimize their processes and troubleshoot common issues.
Remember to properly prepare the PCB surface, choose the appropriate solder ball size and alloy, and employ suitable formation methods like stencil printing, solder preforms, or solder jetting. Regularly inspect and test the solder balls to maintain quality control and address any defects promptly.
By following the guidelines outlined in this article, you can consistently produce high-quality PCB solder balls, leading to more reliable and efficient electronic devices. As technology advances and electronic components become increasingly miniaturized, mastering the art of creating good PCB solder balls will remain a critical skill in the electronics manufacturing industry.
Leave a Reply