Introduction to Rigid-Flex PCBs
Rigid-Flex PCBs are a type of printed circuit board that combines both rigid and flexible substrates, allowing for a more compact and reliable design compared to traditional PCBs. This hybrid design enables the creation of three-dimensional circuits that can fit into tight spaces and withstand harsh environments. Rigid-Flex PCBs have become increasingly popular in various industries, such as aerospace, medical devices, and consumer electronics, due to their numerous advantages over conventional PCBs.
Key Features of Rigid-Flex PCBs
- Combination of rigid and flexible substrates
- Ability to create three-dimensional circuits
- Improved reliability and durability
- Reduced size and weight
- Enhanced signal integrity
Introduction to Flexible PCBs
Flexible PCBs, also known as flex circuits, are a type of printed circuit board that uses a flexible substrate material, such as polyimide or polyester. These PCBs are designed to bend and flex, making them ideal for applications that require a high degree of flexibility or need to fit into tight spaces. Flexible PCBs are commonly used in wearable devices, medical equipment, and consumer electronics.
Key Features of Flexible PCBs
- Highly flexible substrate material
- Ability to bend and flex without damaging the circuit
- Lightweight and thin profile
- Improved heat dissipation
- Reduced assembly time and costs
Advantages of Rigid-Flex PCBs over Flexible PCBs
1. Increased Durability and Reliability
Rigid-flex PCBs offer superior durability and reliability compared to flexible PCBs. The combination of rigid and flexible substrates allows for a more robust design that can withstand repeated bending and flexing without damaging the circuit. Additionally, the rigid portions of the PCB provide structural support, reducing the risk of damage during assembly and use.
2. Improved Signal Integrity
Rigid-flex PCBs offer better signal integrity compared to flexible PCBs due to the presence of rigid substrates. The rigid portions of the PCB provide a stable platform for the components, reducing the risk of signal distortion or interference caused by the flexing of the board. This is particularly important in high-speed applications or when dealing with sensitive analog signals.
3. Reduced Size and Weight
Rigid-flex PCBs allow for a more compact design compared to flexible PCBs. By combining rigid and flexible substrates, designers can create three-dimensional circuits that can fit into tight spaces and reduce the overall size and weight of the device. This is particularly beneficial in applications where space is limited, such as in wearable devices or aerospace equipment.
4. Enhanced Thermal Management
Rigid-flex PCBs offer better thermal management compared to flexible PCBs. The rigid portions of the PCB can act as heat sinks, dissipating heat away from the components and preventing overheating. This is particularly important in high-power applications or when dealing with temperature-sensitive components.
5. Simplified Assembly Process
Rigid-flex PCBs can simplify the assembly process compared to flexible PCBs. The rigid portions of the PCB provide a stable platform for the components, making it easier to align and solder them in place. Additionally, the flexible portions of the PCB can be folded or bent into the desired shape, reducing the need for additional connectors or wiring.
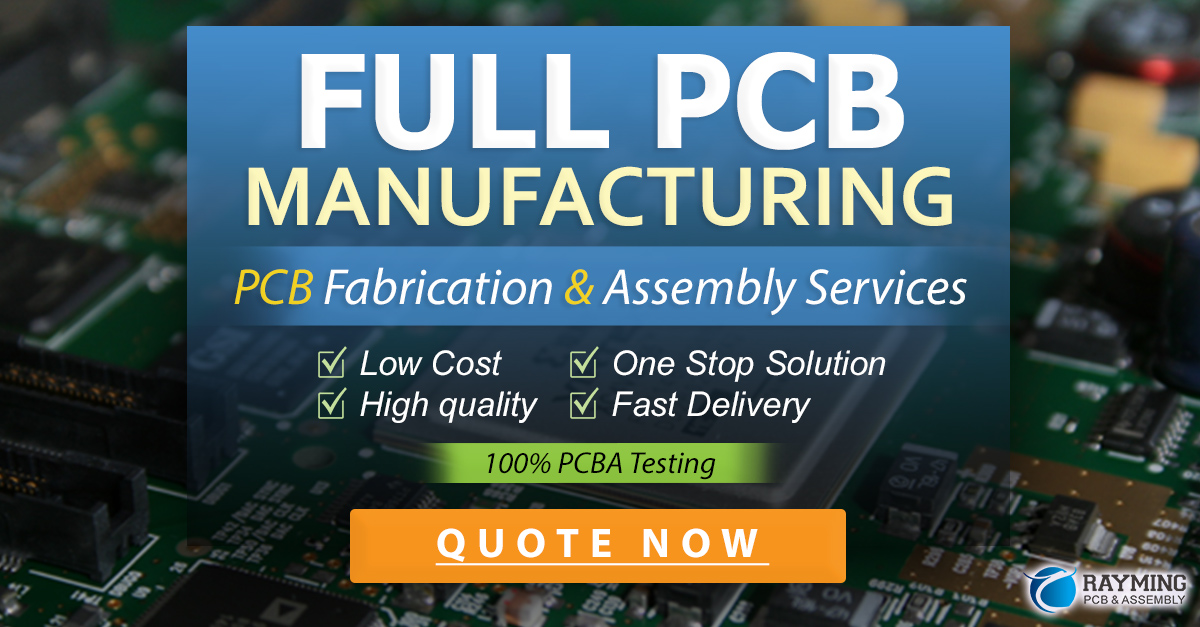
Disadvantages of Rigid-Flex PCBs Compared to Flexible PCBs
1. Higher Cost
One of the main disadvantages of rigid-flex PCBs compared to flexible PCBs is the higher cost. The manufacturing process for rigid-flex PCBs is more complex and requires specialized equipment and materials, resulting in a higher overall cost. This can be a significant consideration for cost-sensitive applications or high-volume production runs.
2. Longer Lead Times
Rigid-flex PCBs typically have longer lead times compared to flexible PCBs due to the more complex manufacturing process. The design and fabrication of rigid-flex PCBs require additional steps, such as the lamination of rigid and flexible substrates, which can increase the overall production time. This can be a disadvantage in fast-paced industries or when quick turnaround times are required.
3. Limited Flexibility
While rigid-flex PCBs offer a degree of flexibility, they are not as flexible as pure flexible PCBs. The rigid portions of the PCB limit the overall flexibility of the board, which can be a disadvantage in applications that require a high degree of bending or folding. In such cases, a pure flexible PCB may be a better choice.
Applications of Rigid-Flex PCBs
Rigid-flex PCBs are used in a wide range of industries and applications due to their unique combination of flexibility and durability. Some of the most common applications of rigid-flex PCBs include:
1. Aerospace and Defense
Rigid-flex PCBs are widely used in the aerospace and defense industries due to their ability to withstand harsh environments and extreme temperatures. They are used in a variety of applications, such as avionics systems, missiles, and satellites. The compact design and improved reliability of rigid-flex PCBs make them ideal for these critical applications.
2. Medical Devices
Rigid-flex PCBs are increasingly being used in medical devices, such as implantable devices, diagnostic equipment, and wearable health monitors. The flexibility and durability of rigid-flex PCBs make them well-suited for these applications, where reliability and patient safety are paramount. Additionally, the compact design of rigid-flex PCBs allows for the creation of smaller and more efficient medical devices.
3. Automotive Electronics
Rigid-flex PCBs are used in various automotive electronics applications, such as infotainment systems, engine control units, and advanced driver assistance systems (ADAS). The harsh environment and vibration encountered in automotive applications require PCBs that are both durable and reliable. Rigid-flex PCBs offer the necessary robustness and signal integrity to meet these challenges.
4. Consumer Electronics
Rigid-flex PCBs are increasingly being used in consumer electronics, such as smartphones, tablets, and wearable devices. The compact design and improved reliability of rigid-flex PCBs make them ideal for these applications, where space is limited and durability is essential. Additionally, the ability to create three-dimensional circuits allows for more innovative and efficient designs.
Applications of Flexible PCBs
Flexible PCBs are used in a variety of industries and applications that require a high degree of flexibility and a compact design. Some of the most common applications of flexible PCBs include:
1. Wearable Devices
Flexible PCBs are widely used in wearable devices, such as smartwatches, fitness trackers, and medical monitoring devices. The flexibility and lightweight nature of flex circuits make them ideal for these applications, where comfort and durability are essential. Additionally, the ability to conform to the shape of the human body allows for more ergonomic and user-friendly designs.
2. Robotics and Automation
Flexible PCBs are used in various robotics and automation applications, such as robotic arms, industrial sensors, and machine vision systems. The flexibility of flex circuits allows for greater freedom of movement and improved durability in these dynamic environments. Additionally, the lightweight nature of flexible PCBs reduces the overall weight of the robotic system, improving efficiency and performance.
3. Displays and Lighting
Flexible PCBs are used in a variety of display and lighting applications, such as flexible displays, OLED lighting, and LED signage. The ability to bend and conform to various shapes makes flexible PCBs ideal for these applications, where a thin and lightweight profile is essential. Additionally, the improved heat dissipation of flex circuits helps to prolong the life of the display or lighting components.
Comparison Table: Rigid-Flex PCBs vs. Flexible PCBs
Feature | Rigid-Flex PCBs | Flexible PCBs |
---|---|---|
Substrate | Combination of rigid and flexible materials | Flexible materials (e.g., polyimide, polyester) |
Flexibility | Moderate flexibility, limited by rigid portions | High flexibility, can bend and flex freely |
Durability | High durability, withstands repeated bending | Moderate durability, may degrade over time with repeated flexing |
Signal Integrity | Excellent signal integrity due to rigid portions | Good signal integrity, but may be affected by flexing |
Size and Weight | Compact and lightweight design | Thin and lightweight profile |
Thermal Management | Good thermal management due to rigid portions | Improved heat dissipation compared to rigid PCBs |
Assembly Process | Simplified assembly due to stable platform | Reduced assembly time and costs |
Cost | Higher cost due to complex manufacturing process | Lower cost compared to rigid-flex PCBs |
Lead Time | Longer lead times due to additional manufacturing steps | Shorter lead times compared to rigid-flex PCBs |
FAQ
1. What is the main difference between rigid-flex PCBs and flexible PCBs?
The main difference between rigid-flex PCBs and flexible PCBs is the substrate material used. Rigid-flex PCBs combine both rigid and flexible substrates, while flexible PCBs use only flexible materials, such as polyimide or polyester. This difference in substrate composition results in varying degrees of flexibility, durability, and signal integrity.
2. Which type of PCB is more durable: rigid-flex or flexible?
Rigid-flex PCBs are generally more durable than flexible PCBs. The rigid portions of the rigid-flex PCB provide structural support and help to protect the flexible portions from damage due to repeated bending and flexing. Flexible PCBs, while still durable, may degrade over time with repeated flexing.
3. Are rigid-flex PCBs more expensive than flexible PCBs?
Yes, rigid-flex PCBs are typically more expensive than flexible PCBs. The manufacturing process for rigid-flex PCBs is more complex and requires specialized equipment and materials, resulting in a higher overall cost. Flexible PCBs, on the other hand, have a simpler manufacturing process and are generally less expensive.
4. Which industries commonly use rigid-flex PCBs?
Rigid-flex PCBs are commonly used in industries that require high reliability, durability, and compact designs. Some of these industries include aerospace and defense, medical devices, automotive electronics, and consumer electronics. The unique combination of flexibility and durability offered by rigid-flex PCBs makes them well-suited for applications in these demanding fields.
5. Can flexible PCBs be used in wearable devices?
Yes, flexible PCBs are widely used in wearable devices, such as smartwatches, fitness trackers, and medical monitoring devices. The flexibility and lightweight nature of flex circuits make them ideal for these applications, where comfort and durability are essential. The ability to conform to the shape of the human body allows for more ergonomic and user-friendly designs.
Conclusion
Rigid-flex PCBs and flexible PCBs are both valuable technologies in the world of electronic design, each with their own unique advantages and disadvantages. Rigid-flex PCBs offer a combination of flexibility and durability, making them ideal for applications that require a compact design and high reliability. On the other hand, flexible PCBs excel in applications that demand a high degree of flexibility and a lightweight profile.
When choosing between rigid-flex PCBs and flexible PCBs, designers must consider factors such as the intended application, required durability, signal integrity, thermal management, and cost. By carefully evaluating these factors and understanding the strengths and limitations of each technology, designers can make an informed decision and select the most appropriate PCB type for their specific needs.
As technology continues to advance, it is likely that both rigid-flex PCBs and flexible PCBs will find new applications and continue to play a crucial role in the development of innovative electronic devices. By staying up-to-date with the latest advancements in PCB technology and understanding the unique characteristics of each type, designers can create more efficient, reliable, and user-friendly electronic products.
Leave a Reply