Introduction to PCB Heatsinks
Printed circuit boards (PCBs) are essential components in most modern electronic devices. As electronic systems become more complex and powerful, managing heat dissipation becomes increasingly critical for ensuring optimal performance and reliability. PCB heatsinks are an effective solution for dissipating excess heat generated by electronic components, preventing overheating and potential damage.
In this comprehensive guide, we will explore the fundamentals of PCB heatsink design and selection, providing you with the knowledge and tools necessary to make informed decisions when implementing thermal management solutions for your PCB projects.
Understanding Heat Transfer in PCBs
Before diving into heatsink design and selection, it is essential to understand the basic principles of heat transfer in PCBs. Heat transfer occurs through three primary mechanisms: conduction, convection, and radiation.
Conduction
Conduction is the transfer of heat through direct contact between two materials. In PCBs, heat is conducted from electronic components to the PCB substrate and then to the heatsink. The effectiveness of heat conduction depends on factors such as the thermal conductivity of the materials and the contact area between the components and the heatsink.
Convection
Convection is the transfer of heat through the movement of fluids or gases. In PCBs, convection occurs when air flows over the surface of the heatsink, carrying heat away from the components. The effectiveness of convection depends on factors such as the surface area of the heatsink, the ambient temperature, and the airflow velocity.
Radiation
Radiation is the transfer of heat through electromagnetic waves. While radiation plays a role in heat transfer in PCBs, its contribution is generally less significant compared to conduction and convection.
Factors Affecting PCB Thermal Performance
Several factors influence the thermal performance of a PCB and the selection of an appropriate heatsink. These factors include:
Power Dissipation
The amount of power dissipated by electronic components is a critical factor in determining the required heatsink size and performance. Higher power dissipation generally requires larger and more efficient heatsinks.
Component Placement
The placement of components on the PCB can significantly impact thermal performance. Components that generate significant heat should be placed in areas with good airflow and sufficient space for heatsink mounting.
PCB Material
The choice of PCB material can affect thermal performance. Materials with higher thermal conductivity, such as aluminum or copper, can help dissipate heat more effectively than standard FR-4 PCBs.
Ambient Temperature
The ambient temperature of the operating environment can influence the effectiveness of heatsinks. Higher ambient temperatures may require larger or more efficient heatsinks to maintain acceptable component temperatures.
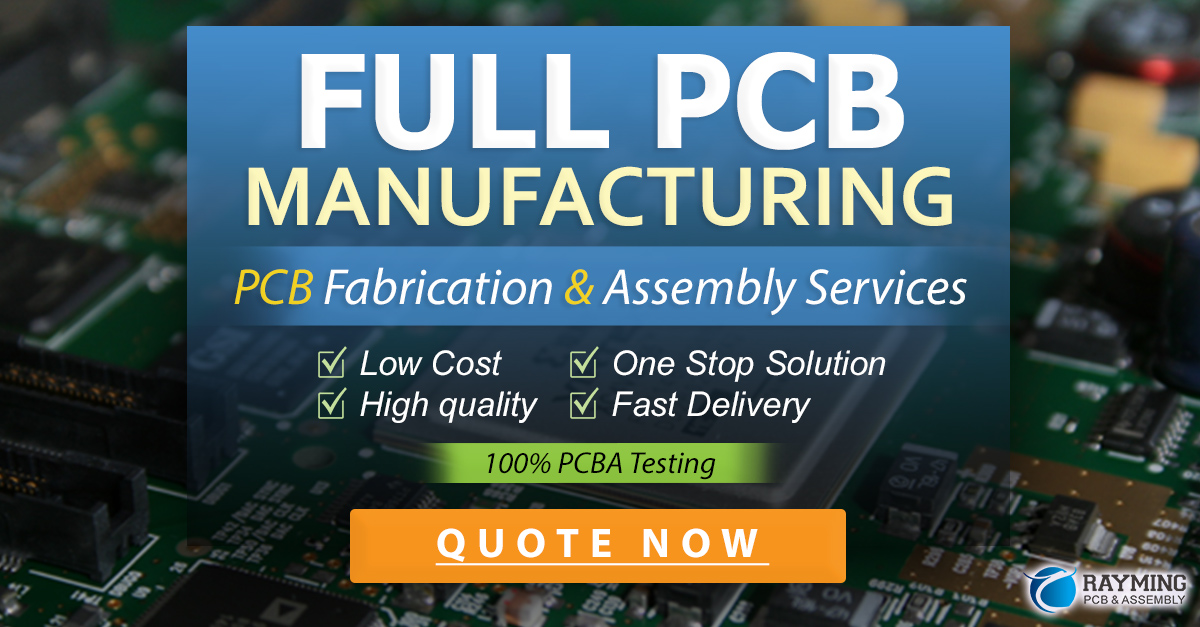
Heatsink Materials and Properties
Heatsinks are typically made from materials with high thermal conductivity, allowing for efficient heat dissipation. The most common materials used for PCB heatsinks include:
Aluminum
Aluminum is a popular choice for heatsinks due to its excellent thermal conductivity, lightweight, and cost-effectiveness. Aluminum heatsinks are available in various shapes and sizes, making them suitable for a wide range of applications.
Copper
Copper has an even higher thermal conductivity than aluminum, making it an excellent choice for high-performance heatsinks. However, copper heatsinks are generally more expensive and heavier than their aluminum counterparts.
Thermal Interface Materials (TIMs)
Thermal interface materials, such as thermal grease, pads, or adhesive tapes, are used to enhance the thermal contact between the electronic components and the heatsink. TIMs help fill any air gaps and improve heat conduction, ensuring efficient heat transfer from the components to the heatsink.
Heatsink Design Considerations
When designing or selecting a heatsink for your PCB, consider the following factors:
Surface Area
The surface area of the heatsink plays a crucial role in its ability to dissipate heat. Larger surface areas allow for more efficient heat transfer through convection. Heatsinks with fins or other features that increase surface area are often used to improve thermal performance.
Thermal Resistance
Thermal resistance is a measure of a heatsink’s ability to dissipate heat. Lower thermal resistance indicates better heat dissipation performance. When selecting a heatsink, choose one with a thermal resistance that is appropriate for your specific application and power dissipation requirements.
Mounting Methods
Heatsinks can be mounted to PCBs using various methods, such as:
- Adhesive mounting: Using thermal adhesive tapes or epoxies to attach the heatsink to the PCB or components.
- Mechanical mounting: Using screws, clips, or other hardware to secure the heatsink to the PCB or components.
- Push-pin mounting: Using push-pins to attach the heatsink to the PCB or components, allowing for easy installation and removal.
Choose a mounting method that provides secure attachment and good thermal contact while considering factors such as ease of installation, component accessibility, and manufacturing processes.
Orientation and Airflow
The orientation of the heatsink and the direction of airflow can significantly impact its performance. Heatsinks should be oriented to maximize exposure to airflow, allowing for efficient convective heat transfer. In applications with forced airflow, such as those using fans, the heatsink should be positioned to take advantage of the airflow direction.
Heatsink Selection Process
When selecting a heatsink for your PCB, follow these steps:
- Determine the power dissipation of the electronic components that require heatsinking.
- Calculate the maximum allowable temperature rise for the components based on their specifications and the ambient temperature.
- Estimate the required thermal resistance of the heatsink using the power dissipation and maximum allowable temperature rise.
- Choose a heatsink with a thermal resistance equal to or lower than the required value, considering factors such as size, weight, and compatibility with your PCB layout.
- Verify the heatsink performance through thermal simulations or testing to ensure that it meets the cooling requirements of your application.
Thermal Simulation and Testing
Thermal simulation and testing are essential steps in validating the performance of your PCB heatsink design. Thermal simulation software, such as ANSYS Icepak or Mentor Graphics FloTHERM, can help predict the temperature distribution and identify potential hot spots on your PCB. These simulations allow you to optimize your heatsink design and placement before manufacturing.
Once your PCB Prototype is built, thermal testing using thermocouples, infrared cameras, or other temperature measurement tools can help verify the actual thermal performance of your heatsink. Testing should be conducted under realistic operating conditions to ensure that the heatsink meets the cooling requirements of your application.
Heatsink Optimization Techniques
In addition to selecting the appropriate heatsink, several optimization techniques can be employed to improve the thermal performance of your PCB:
Thermal Vias
Thermal vias are conductive paths that transfer heat from the PCB surface to the inner layers or the opposite side of the board. By placing thermal vias near heat-generating components, you can improve heat dissipation and reduce component temperatures.
Copper Pours
Copper pours are large areas of copper on the PCB surface or inner layers that help spread heat more evenly across the board. By creating copper pours near heat-generating components and connecting them to the heatsink, you can improve heat conduction and overall thermal performance.
Component Placement and Spacing
Carefully planning the placement and spacing of components on your PCB can help optimize thermal performance. Place heat-generating components in areas with good airflow and sufficient space for heatsink mounting. Ensure adequate spacing between components to avoid thermal coupling and localized hot spots.
Frequently Asked Questions (FAQ)
1. How do I know if my PCB needs a heatsink?
If your PCB contains components that generate significant heat, such as power regulators, MOSFETs, or high-performance processors, a heatsink may be necessary to ensure proper cooling and prevent overheating. Additionally, if your PCB operates in a high-temperature environment or has limited airflow, a heatsink can help maintain acceptable component temperatures.
2. Can I use a heatsink that is larger than the recommended size?
Using a heatsink that is larger than the recommended size is generally acceptable and can provide better cooling performance. However, ensure that the larger heatsink does not interfere with other components or the overall PCB layout. Also, consider any size constraints or weight limitations that may apply to your application.
3. How do I ensure good thermal contact between the component and the heatsink?
To ensure good thermal contact, use an appropriate thermal interface material (TIM) between the component and the heatsink. Thermal grease, pads, or adhesive tapes help fill any air gaps and improve heat conduction. Additionally, ensure that the mounting method provides adequate pressure to maintain good contact between the surfaces.
4. Can I use a fan to improve heatsink performance?
Yes, using a fan to force airflow over the heatsink can significantly improve its cooling performance. Fans help increase convective heat transfer, allowing the heatsink to dissipate more heat. When using a fan, ensure that it is oriented correctly and provides sufficient airflow for your application.
5. How do I maintain and clean my PCB heatsinks?
To maintain the performance of your PCB heatsinks, periodically clean them to remove any dust or debris that may accumulate on the surfaces. Use compressed air or a soft brush to gently remove any contaminants. If necessary, you can use isopropyl alcohol to clean the heatsink surfaces. Avoid using abrasive materials or chemicals that may damage the heatsink or the PCB Components.
Conclusion
Effective PCB heatsink design and selection are critical for ensuring the optimal performance and reliability of electronic systems. By understanding the principles of heat transfer, considering various design factors, and following a systematic selection process, you can choose the most appropriate heatsink for your PCB application.
Remember to consider factors such as power dissipation, component placement, heatsink material, thermal resistance, and mounting methods when designing or selecting a heatsink. Additionally, employ optimization techniques such as thermal vias, copper pours, and component placement to enhance the overall thermal performance of your PCB.
By applying the knowledge and best practices outlined in this essential guide, you can confidently design and select PCB heatsinks that effectively dissipate heat, protect your electronic components, and ensure the long-term reliability of your devices.
Heatsink Material | Thermal Conductivity (W/m·K) | Density (g/cm³) | Specific Heat Capacity (J/g·°C) |
---|---|---|---|
Aluminum | 205 | 2.70 | 0.90 |
Copper | 385 | 8.96 | 0.39 |
Aluminum Alloy | 120-180 | 2.60-2.80 | 0.90-1.00 |
Graphite | 100-400 | 1.60-2.20 | 0.70-0.80 |
Table 1: Properties of common heatsink materials
Thermal Interface Material | Thermal Conductivity (W/m·K) | Thermal Resistance (°C·cm²/W) |
---|---|---|
Thermal Grease | 0.5-10 | 0.05-1.0 |
Thermal Pad | 1-10 | 0.1-1.0 |
Thermal Adhesive Tape | 0.5-2 | 0.5-2.0 |
Phase Change Material | 1-5 | 0.1-0.5 |
Table 2: Properties of common thermal interface materials
Leave a Reply